- March 4, 2025
- Posted by: feinuojixie
- Category: Injection Molding News
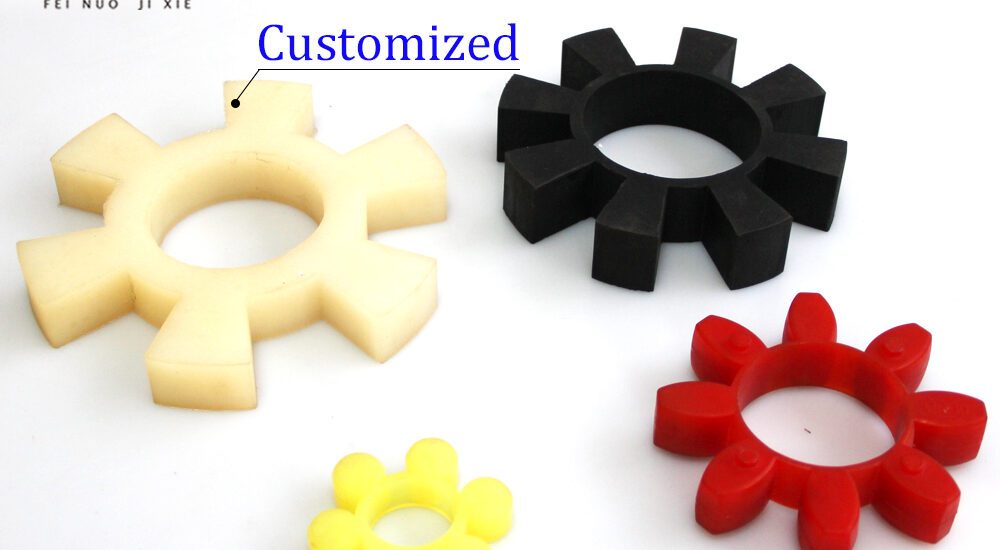
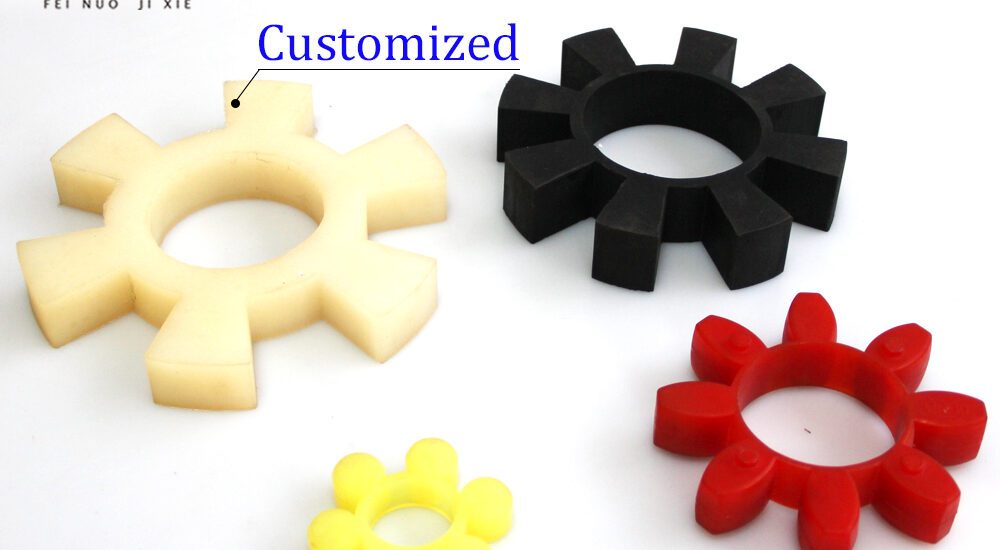
Injection molded part has become an indispensable component in modern manufacturing, playing a crucial role in the production of everyday items. This manufacturing technique allows for the mass production of high-quality, consistent, and durable parts across various industries. From automotive to medical, consumer electronics to packaging, injection molding has revolutionized the way products are made, ensuring efficiency, cost-effectiveness, and innovation. In this article, we will explore the significance of injection molded part, its advantages, applications, and what the future holds for this game-changing technology.
The Fundamentals of Injection Molded Part
Injection molded part is produced using a highly efficient manufacturing process known as injection molding. This process involves injecting molten material, typically plastic, into a mold cavity under high pressure. Once cooled and solidified, the part is ejected, resulting in a precise and durable product.
One of the reasons injection molding is so widely used is its ability to work with a variety of materials. Common plastics such as polypropylene, ABS, and polycarbonate are popular choices due to their durability, flexibility, and cost-effectiveness. In addition, advanced resins and composites have further expanded the possibilities for creating strong yet lightweight components.
The process of creating an injection molded part involves several steps:
- Clamping: The two halves of the mold are secured together.
- Injection: The molten plastic is injected into the mold cavity.
- Cooling: The plastic cools and hardens into the desired shape.
- Ejection: The finished part is removed from the mold.
This method ensures consistent results with minimal material waste, making it ideal for large-scale production.
Why Injection Molded Part Is Essential in Modern Manufacturing
Injection molding has become the backbone of modern manufacturing due to its efficiency and scalability. Unlike traditional machining or casting methods, injection molding allows for rapid production of thousands or even millions of identical parts with unmatched precision.
Another major advantage is cost-effectiveness. Since the molds are reusable and production cycles are fast, the per-unit cost of injection molded part is significantly lower than other manufacturing techniques. Additionally, automation in injection molding further reduces labor costs, making it an economically viable option for businesses.
Precision and consistency are also key factors in its widespread use. Injection molding ensures that every part meets strict design specifications, reducing defects and minimizing variations in quality. This level of accuracy is essential in industries where precision is critical, such as medical and aerospace manufacturing.
Industries That Rely on Injection Molded Part
The versatility of injection molding makes it a preferred manufacturing method across multiple industries:
Automotive Industry
Injection molded part is widely used in automobile production for components such as dashboards, bumpers, and interior trims. These parts are lightweight, durable, and capable of withstanding harsh environmental conditions.
Medical Industry
In the healthcare sector, precision is crucial. Injection molded part is used to create syringes, IV connectors, surgical instruments, and even prosthetic components. The ability to produce sterile, high-quality parts makes injection molding indispensable in medical applications.
Consumer Electronics
From smartphone casings to keyboard keys, injection molded part plays a significant role in electronics manufacturing. The process allows for the production of small, intricate components with superior durability and finish.
Packaging Industry
Many plastic containers, caps, and food packaging products are created through injection molding. This technique ensures lightweight, impact-resistant, and customizable packaging solutions that meet consumer needs.
Key Advantages of Injection Molded Part Over Other Manufacturing Techniques
Compared to traditional manufacturing methods, injection molding offers several benefits:
- Reduced Material Waste: Excess plastic can be recycled and reused, making the process more sustainable.
- Complex Designs with High Precision: Even the most intricate and detailed parts can be produced with exact specifications.
- Versatile Material Selection: From standard plastics to high-performance polymers, manufacturers can choose materials that best suit their needs.
- Scalability: Once the mold is created, mass production becomes quick and cost-effective.
Innovations in Injection Molded Part Technology
Advancements in technology continue to improve the efficiency and capabilities of injection molding:
- 3D Printing in Mold Production: The use of 3D-printed molds speeds up the design process and reduces costs.
- Smart Manufacturing & Automation: Robotics and AI integration enhance precision and reduce errors.
- Eco-Friendly Materials: The rise of biodegradable plastics and recycled resins is making injection molding more sustainable.
These innovations ensure that injection molded part remains a cornerstone of modern production, keeping up with the ever-evolving demands of various industries.
How to Choose the Right Injection Molded Part for Your Needs
Selecting the right injection molded part depends on several factors:
- Material Selection: Different applications require different plastic types. For example, medical devices need biocompatible materials, while automotive parts require high durability.
- Durability Requirements: Some parts need to withstand extreme temperatures, pressure, or impact.
- Cost Considerations: The complexity of the mold, material choice, and production volume all affect overall costs.
- Manufacturer Reputation: Working with a trusted manufacturer ensures high-quality results and reliable production capabilities.
The Future of Injection Molded Part in Manufacturing
The future of injection molding is driven by technological advancements and growing industry demands. Some key trends include:
- Increased Automation: AI-driven systems will make production more efficient and cost-effective.
- Sustainable Practices: The development of biodegradable and recycled materials will minimize environmental impact.
- Lightweight Materials: Industries such as aerospace and automotive will continue to seek strong yet lightweight solutions.
As industries push for higher efficiency, precision, and sustainability, injection molded part will continue to play a vital role in modern manufacturing.
Conclusion
Injection molded part has transformed manufacturing, making it faster, more cost-effective, and highly scalable. Its ability to produce precise, durable components has solidified its importance across various industries, from automotive to medical and electronics. As innovations continue to shape the industry, injection molding will remain a fundamental technology driving the future of production. Whether for small consumer goods or complex industrial applications, injection molded part will continue to be the backbone of modern manufacturing.