- March 7, 2025
- Posted by: feinuojixie
- Category: Injection Molding News
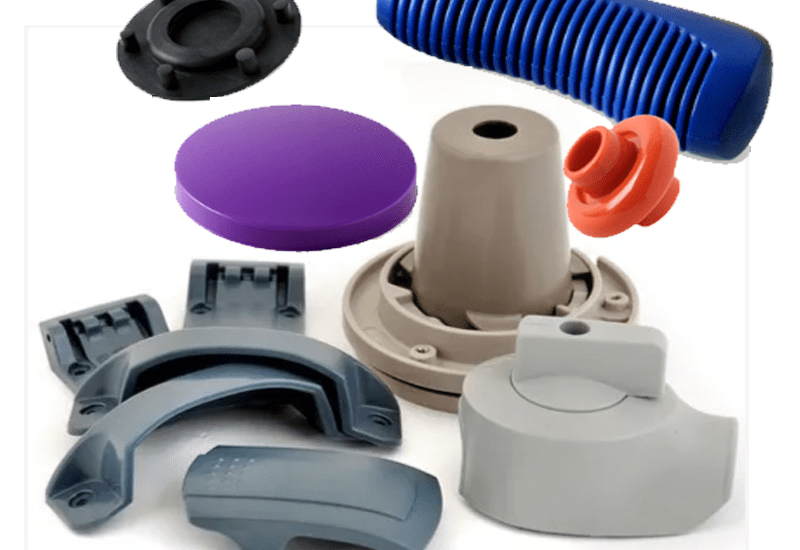
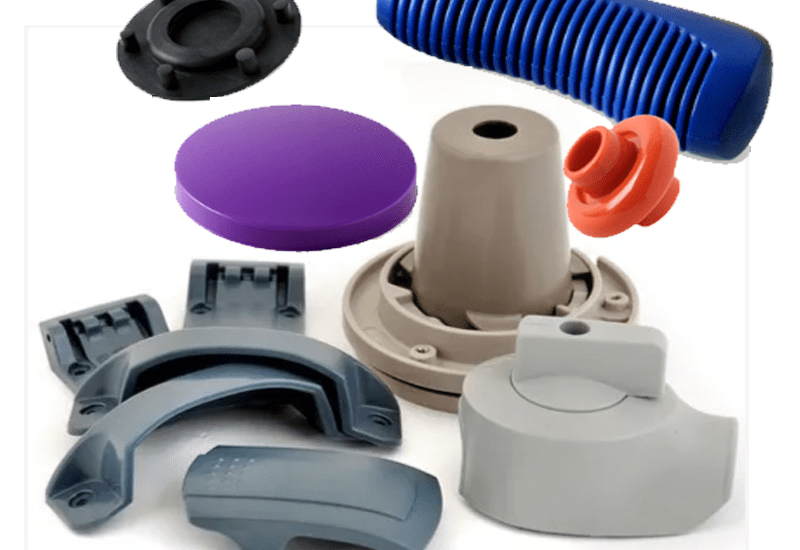
Plastic parts have become integral to almost every sector of manufacturing, from automotive to electronics, medical devices, and consumer goods. The ability to produce high-quality, precise plastic components on a large scale has transformed how industries operate. Among the many manufacturing methods used to create these parts, injection moulding stands out as one of the most powerful and efficient processes. Injection moulding allows manufacturers to turn conceptual designs into tangible, usable plastic parts that meet stringent industry standards.
In this article, we’ll explore the role of injection moulding in plastic part production, diving into the details of the process, its advantages, applications, and innovations. By understanding how injection moulding works, you’ll see why it is essential for producing the precise and complex parts that are vital to modern industries. Let’s journey from the initial design concept all the way to the creation of the finished plastic part.
The Basics of Injection Moulding: What It Is and How It Works
Injection moulding is a manufacturing process used to produce parts by injecting molten plastic material into a mould. The process involves the following essential steps:
- Melted plastic injection: Plastic resin is heated to a molten state and then injected into a mould cavity under high pressure.
- Mould cooling: The molten plastic is allowed to cool and solidify, taking the shape of the mould.
- Ejection of the part: Once cooled, the mould opens, and the finished plastic part is ejected.
Typically, injection moulding is ideal for creating high-volume, precise plastic parts. A wide variety of materials, including thermoplastics and thermosets, can be used, allowing manufacturers to meet specific material properties like strength, flexibility, and heat resistance.
In the following sections, we will examine how injection moulding works in more detail and why it is preferred for the mass production of plastic parts.
Advantages of Using Injection Moulding for Plastic Parts
Injection moulding is one of the most widely used methods for manufacturing plastic parts due to several key advantages:
-
Precision and Complexity: Injection moulding allows manufacturers to produce highly complex and detailed parts with tight tolerances. This precision makes it ideal for industries requiring intricate designs, such as electronics and medical devices.
-
Speed and Efficiency: The injection moulding process is capable of high-speed production, enabling manufacturers to produce thousands or even millions of identical parts quickly.
-
Cost-effectiveness for Large Volumes: Once the mould is created, injection moulding is highly cost-efficient for producing large volumes of plastic parts. The process minimizes material waste and reduces the cost per part over time.
-
Consistency and Repeatability: Injection moulding ensures that every part produced is nearly identical, making it suitable for mass production where consistency is crucial.
These advantages make injection moulding the go-to choice for producing plastic parts in industries where quality, speed, and cost-effectiveness are paramount.
From Design to Mould Creation: How the Process Begins
The journey from concept to creation of a plastic part starts with the design. It is essential to consider the design requirements, including material selection, part geometry, and functionality.
-
Design and CAD: Computer-Aided Design (CAD) software is often used to create the initial design for plastic parts. This digital model allows manufacturers to simulate how the part will behave during the injection moulding process and optimize its design for functionality and manufacturability.
-
Mould Creation: The next step involves designing and creating the mould. A well-designed mould is crucial for ensuring that the final plastic part meets the necessary specifications. Factors like venting, gating, and cooling channels need to be considered when designing the mould.
The mould creation process typically involves high-precision machining to ensure that every detail of the design is replicated accurately.
Injection Moulding Process: The Steps to Producing Plastic Parts
Once the mould is ready, the injection moulding process begins:
- Injection: Molten plastic is injected into the mould cavity under high pressure, filling every detail of the mould.
- Cooling: After injection, the plastic part cools and solidifies within the mould. This step is critical for ensuring the part holds its shape and strength.
- Ejection: Once the part has cooled, the mould opens, and the part is ejected. Any excess material, such as flash, is removed during this step.
This process is repeated in a continuous cycle for high-volume production, ensuring uniformity and speed.
The Role of Material Selection in Injection Moulding for Plastic Parts
Selecting the right material for injection moulding is crucial to ensure the plastic part performs as intended. Different materials offer distinct properties:
- Polypropylene: Lightweight, durable, and resistant to chemicals, making it ideal for automotive and consumer products.
- ABS (Acrylonitrile Butadiene Styrene): Known for its toughness, impact resistance, and ease of processing, ABS is widely used in electronics and toys.
- Polycarbonate: Offers high impact resistance and optical clarity, making it suitable for applications in the medical and electronics industries.
Material selection affects not only the part’s functionality but also the moulding process, as different materials have varying flow characteristics and cooling times.
Applications of Injection Moulding in Various Industries
Injection moulding is utilized across numerous industries to produce a wide variety of parts:
- Automotive: Components like dashboard parts, door panels, and lighting systems.
- Electronics: Precision housings, connectors, and enclosures.
- Medical: Sterile medical devices, surgical instruments, and drug delivery systems.
- Consumer Goods: Packaging, household items, and small appliances.
In each case, the versatility and efficiency of injection moulding enable manufacturers to meet the specific demands of the industry.
Innovations in Injection Moulding Technology
Technological advancements continue to improve the injection moulding process. Some key innovations include:
- 3D Printing: Used for rapid prototyping, 3D printing helps to quickly test designs before committing to injection moulding.
- Sustainable Practices: The growing demand for eco-friendly products has led to innovations in biodegradable and recyclable plastic materials.
- Smart Moulding: Integration of sensors and real-time monitoring systems in the moulding process allows manufacturers to detect issues and optimize production.
These innovations are helping to make injection moulding more efficient, cost-effective, and environmentally friendly.
Challenges in Injection Moulding and How to Overcome Them
While injection moulding offers many benefits, there are also challenges that manufacturers must address:
- Warping: Uneven cooling of the plastic can cause the part to warp. Careful mould design and temperature control can help mitigate this.
- Shrinkage: Some plastics shrink as they cool, affecting the final part dimensions. Accurate mould design and material selection are key to managing shrinkage.
- Material Wastage: Minimizing waste requires efficient material handling and precise process control.
By understanding these challenges and taking proactive steps, manufacturers can ensure a high-quality end product.
The Future of Injection Moulding in Plastic Part Production
As industries continue to demand more complex, durable, and cost-effective plastic parts, injection moulding remains a cornerstone of modern manufacturing. The evolution of materials, technologies, and techniques promises an even brighter future for injection moulding, driving innovation and improving the production of plastic parts across sectors.
Injection moulding’s ability to efficiently produce high-quality plastic parts will continue to play a pivotal role in shaping the future of manufacturing.