- March 7, 2025
- Posted by: feinuojixie
- Category: Injection Molding News
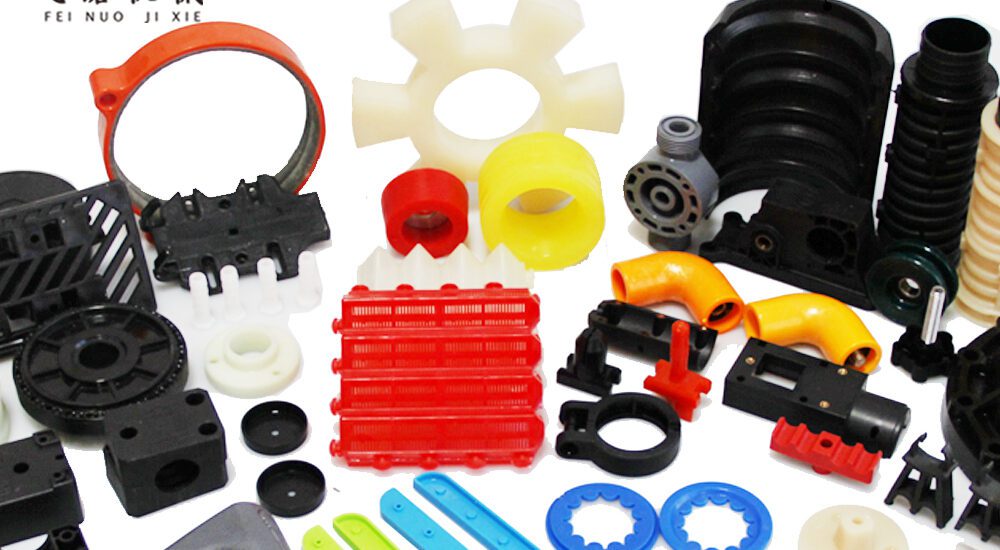
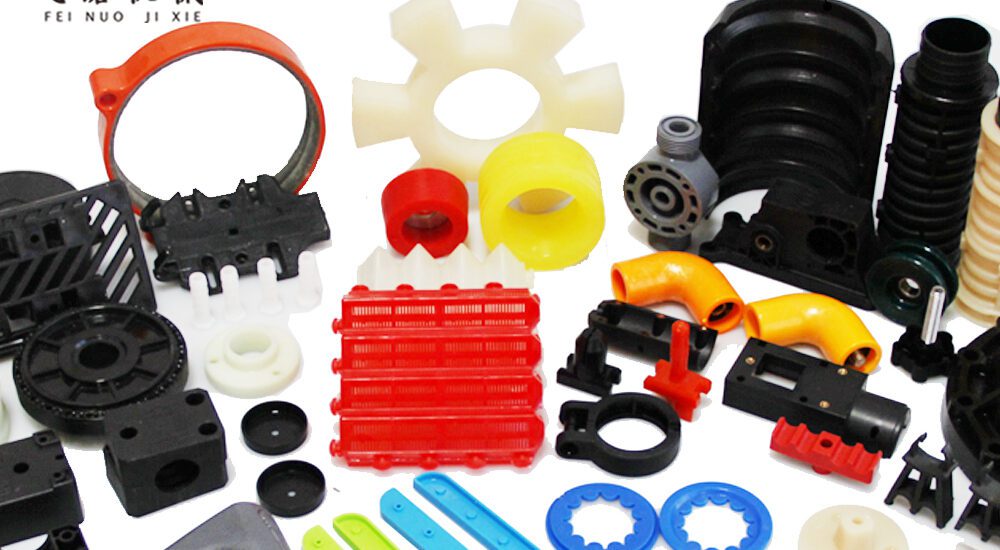
Injection moulding is a transformative manufacturing process that has revolutionized the production of plastic parts across various industries. It offers unmatched efficiency and precision, making it the go-to method for creating high-quality, intricate plastic components. As industries demand higher production rates, lower costs, and greater consistency, injection moulding meets these challenges head-on. In this article, we will explore how injection moulding maximizes efficiency and reshapes the plastic parts production landscape.
Understanding Injection Moulding Process
Injection moulding is a highly efficient manufacturing process used to produce plastic parts by injecting molten plastic into a precisely designed mould. The process begins by heating plastic pellets until they become a viscous liquid. This liquid plastic is then injected into a mould under high pressure, where it solidifies and takes the shape of the mould. Once the part has cooled and hardened, it is ejected from the mould and ready for use.
The key to the success of injection moulding lies in the design and quality of the mould itself. Moulds are made from durable metals like steel or aluminum and are designed to match the exact shape and dimensions of the desired plastic part. Additionally, the material chosen for the process plays a crucial role in the strength, flexibility, and other properties of the final part.
Why Injection Moulding Is the Best Choice for Plastic Part Production
Injection moulding has established itself as the best option for plastic part production for several reasons. One of the primary advantages is its ability to produce highly detailed and consistent parts. Whether the part is small or large, simple or complex, injection moulding ensures that each component produced meets the same exacting standards, minimizing the likelihood of defects.
Another major benefit is the speed at which injection moulding operates. The process can produce large quantities of parts in a short amount of time, which makes it ideal for high-volume production. Furthermore, once the initial set-up is completed, the process can be scaled to meet demand with minimal downtime.
Injection moulding also offers a cost-effective solution. The initial investment in mould design and production can be high, but once the mould is created, the cost per part decreases significantly, especially for mass production. Additionally, the process generates minimal waste, as excess material can often be recycled and reused.
Key Factors That Influence Injection Moulding Efficiency
Several factors influence the efficiency of the injection moulding process. One of the most important is the selection of the right material for the plastic part. The material must be compatible with the injection moulding process, able to flow easily into the mould, and possess the desired properties once cooled. Common materials used in injection moulding include thermoplastics, thermosets, and elastomers.
The design and maintenance of the mould are also critical to ensuring the efficiency of the process. Moulds need to be designed with precision to allow the molten plastic to flow evenly and fill all sections of the mould without defects. Regular maintenance is necessary to prevent wear and tear, which can lead to defects in the final product and increase production downtime.
Finally, modern injection moulding machines are equipped with advanced features that improve efficiency. These machines can be optimized for faster cycle times, precise temperature control, and energy-efficient operation. Machine advancements, such as automation and real-time monitoring, play a crucial role in boosting production rates and reducing human error.
Advancements in Injection Moulding Technology
The field of injection moulding has seen significant advancements in recent years, particularly in automation and technology integration. Automated systems, such as robotic arms, are now commonly used to handle tasks such as loading and unloading parts, reducing human intervention and increasing efficiency.
Real-time monitoring systems and smart sensors are another breakthrough that optimizes the production process. These systems continuously track variables such as temperature, pressure, and material flow, allowing for immediate adjustments and minimizing defects. This technology ensures that the injection moulding process is operating at its peak efficiency, leading to consistent product quality and reduced waste.
Sustainability has also become a focus within the industry. New injection moulding technologies emphasize reducing waste and energy consumption. For example, energy-efficient heating systems and the use of recyclable materials help decrease the environmental impact of production, making injection moulding a more sustainable option for manufacturing plastic parts.
Common Applications of Injection Moulding in Plastic Part Production
Injection moulding is used extensively in a variety of industries due to its versatility and efficiency. In the automotive sector, it plays a crucial role in producing durable plastic parts such as dashboards, bumpers, and interior components. These parts need to be lightweight, yet strong enough to withstand wear and tear, and injection moulding delivers these qualities with precision.
In the consumer electronics industry, injection moulding is essential for creating the intricate plastic components found in smartphones, laptops, and other gadgets. The ability to produce complex shapes with fine details allows for the manufacturing of small, functional parts that are critical to the performance of modern electronics.
Medical devices also benefit from the precision and reliability of injection moulding. Components such as surgical instruments, diagnostic equipment, and drug delivery systems require the highest standards of quality and safety, which injection moulding can provide. The ability to meet strict regulations and produce parts with tight tolerances makes injection moulding ideal for the medical industry.
Challenges in Injection Moulding and How to Overcome Them
While injection moulding is an efficient and reliable process, it does come with certain challenges. One common issue is dealing with material limitations, as not all plastics are suitable for the injection moulding process. Choosing the right material for each application is essential to ensuring that the final product performs as expected.
Another challenge is managing design complexities. The design of the mould plays a significant role in the success of the process, and certain features, such as undercuts or deep cavities, can complicate the manufacturing process. To overcome this, manufacturers must carefully plan the mould design and consider factors such as material flow and cooling rates.
Additionally, defects such as warping, sink marks, and surface blemishes can occur if the injection moulding process is not optimized. Manufacturers can overcome these issues by carefully controlling process variables, maintaining high-quality moulds, and performing regular maintenance on equipment.
Conclusion
Injection moulding is an essential technology in the production of plastic parts, offering unmatched efficiency, precision, and cost-effectiveness. By understanding the intricacies of the process and keeping up with technological advancements, manufacturers can maximize efficiency and produce high-quality parts for a variety of industries. As the demand for high-performance, sustainable plastic parts continues to rise, injection moulding will remain at the forefront of innovation in plastic part production.