- March 10, 2025
- Posted by: feinuojixie
- Category: Injection Molding News
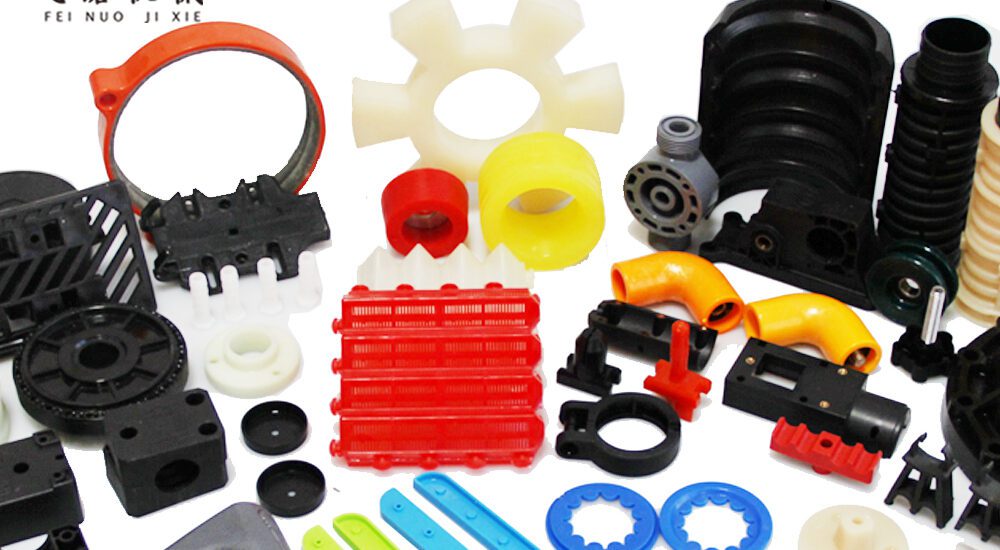
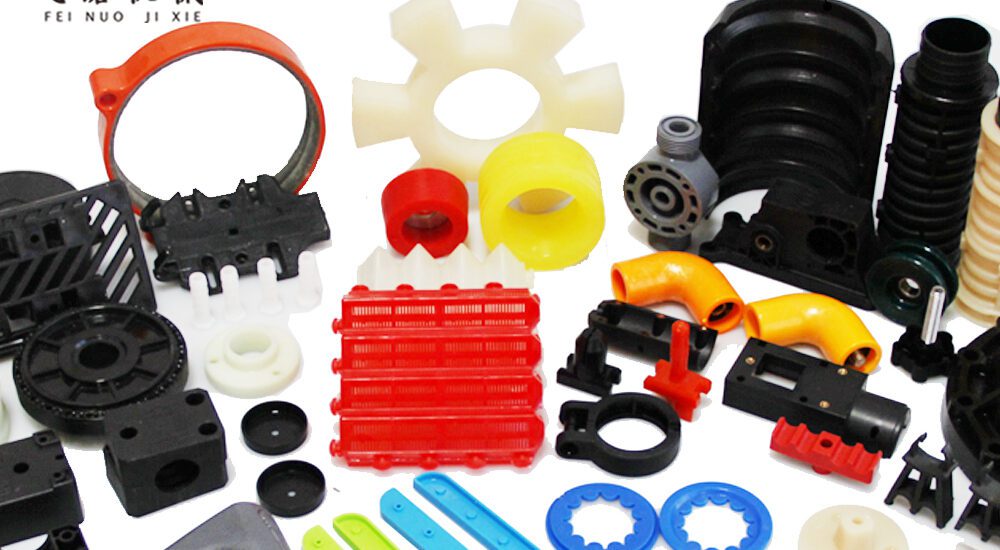
Injection moulding has long been a cornerstone of plastic part manufacturing, offering a reliable and efficient method for producing components across various industries. This highly versatile process enables manufacturers to create complex plastic part with precision and consistency. Over the years, technological advancements have dramatically enhanced injection moulding, making it possible to produce intricate designs with greater efficiency and lower costs.
As industries continue to demand high-quality plastic part with specific functionalities, innovations in injection moulding have paved the way for improved materials, smarter mould designs, and cutting-edge automation. These breakthroughs not only enhance the performance of the final product but also contribute to sustainability and cost reduction. In this article, we will explore the latest developments in injection moulding and how they are transforming the way plastic part are created with ease.
The Evolution of Injection Moulding in Plastic Part Manufacturing
Injection moulding has undergone significant advancements since its inception. Initially, the process was limited by basic machinery and material constraints, restricting the complexity of plastic part that could be produced. Early techniques relied on manual operations, leading to inconsistencies in quality and longer production times.
Over the years, improvements in machinery, mould design, and material science have transformed injection moulding into a highly precise and efficient manufacturing process. The integration of automation, computer-controlled systems, and real-time monitoring has enabled manufacturers to produce complex plastic part with minimal defects. As industries continue to push for higher precision and cost-effectiveness, modern injection moulding techniques have adapted to meet these demands, making it an indispensable technology for large-scale production.
Advanced Materials for Injection Moulding Plastic Part
Material innovation plays a crucial role in the evolution of injection moulding. Today, manufacturers have access to a wide range of high-performance polymers that offer enhanced strength, flexibility, and durability. These materials allow for the creation of lightweight yet robust plastic part suitable for various industries, including automotive, medical, and consumer electronics.
Sustainability is also a key focus in modern injection moulding. The development of biodegradable and recycled plastics has paved the way for more environmentally friendly manufacturing practices. By integrating sustainable materials, manufacturers can reduce waste and minimize the environmental impact of plastic production while maintaining high-quality standards.
Furthermore, custom polymer formulations have become increasingly popular, allowing manufacturers to tailor materials for specific applications. Whether it’s heat-resistant plastics for the automotive industry or biocompatible materials for medical devices, advanced polymers are expanding the possibilities of injection moulding.
Cutting-Edge Technologies in Injection Moulding
Technological advancements have played a vital role in optimizing injection moulding processes. The integration of automation and robotics has significantly improved production efficiency, reducing human error and increasing precision. Automated systems ensure consistent quality while enhancing the speed of manufacturing.
Another game-changing innovation is 3D printing, which has revolutionized mould prototyping and customization. Manufacturers can now create prototype moulds quickly, allowing for rapid testing and modifications before full-scale production. This not only reduces development time but also lowers costs associated with traditional mould fabrication.
Real-time monitoring and quality control systems have also improved injection moulding. Advanced sensors and data analytics enable manufacturers to detect defects early in the process, ensuring that each plastic part meets strict quality standards. These innovations help reduce material waste and enhance overall efficiency.
Innovative Mould Design for Complex Plastic Part
The design of injection moulds plays a critical role in the production of complex plastic part. With the help of computer-aided design (CAD) software, engineers can create highly detailed moulds that optimize material flow and minimize defects. This technology allows for precise mould creation, ensuring that even the most intricate plastic part can be manufactured with accuracy.
Multi-cavity and modular moulds have also improved efficiency by enabling the production of multiple plastic part simultaneously. This reduces cycle times and increases overall output, making injection moulding even more cost-effective.
Innovations in cooling and ejection systems have further enhanced the quality of plastic part. Advanced cooling technologies help regulate temperature during the moulding process, preventing warping and ensuring uniformity. Additionally, improved ejection mechanisms reduce the risk of damage to delicate plastic part, maintaining high production standards.
The Benefits of Modern Injection Moulding Techniques
The advancements in injection moulding have brought numerous benefits to manufacturers and consumers alike. One of the most significant advantages is the reduction in production time. With faster cycle times and automated processes, manufacturers can produce plastic part at a much higher rate while maintaining precision.
Cost-effectiveness is another major benefit. Modern injection moulding techniques minimize material waste and energy consumption, leading to lower production costs. These savings are passed on to consumers, making high-quality plastic part more affordable.
Design flexibility has also improved, allowing manufacturers to create intricate and highly detailed plastic part that were once impossible to achieve. The ability to produce complex shapes and fine details with ease has expanded the application of injection moulding across multiple industries.
Industry Applications of Injection Moulding Plastic Part
Injection moulding is widely used in various industries due to its ability to produce durable and precise plastic part. In the automotive sector, lightweight plastics are replacing traditional metal components, contributing to fuel efficiency and vehicle performance. Advanced injection moulding techniques enable manufacturers to create strong, heat-resistant plastic part for critical automotive applications.
In the medical industry, precision is paramount. Injection moulding is used to produce sterile medical devices, such as syringes, surgical instruments, and implants. The ability to manufacture biocompatible and high-precision plastic part has significantly improved healthcare technology.
Consumer electronics also rely heavily on injection moulding. From smartphone casings to intricate internal components, plastic part manufactured through injection moulding provide durability, aesthetic appeal, and functionality. The advancements in material science and mould design have allowed for thinner, more lightweight plastic part without compromising strength.
Challenges and Future Trends in Injection Moulding
Despite its numerous advantages, injection moulding faces challenges that manufacturers must address. One of the biggest concerns is sustainability. As plastic waste becomes a global issue, companies are seeking ways to reduce environmental impact by using recycled materials and biodegradable plastics. Future innovations in sustainable materials will play a crucial role in making injection moulding more eco-friendly.
Micro-moulding is another emerging trend. As industries demand smaller, highly precise plastic part, manufacturers are investing in micro-moulding technology to produce intricate components with minimal material usage. This is particularly relevant in the medical and electronics industries, where miniaturization is a key focus.
Smart manufacturing and Industry 4.0 are also shaping the future of injection moulding. The integration of AI-driven quality control, predictive maintenance, and real-time data analysis is improving efficiency and reducing downtime. These innovations will further enhance the reliability and scalability of injection moulding in the years to come.
Conclusion
The innovations in injection moulding have revolutionized the way plastic part are manufactured, offering greater precision, efficiency, and cost-effectiveness. Advances in materials, mould design, and automation have enabled the production of complex plastic part with ease, meeting the growing demands of various industries.
As sustainability and technological advancements continue to shape the industry, the future of injection moulding looks promising. From biodegradable materials to AI-driven manufacturing processes, injection moulding is evolving to meet the challenges of modern production while maintaining its position as a leading manufacturing method.
With ongoing innovations, injection moulding will continue to push the boundaries of what is possible in plastic part production, ensuring a future of high-quality, sustainable, and cost-efficient manufacturing.