- March 10, 2025
- Posted by: feinuojixie
- Category: Injection Molding News
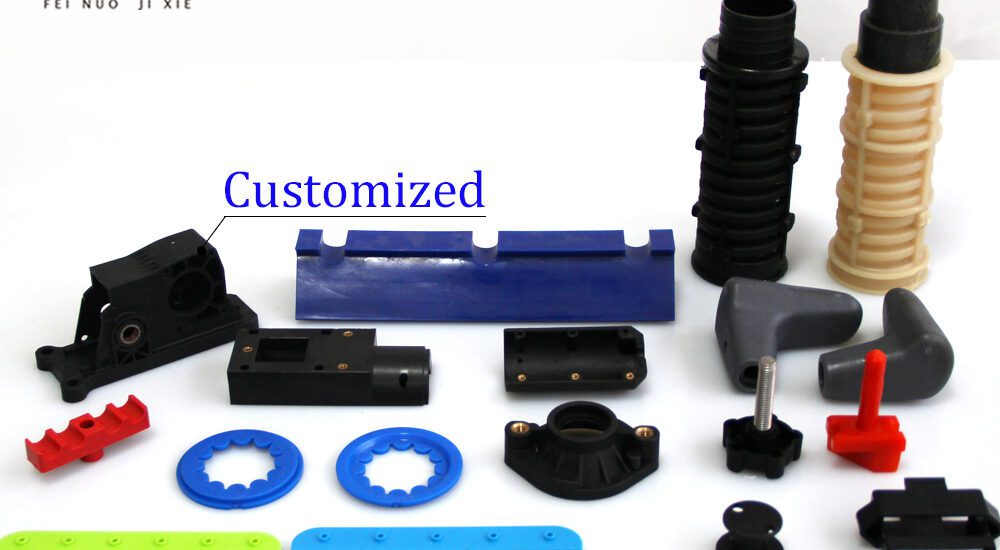
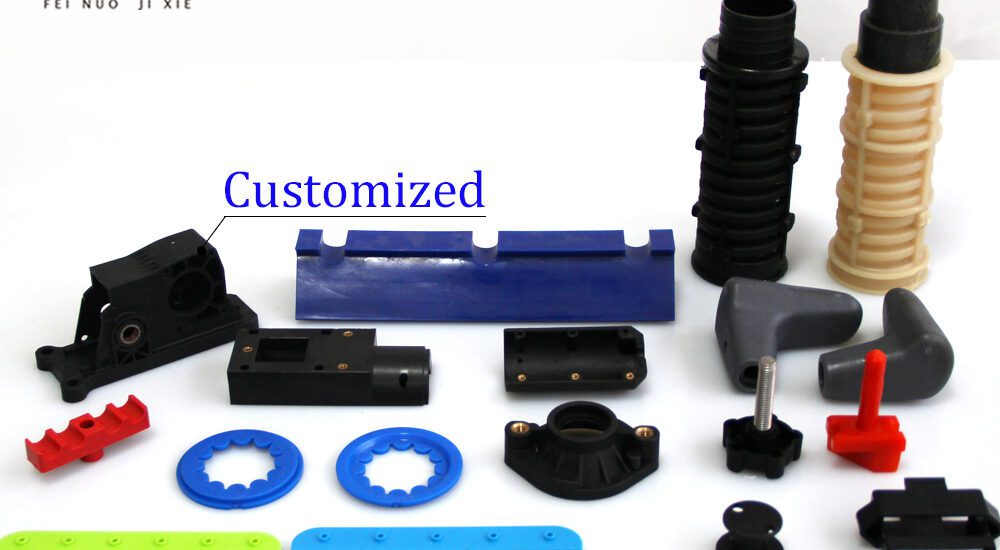
Injection moulding plastic part is one of the most efficient and cost-effective manufacturing methods available. This process allows businesses to produce high-quality, durable, and precision-engineered components at scale. Whether for automotive, medical, consumer electronics, or packaging industries, injection moulding plastic part ensures consistency, speed, and affordability. In this article, we explore the various factors that make injection moulding a cost-effective choice and how manufacturers can optimize production for maximum efficiency.
Understanding Injection Moulding Plastic Part: The Basics
Injection moulding plastic part involves injecting molten plastic into a mould to create a specific shape. This method is widely used due to its ability to produce complex and highly detailed parts with minimal waste. The process consists of the following steps:
- Material melting – Plastic pellets are heated until they become liquid.
- Injection – The molten plastic is injected into a mould cavity under high pressure.
- Cooling and solidification – The plastic cools and hardens into the desired shape.
- Ejection – The finished part is ejected from the mould for further processing or assembly.
By automating this process, manufacturers can produce thousands or even millions of identical parts quickly and efficiently.
Cost Advantages of Injection Moulding Plastic Part
One of the primary reasons businesses choose injection moulding plastic part is its cost-effectiveness. Some key cost advantages include:
- Low unit cost for high-volume production – Once the mould is created, each part can be produced at a fraction of the initial cost.
- Minimal material waste – Unlike machining, where excess material is cut away, injection moulding ensures precise use of materials.
- Automation reduces labour costs – Modern injection moulding machines operate with minimal human intervention, lowering operational costs.
For businesses that require large quantities of plastic parts, injection moulding offers unparalleled cost savings.
Factors That Influence the Cost of Injection Moulding Plastic Part
While injection moulding is a cost-effective solution, several factors can influence the overall production cost:
- Material selection – The type of plastic used can significantly affect costs. Some materials are more expensive but offer better durability or heat resistance.
- Tooling and mould creation – The initial cost of creating a mould can be high, but it is a one-time investment that pays off in large production runs.
- Production volume – The more parts produced, the lower the cost per unit. Small production runs may not be as cost-effective.
Understanding these factors allows manufacturers to optimize costs without compromising quality.
Design Optimization for Cost-Effective Injection Moulding Plastic Part
Efficient design is crucial for reducing costs in injection moulding plastic part. Here are some key design principles:
- Uniform wall thickness – Inconsistent thickness can lead to defects and increased material usage.
- Reducing undercuts – Complex designs with undercuts may require expensive moulds and additional processing.
- Optimized gating and runner systems – Proper placement of gates and runners helps minimize waste and improve efficiency.
By working with experienced designers, manufacturers can reduce costs while maintaining product quality.
Material Selection for Injection Moulding Plastic Part: Balancing Quality and Cost
Choosing the right material is essential for both performance and cost savings. Common materials used in injection moulding plastic part include:
- Polypropylene (PP) – Affordable, durable, and widely used for consumer products.
- Acrylonitrile Butadiene Styrene (ABS) – Strong and impact-resistant, ideal for automotive and electronic components.
- Polycarbonate (PC) – High transparency and heat resistance, suitable for optical applications.
- Recycled plastics – An environmentally friendly and cost-saving option for many applications.
Selecting the best material ensures that the final product meets performance requirements while staying within budget.
Enhancing Production Efficiency in Injection Moulding Plastic Part
To further reduce costs and improve efficiency, manufacturers can implement the following strategies:
- Automation and robotics – Automated systems reduce cycle times and labour costs.
- Cycle time optimization – Shorter cycles lead to higher output and lower energy consumption.
- Defect prevention measures – Quality control and precise mould design reduce the need for rework and scrap.
Continuous process improvements help manufacturers achieve higher profitability.
Comparing Injection Moulding Plastic Part to Other Manufacturing Methods
Injection moulding plastic part is not the only manufacturing method available. Here is how it compares to other techniques:
- Injection moulding vs. CNC machining – CNC machining is suitable for small batches and metal parts, but it generates more waste and is slower than injection moulding.
- Injection moulding vs. 3D printing – 3D printing is ideal for prototyping and low-volume production, while injection moulding is more cost-effective for mass production.
- Injection moulding vs. extrusion and blow moulding – Extrusion is used for continuous shapes like pipes, while blow moulding is best for hollow products like bottles.
Each method has its advantages, but injection moulding remains the most efficient for high-volume plastic parts.
Sustainability and Waste Reduction in Injection Moulding Plastic Part
With growing concerns about environmental impact, manufacturers are adopting sustainable practices:
- Using recycled materials – Many companies are incorporating recycled plastics to reduce waste and lower costs.
- Energy-efficient machines – Modern injection moulding machines consume less power, making production more sustainable.
- Biodegradable plastics – New materials like bioplastics offer eco-friendly alternatives without compromising performance.
These sustainability efforts not only help the environment but also contribute to long-term cost savings.
Conclusion: Maximizing Cost Savings with Injection Moulding Plastic Part
Injection moulding plastic part remains one of the most economical and scalable solutions for manufacturing plastic components. By optimizing design, selecting the right materials, and leveraging automation, businesses can achieve high-quality results while keeping production costs low. Whether producing millions of parts or just a few thousand, injection moulding offers a cost-effective, reliable, and efficient manufacturing solution.