- March 13, 2025
- Posted by: feinuojixie
- Category: Injection Molding News
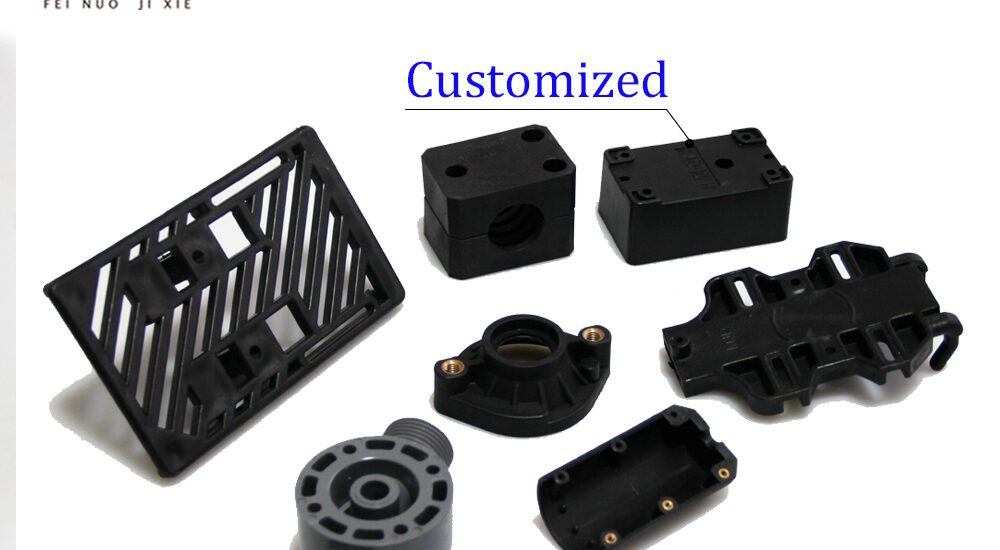
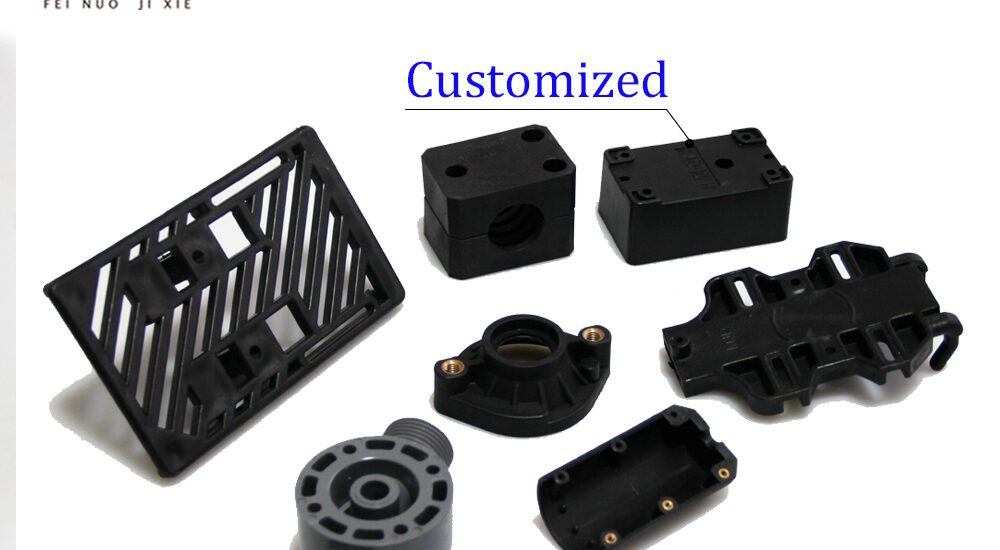
ABS injection moulding has become a cornerstone of modern plastic manufacturing, offering a perfect balance of durability, cost-effectiveness, and design flexibility. ABS plastic, known for its strength and impact resistance, is widely used in industries ranging from automotive to consumer electronics. With the ability to produce high-quality plastic parts efficiently and consistently, ABS injection moulding has gained immense popularity among manufacturers.
This article explores why ABS injection moulding is the best choice for producing high-quality plastic parts. By understanding its process, material benefits, cost advantages, and industry applications, businesses can make informed decisions when selecting the right plastic manufacturing method.
Understanding ABS Injection Moulding
ABS injection moulding is a manufacturing process that involves injecting molten ABS plastic into a mould cavity, where it cools and solidifies into the desired shape. This method is widely used due to its efficiency in producing precise, high-quality plastic parts with minimal waste.
ABS (Acrylonitrile Butadiene Styrene) is a thermoplastic polymer known for its exceptional mechanical properties. It offers high impact resistance, good chemical stability, and an attractive surface finish, making it ideal for a wide range of applications. Industries such as automotive, electronics, and consumer goods heavily rely on ABS injection moulding to create durable and visually appealing products.
Superior Material Properties of ABS Plastic
One of the main reasons ABS injection moulding is the best choice for high-quality plastic parts is the outstanding properties of ABS plastic itself.
- High impact resistance and durability: ABS plastic is tough and resistant to physical impact, making it perfect for applications requiring strength and longevity.
- Excellent dimensional stability: The material retains its shape and size under various conditions, ensuring consistency in moulded parts.
- Good resistance to chemicals and temperature fluctuations: ABS plastic can withstand exposure to certain chemicals and moderate heat without degradation.
- Smooth surface finish: The material naturally produces a polished and aesthetically pleasing surface, reducing the need for additional finishing treatments.
These properties make ABS injection moulding an ideal choice for manufacturers looking for a strong, stable, and visually appealing plastic solution.
Efficiency and Cost-Effectiveness of ABS Injection Moulding
ABS injection moulding is a highly efficient production method that allows manufacturers to create high-quality plastic parts with precision and speed.
- High production speed: The injection moulding process can produce large quantities of parts in a short time, making it ideal for mass production.
- Consistency and accuracy: Each moulded part is identical to the next, ensuring uniformity in large-scale manufacturing.
- Minimal material waste: The process optimizes material usage, reducing waste and lowering production costs.
- Cost-effective production: Due to its fast cycle times and low labour requirements, ABS injection moulding is an economical option for producing durable plastic components.
By choosing ABS injection moulding, businesses can benefit from lower production costs while maintaining superior quality and consistency.
Design Flexibility and Customization
ABS injection moulding provides manufacturers with the flexibility to create complex and customized designs with ease.
- Ability to produce intricate shapes: The process allows for highly detailed and precise moulding, making it suitable for complex components.
- Variety of colors and finishes: ABS plastic can be easily colored or coated to meet aesthetic and branding requirements.
- Compatibility with secondary processes: ABS parts can undergo additional treatments such as painting, plating, and printing, expanding their functionality and appeal.
This versatility makes ABS injection moulding a preferred choice for industries that require both functionality and aesthetics in their plastic parts.
Applications of ABS Injection Moulding in Different Industries
Due to its superior properties, ABS injection moulding is widely used in various industries:
- Automotive: ABS plastic is used for dashboards, interior trims, and structural components due to its strength and lightweight nature.
- Electronics: Many consumer electronics, such as laptop casings and smartphone covers, rely on ABS injection moulding for durability and design flexibility.
- Consumer goods: Items like household appliances, luggage, and toys benefit from the aesthetic appeal and impact resistance of ABS plastic.
- Medical devices: The chemical resistance and safety of ABS plastic make it suitable for medical-grade applications, such as equipment housings and laboratory tools.
This broad range of applications highlights the importance of ABS injection moulding in producing high-quality plastic parts across multiple sectors.
Sustainability and Environmental Benefits of ABS Injection Moulding
As industries move toward more sustainable manufacturing practices, ABS injection moulding plays a role in reducing environmental impact.
- Recyclability: ABS plastic can be recycled and reused, making it a more sustainable choice compared to other plastics.
- Energy-efficient production: The injection moulding process optimizes energy usage, reducing the overall carbon footprint.
- Advancements in eco-friendly ABS materials: Researchers are developing biodegradable and bio-based alternatives to traditional ABS plastic, further improving its sustainability.
By incorporating recycled materials and energy-efficient processes, ABS injection moulding aligns with modern sustainability goals while maintaining high-quality production standards.
Why ABS Injection Moulding Is the Best Choice for High-Quality Plastic Parts
ABS injection moulding offers a combination of durability, efficiency, and design flexibility, making it the ideal choice for high-quality plastic parts.
- Its superior material properties ensure strength, impact resistance, and dimensional stability.
- The efficiency and cost-effectiveness of the process make it suitable for large-scale production.
- Its design versatility allows for customization and aesthetic enhancements.
- The widespread use of ABS injection moulding across industries proves its reliability and adaptability.
For businesses looking for a high-performance plastic manufacturing solution, ABS injection moulding remains the best option. Its balance of quality, affordability, and sustainability makes it a top choice for manufacturers worldwide.