- March 13, 2025
- Posted by: feinuojixie
- Category: Injection Molding News
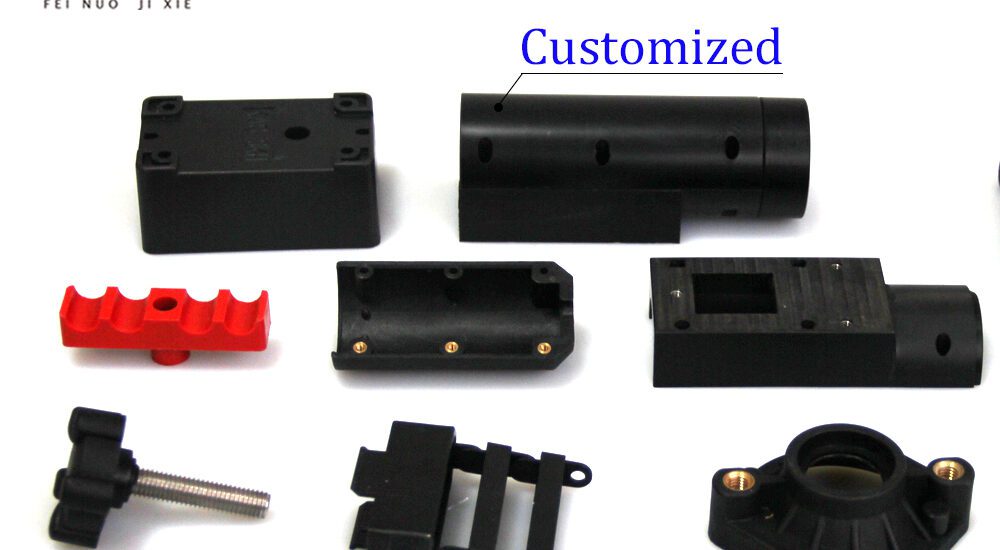
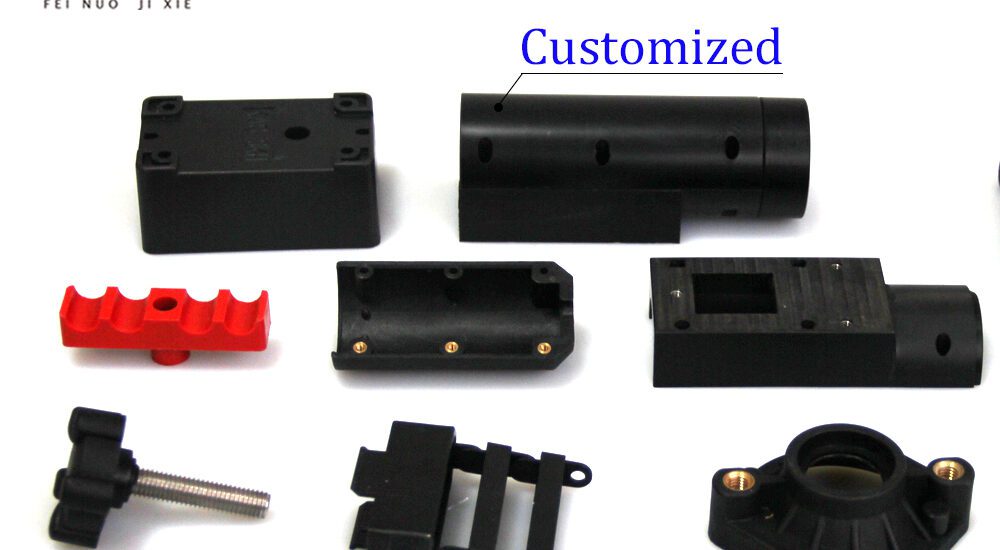
ABS injection moulding is a widely used manufacturing process known for its durability, precision, and cost-effectiveness. But how does it compare to other plastics in terms of performance and application? This article explores what makes ABS injection moulding unique, its benefits, and how it stands out from alternative plastic materials.
Understanding ABS Injection Moulding
What Is ABS Injection Moulding?
Acrylonitrile Butadiene Styrene (ABS) is a thermoplastic polymer used in various industries due to its strength, flexibility, and ease of processing. Injection moulding is the process of heating ABS to a molten state and injecting it into a mould to create precise and high-quality plastic components. This method is highly efficient and ensures uniformity in mass production.
How ABS Injection Moulding Works
The process follows these key steps:
- Melting the Material – ABS pellets are heated until they reach a molten state.
- Injection into the Mould – The molten ABS is injected into a pre-designed mould cavity at high pressure.
- Cooling and Solidification – The moulded part is cooled to allow it to harden and take shape.
- Ejection and Finishing – Once fully formed, the part is ejected and may undergo minor finishing processes like trimming or surface treatments.
This method ensures consistent results, making ABS injection moulding a preferred choice for manufacturers.
Advantages of ABS Injection Moulding
Exceptional Strength and Durability
ABS is well known for its impact resistance and toughness, making it ideal for applications requiring a high level of structural integrity. It does not crack or break easily, making it superior to many other plastics in terms of strength.
High-Quality Surface Finish
One of the main advantages of ABS injection moulding is the smooth and polished finish it provides. The natural properties of ABS allow for easy post-processing, including painting, plating, and texturing. This makes it an excellent choice for products requiring an attractive appearance.
Cost-Effectiveness in Mass Production
ABS injection moulding is a cost-effective manufacturing solution, especially for high-volume production. The material itself is relatively affordable, and the injection moulding process allows for fast and efficient production with minimal waste.
Chemical and Heat Resistance
ABS offers good resistance to chemicals, oils, and heat, making it suitable for use in demanding environments. It can withstand moderate temperatures without deforming, adding to its versatility in various industries.
Comparing ABS Injection Moulding to Other Plastics
ABS vs. Polypropylene (PP)
- ABS is stronger and more rigid than PP, which is known for its flexibility.
- ABS provides a higher-quality surface finish, while PP has better chemical resistance.
- ABS is preferred for structural components, whereas PP is widely used in packaging and disposable products.
ABS vs. Polycarbonate (PC)
- ABS is more cost-effective than PC, which is often more expensive.
- PC offers higher impact resistance, but ABS is easier to process and mould into complex shapes.
- ABS is used for consumer goods, while PC is often found in applications requiring extreme durability, such as safety glasses and bulletproof materials.
ABS vs. Polyethylene (PE)
- ABS is more rigid and heat-resistant, whereas PE is softer and more chemically resistant.
- PE is commonly used in lightweight applications such as plastic bags, while ABS is chosen for more durable products.
ABS vs. PVC (Polyvinyl Chloride)
- ABS has better mechanical strength than PVC, making it suitable for impact-resistant applications.
- PVC is more weather-resistant and commonly used in outdoor and plumbing applications.
Each material has its strengths, but ABS injection moulding stands out for its combination of strength, affordability, and versatility.
Common Applications of ABS Injection Moulding
Automotive Industry
ABS is extensively used in the automotive sector for manufacturing dashboards, interior trims, and protective covers. Its durability, lightweight properties, and ability to withstand moderate heat make it a preferred choice for vehicle components.
Consumer Electronics
Many electronic devices, including laptop casings, remote controls, and gaming consoles, are made using ABS injection moulding. The material’s strength, smooth finish, and ability to be coated or plated contribute to its popularity in the electronics industry.
Household and Industrial Products
ABS is commonly found in everyday household products such as vacuum cleaner parts, power tools, and kitchen appliances. It is also used in industrial settings for manufacturing enclosures, gears, and other mechanical components due to its high impact resistance.
Sustainability and Recycling of ABS Injection Moulding
Environmental Considerations
Although ABS is derived from petroleum-based sources, its durability and long lifespan help reduce waste by extending product usability. Unlike disposable plastics, ABS products are designed to last, which contributes to sustainability.
Recycling Potential
ABS is a recyclable material, meaning it can be reprocessed and reused in the production of new plastic products. Many manufacturers implement recycling programs to reduce environmental impact, making ABS injection moulding a more sustainable choice compared to single-use plastics.
Conclusion
ABS injection moulding offers a perfect balance of strength, cost-efficiency, and versatility, making it one of the most widely used plastic manufacturing processes. Compared to other plastics, ABS stands out due to its superior durability, smooth finish, and adaptability across various industries. Whether in automotive, electronics, or consumer goods, ABS injection moulding continues to be a leading choice for manufacturers looking for high-performance plastic components.