- March 14, 2025
- Posted by: feinuojixie
- Category: Injection Molding News
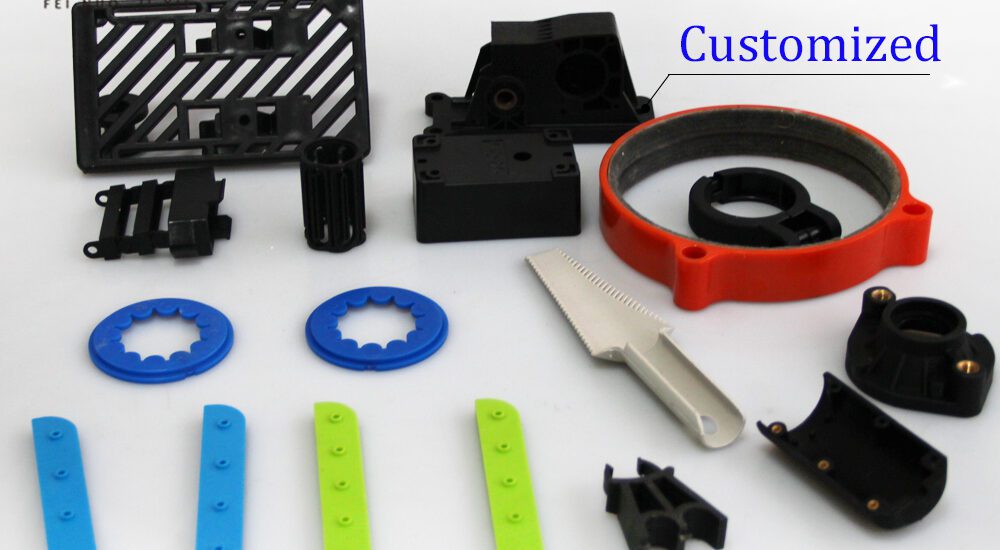
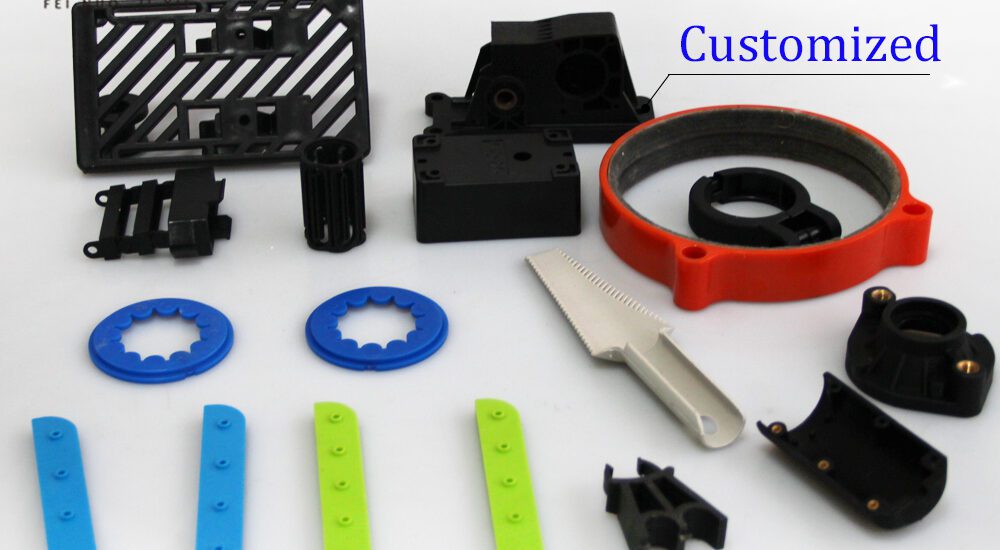
In today’s competitive manufacturing landscape, businesses are constantly looking for efficient, cost-effective, and high-quality production methods. ABS injection moulding stands out as one of the most reliable solutions for mass production, offering a perfect balance of durability, precision, and versatility. Whether in the automotive, electronics, or consumer goods industry, ABS injection moulding plays a crucial role in creating strong, lightweight, and aesthetically appealing products.
This article explores the full potential of ABS injection moulding, explaining its advantages, applications, and best practices to optimize production. By understanding the process and leveraging its benefits, businesses can enhance efficiency, reduce costs, and maintain superior product quality.
Understanding ABS Injection Moulding
ABS injection moulding is a widely used manufacturing process that transforms acrylonitrile butadiene styrene (ABS) plastic into precise and durable components. ABS is a thermoplastic polymer known for its impact resistance, toughness, and ease of processing. The injection moulding process involves heating ABS resin pellets until they become molten, injecting the material into a custom-designed mould, and allowing it to cool and solidify into the desired shape.
One of the key benefits of ABS injection moulding is its repeatability, ensuring that each product meets the same high standards. Additionally, ABS plastic’s ability to withstand mechanical stress, chemicals, and temperature variations makes it ideal for diverse industrial applications.
Key Advantages of ABS Injection Moulding for Your Business
Durability and Strength
ABS plastic is highly resistant to physical impacts, making it ideal for manufacturing products that require durability. It retains its shape and integrity even under mechanical stress, ensuring that parts remain reliable and long-lasting.
Cost-Effectiveness
Compared to other materials, ABS plastic offers an excellent cost-to-performance ratio. Its affordability, combined with the efficiency of the injection moulding process, reduces overall production costs. Businesses can benefit from high-volume manufacturing with minimal material wastage.
Design Flexibility
One of the greatest advantages of ABS injection moulding is its versatility. Manufacturers can create complex shapes, intricate designs, and fine details with high precision. This flexibility allows businesses to produce innovative and aesthetically appealing products.
Consistency and Precision
Injection moulding ensures that every part produced is uniform in size, shape, and quality. This consistency is essential for industries that require precision, such as electronics and automotive manufacturing.
Applications of ABS Injection Moulding in Different Industries
Automotive Industry
ABS injection moulding is extensively used in the automotive sector for producing dashboards, interior panels, trim components, and structural reinforcements. Its durability and lightweight properties help improve fuel efficiency and vehicle longevity.
Electronics Industry
From protective casings for smartphones and laptops to electrical enclosures, ABS plastic is a preferred material in electronics manufacturing. Its insulating properties and impact resistance make it ideal for safeguarding delicate components.
Consumer Goods
Many everyday products, including household appliances, toys, and protective gear, are made using ABS injection moulding. The material’s strength, smooth finish, and ability to hold color well contribute to its widespread use.
Medical Equipment
ABS plastic plays a significant role in medical device manufacturing, where hygiene, strength, and precision are critical. It is used for making instrument housings, surgical tools, and disposable medical components.
Optimizing ABS Injection Moulding for Maximum Efficiency
Choosing the Right Mould Design
A well-designed mould ensures smooth production and minimizes defects. Factors such as cooling channels, gate placement, and part geometry play a crucial role in mould performance.
Process Optimization
Controlling temperature, pressure, and cooling time is essential for achieving high-quality results. Proper process optimization reduces defects, improves efficiency, and enhances product durability.
Material Selection
Adding reinforcements or modifying ABS with additives can enhance its properties. UV stabilizers, flame retardants, and glass fibers can improve strength, heat resistance, and longevity.
Sustainability Considerations
Recycling ABS plastic and adopting eco-friendly manufacturing practices help reduce environmental impact. Many industries are exploring bio-based ABS alternatives to promote sustainable production.
Common Challenges and Solutions in ABS Injection Moulding
Warping and Shrinkage
Uneven cooling can cause parts to warp or shrink. Using proper cooling techniques, balanced mould designs, and optimized processing conditions can minimize these issues.
Surface Defects
Sink marks, flow lines, and rough textures can occur due to inconsistent material flow or improper mould design. Adjusting injection speed and pressure helps achieve a smooth surface finish.
Material Compatibility Issues
When combining ABS with other materials, adhesion problems may arise. Using compatible bonding techniques, such as chemical treatments or co-injection moulding, ensures strong material integration.
Future Trends in ABS Injection Moulding
Advanced Automation
The integration of robotics and artificial intelligence in injection moulding is improving production efficiency and reducing human error. Automated systems allow for real-time monitoring and quality control.
Innovative Materials
The development of reinforced ABS and biodegradable variants is opening new possibilities for eco-friendly and high-performance applications. These advancements will expand the use of ABS injection moulding in various industries.
3D Printing Integration
Hybrid manufacturing techniques that combine 3D printing with injection moulding are gaining popularity. This approach enables rapid prototyping, reducing development time and costs.
Conclusion
ABS injection moulding is a powerful manufacturing solution that offers durability, cost-effectiveness, and design flexibility. Its applications span multiple industries, from automotive and electronics to consumer goods and medical devices. By optimizing mould design, refining process parameters, and embracing new technologies, businesses can unlock the full potential of ABS injection moulding.
As industries evolve, staying ahead with advanced automation, innovative materials, and sustainable practices will ensure long-term success. Whether you are looking to enhance production efficiency, reduce costs, or improve product quality, ABS injection moulding is a strategic investment that can drive business growth and innovation.