- March 14, 2025
- Posted by: feinuojixie
- Category: Injection Molding News
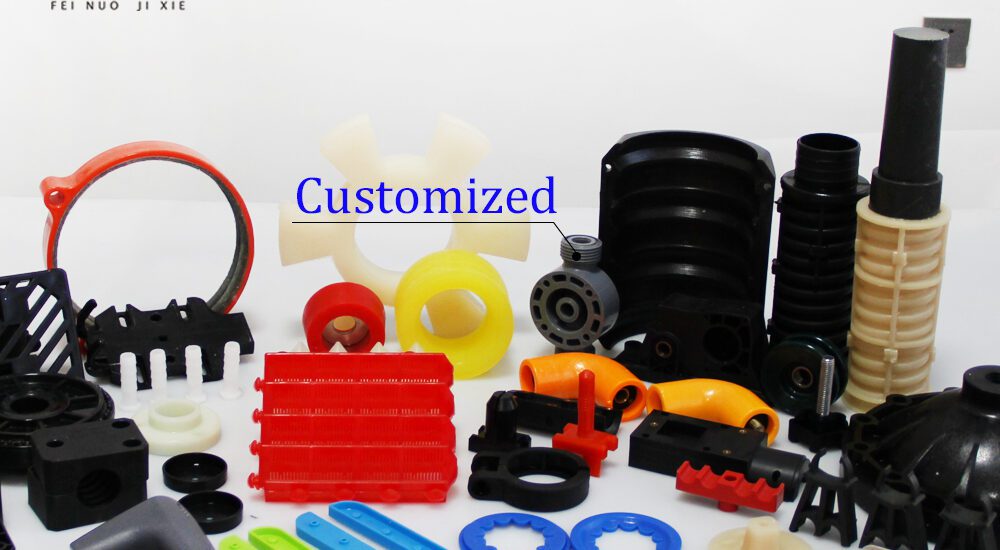
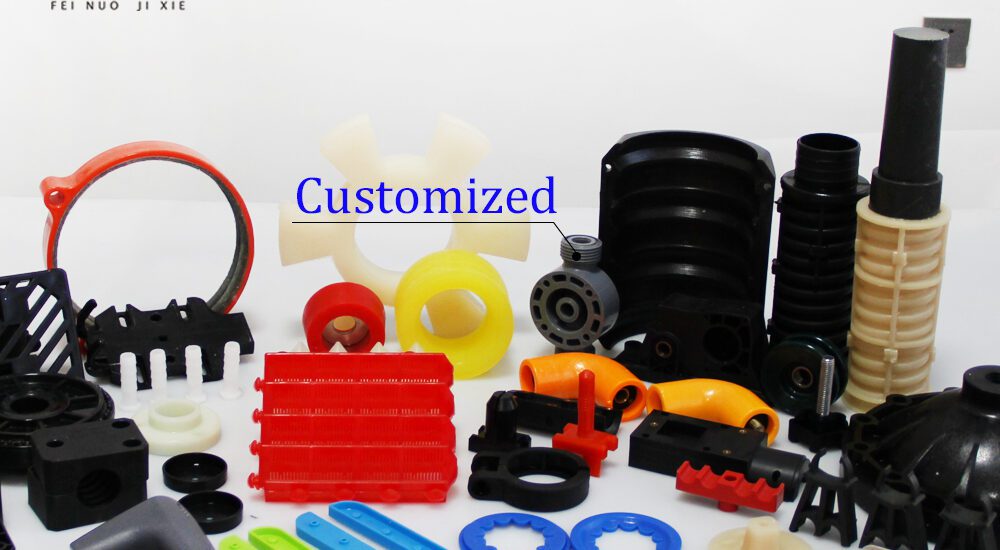
ABS injection moulding has become a game-changer in modern manufacturing, revolutionizing industries with its unique combination of durability, cost-effectiveness, and design flexibility. As businesses seek materials that provide both strength and affordability, ABS has emerged as a leading choice. From automotive components to electronic casings and medical devices, this moulding technique is enabling innovation and efficiency across multiple sectors. In this blog, we will explore the process, benefits, and industry-wide impact of ABS injection moulding, along with the latest advancements shaping its future.
What Is ABS Injection Moulding?
ABS injection moulding is a manufacturing process that utilizes Acrylonitrile Butadiene Styrene (ABS), a thermoplastic polymer known for its toughness, impact resistance, and versatility. The process involves heating ABS plastic to a molten state and injecting it into a pre-designed mould, where it cools and solidifies into the desired shape.
One of the key reasons ABS is widely used in injection moulding is its excellent balance of strength, rigidity, and lightweight properties. Unlike other plastics, ABS maintains durability while allowing for intricate designs, making it ideal for mass production. Compared to other materials like polypropylene (PP) or polycarbonate (PC), ABS offers superior surface finish, better impact resistance, and enhanced processability, making it a preferred choice for industries requiring precision and durability.
Key Advantages of ABS Injection Moulding
Durability and Strength
ABS is known for its high impact resistance, making it ideal for products that need to withstand mechanical stress. Whether in the automotive industry or consumer electronics, ABS ensures long-lasting performance, reducing the risk of cracks or breakage.
Cost-Effectiveness
ABS injection moulding is a highly efficient process, allowing for large-scale production at reduced costs. The material itself is relatively affordable, and its ability to be easily shaped and processed minimizes waste and production downtime.
Precision and Versatility
Manufacturers favor ABS for its ability to produce detailed and complex designs with high precision. The material adapts well to various surface textures and finishes, whether glossy, matte, or even metallic coatings, giving designers more freedom to create aesthetically appealing products.
Lightweight yet Sturdy
ABS provides a perfect balance between lightweight construction and mechanical strength. This makes it suitable for applications where weight reduction is crucial, such as in automotive and aerospace industries, without compromising durability.
Industries Transformed by ABS Injection Moulding
Automotive Industry
ABS injection moulding has revolutionized the automotive sector by providing lightweight, durable, and cost-efficient parts. Common applications include:
- Dashboard components – ABS is used for interior panels, ensuring both aesthetic appeal and durability.
- Exterior trim and grilles – Resistant to weather conditions and impact damage.
- Structural supports and brackets – Offering strength while reducing vehicle weight, which improves fuel efficiency.
Electronics and Appliances
ABS is widely used in the electronics sector due to its insulating properties and resistance to heat and impact. Examples include:
- Laptop and mobile phone casings – Providing a sleek, durable shell to protect sensitive components.
- Television and remote control housings – Offering strength while keeping devices lightweight.
- Kitchen appliances – Used in coffee makers, vacuum cleaners, and refrigerator parts due to its resistance to wear and tear.
Medical Equipment
The medical industry benefits from ABS injection moulding due to its hygienic, chemical-resistant, and durable nature. Some key applications are:
- Medical device casings – Used in diagnostic and monitoring equipment.
- Sterilizable medical instruments – Withstanding frequent cleaning and disinfection.
- Disposable medical components – Ensuring safe and cost-effective production.
Consumer Goods and Packaging
ABS injection moulding plays a crucial role in the production of everyday consumer products due to its aesthetic and functional versatility:
- Toys and gaming accessories – LEGO bricks, game controllers, and other durable plastic toys are made from ABS.
- Household products – Storage containers, tool handles, and decorative elements benefit from ABS’s high strength.
- Protective packaging – Ensuring fragile products remain secure during transport.
Aerospace and Defense
The aerospace industry increasingly incorporates ABS due to its lightweight and high-strength characteristics. ABS injection moulding is used for:
- Aircraft interior components – Reducing overall weight without sacrificing durability.
- Protective housings for avionics – Ensuring electronic equipment remains secure.
- Military-grade equipment – Used for robust and impact-resistant devices.
Innovations in ABS Injection Moulding Technology
3D Printing and ABS Hybrid Techniques
With advancements in additive manufacturing, ABS-based 3D printing is revolutionizing rapid prototyping. Engineers now combine traditional ABS injection moulding with 3D printing to test new designs quickly and cost-effectively before mass production.
Eco-Friendly and Recycled ABS
Sustainability is a growing concern, and manufacturers are now developing recycled ABS materials to reduce environmental impact. Innovations in bio-based ABS and biodegradable additives are paving the way for greener manufacturing solutions.
Automated and Smart Moulding Processes
The integration of AI-driven automation and robotics is making ABS injection moulding more precise, efficient, and cost-effective. These advancements allow for:
- Better quality control – AI can detect defects in real time.
- Faster production cycles – Robotics streamline the injection moulding process.
- Less material waste – Optimized moulding techniques reduce excess plastic usage.
Challenges and Future of ABS Injection Moulding
Environmental Concerns
Although ABS is recyclable, its non-biodegradable nature raises sustainability issues. The industry is actively working on better recycling methods and alternative formulations to reduce its carbon footprint.
Material Limitations
While ABS is highly durable, it may not be suitable for high-heat applications as it can deform under extreme temperatures. In such cases, alternative materials like polycarbonate or nylon might be preferred.
Future Developments
- Improved flame-retardant ABS for use in safety-critical applications.
- Advanced composite materials that combine ABS with other polymers for enhanced performance.
- New coatings and treatments to increase ABS’s resistance to UV exposure and chemicals.
Conclusion
ABS injection moulding has revolutionized manufacturing by offering durability, cost-efficiency, and design versatility. Its impact spans across automotive, electronics, medical, aerospace, and consumer goods industries, driving innovation and efficiency. With continuous advancements in sustainable materials, smart automation, and hybrid manufacturing techniques, ABS injection moulding remains at the forefront of modern industrial production. As industries evolve, this technology will continue to shape the future of manufacturing with even greater precision, sustainability, and efficiency.