- April 3, 2025
- Posted by: feinuojixie
- Category: Injection Molding News
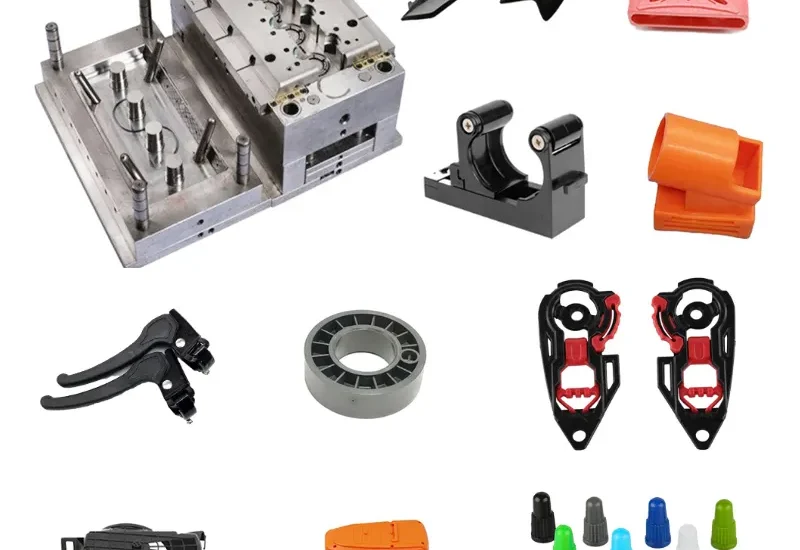
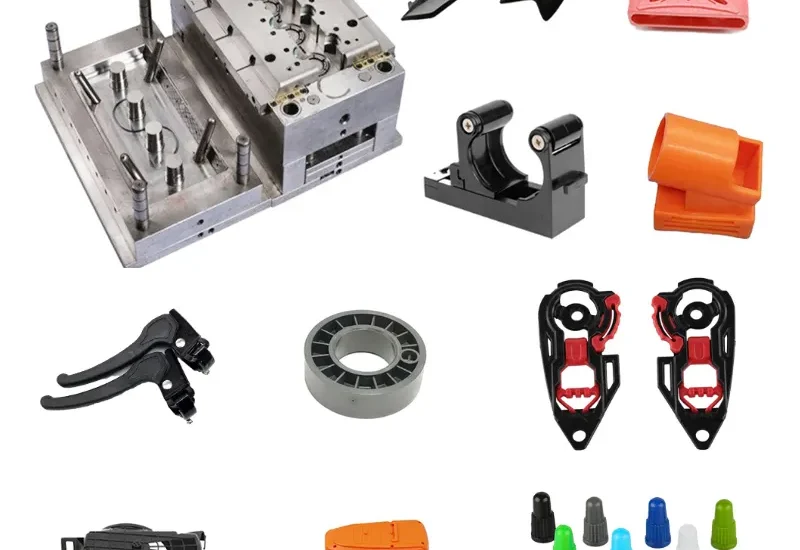
Injection machine parts play a critical role in the manufacturing of plastic products. Whether you are setting up a new production line or maintaining an existing machine, understanding these parts is essential. Selecting the right components ensures efficient operation, reduces downtime, and improves product quality. Before making a purchase, knowing what each part does and how it impacts overall machine performance can save you both time and money.
Essential Injection Machine Parts and Their Functions
To ensure smooth and efficient operation, an injection machine consists of several key components, each with a specific function. Understanding these parts is crucial for maintaining performance and making informed purchasing decisions.
Injection Unit
The injection unit is responsible for melting and injecting plastic material into the mold. Key components include:
-
Injection Barrel: This is where raw plastic material is heated and melted. A high-quality barrel ensures uniform temperature distribution.
-
Screw: The screw rotates within the barrel, mixing and pushing the melted plastic toward the nozzle. Different screw designs affect melting efficiency and material consistency.
-
Nozzle: The nozzle directs the molten plastic into the mold cavity. Choosing the right nozzle size and type is essential to prevent leakage and ensure precise injection.
Clamping Unit
The clamping unit holds the mold in place during the injection and cooling process. Its components include:
-
Clamping Mechanism: This system applies force to keep the mold tightly closed during injection. Insufficient clamping force can lead to defects in the final product.
-
Mold Plates: These plates support and align the mold halves. They must be durable and resistant to high pressure.
-
Ejector System: After the plastic has cooled and solidified, the ejector system pushes the final product out of the mold. Proper maintenance prevents sticking and ensures smooth ejection.
Hydraulic System
The hydraulic system provides the necessary pressure and movement to operate the machine. Key elements include:
-
Hydraulic Pump: Supplies the force needed to move the injection and clamping units. Pumps with high efficiency reduce energy consumption.
-
Valves and Hoses: These regulate and direct hydraulic fluid. Any leakage or blockage can lead to performance issues.
-
Actuators: Convert hydraulic pressure into mechanical motion, ensuring smooth and controlled operations.
Electrical Components
Modern injection machines rely on electronic systems to control and monitor operations. Essential electrical components include:
-
Control Panel: The interface where operators adjust machine settings and monitor performance. Advanced panels feature touchscreen displays for easier operation.
-
Sensors and Switches: These detect pressure, temperature, and position to ensure accurate and safe operation. Faulty sensors can lead to inconsistent production quality.
-
Heating Elements: Responsible for melting plastic material, these components must maintain stable temperatures for optimal molding results.
Key Considerations When Buying Injection Machine Parts
Investing in high-quality injection machine parts is essential for long-term performance and efficiency. Here are some key factors to consider:
Material Compatibility
Different plastic materials require specific machine components. For example, reinforced plastics need a wear-resistant screw and barrel, while heat-sensitive plastics require precise temperature control to prevent degradation.
Durability and Maintenance
Choosing durable parts reduces downtime and maintenance costs. Look for components made from high-strength alloys or coated with wear-resistant materials. Additionally, parts that are easy to clean and replace improve overall machine longevity.
Precision and Efficiency
The accuracy of injection machine parts directly impacts product consistency. High-precision screws, barrels, and nozzles ensure uniform material flow and minimize defects. Investing in quality components enhances productivity and reduces material waste.
Common Issues and Troubleshooting for Injection Machine Parts
Even the best machines experience issues over time. Recognizing and addressing these problems early can prevent costly repairs.
Wear and Tear on the Screw and Barrel
Continuous exposure to heat and friction can wear down the screw and barrel, leading to poor plastic melting and inconsistent injection. Regular inspections and using high-quality, wear-resistant materials can extend their lifespan.
Clamping System Failures
If the mold does not close properly, it can cause defects in the final product. Common issues include misalignment, insufficient clamping force, or worn-out components. Ensuring proper lubrication and alignment can prevent failures.
Hydraulic Leaks and Pressure Loss
Leaks in hydraulic hoses or pump failures can reduce machine performance. Regular maintenance checks and replacing worn-out seals help maintain optimal pressure levels.
Electrical Malfunctions
Faulty sensors, overheating heating elements, or damaged wiring can cause operational failures. Regular system diagnostics and upgrading to modern control systems can improve reliability.
Where to Source High-Quality Injection Machine Parts
Finding reliable suppliers is crucial for ensuring machine efficiency and longevity. Consider the following options when purchasing parts:
OEM vs. Aftermarket Parts
-
OEM (Original Equipment Manufacturer) Parts: These are produced by the machine’s manufacturer and offer guaranteed compatibility and quality. However, they can be more expensive.
-
Aftermarket Parts: These are made by third-party manufacturers and often come at a lower price. While some aftermarket parts offer great value, it is important to verify their quality and compatibility.
Trusted Suppliers and Manufacturers
Look for suppliers with a strong reputation in the industry. Consider factors like product warranties, customer reviews, and technical support availability before making a purchase.
Customization Options
For specialized applications, custom-designed parts may be necessary. Some manufacturers offer tailored solutions to optimize performance based on specific production needs.
Conclusion
Understanding the breakdown of injection machine parts is essential before making a purchase. From the injection and clamping units to the hydraulic and electrical components, every part plays a crucial role in machine performance. Investing in high-quality, compatible, and durable parts ensures efficiency, reduces maintenance costs, and enhances product consistency. By carefully considering material compatibility, sourcing from reliable suppliers, and performing regular maintenance, you can maximize the lifespan of your injection machine and achieve optimal manufacturing results.