- April 7, 2025
- Posted by: feinuojixie
- Category: Injection Molding News
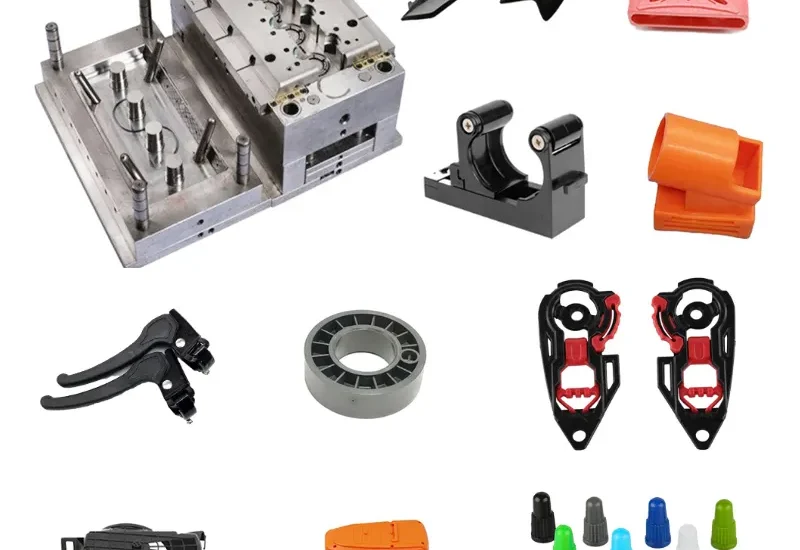
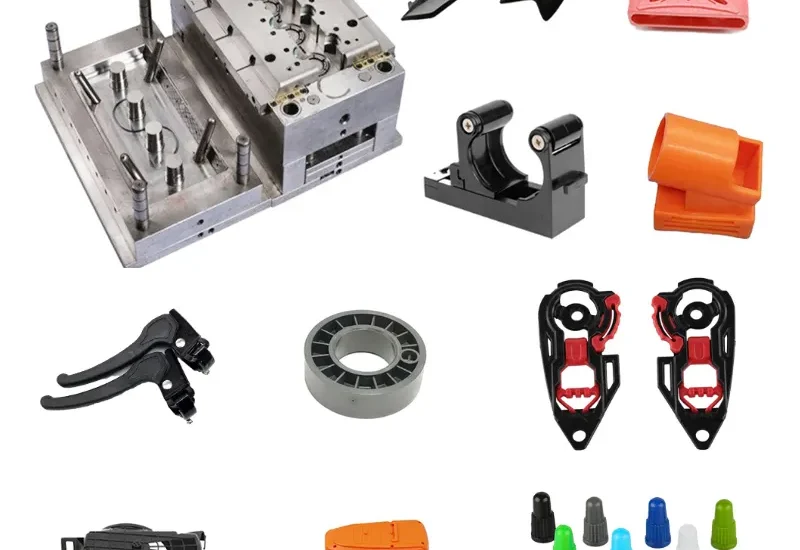
In today’s fast-paced manufacturing world, plastic injection molding part is at the heart of countless products—from the case of your smartphone to components in your car. These parts are manufactured using one of the most efficient and scalable processes available: plastic injection molding. Despite their ubiquity, many designers, engineers, and even product developers only scratch the surface of how these parts are created and optimized.
Understanding the key aspects of a plastic injection molding part not only helps in achieving better performance and cost-efficiency but also opens doors to innovation in design and functionality. Whether you’re new to the field or looking to sharpen your technical knowledge, knowing these essential facts can dramatically change how you approach manufacturing with plastic. From choosing the right material to understanding how mold design affects final quality, this guide uncovers everything you need to know to make informed, smart decisions.
What Is a Plastic Injection Molding Part?
A plastic injection molding part is a component created by injecting molten plastic into a custom-designed mold. Once cooled and solidified, the part is ejected from the mold, ready for use. This process allows for high-volume production of highly detailed and consistent parts with minimal post-processing required.
Used across industries like automotive, medical, aerospace, and consumer electronics, plastic injection molding part offers unmatched scalability and design flexibility. The process supports complex geometries and tight tolerances, making it ideal for both functional and aesthetic components. Understanding the process behind it lays the foundation for evaluating quality, performance, and design potential.
The Precision Advantage: Why Tolerance Matters in a Plastic Injection Molding Part
Precision is a critical factor in the success of a plastic injection molding part. Tolerances define how closely the final part matches its design specifications, and even a small deviation can cause misalignment, poor fit, or failure during assembly.
In high-performance applications—such as medical devices or aerospace connectors—tight tolerance control ensures that parts function as intended and interact correctly with other components. Manufacturers use advanced tooling and machinery to achieve tolerances as fine as ±0.001 inches. Knowing the importance of precision helps guide both design choices and communication with suppliers.
Material Selection Is Everything: Choosing the Right Resin for Your Plastic Injection Molding Part
The performance of a plastic injection molding part heavily depends on the resin selected. Different thermoplastics have different mechanical, thermal, and chemical resistance properties. For instance, ABS is commonly used for consumer electronics due to its strength and finish, while polycarbonate offers impact resistance for safety equipment.
Other factors include cost, processability, and environmental resistance. For high-heat applications, materials like PEEK or PPS might be preferred. A well-matched material ensures the part performs under stress, lasts longer, and aligns with the final product’s intended use.
The Role of Mold Design in a High-Quality Plastic Injection Molding Part
The mold is the blueprint of every plastic injection molding part. A poorly designed mold can lead to defects, uneven cooling, or inefficient cycle times. Mold design includes aspects like parting lines, gate types, runner systems, and ejection methods.
A robust mold should allow for uniform material flow, minimize air traps, and ensure consistent temperature distribution. Collaboration between designers and mold makers early in the development phase can significantly improve the quality and lifespan of both the mold and the final part.
Cycle Time Efficiency: The Hidden Factor That Impacts Plastic Injection Molding Part Cost
Cycle time—the duration of a complete injection molding cycle—directly impacts the cost of each plastic injection molding part. The faster the cycle, the more parts produced per hour, reducing unit cost.
However, cycle time shouldn’t be rushed at the expense of quality. Balancing speed with proper cooling, material flow, and mold filling ensures that parts come out correctly without compromising performance. Automated systems and optimized tooling help achieve efficient cycle times with minimal waste.
Surface Finish and Texture: Enhancing the Look and Feel of a Plastic Injection Molding Part
A plastic injection molding part isn’t just about performance—it’s also about appearance and user experience. Surface finish options range from glossy and smooth to textured and matte, depending on mold treatment and material.
These finishes affect not only aesthetics but also functionality. For example, a textured grip on a tool handle enhances usability, while a smooth finish on a housing adds visual appeal. Finishes can also hide minor defects or make post-processing like painting easier. The right texture elevates the perceived quality of the end product.
Common Defects Found in a Plastic Injection Molding Part and How to Prevent Them
Even with the best planning, defects can occur. Common issues include:
Sink marks: caused by uneven cooling or thick wall sections
Warping: due to internal stresses or poor cooling
Short shots: incomplete filling of the mold
Flash: excess material that leaks from the mold cavity
Preventing defects involves proper mold design, precise temperature and pressure control, and consistent material quality. Regular maintenance of molds and monitoring of production parameters go a long way in ensuring part reliability.
Quality Control Is Non-Negotiable: Testing a Plastic Injection Molding Part
Quality control is essential to verify that each plastic injection molding part meets specifications. Common inspection techniques include:
Visual inspection for surface flaws or warping
Dimensional checks using calipers or CMM machines
Functional testing for stress, impact, or heat resistance
Documentation and traceability are also important in regulated industries. Establishing robust quality protocols reduces risk and ensures that every part leaving the production line meets its performance standards.
Sustainability and Recycling: The Future of Plastic Injection Molding Part
Sustainability is becoming a major priority. Many manufacturers now use recyclable thermoplastics or biodegradable alternatives. Scrap plastic from the injection process can often be reground and reused, reducing waste.
In addition, advancements in energy-efficient machinery and the use of digital twins are optimizing production with minimal environmental impact. A plastic injection molding part designed with lifecycle and recyclability in mind contributes to greener manufacturing.
Real-World Applications: Where You’ll Find a Plastic Injection Molding Part in Everyday Life
You encounter plastic injection molding part every day, whether you realize it or not. Examples include:
Automotive: dashboards, trim components, under-the-hood parts
Medical: syringes, diagnostic devices, housings
Consumer electronics: smartphone cases, remote controls, chargers
Home appliances: knobs, panels, water filter housings
Its versatility allows for use in virtually every industry. Knowing where and how these parts are used offers inspiration for new designs and product innovations.
Mastering the Plastic Injection Molding Part Landscape
Plastic injection molding part continues to shape the modern manufacturing world—literally. With unmatched precision, scalability, and design flexibility, it remains one of the most powerful tools available to engineers and product developers. From understanding the impact of material selection to recognizing the role of quality control, each of these ten facts provides insight into optimizing your design and production strategy.
Whether you’re developing a new product, refining an existing one, or simply looking to improve your knowledge, mastering these key aspects will put you on the path to creating better, stronger, and more cost-effective parts. Don’t overlook the power and potential packed into every molded piece of plastic—it might just be the foundation of your next big innovation.