- April 7, 2025
- Posted by: feinuojixie
- Category: Injection Molding News
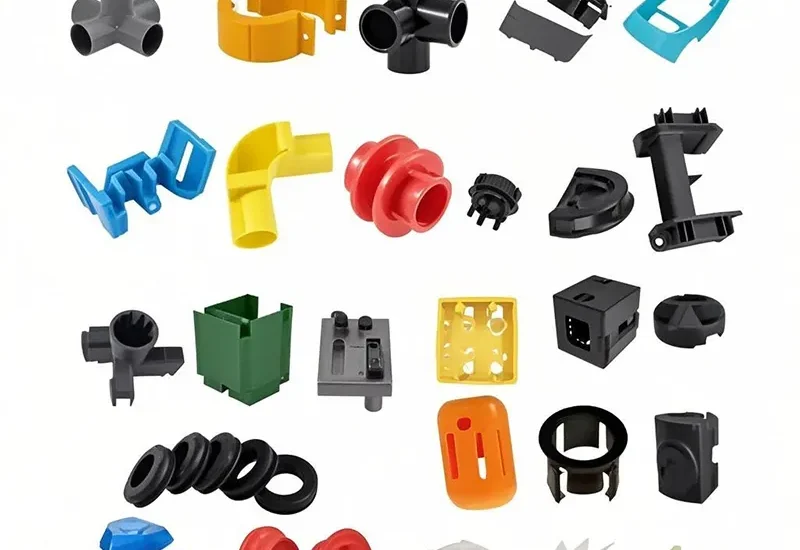
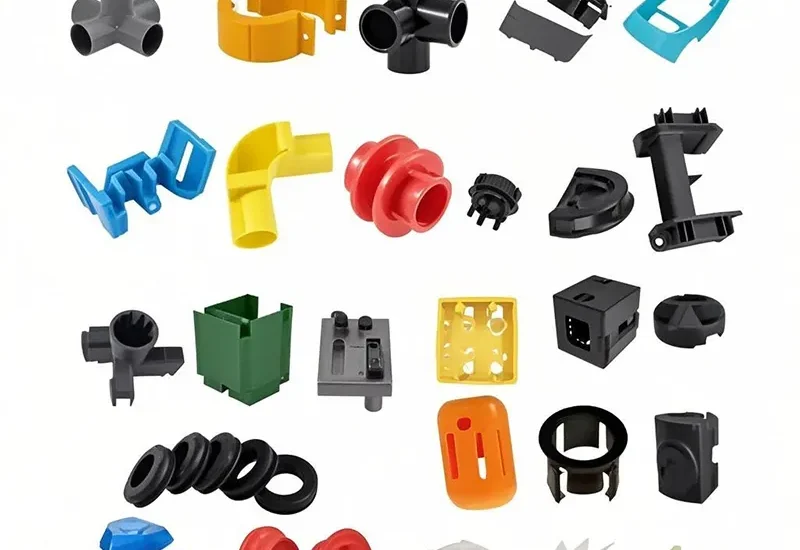
In today’s fast-paced and competitive industrial landscape, manufacturers are constantly looking for ways to streamline production while maintaining top-tier quality. One of the most significant breakthroughs driving this transformation is the use of plastic injection molding parts. These components have evolved far beyond simple plastic shapes—they now represent precision, efficiency, and scalability in manufacturing. From automotive assemblies to consumer electronics, plastic injection molding parts are redefining what’s possible on the factory floor. Their ability to reduce production costs, enhance design possibilities, and meet exacting quality standards makes them a vital cornerstone of modern production processes.
The Fundamentals of Plastic Injection Molding Parts
Understanding the process behind plastic injection molding parts reveals why they are such a manufacturing marvel. At its core, the technique involves injecting molten plastic into a precisely machined mold cavity, where it cools and solidifies into the final shape. This method supports high-volume production with minimal waste and offers a high degree of accuracy. Whether the part is small and intricate or large and robust, the process ensures consistency across every single piece. This repeatability is crucial for industries where tolerances are tight and quality control is non-negotiable.
Precision and Consistency: A New Standard in Manufacturing
One of the defining strengths of plastic injection molding parts is their unparalleled precision. Once the mold is created, each part can be replicated with microscopic accuracy. This consistency is particularly valuable in sectors like aerospace, medical devices, and electronics, where even the slightest deviation can lead to failure. Engineers rely on this process to ensure that every component fits perfectly, functions as intended, and meets rigorous regulatory standards. This level of quality, combined with rapid output, positions plastic injection molding as a gold standard in modern manufacturing.
Cost-Effective Production Without Compromising Quality
While the upfront cost of creating a mold can be high, the long-term savings offered by plastic injection molding parts are significant. Once the mold is in place, thousands—or even millions—of identical parts can be produced at a low cost per unit. Additionally, the process minimizes material waste through precise injection, and labor costs are reduced thanks to automation. This makes it an ideal solution for companies aiming to scale production without inflating budgets. The result is a high-quality product that is both affordable and efficient to manufacture.
Design Flexibility That Encourages Innovation
Plastic injection molding parts offer incredible design freedom. Engineers and designers can create highly complex geometries that would be difficult or impossible to achieve with traditional manufacturing methods. Features such as undercuts, threaded inserts, and intricate surface textures can be easily integrated into the mold. This flexibility accelerates product development cycles, supports rapid prototyping, and enables customization. By removing design limitations, injection molding inspires innovation and creativity across a wide range of industries.
Durability and Performance in End-Use Applications
Despite being lightweight, plastic injection molding parts can deliver impressive mechanical performance. Advanced polymer materials used in the process can be tailored to offer high strength, impact resistance, thermal stability, and chemical durability. This makes them suitable for demanding applications such as automotive engine components, electrical housings, and medical instruments. In many cases, these parts can match or even exceed the performance of their metal counterparts—while offering additional advantages like corrosion resistance and easier handling.
Sustainability in Modern Manufacturing
Sustainability has become a top priority for manufacturers, and plastic injection molding parts support this shift in several key ways. First, the precision of the process minimizes material waste. Second, many thermoplastics used in injection molding are recyclable, allowing manufacturers to repurpose scrap material. Some companies are also exploring biodegradable plastics and bio-based resins to reduce environmental impact. By optimizing resource use and supporting greener material options, plastic injection molding plays a vital role in building more sustainable supply chains.
Applications Across Industries
The versatility of plastic injection molding parts is evident in their widespread use across industries. In the automotive world, they are found in dashboards, connectors, and under-the-hood components. In healthcare, they enable the production of sterile syringes, implants, and diagnostic equipment. Consumer electronics rely on injection molded parts for everything from smartphone casings to internal circuit board mounts. Even household products like kitchenware and toys benefit from this technology. The adaptability of the process ensures that no matter the industry, there is a solution that fits.
Automation and Speed: Meeting the Demands of Today’s Market
In an era where time-to-market can make or break a product, plastic injection molding parts offer unmatched speed and automation. Once the mold is prepared, the entire process can run continuously with minimal human intervention. Modern injection molding machines are equipped with smart sensors and robotics that monitor quality, optimize efficiency, and reduce downtime. This level of automation ensures consistent output while keeping pace with global demand. Companies can bring products to market faster, meet tight deadlines, and maintain a competitive edge.
Future Outlook: How Plastic Injection Molding Parts Will Shape Tomorrow’s Manufacturing
As manufacturing evolves, so too will the role of plastic injection molding parts. Advances in materials science are introducing new high-performance polymers with unique properties. The integration of artificial intelligence and machine learning into the molding process is opening new doors for predictive maintenance and intelligent design optimization. Additive manufacturing is also merging with injection molding to create hybrid processes that offer the best of both worlds. With these innovations on the horizon, plastic injection molding is poised to remain at the forefront of manufacturing technology for decades to come.
The Backbone of Modern Manufacturing
Plastic injection molding parts are more than just components—they are the foundation of a smarter, faster, and more efficient manufacturing world. Their ability to combine precision, cost-efficiency, and adaptability makes them an indispensable part of countless industries. As companies continue to seek out ways to innovate and compete globally, injection molding will play an ever-expanding role. Whether you’re a manufacturer, designer, or product developer, understanding the power of plastic injection molding parts is key to staying ahead in the modern industrial revolution.