- April 8, 2025
- Posted by: feinuojixie
- Category: Injection Molding News
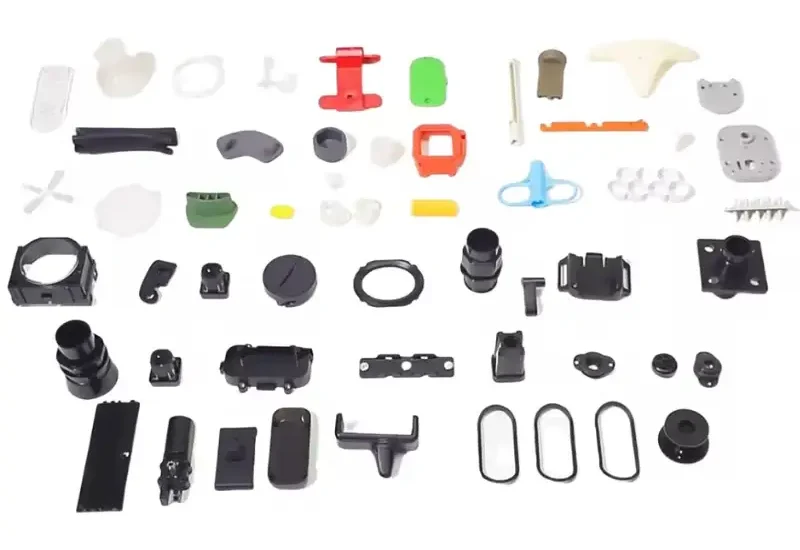
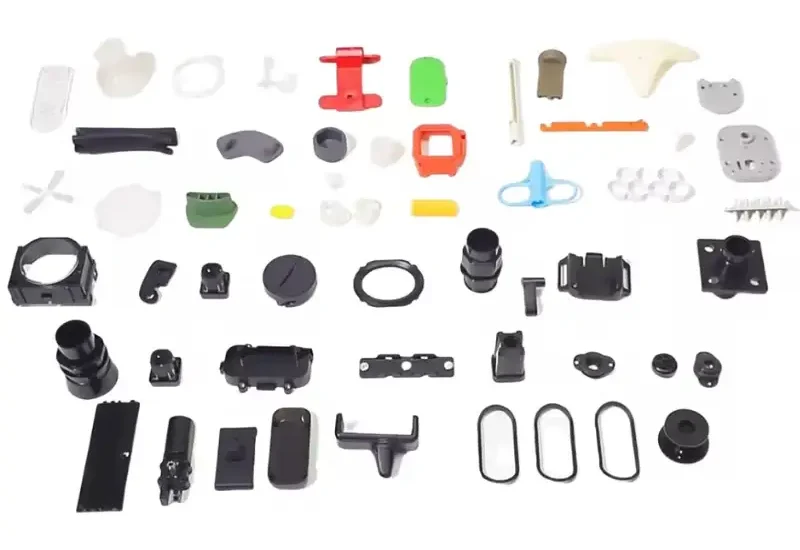
In today’s highly competitive automotive landscape, manufacturers are under constant pressure to deliver high-performance parts at a lower cost and with faster turnaround times. One technology that’s rapidly reshaping the way components are made is injection molding automotive parts. This innovative process offers a powerful combination of speed, efficiency, and precision, allowing automakers to meet increasing demands without sacrificing quality.
From intricate interior trims to rugged under-the-hood components, injection molding is enabling the creation of parts that are not only strong and lightweight but also highly customizable. More importantly, it’s revolutionizing how the industry approaches mass production, with benefits that ripple through design, manufacturing, logistics, and sustainability.
As automakers race toward electrification, autonomy, and smarter mobility, injection molding has become a central technology in crafting the next generation of vehicles. In this article, we explore how this process is driving a silent revolution in auto part production—making it faster, cheaper, and better than ever before.
The Basics of Injection Molding in Automotive Part Manufacturing
Injection molding is a manufacturing process where molten material, typically a thermoplastic polymer, is injected into a mold cavity. Once cooled and solidified, the part is ejected, resulting in a precisely shaped component. In the context of automotive part production, this technique has become indispensable.
The process is favored for its ability to create consistent, high-precision parts with complex geometries that would be difficult or expensive to produce using traditional methods like machining or casting. Injection molding automotive parts has not only accelerated production cycles but also allowed manufacturers to maintain tight tolerances and repeatability—critical in safety-focused automotive applications.
Today’s advanced molding machines can produce a single part in seconds, making them ideal for both high-volume runs and just-in-time manufacturing. With customizable molds, manufacturers can pivot quickly between different parts or design iterations, ensuring agility in a fast-evolving market.
Speed and Scale: Meeting the Demands of Modern Auto Production
Automotive manufacturing demands speed—vehicles are assembled on tight schedules, and every part must arrive on time and to specification. Injection molding automotive parts fits this model perfectly, enabling high-speed production without sacrificing quality.
Modern injection molding machines utilize automation, robotics, and multi-cavity molds to produce several parts simultaneously. Cycle times can be as short as a few seconds, allowing for tens of thousands of identical components to be manufactured in a single day.
Furthermore, this scalability means manufacturers can meet rising consumer demand while keeping production costs under control. The ability to ramp up or scale down with minimal retooling also offers a competitive advantage in an industry known for rapid product cycles and shifting trends.
Cost Efficiency Through Material Optimization and Process Precision
Cost remains a major consideration in automotive part production, and injection molding delivers strong savings on multiple fronts. The molds, though initially expensive, are highly durable and reusable, dramatically reducing long-term tooling expenses.
Material usage is also optimized—molded parts are created with minimal excess, and leftover plastics can often be recycled and reused. In addition, precise control over temperature, pressure, and injection speed means less scrap and fewer defective parts.
Injection molding automotive parts also opens the door to using advanced thermoplastics and composites that offer excellent mechanical properties while remaining affordable. These materials help reduce vehicle weight—improving fuel efficiency and complying with environmental regulations—all while keeping production budgets in check.
Design Flexibility and Performance Enhancement
The versatility of injection molding means engineers can push the limits of design without compromising manufacturability. Complex shapes, integrated features, and tight tolerances are all achievable, allowing for consolidated parts that eliminate the need for multiple assembly steps.
For example, parts like air intake manifolds, instrument panels, and headlamp housings are frequently made using injection molding. These components benefit from reduced weight, improved aerodynamics, and enhanced durability—all crucial for performance and longevity.
Injection molding automotive parts also supports overmolding and insert molding techniques, enabling multiple materials or components to be combined in a single mold. This enhances functionality, reduces assembly time, and often improves aesthetics—a key consideration in vehicle interiors.
Sustainability and Eco-Friendly Innovation in Injection Molding
As the automotive industry embraces greener practices, injection molding is evolving to support sustainability goals. Many manufacturers are incorporating recycled polymers and bio-based materials into their processes, minimizing the environmental footprint of each component.
Energy-efficient machinery and process automation help reduce electricity consumption and waste generation. Additionally, innovations like waterless cooling and closed-loop systems are becoming standard, making injection molding an environmentally responsible choice.
For automakers, using injection molding automotive parts means not only meeting regulatory requirements but also appealing to eco-conscious consumers who expect sustainability to be built into every level of vehicle design and production.
Real-World Case Studies: Injection Molding Driving Success
Across the globe, automotive giants and tier-1 suppliers are reaping the benefits of injection molding. For instance, a leading electric vehicle manufacturer has adopted the process for its battery housing units, leveraging high-strength polymers to reduce weight without compromising safety.
Another automaker has used injection molding to produce modular dashboard systems, cutting production time by 30% and enabling easy customization across multiple vehicle models. In yet another case, a supplier used the technique to produce underbody shields that are both lightweight and corrosion-resistant—an ideal solution for electric vehicle platforms.
These examples illustrate the widespread and growing reliance on injection molding automotive parts, not just for economic reasons, but for innovation and competitive differentiation as well.
The Future of Automotive Manufacturing: Smart Factories and Advanced Molding Technologies
The next frontier for injection molding in automotive production lies in digital integration and material science. Smart factories are utilizing real-time sensors, predictive analytics, and AI-driven quality control systems to enhance every aspect of molding operations.
New materials such as carbon-fiber-reinforced polymers and heat-resistant composites are expanding the range of parts that can be injection molded. Hybrid molding methods that combine 3D printing with traditional molding are also emerging, offering unmatched flexibility and customization.
As vehicles become smarter, lighter, and more connected, the demand for innovative parts made through injection molding will only grow. The process is poised to play a central role in shaping the next generation of automotive design and manufacturing.
Embracing the Injection Molding Revolution
Injection molding automotive parts is no longer a niche solution—it’s the backbone of modern vehicle manufacturing. Its unmatched speed, cost-effectiveness, and design capabilities are helping automakers meet the challenges of today and prepare for the innovations of tomorrow.
Whether it’s reducing weight for better fuel efficiency, enabling bold new designs, or improving sustainability, injection molding is at the heart of a manufacturing revolution. By embracing this technology, automotive companies can drive forward with confidence—faster, cheaper, and better than ever before.