- April 8, 2025
- Posted by: feinuojixie
- Category: Injection Molding News
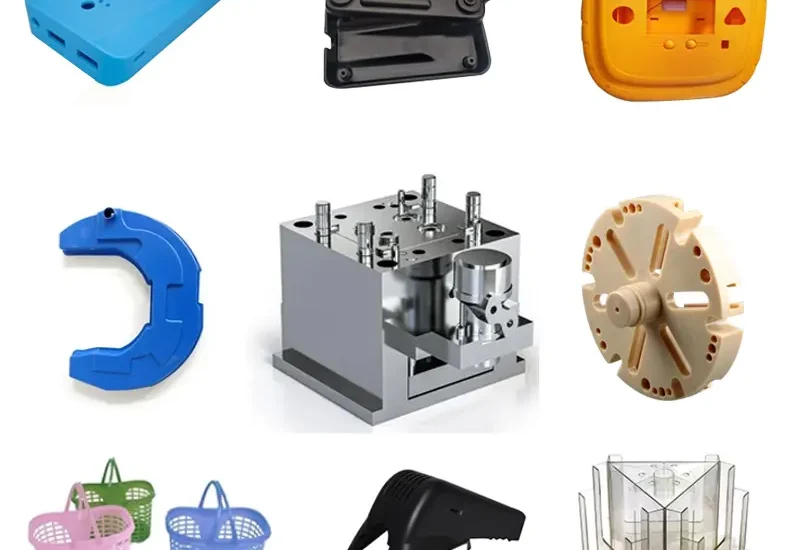
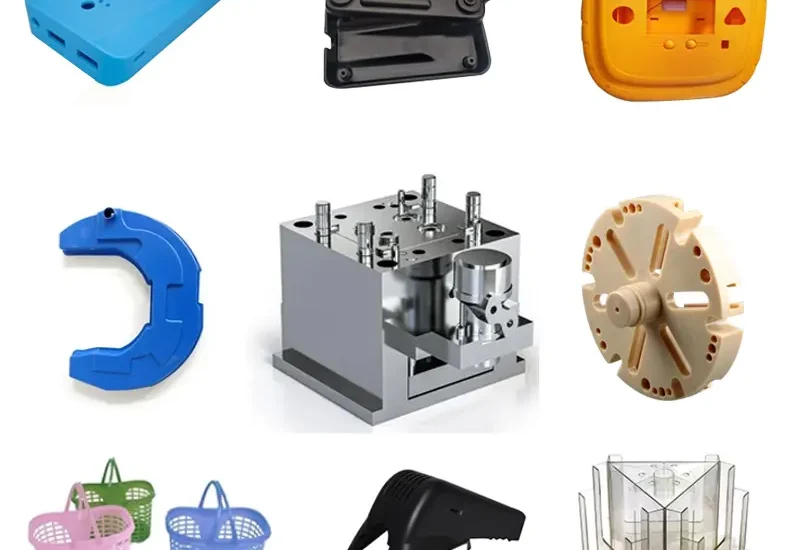
The automotive industry is undergoing a profound transformation. From the rise of electric vehicle to the integration of smart technology, innovation is reshaping the way vehicles are designed, built, and driven. At the core of this revolution lies a quiet but powerful process—injection molding automotive part. No longer just a technique for producing plastic toys or consumer goods, injection molding has become a cornerstone in modern automotive manufacturing. Automakers are embracing this method for its unmatched combination of light weight, high durability, design flexibility, and production efficiency. As the demand grows for cars that are fuel-efficient, environmentally friendly, and built to last, injection molded components are proving to be a key enabler in meeting these challenges. This article explores how injection molding is driving innovation across the automotive world, delivering smarter solutions from bumper to dashboard.
The Basics of Injection Molding in the Automotive World
Injection molding is a manufacturing process that involves injecting molten material—typically thermoplastic—into a mold to form a specific shape. Once cooled, the part is ejected and ready for use. In the automotive industry, this method allows for the precise creation of complex shapes and intricate designs that would be costly or impossible with traditional metal fabrication. Injection molding automotive part can be produced in large volumes with consistent quality, making it an ideal choice for both interior and exterior components. The process also supports a wide variety of material, enabling customization based on strength, flexibility, and temperature resistance requirements.
Why Lightweight Matter: Fuel Efficiency and Performance Gains
One of the most significant advantages of using injection molding in automotive design is weight reduction. Traditional steel or aluminum parts are often heavy, contributing to higher fuel consumption and reduced efficiency. By contrast, injection molding automotive part is significantly lighter, helping manufacturers reduce the overall vehicle weight. This directly impacts fuel economy, making cars more efficient and environmentally friendly. In electric vehicles, lighter components mean extended battery life and improved performance. Beyond fuel savings, a lighter vehicle also accelerates faster, handles better, and brakes more effectively—benefits every driver can appreciate.
Durability Without Compromise: How Injection Molded Part Stand the Test of Time
Despite being lighter, injection molded automotive part offers impressive strength and durability. Modern thermoplastics and composite material used in the molding process are engineered to withstand extreme temperatures, mechanical stress, and environmental exposure. These parts resist corrosion, impact, and UV radiation, making them ideal for both under-the-hood applications and exposed exterior areas. Whether it’s a grille, engine cover, or structural bracket, the durability of these components ensures long-term reliability and safety. Automakers can confidently replace traditional metal parts with molded alternatives without sacrificing quality.
Design Flexibility: Unleashing Creativity in Automotive Engineering
Injection molding offers a level of design freedom that is hard to match. Complex geometries, intricate textures, and seamless integration with other parts are all possible with this process. Designers can create parts that are not only functional but also visually appealing and ergonomic. This flexibility allows for the integration of multiple features into a single component, reducing the number of individual parts needed and simplifying assembly. Injection molding automotive part also supports rapid prototyping, enabling manufacturers to iterate quickly and bring innovative designs to market faster.
Cost Efficiency and Mass Production Advantages
In a competitive industry like automotive manufacturing, cost control is essential. Injection molding automotive part helps companies reduce production expenses in several ways. First, the ability to produce large quantities of identical parts lowers per-unit costs. Second, cycle times are short, meaning more parts can be made in less time. Third, less labor is required thanks to automation and streamlined processes. Over time, the initial investment in molds pays off through lower operational costs and fewer material wastage. For high-volume manufacturing, injection molding is not just efficient—it’s essential.
Eco-Friendly Innovation: Sustainable Material and Reduced Waste
As sustainability becomes a priority, injection molding offers significant environmental benefits. Many thermoplastic material used in the process are recyclable, meaning excess or defective parts can be reprocessed rather than discarded. The process also generates minimal scrap compared to metalworking. Some manufacturers are even exploring the use of biodegradable or bio-based plastic for certain applications. By choosing injection molding automotive part, companies can reduce their carbon footprint, minimize waste, and align with global efforts toward greener manufacturing.
Real-World Applications: Common Injection Molded Part in Modern Vehicle
Injection molded parts can be found throughout today’s vehicles, both inside and out. In the interior, molded components include dashboards, door panels, center consoles, seat frames, and air vent housings. Under the hood, parts like battery trays, fuse boxes, engine covers, and air intake systems are often made with molded thermoplastics. On the exterior, bumpers, grilles, light housings, and mirror casings are all commonly produced using this method. These components demonstrate the wide-ranging versatility and reliability of injection molding automotive part in real-world scenarios.
Future Outlook: The Growing Role of Injection Molding in Next-Gen Vehicle
Looking ahead, the role of injection molding in automotive design is set to expand even further. With the rise of electric vehicle, there’s a growing need for lightweight and heat-resistant components that support battery systems and electronics. Autonomous vehicle will also require new sensor housings, interior modules, and connectivity structures—all of which are well-suited to injection molding. Advances in material science, such as high-performance composites and conductive polymers, will unlock even more possibilities. As technology evolves, injection molding automotive part will remain at the forefront of innovation, shaping the next generation of smarter, cleaner, and more efficient vehicles.
The Smart Choice for a Smarter Automotive Industry
From lightweight construction to high-performance durability and eco-conscious production, injection molding automotive part is helping redefine what’s possible in vehicle design. It combines engineering precision with economic efficiency, allowing automakers to meet the evolving demands of modern transportation. As the industry continues to innovate, one thing is clear: injection molding is not just a method—it’s a movement. For manufacturers and consumers alike, it represents a smarter, more sustainable future on the road ahead.