- April 9, 2025
- Posted by: feinuojixie
- Category: Injection Molding News
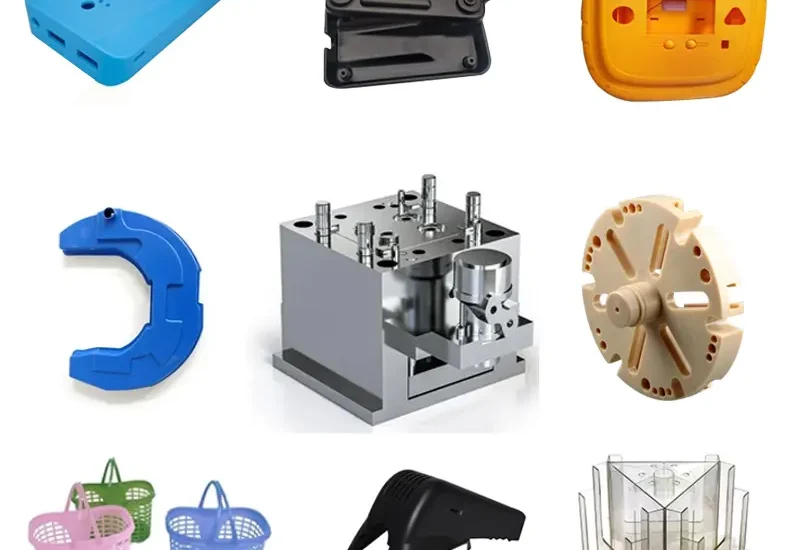
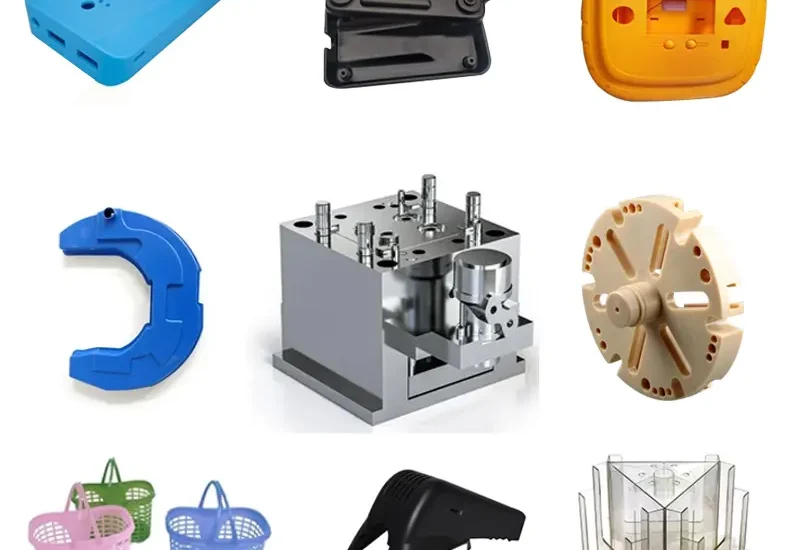
The automotive industry is in the midst of a technological revolution, and one of the most impactful innovations reshaping this sector is injection molding. This advanced manufacturing process has become a go-to solution for producing complex and durable automotive components with unmatched precision. From dashboards to air vents, injection molding automotive parts are becoming increasingly common in modern vehicle design. As manufacturers strive to meet higher standards of efficiency, performance, and sustainability, injection molding is emerging as a key player. In this blog, we’ll explore the top benefits of using injection molding for automotive components and how this technique is transforming the future of vehicle production.
Precision Engineering: How Injection Molding Automotive Parts Enhance Accuracy
One of the defining advantages of injection molding is its ability to produce automotive components with exceptional accuracy. The process allows for tight tolerances and intricate geometries, which are critical in ensuring optimal performance and safety in vehicles. Whether it’s a small gear or a dashboard panel, injection molding automotive parts maintain uniform dimensions from the first unit to the last. This level of precision is particularly important in the automotive industry, where even the slightest deviation can affect overall vehicle functionality.
Material Versatility: Wide Range of Options for Injection Molding Automotive Parts
Injection molding offers access to a broad spectrum of materials tailored to different automotive needs. Thermoplastics, glass-filled polymers, and advanced composites can all be used depending on the part’s performance requirements. Whether manufacturers need materials that are heat-resistant, impact-tolerant, or lightweight, the flexibility of this process delivers. This material diversity ensures that injection molding automotive parts can meet the demands of various applications, from interior trims to under-the-hood components.
Cost Efficiency: Reducing Manufacturing Costs with Injection Molding Automotive Parts
Injection molding stands out for its cost-effectiveness, especially in high-volume production. Once the mold is created, each part can be reproduced quickly and consistently with minimal manual labor. This scalability dramatically reduces the cost per unit, making it a smart long-term investment for automotive manufacturers. Additionally, the process generates very little material waste, and any excess material can often be recycled, further reducing production costs.
Design Flexibility: Customization Possibilities for Injection Molding Automotive Parts
Modern vehicles demand innovative designs and integrated functionality, and injection molding rises to the challenge. Engineers can incorporate intricate details, varying wall thicknesses, and even multi-material combinations into a single component. This flexibility allows designers to optimize injection molding automotive parts for aesthetics, performance, and ease of assembly. The ability to customize shapes and integrate multiple features into one part also reduces the need for secondary processes and fasteners.
High Production Speed: Fast Turnaround for Injection Molding Automotive Parts
In the automotive sector, speed to market can be a game-changer. Injection molding is capable of producing thousands of identical parts in a matter of hours. With cycle times often under a minute, it supports fast, continuous production without compromising on quality. This makes it ideal for automotive companies looking to meet tight deadlines and high demand. Injection molding automotive parts can be manufactured and delivered efficiently, keeping supply chains moving smoothly.
Lightweight Solutions: Reducing Vehicle Weight with Injection Molding Automotive Parts
Reducing vehicle weight has become a top priority for improving fuel efficiency and lowering emissions. Injection molding enables the use of high-strength yet lightweight materials that replace heavier metal components. Parts like bumpers, interior panels, and engine covers are now commonly produced using reinforced plastics. By utilizing injection molding automotive parts, manufacturers can achieve significant weight reduction without sacrificing durability or safety, directly contributing to better vehicle performance.
Consistency and Repeatability: Uniform Quality in Injection Molding Automotive Parts
Consistency is crucial in the automotive industry, and injection molding delivers it flawlessly. Once the mold is finalized, the process ensures that every part produced meets the same specifications. This repeatability reduces quality control issues and guarantees that each injection molding automotive part performs reliably in its intended application. It also enhances the brand’s reputation by ensuring uniform quality across all production batches.
Sustainability Focus: Eco-Friendly Trends in Injection Molding Automotive Parts
As sustainability becomes a global priority, injection molding is adapting to support greener manufacturing practices. Many automotive companies are now using biodegradable or recycled plastics, along with energy-efficient machinery, to lower their environmental footprint. The closed-loop nature of some systems allows for scrap material to be reprocessed and reused. Injection molding automotive parts are increasingly contributing to a more sustainable production cycle without compromising on strength or quality.
Why Injection Molding is the Future of Automotive Component Manufacturing
The use of injection molding in the automotive industry is not just a trend—it’s a technological evolution. With its unmatched precision, speed, design versatility, and cost efficiency, injection molding automotive parts are revolutionizing vehicle manufacturing. From reducing environmental impact to enabling innovative designs, this method offers solutions that align perfectly with the industry’s future goals. As the demand for smarter, lighter, and more sustainable vehicles continues to grow, injection molding will remain at the heart of automotive innovation.