- April 10, 2025
- Posted by: feinuojixie
- Category: Injection Molding News
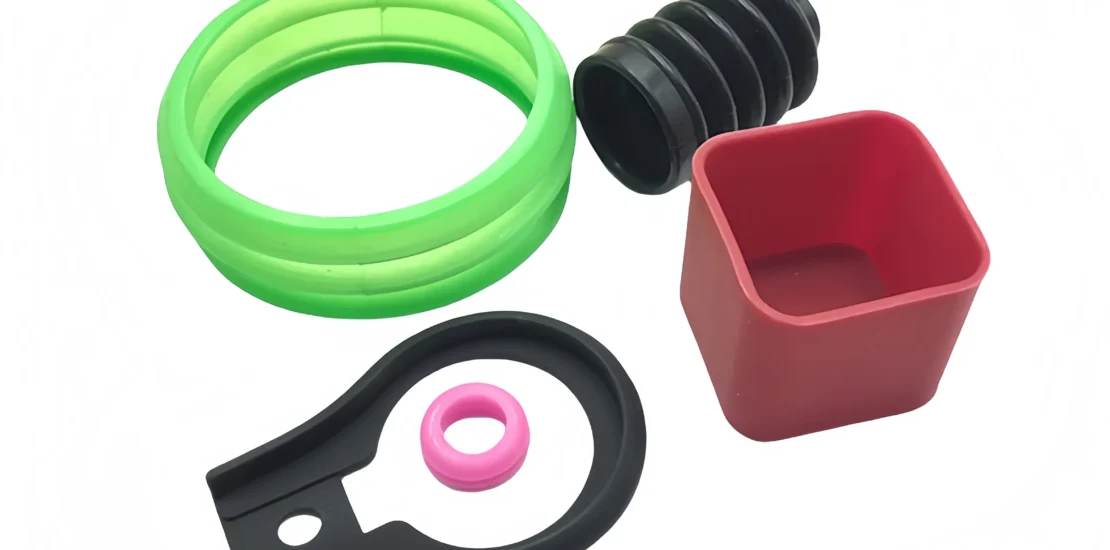
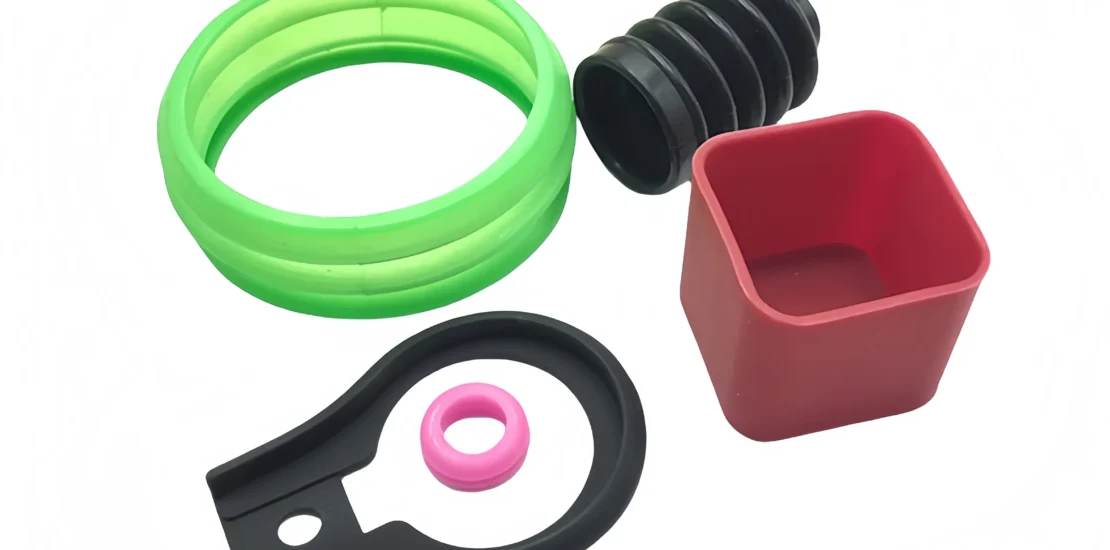
Plastic injection molding part has become a cornerstone of modern manufacturing, offering precision, repeatability, and scalability across industries. From consumer electronics to automotive components, it allows companies to produce complex parts at high volumes with impressive accuracy. However, as competition grows and margins tighten, it’s not enough to simply use this technology—it must be used wisely.
This blog post is designed to guide manufacturers, engineers, and product developers through the key strategies that can reduce cost while enhancing the quality of their plastic injection molding part. By focusing on smart design, proper material selection, efficient cycle management, and strong manufacturing partnerships, businesses can unlock significant savings while delivering superior products. Whether you’re launching a new product or looking to improve an existing one, the principles outlined here will help you get more out of every molded part.
Understanding the Basics of Plastic Injection Molding Part
To optimize savings and quality, it’s essential to understand how the plastic injection molding process works. The cycle begins with designing the part and mold, followed by tooling, material selection, and finally, high-pressure injection of molten plastic into a custom mold cavity. Once cooled, the solidified part is ejected and the cycle repeats.
Each stage in this process affects the overall cost and quality. Mistakes in the early design phase can lead to expensive mold reworks or defective parts. Similarly, inefficient tooling or incorrect material choice can increase cycle times and create inconsistencies. Mastering these fundamentals is the first step toward producing high-quality plastic injection molding part at a lower cost.
Design Smart: How Part Design Impacts Cost and Quality
The design of your plastic injection molding part can significantly influence both production cost and end-product performance. A poorly designed part often leads to material waste, warping, or complex mold structures that raise manufacturing expenses.
Key design principles include maintaining uniform wall thickness to prevent uneven cooling, using draft angles to ease part ejection, and minimizing intricate features that require more complex mold tooling. By collaborating early with your mold manufacturer or design engineer, you can identify areas for simplification that improve manufacturability without sacrificing functionality. Smart design ultimately results in lower production costs and fewer defects.
Tooling Strategies: Investing Right in Your Mold for Long-Term Savings
Tooling is often the most significant upfront investment in plastic injection molding part production, but it also plays a critical role in long-term efficiency. High-quality molds made from hardened steel can run millions of cycles with minimal maintenance, making them ideal for large production volumes.
Choosing the correct number of cavities is another cost-saving factor. A multi-cavity mold increases throughput, while a family mold allows for simultaneous production of multiple part variations. Though these options may raise initial costs, they dramatically reduce cost-per-part in the long run.
Additionally, investing in precision tooling ensures consistent part dimensions, reducing the need for post-processing or quality rechecks. Over time, a well-made mold will save money and reduce waste.
Material Matters: Choosing the Right Resin for Cost and Performance
The material you select affects every aspect of your plastic injection molding part—from cost to durability. While some resins are budget-friendly, others offer specific properties like high impact resistance, flexibility, or chemical resistance, which might be crucial depending on your application.
ABS, polypropylene, and polycarbonate are common choices, each with unique benefits. Using reinforced or filled materials can improve strength but may also increase tooling wear or extend cycle times.
Partnering with an experienced material supplier or consultant can help you balance price and performance. In some cases, blending virgin and recycled materials can also offer cost savings without compromising quality.
Cycle Time Optimization: The Secret to Efficient Plastic Injection Molding Part
Cycle time directly impacts your production rate and overall cost. Even small reductions in cycle time can lead to major savings over large runs. One of the most effective ways to shorten cycle time is through mold design—features like optimized cooling channels or hot runner systems ensure faster, more uniform part cooling.
Automation can also help. Using robotic arms for part removal or in-line inspection not only speeds up the process but reduces the risk of human error. Additionally, refining your injection molding parameters—such as pressure, temperature, and cooling duration—can reduce wasted time and energy.
By focusing on cycle time, manufacturers can increase output while lowering operating costs.
Quality Control Techniques to Avoid Costly Defects in Plastic Injection Molding Part
Defects can be expensive, not just due to scrap and rework costs but also because of potential reputational damage. Establishing robust quality control measures is key to consistent production.
This starts with preventive strategies like mold flow analysis and design for manufacturability (DFM) checks. During production, tools such as in-mold sensors, pressure monitoring, and vision inspection systems can detect problems in real-time, allowing quick corrective action.
Statistical process control (SPC) methods can further ensure that the plastic injection molding part stays within tolerances. Proactive quality control minimizes waste, reduces downtime, and keeps customer satisfaction high.
Partnering with the Right Manufacturer: How It Can Save You Time and Money
Your choice of injection molding partner can make or break your project’s success. A reliable manufacturer brings technical expertise, streamlined processes, and transparency that drive both cost efficiency and product quality.
Look for partners with in-house tooling capabilities, a strong track record, and certifications such as ISO 9001. Ask about their experience with similar plastic injection molding part and whether they offer design support or prototyping services.
The best manufacturers act as collaborators, helping you identify cost-saving opportunities and anticipating potential challenges. A strong partnership ensures smoother communication, fewer production issues, and better end results.
Sustainability and Waste Reduction: An Overlooked Cost-Saving Opportunity
Sustainability in injection molding isn’t just about environmental impact—it’s also a path to financial savings. Reducing material waste, optimizing energy usage, and recycling scrap can all lead to lower production costs.
For example, using regrind material where possible can lower material expenses. Designing molds that minimize runner waste or adopting closed-loop water cooling systems also reduces operational costs.
Many customers today value eco-conscious production, which can translate into brand loyalty and competitive advantage. Embracing sustainable practices with your plastic injection molding part benefits both your bottom line and the environment.
Make Smarter Choices with Plastic Injection Molding Part
Producing high-quality plastic injection molding part doesn’t have to come at a premium. By taking a strategic approach—starting with smart design, investing in reliable tooling, optimizing materials and cycle time, enforcing strong quality controls, and working with the right manufacturing partner—you can achieve superior results while staying within budget.
Efficiency, precision, and sustainability are not just ideals—they’re actionable goals. With the right planning and execution, your plastic injection molding part can become a powerful asset in delivering both cost savings and product excellence. Now is the time to rethink your approach and take your manufacturing strategy to the next level.