- April 14, 2025
- Posted by: feinuojixie
- Category: Injection Molding News
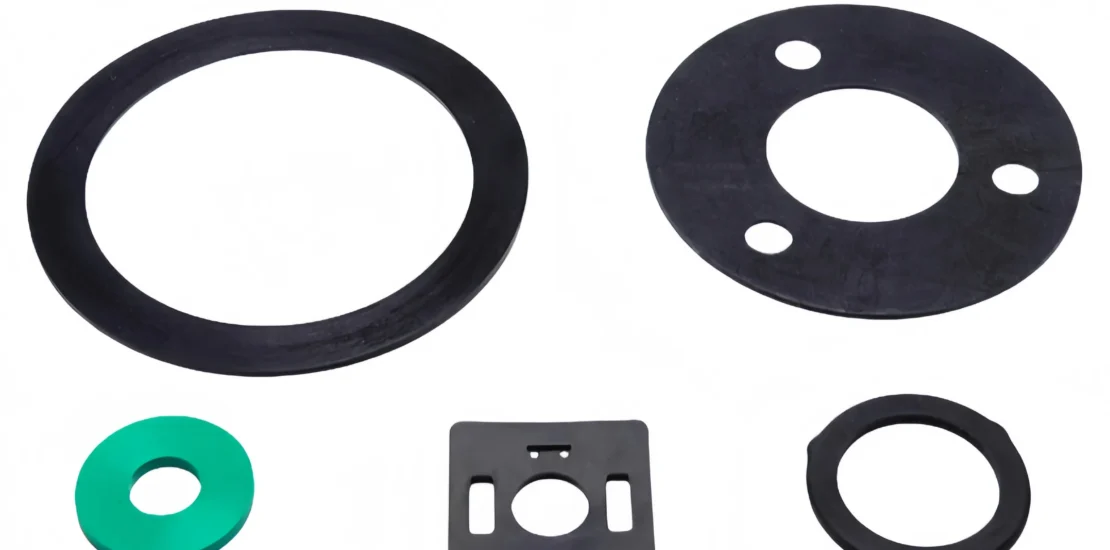
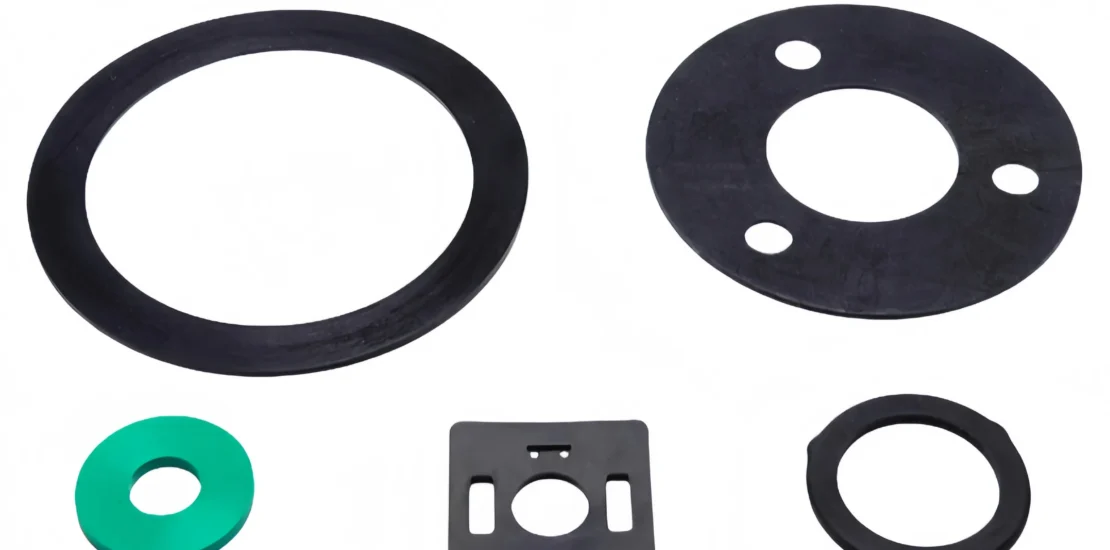
The automotive industry is undergoing a transformation, driven by rapid advancements in materials, design, and manufacturing technology. Among these innovations, plastic injection molding parts are becoming a cornerstone of modern vehicle design. These components are not only helping manufacturers meet ever-tightening efficiency standards but are also enabling new levels of creativity, comfort, and performance. From sleek interior trims to complex under-the-hood elements, plastic injection molding is redefining how cars are built and experienced. This article explores how this versatile technology is transforming the very DNA of automotive design.
The Evolution of Automotive Design and the Rise of Plastic Injection Molding
Automotive design has come a long way from the heavy, metal-dominated vehicles of the past. As consumer expectations for fuel efficiency, safety, and sleek aesthetics increased, so did the demand for innovative manufacturing methods. Plastic injection molding parts have emerged as a game-changer, offering engineers and designers a lightweight yet durable alternative to traditional materials. The shift to plastic was not just about replacing metal—it was about unlocking new design possibilities that were previously unachievable due to limitations in material flexibility and processing methods.
Precision and Complexity: Why Plastic Injection Molding Is Ideal for Modern Vehicles
Today’s vehicles are engineering marvels composed of thousands of parts that must fit together seamlessly. Plastic injection molding enables the creation of highly complex components with microscopic precision. Whether it’s a gear mechanism, a ventilation grille, or a control panel, these parts demand exact specifications to function properly and integrate smoothly. Injection molding allows manufacturers to replicate fine details consistently across massive production volumes, ensuring that every part meets the highest standards without the need for extensive post-processing or modification.
Weight Reduction and Fuel Efficiency Through Plastic Injection Molding Parts
Weight reduction is critical in automotive design as it directly impacts fuel efficiency, performance, and emissions. Replacing heavy metal parts with plastic injection molding parts allows carmakers to shed significant weight without sacrificing strength or durability. A lighter vehicle consumes less fuel, accelerates more efficiently, and reduces the strain on components such as brakes and suspension. As regulations around fuel consumption and emissions continue to tighten, plastic injection molding provides a practical solution for meeting these challenges while maintaining superior design quality.
Enhancing Aesthetics and Ergonomics in Car Interiors
The look and feel of a car’s interior are essential for brand identity and user satisfaction. Plastic injection molding parts are instrumental in creating ergonomic, visually appealing interiors that are both functional and stylish. With this technology, designers can experiment with smooth curves, textured surfaces, and integrated features like cup holders and control panels. The ability to add color and texture during the molding process eliminates the need for additional treatments, resulting in a cleaner manufacturing process and a premium finish that appeals to consumers.
Cost-Effective Production and Scalability for Automotive Manufacturers
In the competitive automotive market, efficiency and cost control are paramount. Plastic injection molding is ideally suited for high-volume production, where tooling costs are offset by low per-unit costs. Once a mold is created, manufacturers can produce thousands or even millions of identical plastic injection molding parts with minimal variation. This repeatability ensures uniform quality and reduces production errors, while also speeding up assembly times and reducing waste. The scalability of injection molding supports both mass-market vehicles and specialized models, offering flexibility to automakers of all sizes.
Durability and Performance in Challenging Conditions
Automotive parts must perform reliably in a variety of demanding environments—extreme heat, cold, moisture, and mechanical stress. Modern plastic injection molding parts are engineered to withstand these conditions thanks to advanced polymers and reinforced materials. Whether installed in engine compartments, exterior trims, or undercarriage systems, these parts maintain their structural integrity and functionality over time. Their resistance to corrosion, impact, and UV radiation makes them ideal for both internal and external applications in automotive design.
The Role of Advanced Materials and Smart Technology Integration
As vehicles become more connected and technologically advanced, so too must their components. Plastic injection molding supports the integration of sensors, LEDs, and circuit pathways directly into the part itself through processes like overmolding. This allows for the creation of smart components—such as illuminated controls or touch-sensitive panels—without the need for separate enclosures or wiring systems. Additionally, the availability of high-performance thermoplastics expands the range of use cases, from structural applications to electronic housing.
Sustainability in Automotive Design: Recycling and Green Materials
Sustainability is no longer optional—it’s a priority for automakers and consumers alike. Plastic injection molding contributes to greener vehicle production by utilizing recyclable and biodegradable materials, as well as energy-efficient molding techniques. Many manufacturers are adopting closed-loop systems that repurpose scrap materials directly back into production. Furthermore, bio-based plastics are becoming more prevalent, reducing the industry’s reliance on fossil-based resources. These sustainable practices not only help meet environmental regulations but also strengthen a brand’s commitment to eco-friendly innovation.
Future Outlook: What’s Next for Automotive Design with Plastic Injection Molding
The future of automotive design is closely tied to the evolution of plastic injection molding. As digital modeling, automation, and smart manufacturing tools advance, the production of plastic injection molding parts will become even more precise, efficient, and innovative. Emerging trends like 3D-printed molds and AI-driven defect detection are poised to redefine how designers and engineers approach vehicle development. Combined with material breakthroughs and growing demand for lightweight, customizable solutions, injection molding will continue to be a driving force behind the cars of tomorrow.
The Road Ahead for Innovative Vehicle Design
Plastic injection molding parts are more than just components—they are catalysts for innovation in automotive design. From enabling lightweight construction and smart features to supporting sustainability and mass customization, this manufacturing method is reshaping the future of mobility. As the industry accelerates toward electrification, autonomy, and greater user personalization, plastic injection molding stands at the forefront, offering limitless possibilities for creative, efficient, and forward-thinking automotive engineering.