- April 16, 2025
- Posted by: feinuojixie
- Category: Injection Molding News
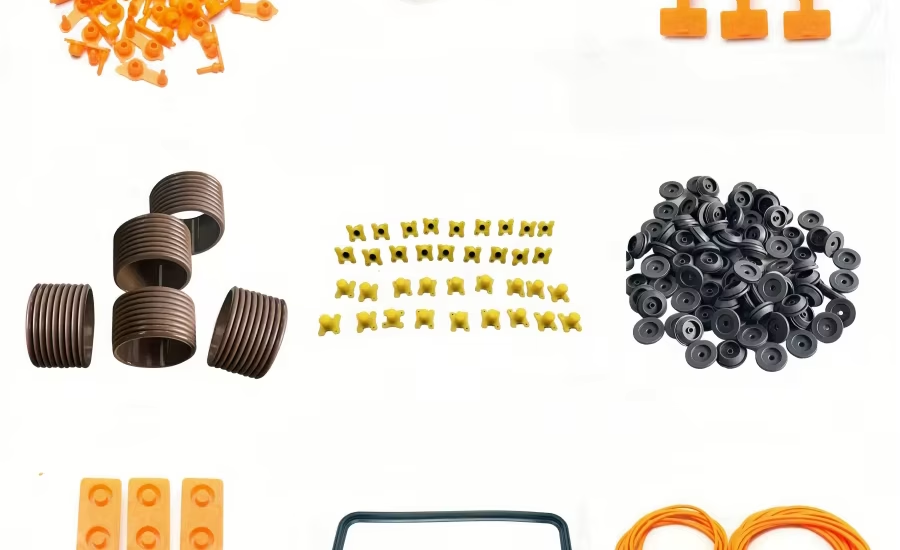
In the ever-evolving world of manufacturing, some technologies make loud, attention-grabbing entrances. Others, like injection molding parts, work behind the scenes—quietly transforming how industries operate. From automotive to aerospace, electronics to healthcare, injection molding parts have become the unsung heroes of modern production. They bring precision, repeatability, and cost-efficiency to an industry that increasingly demands all three. Whether you’re holding a sleek smartphone or driving a car packed with performance components, chances are you’re experiencing the result of an expertly engineered injection molding part. As manufacturers continue to search for ways to innovate without inflating costs, injection molding has become a cornerstone of progress—efficient, scalable, and ready to shape the future.
The Basics of Injection Molding Parts and How They Work
Injection molding parts are created through a highly efficient process that involves injecting molten material into a pre-designed mold. Once the material cools and solidifies, the mold opens, and the finished part is ejected. This process allows for mass production of components with extreme accuracy and minimal variation. The molds themselves are typically made from steel or aluminum and are carefully machined to exact specifications. This method is ideal for producing high volumes of identical parts with intricate designs. Because of the speed, efficiency, and reliability of the process, injection molding has become a go-to solution for manufacturers across the globe.
Unmatched Precision and Consistency in Every Injection Molding Part
One of the biggest advantages of using an injection molding part in production is the ability to achieve incredible precision. The process allows for tight tolerances and uniformity that would be difficult, if not impossible, to replicate with traditional manufacturing methods. This precision is particularly important in industries like electronics and medical devices, where even a fraction of a millimeter can make a significant difference. Once a mold is created, every injection molding part produced from it is virtually identical, eliminating inconsistencies and significantly reducing quality control issues.
Cost-Effectiveness: Reducing Waste and Boosting Efficiency
Manufacturers are always looking for ways to reduce costs without sacrificing quality, and injection molding parts provide a smart solution. The initial investment in a mold can be high, but once in place, the cost per part drops dramatically as production scales. Additionally, the process minimizes waste by using only the exact amount of material needed for each part, and any excess can often be recycled. With faster cycle times and lower labor requirements compared to traditional methods, injection molding is not only cost-effective but also environmentally and economically sustainable.
Versatility in Materials and Applications
Another reason injection molding parts have revolutionized manufacturing is their incredible material versatility. Manufacturers can choose from a wide range of thermoplastics, thermosets, elastomers, and even composite materials depending on the application. Whether it’s a flexible rubber-like grip or a rigid, heat-resistant enclosure, the possibilities are endless. This adaptability makes injection molding suitable for countless industries, each with its own unique performance and aesthetic requirements.
How Injection Molding Parts Enable Scalable Manufacturing
Scalability is essential in modern production, especially in fast-paced markets where demand can shift rapidly. Injection molding parts offer a level of scalability that few other manufacturing processes can match. Once a mold is built, it can be used to produce tens of thousands—or even millions—of identical parts without degradation in quality. This makes it possible for businesses to respond quickly to market demand and reduce lead times significantly. As a result, companies can streamline their operations and bring products to market faster than ever before.
Driving Innovation in Automotive and Aerospace
In the automotive and aerospace sectors, performance and safety are non-negotiable. Injection molding parts have enabled manufacturers in these fields to push the boundaries of innovation while meeting strict regulatory standards. From lightweight interior components to high-strength brackets and under-the-hood parts, injection molding supports the production of durable, heat-resistant, and complex shapes that meet rigorous performance demands. Moreover, the ability to integrate multiple functions into a single part helps reduce vehicle weight and improve fuel efficiency—two critical goals for these industries.
Changing the Game in Consumer Electronics
Injection molding parts are a staple in the consumer electronics industry, where sleek design and compactness are key. Whether it’s smartphone casings, laptop components, or wearable tech housings, injection molding delivers the high-quality finishes and tight tolerances required by tech giants. The process also allows for the incorporation of branding elements, textured surfaces, and complex geometries that are essential to product differentiation in a highly competitive market. As electronics continue to shrink in size but grow in complexity, injection molding provides the precision and flexibility manufacturers need.
Medical Advancements Powered by Injection Molding Parts
The medical field depends heavily on components that are sterile, reliable, and precisely engineered. Injection molding parts are instrumental in producing surgical instruments, diagnostic devices, and single-use items like syringes and tubing connectors. The process supports cleanroom manufacturing and the use of biocompatible materials, ensuring patient safety. Additionally, the consistency of injection molding makes it easier to meet the strict quality standards imposed by health authorities. In life-or-death applications, reliability is everything—and injection molding delivers.
Sustainability and Eco-Friendly Practices in Injection Molding
Today’s manufacturers are increasingly focused on reducing their environmental impact, and injection molding parts are helping them meet their sustainability goals. Advances in biodegradable plastics, recycled materials, and energy-efficient machinery are transforming the industry. Because the process produces minimal waste and supports high-volume production with limited resources, it is inherently eco-friendly. Additionally, many companies now implement closed-loop systems that recycle scrap material and reduce overall consumption. The result is a greener supply chain without compromising product quality.
Challenges and Future Trends in Injection Molding Parts
While the benefits are clear, injection molding is not without challenges. Tooling costs and lead times for mold development can be high, particularly for complex parts. However, innovations such as 3D printed molds and modular tooling are beginning to reduce these barriers. Meanwhile, trends like micro molding are opening new possibilities for producing tiny, intricate parts for use in electronics and medical devices. Smart manufacturing technologies—such as real-time monitoring and AI-driven quality control—are also being integrated to further optimize the process. As these advancements gain traction, the capabilities of injection molding parts will only expand.
Why Injection Molding Parts Are Here to Stay
Injection molding parts have fundamentally reshaped the manufacturing landscape. Their unmatched precision, scalability, material versatility, and cost-efficiency make them indispensable across a wide range of industries. As technology continues to evolve, so too will the injection molding process—driving innovation and sustainability at every step. For manufacturers aiming to stay competitive in a fast-changing world, investing in injection molding isn’t just a smart choice—it’s a necessity. The future of manufacturing is being molded today, one part at a time.