- April 17, 2025
- Posted by: feinuojixie
- Category: Injection Molding News
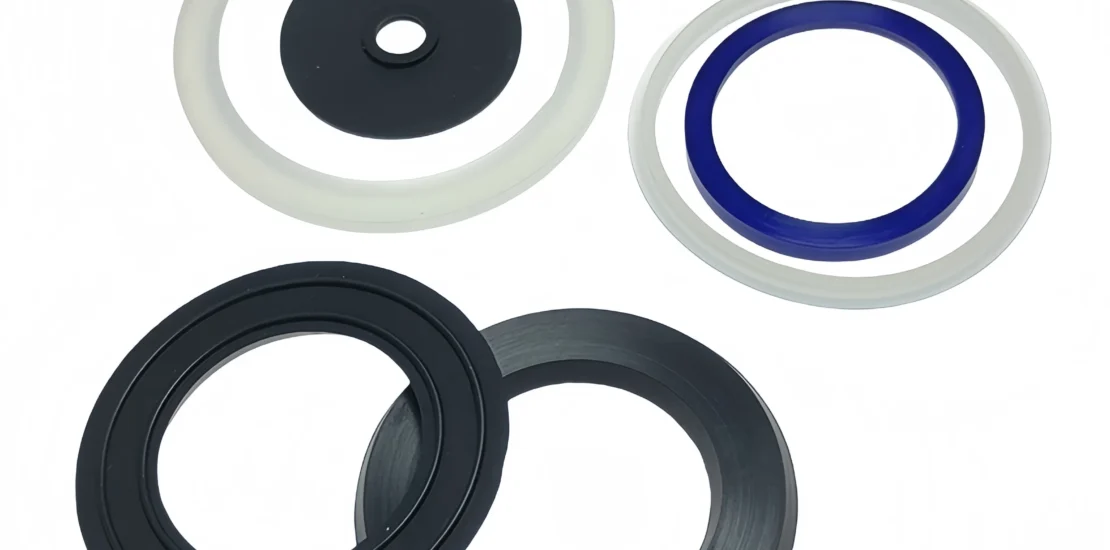
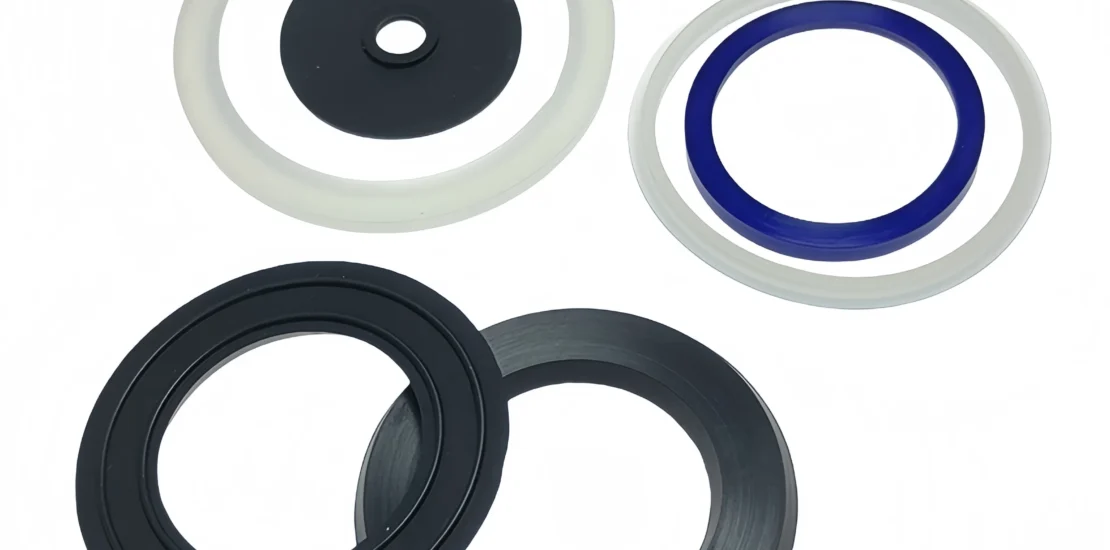
Injection molding part has long been the backbone of industries ranging from automotive and aerospace to consumer electronics and healthcare. Its ability to produce complex shapes with high precision and repeatability has made it a cornerstone of mass production. But as technology evolves and market demands shift, the traditional boundaries of what injection molding part can achieve are being redefined. Today, manufacturers are not just producing components—they are shaping the future. With the rise of intelligent automation, sustainability, and next-gen materials, injection molding part is entering a new era where performance, efficiency, and innovation converge. This article explores the cutting-edge trends transforming the landscape and what they mean for the future of manufacturing.
Smart Manufacturing and Digital Integration in Injection Molding Part Production
The future of injection molding part is being shaped by smart manufacturing. Industry 4.0 has ushered in a wave of digital transformation that allows machines, systems, and people to connect like never before. IoT-enabled molding machines can now collect real-time data on temperature, pressure, cycle time, and material usage, optimizing processes with minimal human intervention. Artificial intelligence is also stepping in, using predictive algorithms to prevent defects and maintain consistent quality. Automation, meanwhile, enhances productivity and reduces labor costs. With these advancements, manufacturers can achieve greater control, speed, and efficiency—making injection molding part production smarter and more responsive to changing needs.
Sustainable Innovations: Eco-Friendly Injection Molding Part Trends
Sustainability is no longer optional—it’s essential. Today’s manufacturers are under increasing pressure to reduce their environmental footprint, and injection molding part is no exception. A growing number of companies are shifting to biodegradable or plant-based polymers that offer similar performance to traditional plastics. Recycled resins are also gaining popularity, allowing producers to reuse materials without compromising quality. On the equipment side, energy-efficient machines and closed-loop systems are reducing power consumption and material waste. These eco-conscious innovations not only align with global sustainability goals but also appeal to environmentally aware consumers and partners.
Advanced Materials: Pushing the Boundaries of Performance
Material science is driving a major leap in injection molding part capabilities. High-performance polymers such as PEEK, PPS, and LCP are enabling parts to withstand extreme temperatures, chemical exposure, and mechanical stress. These materials are ideal for applications in aerospace, medical, and automotive sectors where reliability is critical. Another major trend is the use of metal-replacement compounds—plastic blends reinforced with glass or carbon fibers—to reduce weight without sacrificing strength. These advanced materials are unlocking new possibilities for part design, allowing manufacturers to produce lighter, stronger, and more durable components.
Micro Molding: Precision at the Smallest Scale
Miniaturization is a defining trend in industries like electronics, medical devices, and telecommunications. Micro molding addresses this need by producing tiny injection molding part with precise dimensions and intricate features. These parts often weigh less than a gram and require tolerance levels within microns. The process involves specialized machines and tooling designed for ultra-small components. Applications include hearing aids, micro-sensors, catheters, and other devices where size and precision are non-negotiable. As technology continues to shrink, micro molding will play an increasingly vital role in meeting the demand for miniature solutions.
3D Printing and Hybrid Techniques: A Complement to Injection Molding Part
While 3D printing is not set to replace traditional molding any time soon, it is becoming a valuable partner. Additive manufacturing allows for rapid prototyping, quick design iterations, and the production of complex geometries that would be impossible or cost-prohibitive with conventional methods. Hybrid techniques that combine 3D printing with injection molding are now emerging, enabling manufacturers to print inserts or cores and overmold them using injection molding. This approach reduces lead times, cuts tooling costs, and fosters innovation in part design. For low-volume or customized production, the synergy between these technologies offers a flexible and cost-effective solution.
Design for Manufacturability (DFM): Smarter Injection Molding Part Design
Designing with manufacturability in mind is more crucial than ever. DFM is a principle that ensures a product can be efficiently and economically produced using available processes. In injection molding part development, this involves choosing the right materials, optimizing wall thickness, reducing undercuts, and designing parts that minimize waste and cycle time. By incorporating DFM early in the design phase, engineers can avoid costly redesigns, streamline tooling, and improve product quality. With digital simulation tools now widely available, virtual testing can validate mold flow and cooling before any physical tool is made—saving time and money.
Real-Time Monitoring and Predictive Maintenance in Injection Molding Part Facilities
Operational efficiency in injection molding part facilities is reaching new heights through real-time monitoring and predictive maintenance. Sensors installed on machines provide constant feedback on key performance indicators. Operators can monitor every aspect of production, from mold temperature to hydraulic pressure, enabling immediate adjustments to maintain optimal conditions. Predictive maintenance uses data analytics to forecast equipment wear and prevent unexpected failures. This minimizes downtime, reduces maintenance costs, and extends the life of machines. These intelligent systems ensure that production lines are running smoothly, reducing waste and improving overall output quality.
Global Market Trends and the Future Outlook for Injection Molding Part
The global market for injection molding part is poised for steady growth, fueled by demand in automotive, electronics, packaging, and medical industries. Asia-Pacific remains the dominant region due to its strong manufacturing base, but North America and Europe are seeing renewed investment in high-tech molding capabilities. Key trends shaping the future include the push for local production, the adoption of sustainable practices, and the integration of digital tools across the supply chain. As customization becomes more important, manufacturers are focusing on flexible production systems that can adapt quickly to changing orders. Looking ahead, innovation will be the driving force behind growth and competitiveness in the injection molding part industry.
Molded to Innovate – Embracing the Future of Injection Molding Part
The landscape of injection molding part is undergoing a transformation marked by smart technology, sustainable practices, and cutting-edge materials. As the demand for more precise, durable, and eco-friendly components rises, manufacturers must adapt by embracing innovation at every stage—from design and prototyping to production and maintenance. The future isn’t just being imagined—it’s being molded, piece by piece, by those who dare to lead. By staying informed and proactive, businesses can not only keep pace but thrive in this evolving industrial revolution.