- April 17, 2025
- Posted by: feinuojixie
- Category: Injection Molding News
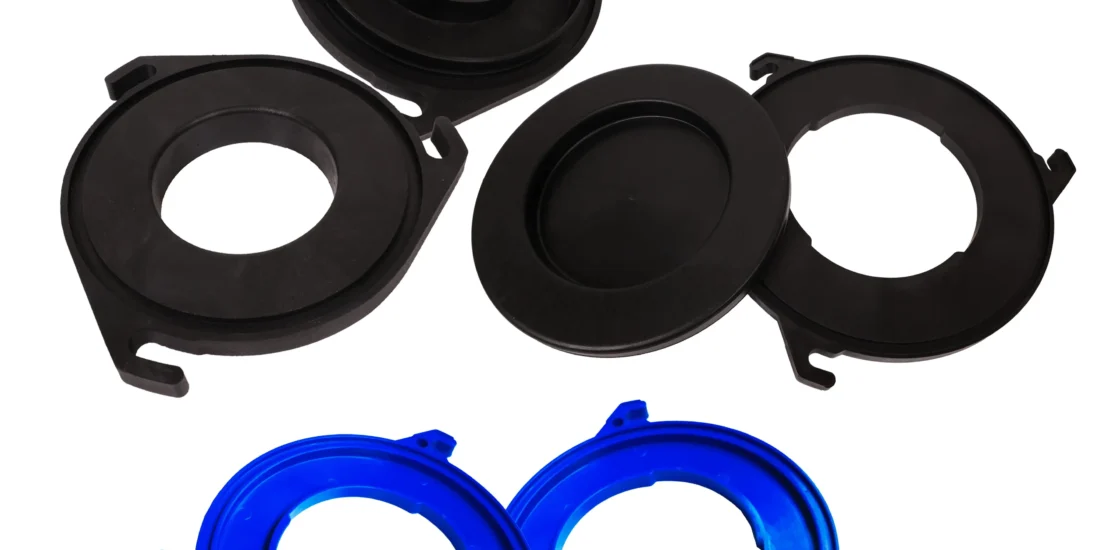
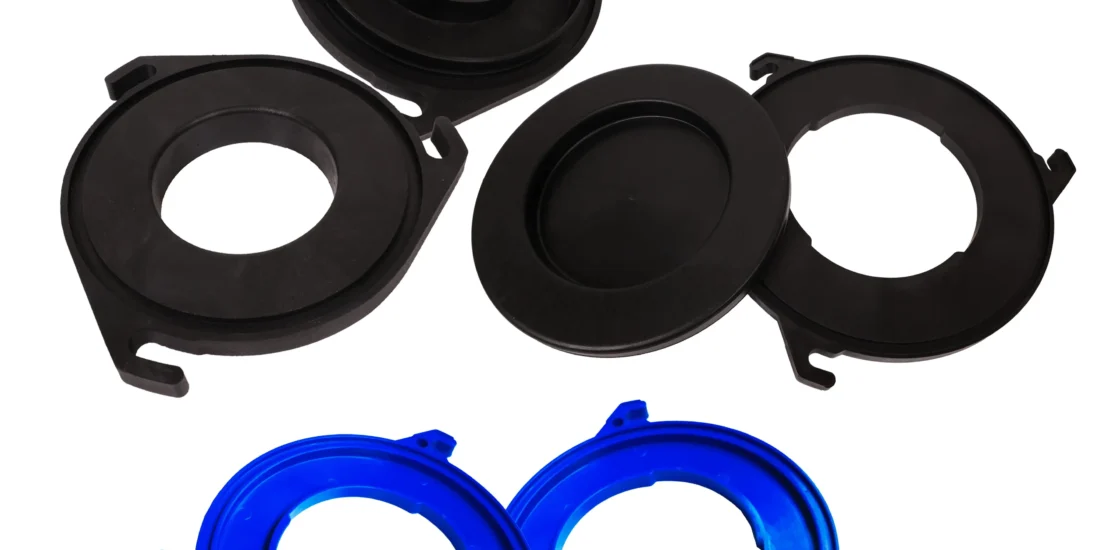
In today’s fast-paced manufacturing world, performance is everything. From the automotive sector to cutting-edge medical devices, industries across the board are demanding components that are not only made faster but also stronger and more reliable than ever. At the center of this transformation lies the injection molding part—a cornerstone of modern production.
This new era is defined by precision, innovation, and the ability to meet evolving performance benchmarks. High-performance injection molding part is no longer just about volume; it’s about quality, consistency, and pushing material science to its limits. Manufacturers are turning to advanced molding processes to meet the need for complex shapes, tight tolerances, and extreme durability.
As we dive into this blog, you’ll discover how technology, design, and engineering excellence are converging to redefine what injection molding part can achieve—and why this matters more than ever in today’s competitive landscape.
What Is a High-Performance Injection Molding Part?
A high-performance injection molding part goes beyond basic functionality. It is designed and engineered to perform in extreme environments, maintain structural integrity over long lifespans, and meet tight dimensional accuracy. These parts are often made using advanced polymers and composites that offer exceptional strength-to-weight ratios, heat resistance, and chemical durability.
Unlike traditional molded components, high-performance part is often tailored for mission-critical applications. Whether it’s a precision gear in a medical pump or a structural support in an aircraft, the focus is on delivering consistent performance where failure is not an option.
The Technology Behind the Transformation
Modern injection molding has become a high-tech operation. Cutting-edge machines with servo-driven systems, high-speed injection units, and real-time quality monitoring are becoming standard. Advanced automation ensures repeatability while reducing human error and labor cost.
Software also plays a significant role. Simulation tools allow engineers to predict how molten plastic flows through a mold, identifying issues before physical production begins. This leads to optimized designs, fewer defects, and less wasted material.
Smart manufacturing technologies are enabling injection molding systems to adapt on the fly, adjusting parameters in real-time based on sensor feedback. The result is faster cycle times, tighter tolerances, and more consistent output—all hallmarks of high-performance part production.
Material Innovation and Its Impact
The leap in performance isn’t just mechanical—it’s also chemical. Materials science has introduced new polymers and composites that elevate the properties of the injection molding part. High-heat thermoplastics like PEEK and PPS, fiber-reinforced materials, and bio-resins are now widely used to enhance durability, stiffness, and sustainability.
Material innovation allows manufacturers to match the right resin to the right application. For example, automotive components may require UV resistance and temperature stability, while medical devices need biocompatibility and sterilization resistance. The ability to fine-tune performance through material selection is a game-changer.
Why Faster Matters: Speed as a Competitive Edge
In modern manufacturing, speed isn’t just a nice-to-have—it’s a critical differentiator. The faster a company can get a product to market, the greater its advantage. High-speed injection molding delivers rapid production cycles while maintaining high-quality standards.
Cycle time reductions mean lower unit costs and the ability to scale efficiently. This is particularly important for industries under constant pressure to innovate and release new products. Faster molding doesn’t sacrifice precision either. With the right tools and processes, manufacturers can achieve both speed and excellence, delivering high-performance injection molding part in record time.
Strength Redefined: Meeting Demanding Applications
Strength in injection molding isn’t just about brute force—it’s about performance under stress. High-performance part is expected to withstand extreme environments, such as fluctuating temperatures, mechanical stress, and chemical exposure.
Engineered resins, reinforced fibers, and smart part design all contribute to this enhanced strength. Components like under-the-hood automotive brackets, aerospace housings, and industrial gears are all molded to meet specific load-bearing and fatigue requirements. These parts must not only last—they must also perform reliably in conditions where failure could be catastrophic.
Better by Design: Complex Geometry and Customization
Thanks to powerful CAD tools and digital simulations, designers can now push the boundaries of what’s possible in injection molding. From internal cooling channels to intricate lattice structures, modern part design allows for lighter, stronger, and more complex geometries.
Customization is also key. High-performance injection molding part can be optimized for the exact function it will perform. Whether it’s a textured grip, a snap-fit feature, or integrated electronics, the flexibility of injection molding design opens doors to innovation that was unthinkable a decade ago.
Sustainability in High-Performance Manufacturing
Sustainability is becoming non-negotiable in today’s manufacturing landscape. Fortunately, the injection molding industry is embracing greener practices without compromising performance. Recycled and bio-based resins are increasingly used in high-performance applications.
Advanced molding techniques also reduce scrap rates and material usage. Energy-efficient machines and closed-loop cooling systems further decrease environmental impact. In some cases, parts can be designed for disassembly and recycling, supporting circular manufacturing goals. High-performance no longer means high waste.
Industries Driving the Demand
Several industries are leading the charge for high-performance injection molding part. In automotive, lightweight yet strong components help improve fuel efficiency. Aerospace demands precision and reliability at high altitudes and temperatures. The medical sector requires sterile, highly accurate parts that perform flawlessly in life-critical applications.
Consumer electronics, too, benefit from this evolution—think of the durable, thin casings and connectors in smartphones and wearable devices. As innovation in these industries accelerates, so too does the need for advanced molded part that can keep up.
The Future Outlook of Injection Molding Part
The future of injection molding part is bright and dynamic. Technologies like 3D hybrid molding, where additive manufacturing meets traditional molding, are expanding the possibilities for rapid prototyping and complex geometry. AI and machine learning are beginning to influence mold design, process optimization, and quality control.
Global manufacturing trends also point to decentralized, flexible production where injection molding can be scaled locally and sustainably. As demand for speed, strength, and customization continues to grow, the injection molding part will remain a cornerstone of innovation—faster, stronger, and better than ever before.