- April 18, 2025
- Posted by: feinuojixie
- Category: Injection Molding News
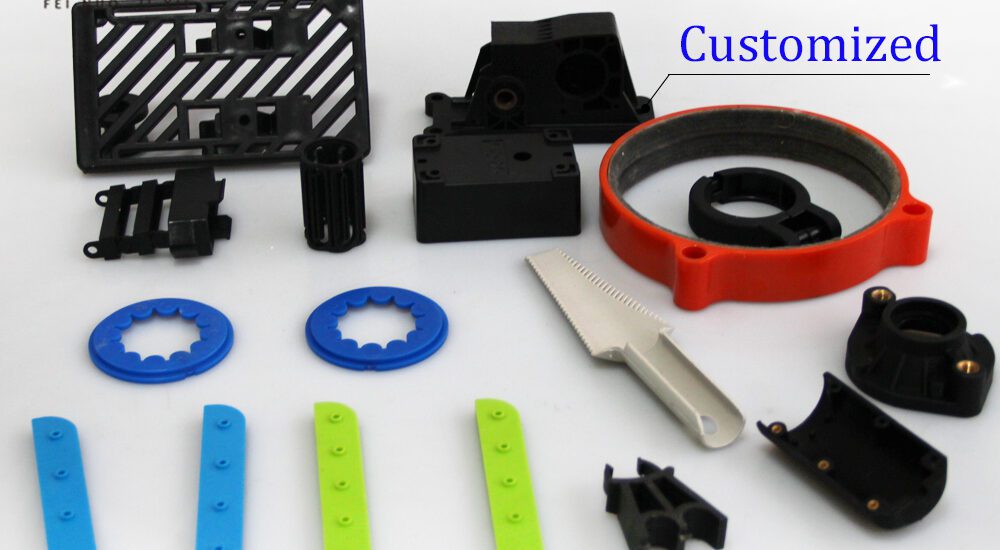
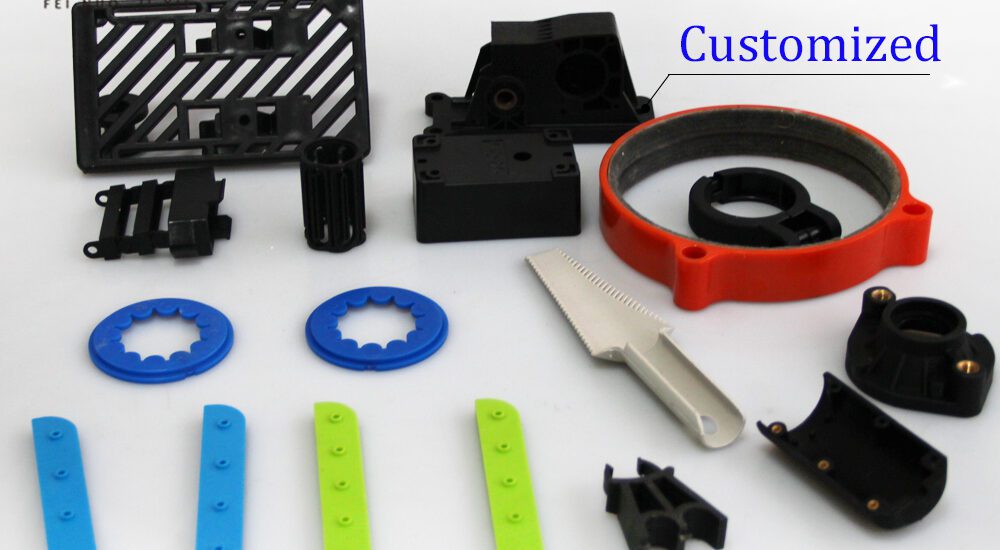
In today’s fast-paced manufacturing landscape, precision and customization are no longer luxuries—they are necessities. Whether it’s a high-performance medical device or a sleek consumer product, every detail matters. That’s where a custom injection molding part plays a pivotal role. Designed specifically to meet unique specifications, this type of component ensures that your product performs as intended, with the perfect fit and function you need to stay competitive.
This guide dives deep into the world of custom injection molding. We’ll explore everything from material choices and design principles to tooling and production. You’ll learn how to optimize every step of the process to achieve flawless results—no matter your industry. Whether you’re a product developer, engineer, or entrepreneur, understanding how to create a high-quality injection molding part can elevate your project from good to exceptional.
What Is a Custom Injection Molding Part?
A custom injection molding part is a precisely engineered component created using the injection molding process and tailored to a specific application or function. Unlike off-the-shelf components, custom parts are built from scratch to meet unique requirements, such as specific dimensions, tolerances, material characteristics, or aesthetic needs.
The injection molding process involves injecting molten plastic into a steel or aluminum mold under high pressure. Once cooled, the plastic solidifies into the desired shape. This method is ideal for producing high volumes of consistent parts with intricate geometries. When customized, the process becomes a powerful solution for creating components that perfectly integrate into your final product.
Why Customization Matters in Injection Molding Part Design
Customization enables manufacturers to align every detail of an injection molding part with the overall product’s purpose and performance requirements. It allows designers to:
-
Ensure compatibility with other components
-
Enhance product durability and longevity
-
Reduce assembly time and costs
-
Achieve a unique look or brand aesthetic
By designing the part around your product’s exact needs, you eliminate compromise. The result is improved functionality, greater user satisfaction, and a product that stands out in the market.
Key Industries That Rely on Custom Injection Molding Part
Numerous industries depend on custom injection molding part solutions to drive innovation and ensure high performance:
-
Automotive: Custom clips, housings, and interior components require precision and durability under high-stress conditions.
-
Medical: Devices like syringes, casings, and surgical tools must meet strict hygiene and performance standards.
-
Consumer Electronics: Sleek, compact designs demand parts that fit perfectly and maintain aesthetic appeal.
-
Industrial Equipment: Custom parts help improve machine function and simplify maintenance.
Each of these sectors benefits from the reliability, repeatability, and efficiency that a well-designed custom injection molding part offers.
Material Selection for a Custom Injection Molding Part
The choice of material plays a crucial role in the performance and cost of your injection molding part. Common materials include:
-
ABS: Known for toughness and impact resistance
-
Polycarbonate: Offers high strength and transparency
-
Nylon: Excellent for wear and chemical resistance
-
Polypropylene: Lightweight, flexible, and economical
-
TPU (Thermoplastic Polyurethane): Great for soft-touch and elastic properties
When selecting material, consider factors such as operating temperature, exposure to chemicals, required flexibility, and production volume. The right material ensures that your part functions correctly under real-world conditions.
Design Considerations for a Custom Injection Molding Part
Effective design is the foundation of a reliable injection molding part. Key considerations include:
-
Wall Thickness: Consistent wall thickness prevents warping and sink marks.
-
Draft Angles: Angled surfaces help with easy part ejection from the mold.
-
Undercuts: Should be minimized or addressed with sliders in the mold design.
-
Tolerances: Tight tolerances must be achievable with the chosen material and mold.
-
Mold Flow: Design should ensure proper filling of the mold cavity with minimal defects.
Collaborating with an experienced mold designer can help ensure that your design supports both function and manufacturability.
Prototyping and Testing the Injection Molding Part
Before committing to full-scale production, it’s essential to prototype your injection molding part. Common prototyping methods include:
-
3D Printing: Quick and affordable, ideal for early design validation.
-
Soft Tooling: Creates limited quantities of actual molded parts using temporary molds.
Once the prototype is ready, testing should evaluate fit, mechanical strength, thermal performance, and assembly compatibility. Any issues discovered at this stage can be corrected before investing in production tooling.
Tooling for Custom Injection Molding Part
Tooling refers to the mold used to create the injection molding part. Designing and manufacturing the mold is one of the most critical and cost-intensive steps. Key considerations include:
-
Tool Material: Steel offers durability for high volumes; aluminum is more affordable for short runs.
-
Single vs. Multi-Cavity: Multi-cavity molds increase output but cost more upfront.
-
Tool Life: A well-maintained mold can produce millions of parts.
-
Lead Time: Custom tooling can take weeks or months, depending on complexity.
Investing in high-quality tooling ensures consistent, repeatable parts over the life of the project.
Production and Quality Control
Once tooling is complete, production begins. The molding machine injects plastic into the mold repeatedly to produce the final injection molding part. Maintaining consistent process parameters—such as temperature, pressure, and cooling time—is key to part quality.
Quality control measures may include:
-
In-Process Inspection: Verifying dimensions and appearance during production
-
Post-Production Testing: Stress tests, drop tests, or fit tests with assemblies
-
Statistical Process Control (SPC): Tracking variations to maintain tight tolerances
These practices ensure that each part meets specifications and functions flawlessly.
Common Challenges and How to Overcome Them
Producing a custom injection molding part is not without its challenges. Common issues include:
-
Warping: Caused by uneven cooling or poor material selection
-
Sink Marks: Result from thick sections and slow cooling
-
Flash: Excess material seeping out of the mold, due to poor clamping or worn tooling
-
Short Shots: Incomplete filling of the mold cavity
To overcome these issues, focus on balanced design, precise tooling, and consistent processing parameters.
Cost Considerations and ROI of Custom Injection Molding Part
While the upfront costs of tooling and design may seem high, a custom injection molding part often leads to long-term savings. Cost factors include:
-
Design and Engineering Time
-
Tooling Investment
-
Material Costs
-
Cycle Time and Labor
The ROI comes from improved product performance, lower defect rates, and faster assembly. In many cases, customizing a part enables competitive pricing and a better end-user experience.
Choosing the Right Partner for Your Custom Injection Molding Part
Finding the right manufacturing partner is crucial. Look for:
-
Technical Expertise: A team that understands both design and mold making
-
Quality Certifications: ISO, FDA, or other industry-specific standards
-
Communication: Transparent updates and design collaboration
-
Support Services: Prototyping, testing, and design refinement
An experienced partner can guide you from concept through production, helping you avoid pitfalls and deliver superior results.
Future Trends in Injection Molding Part Customization
The world of injection molding part production is evolving rapidly. Emerging trends include:
-
Micro Molding: Creating ultra-small, precise parts for electronics and medical devices
-
Eco-Friendly Materials: Using biodegradable or recycled resins to meet sustainability goals
-
Digital Manufacturing: Integrating simulation and automation for faster development
-
Smart Molds: Using sensors to monitor mold conditions in real time
Staying ahead of these trends allows businesses to innovate and gain a competitive edge in their markets.
Conclusion
A custom injection molding part is more than just a component—it’s a strategic asset that ensures your product works as intended. From design and material selection to tooling and production, every decision plays a role in the final performance and quality.
By understanding the process and embracing customization, you can develop parts that not only fit perfectly but also elevate your product’s function, appearance, and value. Whether you’re launching a new product or refining an existing one, investing in a well-executed custom injection molding part is a smart move toward long-term success.