- April 18, 2025
- Posted by: feinuojixie
- Category: Injection Molding News
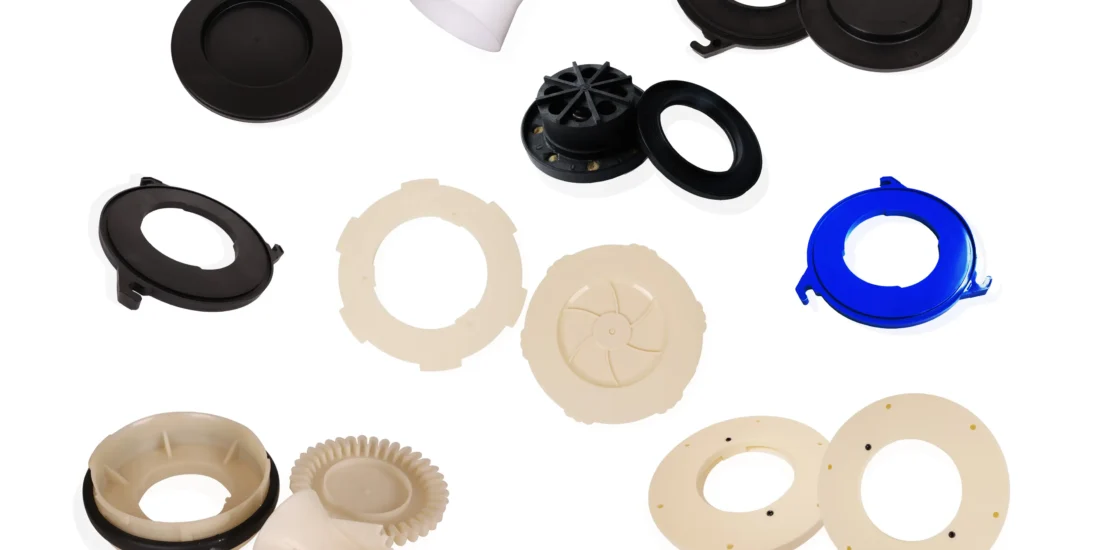
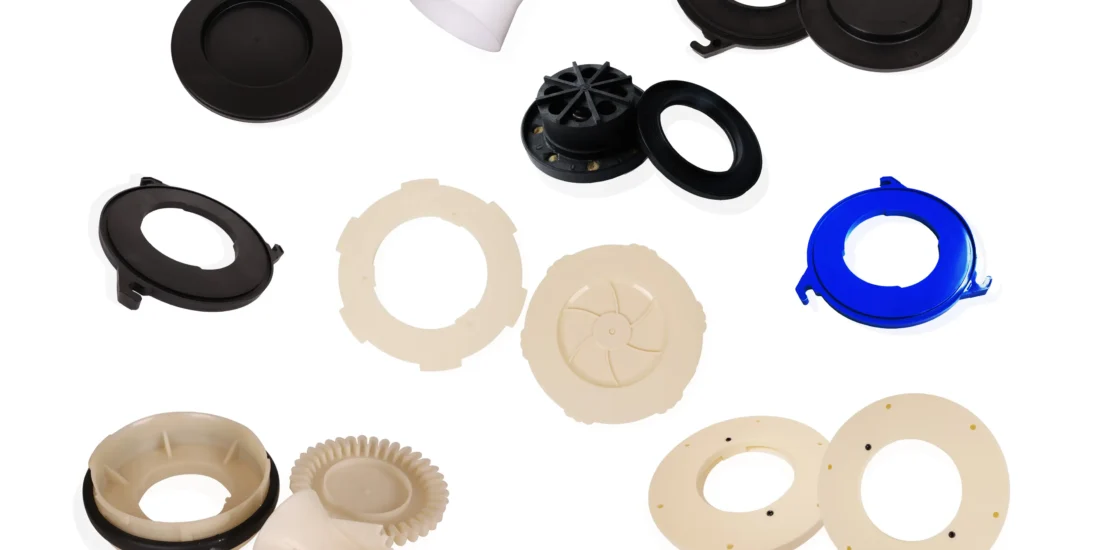
In today’s fast-paced manufacturing environment, production efficiency isn’t just a competitive advantage—it’s a survival tool. Whether you’re crafting high-precision automotive components or everyday consumer goods, the injection molding part you choose can dramatically impact everything from cycle time to product quality. And yet, many production lines unknowingly overlook components that could streamline their process, cut costs, and improve consistency.
If your team is still relying on the same parts year after year without a critical review, you could be leaving untapped performance on the table. This article explores the often-missed injection molding part that can make or break a high-performing production line. We’ll uncover how these elements work behind the scenes, how to select them intelligently, and how forward-thinking manufacturers are staying ahead with better part choices.
Understanding Injection Molding Part in the Manufacturing Landscape
An injection molding part is more than just a component of a tool—it is the foundation of consistent, scalable production. Whether it’s guiding the flow of molten resin or shaping the final surface finish, each injection molding part plays a precise role in achieving dimensional accuracy and durability.
In sectors like automotive, medical, electronics, and consumer packaging, where tolerance and repeatability are non-negotiable, the right part ensures that every cycle delivers the same result. However, when manufacturers fail to optimize these parts, it often leads to inefficiencies like warping, flashing, or frequent mold maintenance. Understanding the importance of each injection molding part within the broader system is the first step toward optimizing performance and minimizing waste.
The Hidden Heroes: Underrated Injection Molding Part That Boost Efficiency
Some of the most powerful improvements come from the parts you rarely hear about. Core pins, for example, influence internal cavity geometry and heat distribution, yet many companies continue using generic options instead of application-specific designs. Similarly, ejector sleeves—often viewed as a standard item—can greatly affect part ejection timing and surface finish when optimized correctly.
Another overlooked injection molding part is the cooling channel insert. With proper placement and contouring, these inserts regulate mold temperature more efficiently, significantly reducing cycle times and part distortion. Manufacturers who take the time to evaluate and upgrade these “hidden” parts often see a surprising jump in overall equipment effectiveness (OEE) and quality output.
Choosing the Right Injection Molding Part for Specific Applications
Every industry demands something different from its injection molding process. In the medical field, precision and sterilizability are paramount. In consumer electronics, it’s about ultra-thin tolerances and aesthetic finish. Automotive parts must withstand harsh conditions without deforming or cracking over time.
Choosing the right injection molding part begins with understanding the end-use application. For instance, a part designed for high-heat resistance in under-the-hood automotive components would be wildly different from one intended for a translucent cosmetic bottle. Material selection, surface treatment, and even gate design all play a role. Matching part capabilities with industry requirements ensures long-term reliability and regulatory compliance.
Common Mistakes in Injection Molding Part Selection
Even experienced manufacturers fall into the trap of selecting injection molding part based on habit rather than performance. One of the most frequent mistakes is over-engineering a mold with features that add cost without real value. Another is ignoring wear patterns on high-stress components, leading to unplanned downtime and rework.
A manufacturer may use a standard bushing or gate insert when a hardened or coated version would last significantly longer in a high-volume environment. These choices accumulate over time and can drastically affect production cost. A better approach is to review part performance regularly and incorporate data from maintenance logs to inform future selections.
Material Matters: The Role of Resin and Mold Compatibility
Not every injection molding part performs equally across different resins. A gate insert that works perfectly with polypropylene may wear rapidly when exposed to glass-filled nylon. Likewise, venting features that release trapped gases efficiently in one application may clog or degrade in another.
To ensure optimal performance, the chosen mold material and injection molding part must be compatible with the resin’s thermal and chemical characteristics. This includes considering wear resistance, coefficient of thermal expansion, and mold release behavior. Consulting with resin and tooling suppliers early in the design phase can eliminate costly mismatches and extend tool life.
Custom vs Standard: Which Injection Molding Part Makes Sense for You?
When deciding between standard and custom injection molding part, the answer depends largely on production goals. Standard parts offer affordability and shorter lead times, making them ideal for prototyping or short runs. However, custom parts are tailored to your mold geometry, part design, and performance needs, often delivering better longevity and quality in high-volume scenarios.
A startup might begin with standard components to keep costs low. But as volumes increase and cycle optimization becomes critical, switching to custom inserts, gates, or ejectors can bring significant ROI. It’s about aligning part strategy with your current and future manufacturing goals.
How to Audit Your Production Line for Missing Injection Molding Part
Many performance issues in molding operations can be traced back to underperforming or misused components. Conducting a thorough audit of every injection molding part on your line can uncover inefficiencies that are otherwise invisible.
Start by reviewing your tool’s historical performance: where have failures or quality issues occurred most frequently? Use that data to inspect part wear, cooling efficiency, and part ejection performance. A structured checklist, combined with the input of a tooling engineer or specialist, can help identify opportunities for replacing or upgrading parts. Even something as small as a redesigned sprue bushing could enhance mold fill and reduce material waste.
Future Trends in Injection Molding Part Design and Integration
Innovation in mold design is rapidly evolving. One of the most exciting trends is the integration of smart sensor-enabled injection molding part that track pressure, temperature, and part ejection in real-time. These intelligent systems allow for predictive maintenance and process optimization based on live data.
In parallel, additive manufacturing is enabling more complex, conformal-cooled inserts that dramatically outperform traditional designs. AI-driven simulation software is also being used to refine part geometry for improved flow and reduced stress concentration. As these technologies mature, staying ahead means not only adopting new tools—but also rethinking the role of every injection molding part in your workflow.
Stop Leaving Performance on the Table
In the race to optimize production, every detail matters. Injection molding part may seem like small cogs in a much larger system, but their impact on performance, quality, and cost is undeniable. By overlooking or underutilizing the right components, manufacturers risk falling behind competitors who treat tooling strategy as a priority—not an afterthought.
Now is the time to review your setup, engage with tooling experts, and explore what upgrades could mean for your operation. Because the parts you’re missing may just be the ones that unlock your next level of performance.