- April 21, 2025
- Posted by: feinuojixie
- Category: Injection Molding News
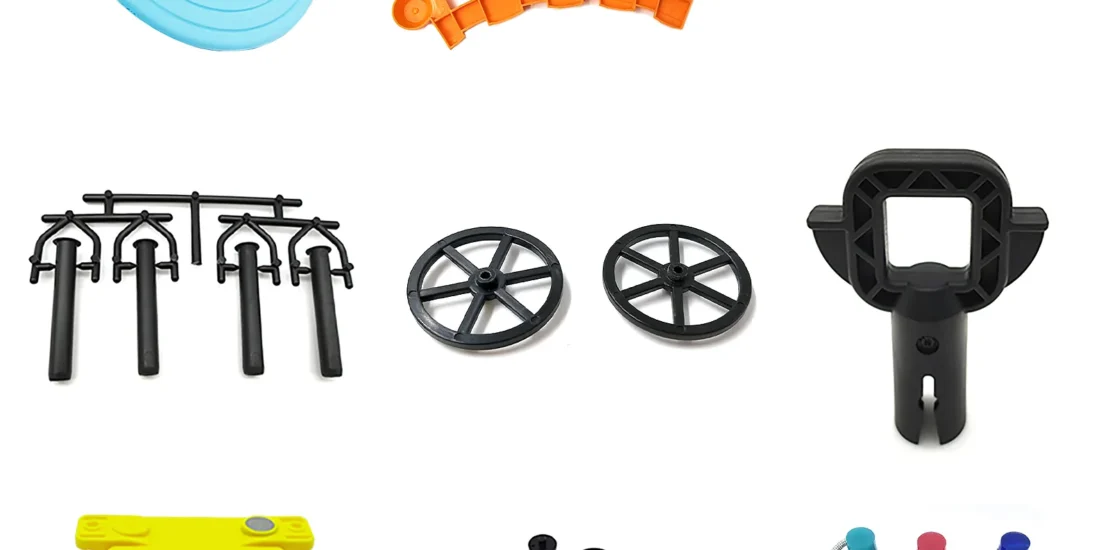
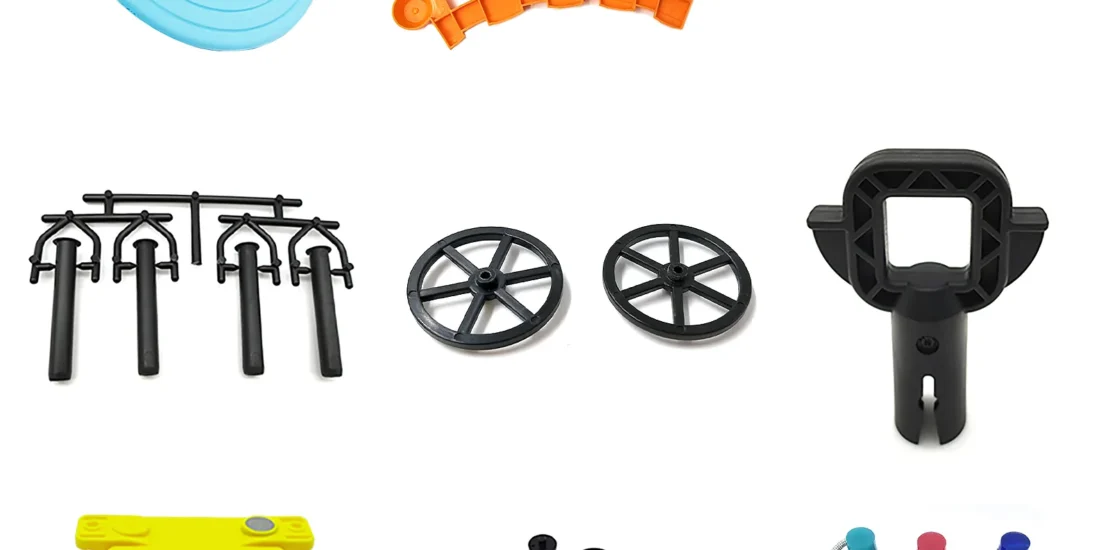
Injection moulding is the go-to manufacturing method for creating high-quality, cost-effective plastic parts in mass volumes. From consumer goods to medical devices and automotive components, injection moulding plastic part production powers countless industries. But success isn’t just about injecting molten plastic into a mould — it’s a precise science that rewards those who understand its nuances. In this post, we’ll uncover ten must-know secrets about injection moulding plastic parts that will help you avoid costly mistakes and create better products faster.
Design Matters: The Foundation of Every Injection Moulding Plastic Part
Every successful injection moulding plastic part begins with a solid design. This stage sets the tone for manufacturability, quality, and cost. Designers must consider factors like uniform wall thickness to avoid warping, proper draft angles for easy part ejection, and smooth transitions to facilitate material flow. Small changes in the design phase can significantly reduce tooling costs and production time. Ignoring these elements often leads to parts that are difficult to mould or fail to meet specifications.
Material Choice Defines Performance and Cost
Not all plastics are created equal, and the resin you choose directly affects your part’s functionality and durability. Whether it’s ABS, polypropylene, nylon, or polycarbonate, each material has unique mechanical and thermal properties. The right choice depends on the application — for instance, outdoor parts may require UV resistance, while load-bearing components need high tensile strength. A mismatch in material selection can lead to cracking, deformation, or premature wear, undermining the performance of the injection moulding plastic part.
Tooling is an Investment, Not Just a Cost
The mould is the heart of the injection moulding process, and its quality directly influences the final part. High-precision tooling may require a significant upfront investment, but it pays dividends through longer mould life, tighter tolerances, and fewer defects. Conversely, cutting corners on tooling often results in inconsistent parts and unplanned downtime. A well-made mould ensures consistent cycle times and minimizes maintenance, making it a crucial factor in long-term production success.
DFM (Design for Manufacturability) Can Save Thousands
Design for Manufacturability (DFM) is an engineering approach that simplifies the production process while enhancing part quality. By integrating DFM early in the design phase, teams can eliminate unnecessary complexity, reduce the risk of defects, and streamline assembly. For injection moulding plastic parts, this means adjusting features to support better flow, proper cooling, and easier mould release. Companies that embrace DFM often save significant costs through faster production and lower reject rates.
Undercuts and Complex Features May Complicate Everything
Adding features like threads, snap fits, or side holes may seem essential, but they often introduce complexity to the tooling process. Undercuts, in particular, require side actions or collapsible cores, which increase mould cost and cycle time. If not properly accounted for, such features can lead to part sticking, incomplete fills, or cosmetic issues. Whenever possible, simplify the geometry or explore design alternatives that eliminate the need for complex tooling solutions.
Cycle Time Efficiency Makes or Breaks Production
Cycle time — the total time to complete one moulding cycle — has a direct impact on throughput and cost. Each phase, from injection and cooling to part ejection, must be optimized for speed without compromising quality. Cooling time alone can account for 60% of the total cycle. Efficient mould design, including proper cooling channels and uniform wall thickness, helps reduce cycle time and improve overall efficiency. Shorter cycles mean more parts in less time, maximizing profitability.
Surface Finish Isn’t Just Cosmetic
The surface finish of an injection moulding plastic part affects more than just its appearance. A glossy or matte finish can influence tactile feel, scratch resistance, and even part function in high-friction environments. The finish is determined by the mould’s surface texture and the material used. For applications where aesthetics matter — such as consumer electronics or packaging — the right surface finish can elevate brand perception. Functional finishes, like textured grips or anti-glare surfaces, enhance usability and safety.
Tolerances Should Be Realistic, Not Idealistic
While tight tolerances may seem ideal, they’re often unnecessary and costly. Injection moulding inherently involves thermal expansion and cooling shrinkage, which must be factored into tolerance expectations. Overly tight specs can lead to increased moulding difficulty, higher rejection rates, and more expensive tooling. A better approach is to define functional tolerances — values that meet the product’s performance needs without over-engineering. This allows manufacturers to balance precision with efficiency.
Quality Control Starts Before Production
High-quality injection moulding plastic parts don’t happen by chance. They result from careful planning, pre-production validation, and consistent process control. Before full-scale production, it’s essential to conduct mould trials, material verification, and first-article inspections. These steps help identify issues early, when corrections are easier and less expensive. Throughout production, monitoring key parameters like temperature, pressure, and cycle consistency ensures that every part meets the intended standard.
Partnering With the Right Manufacturer Is Half the Battle
Even the best design and material choices fall short if your manufacturing partner lacks the expertise to bring your vision to life. A strong manufacturing partner will provide technical guidance, help refine your design, and maintain consistent quality from prototype to full-scale production. Look for experience with similar injection moulding plastic parts, robust quality systems, and a collaborative approach. The right partner isn’t just a vendor — they’re a critical extension of your team.
Conclusion
Injection moulding plastic part production is a precise, high-stakes process that rewards knowledge and attention to detail. By mastering these ten essential secrets — from smart design and material selection to efficient tooling and reliable partnerships — you can avoid pitfalls, lower costs, and achieve superior product performance. Whether you’re launching a new product or scaling an existing one, these insights will help you navigate the complexities of injection moulding with confidence.