- April 21, 2025
- Posted by: feinuojixie
- Category: Injection Molding News
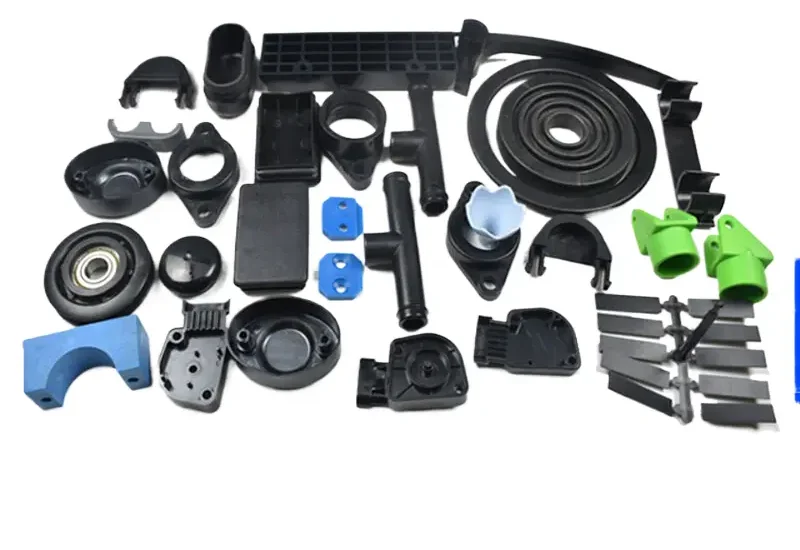
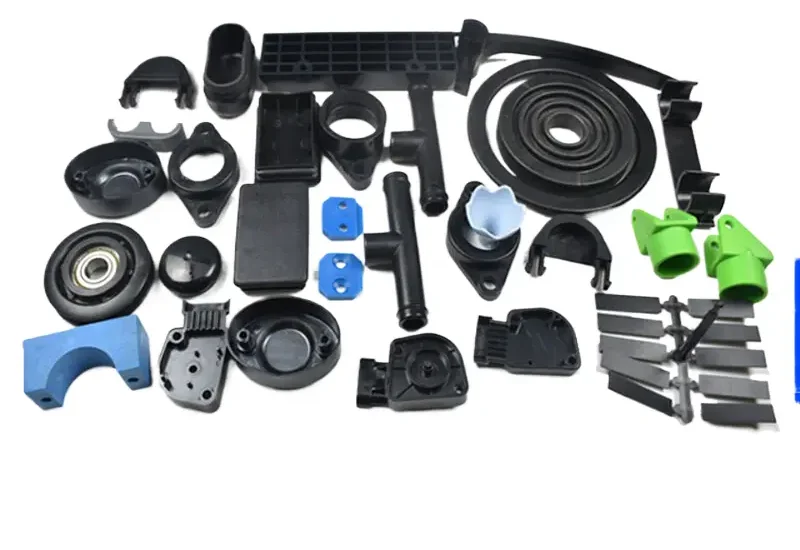
Injection moulding has become one of the most powerful and widely-used manufacturing methods for creating plastic part with precision and speed. From smartphone casing to automotive interiors, this technique enables mass production of complex and durable component. Whether you’re a designer, engineer, or production manager, understanding the ins and outs of injection moulding can significantly improve product quality, reduce cost, and speed up time-to-market.
In this guide, we’ll break down every step of the injection moulding process, from material selection to defect troubleshooting. You’ll gain expert-level insight into how to design, produce, and optimise a plastic part using this method — all without the trial-and-error. Let’s get started on the path to injection moulding success.
What is Injection Moulding Plastic Part?
Injection moulding is a manufacturing process used to produce plastic part by injecting molten plastic material into a mould cavity. Once cooled, the material solidifies into the desired shape. This method is ideal for creating complex geometries with high precision and repeatability.
The process begins with plastic pellets being fed into a heated barrel, melted, and then injected under high pressure into a mould. After the plastic part cools and hardens, it is ejected and the cycle begins again. This technique is widely used in industries such as automotive, electronics, consumer goods, and medical devices due to its speed, accuracy, and scalability.
Why Choose Injection Moulding for Plastic Part Manufacturing
Injection moulding is a preferred choice for plastic part production for several compelling reasons. First, it allows for high-volume manufacturing at relatively low per-unit cost once the initial mould is made. The repeatability of this process ensures consistent product quality across thousands or millions of units.
Additionally, injection moulding supports intricate part designs with complex features that would be difficult or impossible to achieve through other methods. The process also produces minimal waste, especially when paired with modern recycling practices. It’s fast, reliable, and well-suited for automation, making it a top choice in both prototyping and mass production environments.
Understanding the Injection Moulding Machine
An injection moulding machine is composed of several key parts that work together to create a plastic part:
-
Hopper: Holds and feeds the plastic pellets into the barrel.
-
Barrel and Screw: The plastic is melted by heaters as the screw rotates, mixing and pushing it forward.
-
Nozzle: Injects the molten plastic into the mould.
-
Mould: The custom-designed cavity that shapes the plastic.
-
Clamping Unit: Holds the mould halves tightly together during injection and cooling.
Understanding these components and their functions is essential for troubleshooting issues and optimising production settings.
Selecting the Right Plastic Material
Choosing the right plastic is crucial for the success of your injection moulding project. Common thermoplastics include:
-
ABS: Strong, lightweight, and impact-resistant; ideal for electronic housings.
-
Polypropylene (PP): Chemically resistant and flexible; often used in packaging and automotive parts.
-
Polycarbonate (PC): Transparent, tough, and heat-resistant; used for lenses and enclosures.
The right material depends on your application’s requirements: strength, flexibility, temperature resistance, transparency, and cost. It’s also important to consider the material’s flow characteristics, shrinkage rate, and compatibility with the intended finish or texture.
Designing for Injection Moulding Plastic Part Success
Effective part design is key to achieving both quality and efficiency. Here are essential design tips:
-
Uniform Wall Thickness: Avoids sink marks and warping.
-
Draft Angles: Allows easy ejection of the part from the mould.
-
Ribs and Bosses: Add strength without increasing wall thickness.
-
Avoid Undercuts: These complicate the mould design and increase costs.
-
Corner Radii: Rounded corners improve material flow and reduce stress concentrations.
By following these principles, you reduce the likelihood of defects and ensure a smoother production cycle.
Creating the Perfect Mold Tool
The quality of the mould directly affects the quality of the plastic part. Moulds are typically made from hardened steel or aluminum, depending on expected production volume. Key considerations include:
-
Cooling Channels: Ensure even cooling to reduce cycle time and prevent warping.
-
Gate Design: Controls how the plastic enters the mould, affecting fill pattern and part strength.
-
Surface Finish: Impacts appearance and functionality of the finished part.
Prototype moulds are often simpler and less expensive, while production moulds are more robust and engineered for long-term use.
Injection Moulding Process Step-by-Step
A standard injection moulding cycle consists of:
-
Clamping: The mould closes and is held under pressure.
-
Injection: Molten plastic is injected into the mould cavity.
-
Cooling: The part solidifies as it cools in the mould.
-
Ejection: The mould opens and the part is pushed out.
Each stage affects the quality and efficiency of the final product. Parameters like injection speed, pressure, temperature, and cooling time must be precisely controlled to ensure optimal results.
Common Defects in Injection Moulding Plastic Part and How to Fix Them
Even with a well-designed process, defects can occur. Here are some common ones and how to fix them:
-
Sink Marks: Caused by thick sections. Solution: maintain uniform wall thickness or adjust cooling time.
-
Warping: Happens due to uneven cooling. Use proper cooling channels and material selection.
-
Short Shots: Incomplete filling. Increase injection pressure or check for blockages.
-
Flash: Excess plastic escapes mould. Adjust clamp force or check mould alignment.
-
Burn Marks: Due to trapped air or overheating. Add vents and reduce injection speed.
Identifying and correcting these issues early can save time and reduce waste.
Optimising Production for Efficiency and Quality
To produce high-quality plastic part at scale, efficiency is key. Strategies include:
-
Cycle Time Reduction: Minimize cooling and injection times without sacrificing quality.
-
Preventive Maintenance: Regularly service moulds and machines to avoid breakdowns.
-
Quality Control: Use in-line sensors and visual inspections to catch defects early.
-
Automation: Robotic arms and conveyors can speed up handling and packing.
Advanced tools such as real-time monitoring systems and AI-driven analytics can further streamline operations.
Sustainable Injection Moulding Plastic Part Practices
Sustainability is increasingly important in manufacturing. Here’s how injection moulding supports eco-friendly practices:
-
Recycled Resin: Many plastic materials can be reground and reused.
-
Bioplastics: Derived from renewable sources like corn or sugarcane.
-
Energy Efficiency: Modern machines use servo motors and smart controls to reduce power consumption.
-
Lean Manufacturing: Reduces excess material and overproduction.
Sustainable design, such as reducing material use and designing for recyclability, also plays a crucial role in minimizing environmental impact.
Mastering the Art of Injection Moulding Plastic Part
Injection moulding is a powerful and efficient way to produce high-quality plastic part for a wide range of industries. By understanding the machinery, selecting the right material, designing with manufacturability in mind, and continually optimising your process, you can produce durable and precise component with confidence.
Whether you’re just starting out or looking to refine your existing workflow, applying the principles in this guide will put you on the path to mastering injection moulding like a pro.