- April 22, 2025
- Posted by: feinuojixie
- Category: Injection Molding News
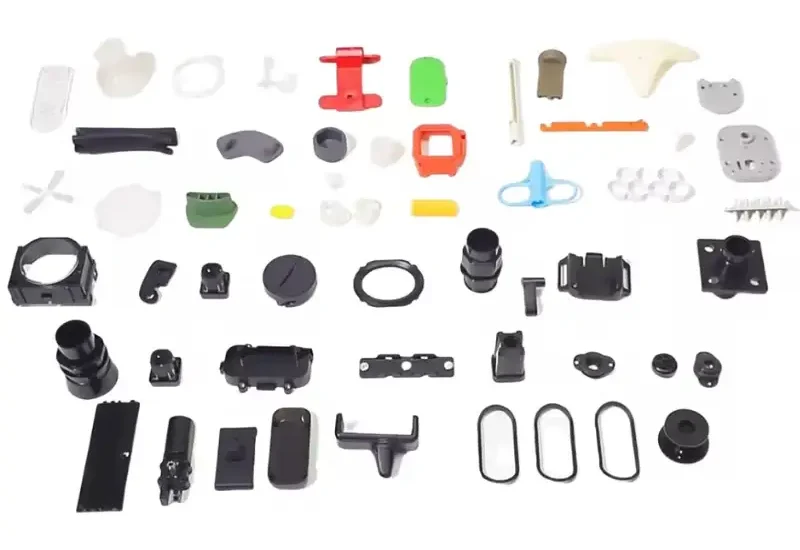
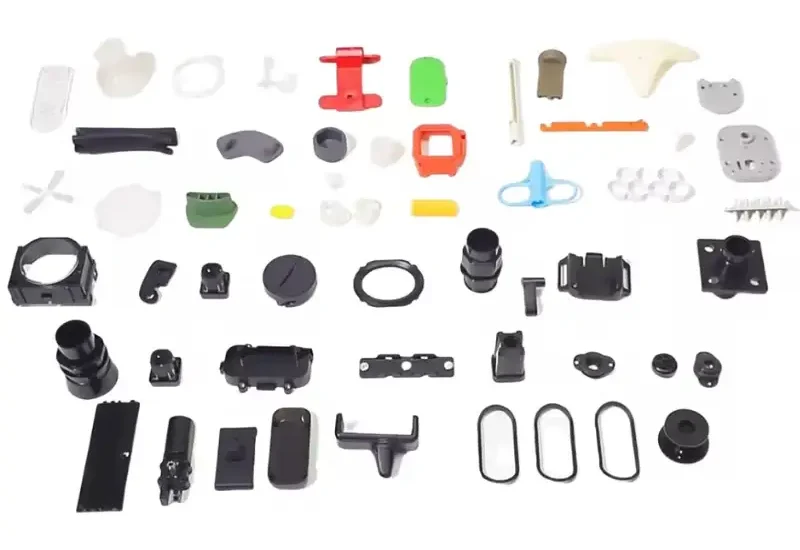
Injection moulding plastic parts has become an essential method for producing high-quality, high-volume components across a wide range of industries. Its unique ability to deliver precise, repeatable, and complex shapes at relatively low cost makes it indispensable for manufacturers worldwide. Whether it’s the sleek casing of a smartphone, the functional dashboard of a car, or a medical syringe, chances are it’s been produced through this process. The magic lies not only in the machines but also in the synergy of design, engineering, and manufacturing expertise that turns a simple plastic pellet into a market-ready product. This article explores every step of that transformation, from the first sketch to the finished part, uncovering the fascinating world behind injection moulding plastic parts.
Designing for Success: Turning Ideas into Manufacturable Plastic Parts
Every great plastic product starts with a solid design. The journey begins by translating an idea into a digital concept using computer-aided design (CAD) tools. Engineers must consider not only the function and form of the product but also how it will behave during the injection moulding process. This includes accounting for wall thickness, draft angles, and potential warpage.
Material selection is equally important. Different polymers offer varying strengths, flexibilities, and resistance to heat or chemicals. Designers collaborate with material scientists to choose the ideal resin that balances performance with cost-effectiveness.
Design for manufacturability (DFM) ensures the concept can be efficiently and reliably produced. By making smart design choices early—like avoiding undercuts or ensuring uniform wall thickness—teams reduce the likelihood of defects and simplify the production process. Ultimately, this stage lays the foundation for success in creating injection moulding plastic parts.
Tooling Matters: The Critical Role of Mould Design and Fabrication
Once a product design is finalized, the next step is to create the mould—arguably the most crucial and expensive component of the entire process. Moulds are typically made from hardened steel or aluminum and are precision-machined to the exact dimensions required by the plastic part.
A well-designed mould not only defines the shape of the part but also ensures proper material flow, cooling, and ejection. It can include features like runners, gates, vents, and cooling channels, all of which must be carefully engineered to optimize cycle time and part quality.
Mould fabrication can take several weeks and requires advanced CNC machining and EDM (electrical discharge machining). While the upfront cost is significant, a high-quality mould can produce millions of consistent plastic parts with minimal maintenance, making it a worthwhile investment for large-scale production.
Injection Moulding Machines: Where Precision Meets Power
With the mould ready, it’s time to move to the injection moulding machine. These powerful systems melt plastic pellets and inject them into the mould under high pressure. Machines range in size and capability, from compact desktop units to industrial-scale systems producing automotive or aerospace components.
Three main types of machines dominate the industry: hydraulic, electric, and hybrid. Hydraulic machines are known for their robust clamping force, while electric machines offer cleaner, quieter, and more energy-efficient operation. Hybrids aim to combine the best of both worlds.
Regardless of type, these machines are engineered for precision. Temperature controls, pressure sensors, and computer-aided controls ensure every shot is consistent, minimizing variation and defects. The harmony between machine, mould, and material is what brings injection moulding plastic parts to life.
The Moulding Process: How Plastic Becomes Product
The heart of injection moulding lies in the process itself. It unfolds in several stages:
-
Melting: Plastic granules are fed into a heated barrel where they are melted by friction and heaters.
-
Injection: The molten plastic is injected into the closed mould cavity at high pressure.
-
Cooling: As the plastic cools and solidifies, it takes the shape of the mould.
-
Ejection: Once cooled, the mould opens, and ejector pins push the finished part out.
Timing, temperature, and pressure must be meticulously controlled at each step. Too much heat or pressure can damage the mould or the part. Too little, and the part may be incomplete or warped. Advanced moulding systems use sensors and feedback loops to monitor the process in real time, ensuring consistency and quality in every injection moulding plastic part produced.
Quality Control: Ensuring Perfection in Every Plastic Part
Creating consistent, defect-free plastic parts at high volumes demands rigorous quality control. The process starts with dimensional inspections using tools like calipers, coordinate measuring machines (CMM), or laser scanners to verify the parts meet design specifications.
Surface finish and cosmetic appearance are also checked, especially for consumer-facing products. Any signs of warping, sink marks, flash, or discoloration are identified and corrected.
Mechanical and environmental tests—such as tensile strength, impact resistance, and thermal cycling—may be conducted based on the part’s intended use. Advanced facilities may also implement statistical process control (SPC) to monitor trends and detect anomalies before they turn into defects.
Through careful inspection and testing, manufacturers ensure each injection moulding plastic part is ready to meet performance expectations in the real world.
Post-Moulding Operations: Adding Value After the Shot
The journey doesn’t always end at ejection. Many injection moulding plastic parts go through post-moulding operations that enhance their function or appearance.
Common steps include:
-
Trimming: Removing excess plastic or flash.
-
Painting or Printing: Adding color, logos, or labels.
-
Ultrasonic Welding: Joining two plastic components without adhesives.
-
Assembly: Combining the plastic part with other components into a finished product.
-
Packaging: Preparing the part for shipping or retail display.
These secondary processes are often integrated into automated production lines, ensuring speed and consistency. In many cases, the value added after moulding can be as important as the part itself—especially in consumer products where aesthetics and usability are critical.
Sustainability and Innovation: The Future of Injection Moulding Plastic Parts
As industries evolve, so does the demand for greener, smarter manufacturing. Injection moulding is keeping pace through several innovations aimed at sustainability and efficiency.
-
Biodegradable and Recycled Materials: More manufacturers are turning to plant-based or recycled resins to reduce environmental impact.
-
Energy-Efficient Machines: Electric and hybrid injection moulding machines consume less power and produce less waste.
-
Smart Factories: Industry 4.0 technologies like IoT, AI, and predictive maintenance are optimizing production and minimizing downtime.
Innovative moulding techniques such as micro moulding, gas-assisted moulding, and multi-shot moulding are expanding the capabilities of what plastic parts can do. As sustainability and precision continue to shape manufacturing, the future of injection moulding plastic parts looks both promising and transformative.
From Vision to Reality Through Injection Moulding
Injection moulding plastic parts represent the perfect fusion of creativity, engineering, and manufacturing. From the initial design on a screen to the final product in a user’s hand, each stage of the process contributes to a remarkable transformation. The power of injection moulding lies in its ability to deliver complex, precise, and high-quality parts at scale—quickly and cost-effectively.
As industries demand more from their components and customers seek faster, greener, and smarter solutions, injection moulding will continue to play a vital role in shaping the products of tomorrow. From concept to creation, it’s a process full of precision, power, and a bit of magic.