- April 24, 2025
- Posted by: feinuojixie
- Category: Injection Molding News
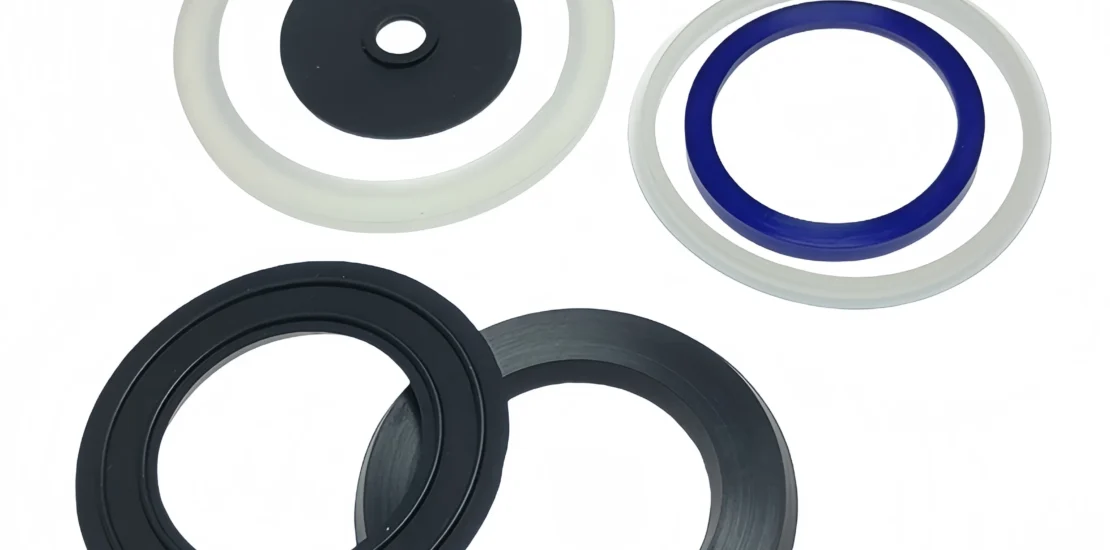
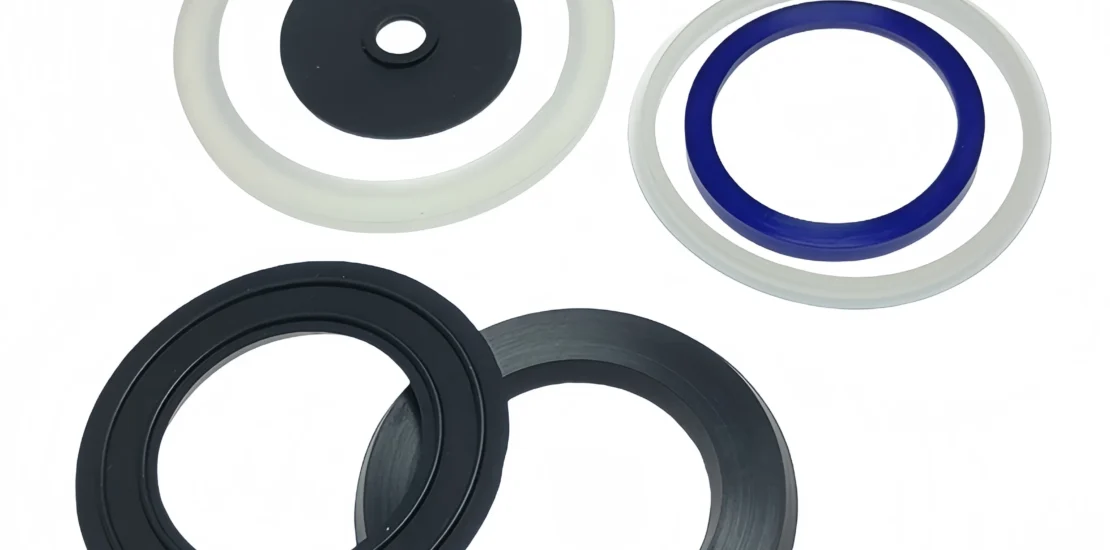
In a world where time-to-market, performance, and design all play critical roles in product success, injection moulding stands out as a manufacturing powerhouse. It delivers plastic parts with a rare combination of precision, speed, and strength—factors that are essential across industries from automotive and aerospace to consumer goods and healthcare. At the heart of this process lies the ability to shape complex forms with consistent quality and efficiency. Whether you are creating intricate components or robust everyday items, injection moulding plastic parts has become the go-to method for turning vision into reality.
How Injection Moulding Plastic Parts Are Made
The process of creating injection moulding plastic parts begins with the selection of the right thermoplastic material. Granules of this material are fed into a heated barrel, where they are melted and injected into a precision-engineered mould cavity under high pressure. Once the molten plastic fills the mould, it is cooled rapidly to form the desired shape. After cooling, the mould opens, and the part is ejected—ready for use or further processing.
This highly automated cycle can be completed in seconds, making it one of the most efficient manufacturing methods available. From initial design to final product, every step is optimized for repeatability and consistency, which is why injection moulding is trusted for high-volume production runs of plastic parts with tight specifications.
Why Injection Moulding Plastic Parts Offer Unmatched Accuracy
Precision is one of the hallmarks of injection moulding. Modern machines are capable of achieving tolerances within fractions of a millimeter, making the process ideal for applications where accuracy is non-negotiable. This includes everything from micro-sized medical devices to detailed enclosures for electronics.
Computer-aided design (CAD) software plays a crucial role in ensuring the final plastic parts match the original specifications. These designs are converted into moulds using CNC machining, which carves out exact geometries in steel or aluminum tooling. This precision tooling ensures every plastic part produced is virtually identical, no matter how many cycles are run.
How Injection Moulding Plastic Parts Accelerate Production Timelines
In competitive markets, speed can be the deciding factor between success and failure. Injection moulding delivers high-speed manufacturing without sacrificing quality. Once a mould is created, it can be used to produce thousands—or even millions—of identical parts with extremely short cycle times.
Industries that operate on rapid product development timelines, such as consumer electronics and automotive, rely heavily on injection moulding. The ability to launch new designs quickly while maintaining consistency makes this process essential for keeping up with demand and staying ahead of the competition.
The Structural Integrity of Injection Moulding Plastic Parts
Strength is often a critical requirement for plastic parts, especially those used in demanding environments. Injection moulding supports a variety of engineering-grade plastics that offer excellent tensile strength, impact resistance, and thermal stability.
Additionally, fillers like glass fibers or mineral reinforcements can be added to improve structural performance. This versatility allows manufacturers to create parts that meet strict safety and durability standards in sectors such as aerospace, industrial equipment, and medical technology—all while keeping production efficient and cost-effective.
Design Freedom with Injection Moulding Plastic Parts
Injection moulding allows for exceptional design flexibility. Complex shapes, undercuts, and integrated features like hinges or snap-fits can be built directly into the part design. This means fewer assembly steps and improved product functionality.
Furthermore, the aesthetic aspect of plastic parts can be tailored during the moulding process. Texture, color, and even branding elements such as logos can be incorporated directly into the mould, eliminating the need for secondary processes like painting or labeling.
This level of customization opens up creative possibilities for product designers while maintaining the practical benefits of manufacturing efficiency.
How Injection Moulding Plastic Parts Save Costs in the Long Run
While the initial investment in mould creation can be high, the long-term cost benefits of injection moulding are substantial. Once the mould is built, the per-unit cost drops significantly as production volume increases.
Material waste is minimal, and automation reduces the need for manual labour, further lowering production costs. For businesses focused on scalability and profitability, injection moulding provides a dependable path to cost control and operational efficiency.
Making Eco-Friendly Choices with Injection Moulding Plastic Parts
Sustainability is becoming a priority for manufacturers worldwide, and injection moulding is evolving to meet these expectations. Many modern machines are designed with energy efficiency in mind, and closed-loop systems are being used to recycle excess material back into the production process.
Moreover, a growing range of biodegradable and recyclable plastics is available, allowing businesses to choose materials that align with their environmental goals. Designing plastic parts for end-of-life recyclability also helps reduce waste and support a circular economy.
What’s Next for Injection Moulding Plastic Parts in a Changing World
The future of injection moulding is being shaped by innovation. Smart factories equipped with sensors and AI-driven analytics are enabling real-time quality control and predictive maintenance. This ensures not only higher output but also improved reliability and reduced downtime.
Advancements in material science are introducing new types of plastics with enhanced properties—such as flame retardancy, conductivity, or antimicrobial protection—further expanding the possibilities of what injection moulding can achieve.
As digital transformation continues, expect injection moulding to become even more adaptive, data-driven, and sustainable.
Why Injection Moulding Plastic Parts Are the Smart Choice
Precision, speed, and strength—these core advantages define injection moulding and set it apart as a leading manufacturing method for plastic parts. Its ability to produce high-quality components quickly, accurately, and at scale makes it a cornerstone of modern production.
Whether you’re bringing a new product to market, optimizing an existing design, or aiming for greater sustainability, injection moulding offers the flexibility and performance to meet your goals. It’s not just a manufacturing process—it’s a strategic advantage.