- April 24, 2025
- Posted by: feinuojixie
- Category: Injection Molding News
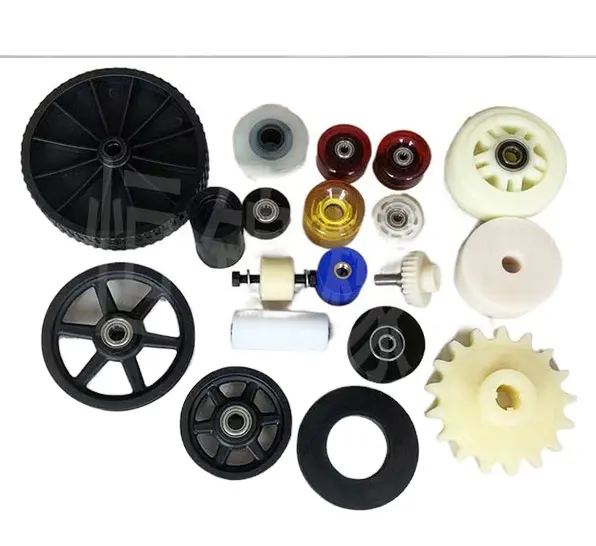
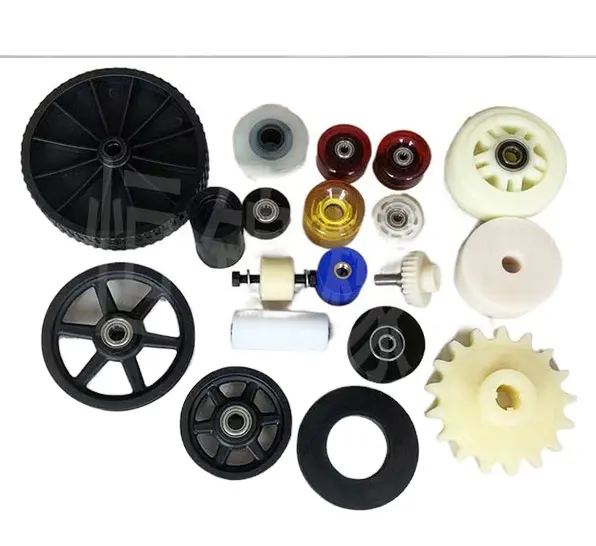
In the world of product development and manufacturing, choosing the right method for producing a plastic part can make the difference between success and delay, cost-efficiency and overspending. Two of the most widely used technologies—injection moulding and 3D printing—offer distinct advantages depending on the application, quantity, and complexity of the part being produced.
While injection moulding has long been the industry standard for mass-producing plastic part with precision and speed, 3D printing has rapidly gained popularity for its flexibility and ability to produce detailed designs without the need for tooling. As businesses navigate tight deadlines, cost constraints, and ever-evolving design requirements, understanding the strengths and trade-offs of these two manufacturing methods is essential.
This article dives deep into the processes, cost structures, design capabilities, and environmental considerations of injection moulding and 3D printing. Whether you’re developing a prototype or preparing for full-scale production, this guide will help you decide which process is better suited for your plastic part project.
Understanding Injection Moulding for Plastic Part Production
What Is Injection Moulding?
Injection moulding is a traditional manufacturing method where molten plastic is injected into a pre-designed mould cavity under high pressure. Once the plastic cools and solidifies, the mould opens, and the finished plastic part is ejected. This process is ideal for producing high volumes of consistent, high-quality part with tight tolerances. The initial setup involves creating a steel or aluminum mould, which is a significant upfront investment but pays off in high-output scenarios.
When Is Injection Moulding Most Effective?
Injection moulding excels in large-scale production due to its fast cycle times and repeatable results. It is widely used in industries like automotive, consumer electronics, medical devices, and packaging. If the goal is to produce thousands or millions of identical plastic part with high strength and durability, injection moulding remains the go-to solution.
Exploring 3D Printing for Plastic Part Manufacturing
What Is 3D Printing and How Does It Work?
3D printing, or additive manufacturing, builds a plastic part layer by layer based on a digital model. Technologies such as FDM (Fused Deposition Modelling), SLA (Stereolithography), and SLS (Selective Laser Sintering) allow for the creation of complex designs directly from CAD files, with no need for tooling or moulds. This digital-driven process allows for unmatched design freedom and rapid turnaround.
Why Choose 3D Printing?
The main advantage of 3D printing is its flexibility. It allows for fast prototyping, one-off designs, and small-batch production without the need for costly moulds. For product development cycles, R&D, and startups testing new designs, 3D printing offers an accessible, low-risk way to bring a plastic part to life quickly and affordably.
Comparing Cost Efficiency
Upfront Cost and Tooling Investment
Injection moulding requires expensive mould creation, often costing thousands to tens of thousands of dollars. However, once the mould is made, the cost per plastic part drops significantly in large quantities. In contrast, 3D printing has minimal setup costs—no tooling is needed—making it much more affordable for low-volume runs or prototypes.
Per Unit Cost in Mass vs Low-Volume Production
While 3D printing is cost-effective for producing a few units, its per-unit cost does not decrease significantly with volume. Injection moulding becomes more economical as production scales, making it the more efficient option for high-volume manufacturing of plastic part.
Design Flexibility and Complexity
Geometric Freedom in 3D Printing
3D printing supports highly complex shapes, internal channels, lattice structures, and undercuts that would be impossible or extremely costly with injection moulding. Designers can innovate freely without worrying about mouldability constraints, making it ideal for unique plastic part with complex geometries.
Design Constraints in Injection Moulding
Injection moulding requires careful attention to design limitations such as draft angles, wall thickness, and parting lines. These constraints ensure the part can be ejected from the mould without defects. Although design changes are possible, they can be expensive if the mould needs to be altered or remade.
Material Choice and Part Strength
Material Options Available
Injection moulding supports a vast range of thermoplastics, including high-performance engineering materials that offer excellent mechanical and thermal properties. 3D printing materials are more limited, although advances in industrial 3D printers are closing the gap.
Durability and Structural Integrity
Plastic part made via injection moulding tend to have superior structural integrity and uniformity compared to those made with 3D printing. Printed part may exhibit layer lines or weaknesses between layers, especially under stress or in load-bearing applications.
Speed of Production
Prototype to Final Product Timeline
3D printing shines in the early stages of development. A plastic part design can be printed and tested within hours or days, significantly reducing the time to market. Injection moulding, however, requires weeks or even months to produce a mould before the first part can be made.
Cycle Time and Output Rate
Once set up, injection moulding is extremely fast—capable of producing dozens of part per minute. 3D printing, by comparison, is slow for high volumes since each part must be printed individually or in small batches.
Environmental Impact and Waste
Sustainability in Injection Moulding
Injection moulding generates some waste from sprues and runners, but efficient recycling systems and automation reduce its environmental footprint over time. For mass production, its low energy consumption per part can be relatively eco-friendly.
Eco-Friendliness of 3D Printing
3D printing produces little waste since it only uses the material needed for the part. However, many materials are difficult to recycle, and post-processing chemicals (e.g., for SLA) may impact sustainability. Still, for prototyping or small runs, its environmental impact can be lower.
Which Process Is Right for Your Plastic Part?
Decision Factors: Volume, Budget, Timeline, and Complexity
When choosing between injection moulding and 3D printing for a plastic part, consider the following:
-
Volume: High volumes favor injection moulding; low volumes favor 3D printing.
-
Budget: Limited budgets for early-stage development benefit from 3D printing.
-
Timeline: 3D printing is faster for initial samples; injection moulding is faster for high output after setup.
-
Complexity: Highly complex or customized part are better suited to 3D printing.
For many projects, a hybrid approach works best—3D print for prototyping, then transition to injection moulding for production.
Conclusion
Both injection moulding and 3D printing offer valuable solutions for manufacturing a plastic part, each excelling in different contexts. Injection moulding delivers speed, strength, and scalability for mass production, while 3D printing provides flexibility, innovation, and low-cost prototyping.
By evaluating your project’s needs—whether it’s cost, complexity, or volume—you can choose the right method to produce your plastic part efficiently and effectively. The key is understanding not just the capabilities of each technology, but also how they align with your goals and constraints.