- April 29, 2025
- Posted by: feinuojixie
- Category: Injection Molding News
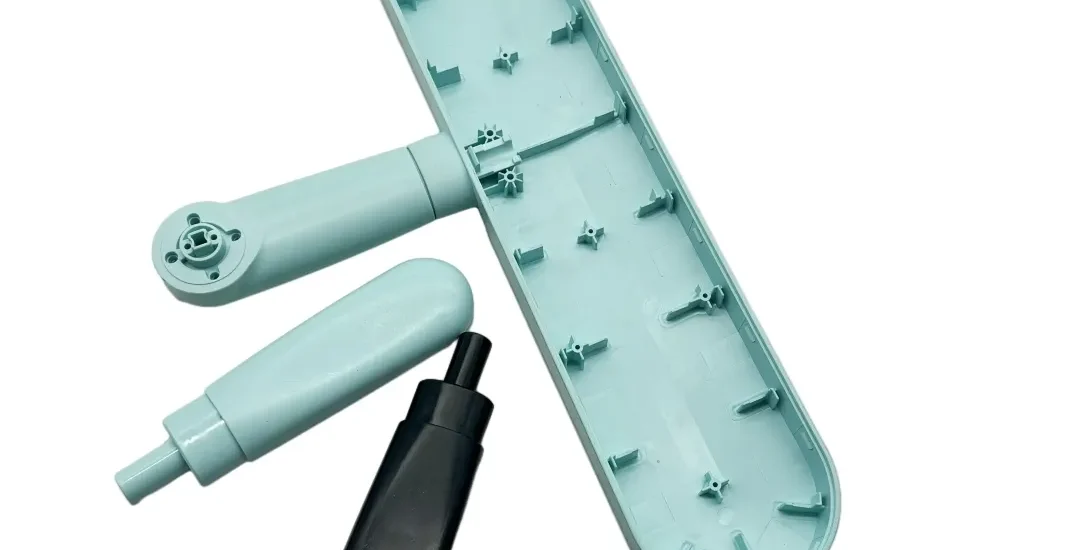
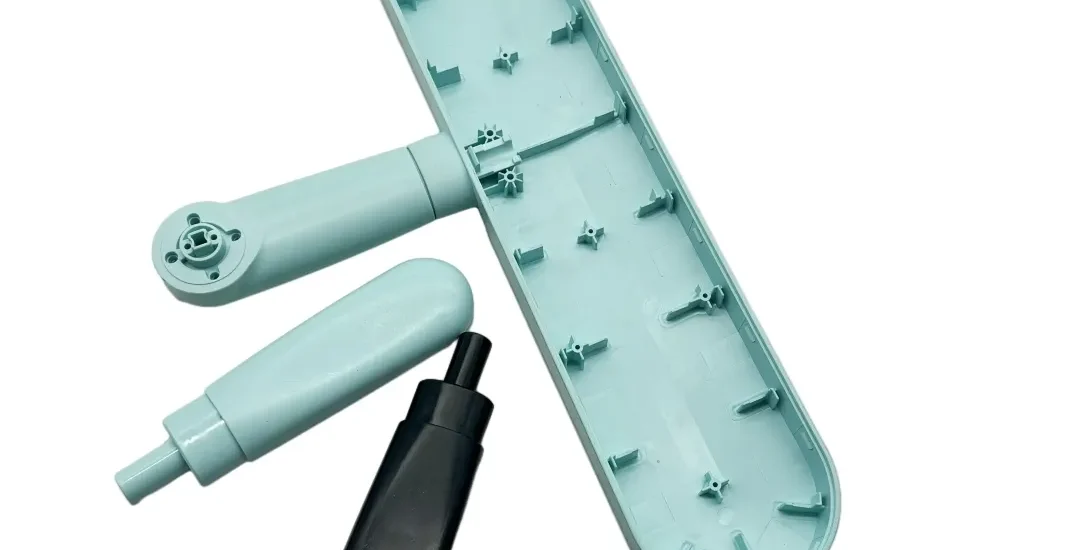
When it comes to product development, the plastic injection molded part you choose can make or break your project. Whether you’re building a consumer gadget, automotive component, or industrial device, the right part ensures durability, functionality, and cost-efficiency. Many product failures stem not from design flaws but from poor component choices made early in the development cycle. Selecting a plastic injection molded part is not just about shape or material—it’s about how the part fits into the bigger picture of manufacturing performance, assembly ease, and product longevity. Understanding what to look for upfront gives your project a solid foundation for success.
Understand the Role of the Plastic Injection Molded Part in Your End Product
Before you source or design a plastic injection molded part, you must fully understand its role within your product. Will it support structural loads, serve as a visible exterior, or perform a mechanical function? Clearly identifying its purpose helps determine the required strength, tolerance, and environmental resistance. For example, a part that houses electronics must be heat-resistant and insulating, while a cosmetic panel needs superior surface finish. Without this clarity, you risk compromising on quality or overengineering the part, driving up unnecessary costs.
Start with Material Selection for Optimal Performance
Material selection is one of the most critical decisions when choosing a plastic injection molded part. Different polymers offer distinct mechanical, thermal, and chemical properties. ABS, for example, offers good impact resistance, while nylon provides excellent wear resistance for moving parts. Consider the conditions the part will face—extreme temperatures, UV exposure, or chemical contact—and choose a resin that can withstand them. In many cases, a blend or engineered material may offer the best balance between performance and price. Working with a knowledgeable supplier can help you navigate material options efficiently.
Evaluate Mold Design Precision for Consistent Quality
The quality of the mold directly influences the quality of every plastic injection molded part it produces. Precision in cavity dimensions, cooling channels, and gate placement ensures consistent output with minimal defects. Even a small deviation in the mold can lead to warping, sink marks, or dimensional errors in the final part. It’s essential to review the mold design in collaboration with engineers who understand how mold flow and shrinkage affect the finished product. Investing in high-precision tooling may cost more upfront but delivers long-term savings through fewer reworks and rejects.
Prioritize Manufacturer Experience in Plastic Injection Molded Part Production
Not all manufacturers are created equal. Choosing a supplier with deep experience in plastic injection molded part production can save you from delays, quality issues, and communication headaches. An experienced team knows how to optimize mold designs, handle complex geometries, and anticipate potential defects before they occur. They can also provide insights on design for manufacturability, helping you tweak the part early to avoid costly changes later. Ask for case studies, certifications, and examples of past projects that match your part’s complexity and requirements.
Consider the Volume Requirements and Production Scalability
Volume matters more than many realize when choosing the right plastic injection molded part. A part that works well in a prototype or small batch might not be cost-effective or scalable in full production. Low-volume projects may benefit from aluminum molds and simpler gating systems, while high-volume runs require hardened steel tools and automated systems for repeatability. Make sure your design and material choices align with your production goals. Planning for scalability from the start avoids redesigns and supports a smooth transition from prototype to mass production.
Assess Surface Finish and Aesthetic Requirements Early On
Surface finish is more than a cosmetic detail—it impacts the perceived quality and even the functionality of a plastic injection molded part. Whether you need a glossy consumer-facing shell or a matte industrial enclosure, finishing requirements must be defined before mold fabrication begins. The mold surface must be prepared to exact texture specifications, and certain materials take finishes better than others. Waiting until after production to address appearance can lead to costly mold rework or subpar visual results. Set your finish expectations early and ensure the design accommodates them.
Check Regulatory Compliance and Industry Standards
Depending on your industry, the plastic injection molded part may need to meet specific regulatory or safety requirements. Medical, automotive, aerospace, and food-contact products all have strict material and testing standards. Using a non-compliant resin or overlooking certification requirements can result in failed audits, product recalls, or legal consequences. Work with a supplier who understands these obligations and can provide documentation such as UL ratings, FDA approvals, or ISO certifications. It’s better to build compliance into the design than to scramble for it later.
Analyze Cost vs. Value: Don’t Just Pick the Cheapest Option
While it’s tempting to choose the least expensive option, the true cost of a plastic injection molded part includes far more than its unit price. A cheaper part may have higher failure rates, longer cycle times, or hidden quality issues. Consider long-term factors like tool life, material waste, downtime due to defects, and the total cost of ownership. Sometimes a slightly more expensive part made with better materials or tighter tolerances will yield better reliability and fewer production problems, ultimately saving you time and money.
Use Prototyping to Validate Plastic Injection Molded Part Performance
Before committing to full-scale production, use prototyping to test and validate your plastic injection molded part. Technologies like 3D printing or soft tooling let you assess fit, function, and durability without incurring high tooling costs. Prototypes can also reveal design flaws, assembly issues, or material weaknesses that may not be visible in CAD models. Early testing helps refine the part design, improve manufacturability, and reduce the risk of costly mistakes in production. Treat prototyping as a vital part of your development cycle, not an optional extra.
Collaborate Early with a Design and Manufacturing Team
The most successful plastic injection molded part projects involve close collaboration between designers, engineers, and manufacturers from day one. By aligning goals and sharing feedback early, you can spot challenges, adjust specifications, and streamline the mold development process. A collaborative approach ensures that design intent meets manufacturability, reducing iteration cycles and avoiding last-minute surprises. Include tooling experts, material specialists, and quality engineers in early discussions to gain a well-rounded perspective that improves the final outcome.
Making Smart Choices to Ensure Project Success
Selecting the best plastic injection molded part requires more than picking a design off the shelf. It demands a thoughtful, informed approach that considers performance, cost, compliance, and scalability from the beginning. By understanding the role of the part, choosing the right materials, partnering with the right team, and planning for every stage of production, you set your project up for success. These ten secrets are not shortcuts—they’re proven strategies for making smart, strategic decisions that pay off in quality, efficiency, and long-term value.