- April 29, 2025
- Posted by: feinuojixie
- Category: Injection Molding News
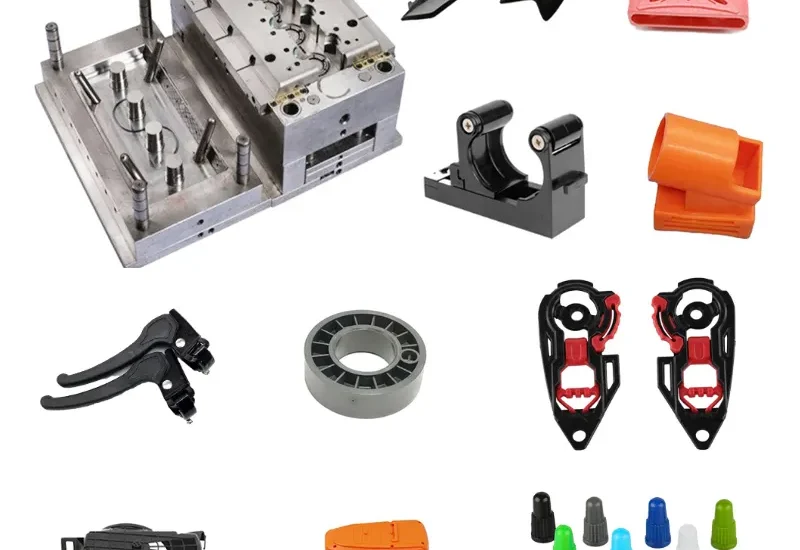
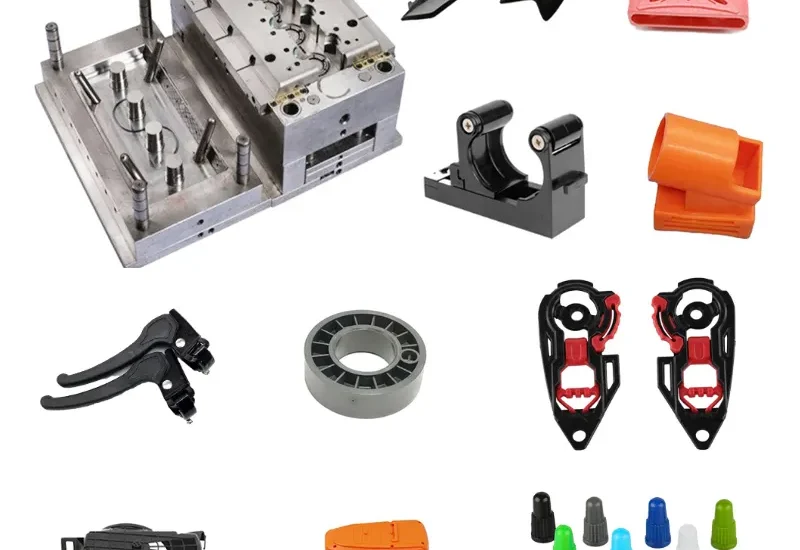
Plastic injection molding is one of the most widely used manufacturing processes, providing a fast, cost-effective way to produce a wide range of parts. From automotive components to household goods, plastic injection molded parts are integral to numerous industries. However, ordering these parts can be complex, and small mistakes in the ordering process can lead to significant production delays, increased costs, or suboptimal part quality. In this blog, we’ll explore common mistakes people make when ordering plastic injection molded parts and provide valuable tips on how to avoid them, ensuring a smooth and successful manufacturing experience.
Understanding the Basics of Plastic Injection Molding
Before diving into the common mistakes, it’s essential to understand the basic process of plastic injection molding. The process begins with melting plastic material, which is then injected into a mold cavity under high pressure. Once the material cools and hardens, it takes the shape of the mold. This method is highly versatile and allows for the production of intricate parts in high volumes. Industries ranging from automotive to electronics rely on plastic injection molded parts for their durability, precision, and cost-effectiveness. However, mistakes in the design or ordering process can have significant consequences, making it crucial to understand the basics of the process to avoid these pitfalls.
Common Mistakes When Ordering Plastic Injection Molded Part
Failing to Provide Accurate Specifications
One of the most common mistakes when ordering plastic injection molded part is providing inaccurate or incomplete specifications. These details—such as dimensions, material choices, and finish requirements—are the foundation for the mold design and the final product. Without precise information, the manufacturer can’t produce the part to the desired specifications, leading to costly reworks or delays. To avoid this mistake, ensure that you provide as much detail as possible about the part’s intended use, including any relevant environmental conditions (e.g., heat, UV exposure, etc.), which will impact material choice and part design.
Ignoring Material Selection
Material selection is a critical factor in the performance, cost, and longevity of a plastic injection molded part. Each material has its own properties, including strength, flexibility, temperature resistance, and chemical stability. Ignoring these characteristics when choosing materials can lead to parts that fail to meet functional requirements or are too costly for the intended application. Always consult with your supplier about material properties and select one that aligns with your part’s intended use and environmental conditions. A mistake here could result in a part that either underperforms or exceeds budget due to expensive, unnecessary material choices.
Underestimating Tooling Costs
Tooling is the design and creation of molds used to shape the plastic. Many people make the mistake of underestimating the cost of tooling when ordering plastic injection molded parts. The tooling process requires precision and high-quality materials, and its cost can significantly impact the overall cost of the project. If the tooling is poorly designed or made from low-quality materials, it can lead to part defects and production delays. To avoid this mistake, make sure you understand tooling costs upfront and factor them into your budget. High-quality tooling may come with a higher initial cost, but it often leads to better results in the long run.
Not Considering Tolerances and Quality Standards
Another common mistake is not taking tolerances and industry quality standards into account. Tolerances refer to the allowable deviations from the specified dimensions, and they play a significant role in ensuring that the part fits and functions properly in its intended application. If tolerances are too tight or not considered during the design phase, the part may not fit with other components or fail to perform under stress. Additionally, different industries have various quality standards, such as ISO or ASTM, which must be adhered to for safety, performance, and regulatory compliance. Always specify the required tolerances and quality standards early in the process to avoid costly mistakes down the line.
Overlooking Part Design Optimization
The design of the part itself can have a significant impact on the efficiency of the molding process. Overlooking design optimization is a mistake that can lead to increased production costs and wasted material. Design elements such as wall thickness, part geometry, and undercuts all affect how easily the mold can be created and how efficiently the part can be produced. A design that is not optimized for injection molding may result in defects, longer production times, and higher costs. Work closely with your designer and supplier to ensure that the part design is optimized for the injection molding process.
How to Avoid These Mistakes
Collaborating Closely with Your Supplier
One of the most effective ways to avoid mistakes is to establish a strong, collaborative relationship with your supplier. Communication is key to ensuring that both parties are on the same page regarding part specifications, materials, tolerances, and tooling requirements. Regularly review and discuss design concepts with your supplier and don’t hesitate to ask for clarification on any aspect of the project. A reputable supplier will provide guidance and advice based on their experience, helping you avoid common pitfalls.
Reviewing Prototypes and Samples
Another key step in avoiding mistakes is reviewing prototypes and samples before committing to mass production. Prototypes allow you to test the part’s design, material, and functionality, and they can help identify any potential issues early in the process. Once you approve the prototype, you can move forward with confidence, knowing that the part will meet your specifications. If the prototype reveals any issues, you can address them before production begins, saving both time and money.
Understanding Lead Times and Production Schedules
Lead times and production schedules play a crucial role in ensuring that your parts are delivered on time. Many people overlook these factors and fail to plan for potential delays. Always clarify the lead time with your supplier and ensure that the production schedule aligns with your project timelines. Keep in mind that factors such as tooling development, material availability, and the complexity of the design can all impact the timeline. Planning ahead and understanding the production schedule will help prevent rushed decisions that could lead to mistakes.
The Role of Experienced Professionals in Plastic Injection Molding
Working with experienced professionals is one of the best ways to avoid common mistakes when ordering plastic injection molded parts. Experienced manufacturers understand the intricacies of the molding process and can guide you through each step, from design to production. They can help you navigate the complexities of material selection, tooling, tolerances, and part design optimization. Choosing a reputable supplier with a proven track record ensures that your parts are manufactured to the highest standards, reducing the risk of mistakes and improving overall project success.
Conclusion
Ordering plastic injection molded part requires careful planning and attention to detail. By understanding the common mistakes and taking steps to avoid them, you can ensure a smoother and more successful ordering process. Be sure to provide accurate specifications, select the right material, factor in tooling costs, and consider tolerances and quality standards. Collaborate closely with your supplier, review prototypes, and understand production schedules to prevent issues. Lastly, working with experienced professionals will ensure that your parts meet the required specifications and are delivered on time. With these strategies in place, you can avoid costly mistakes and achieve the best possible results for your project.