- May 5, 2025
- Posted by: feinuojixie
- Category: Injection Molding News
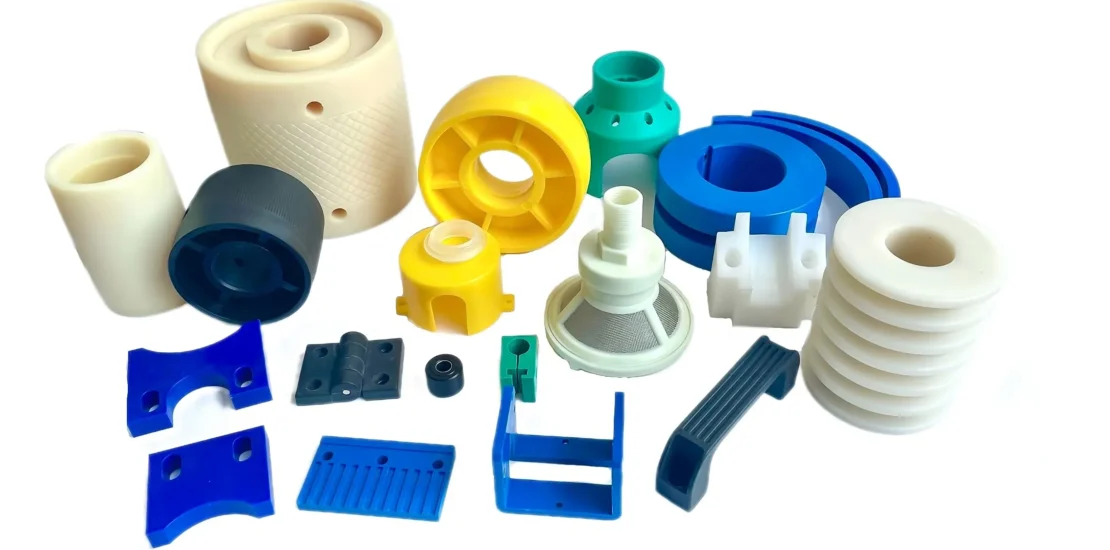
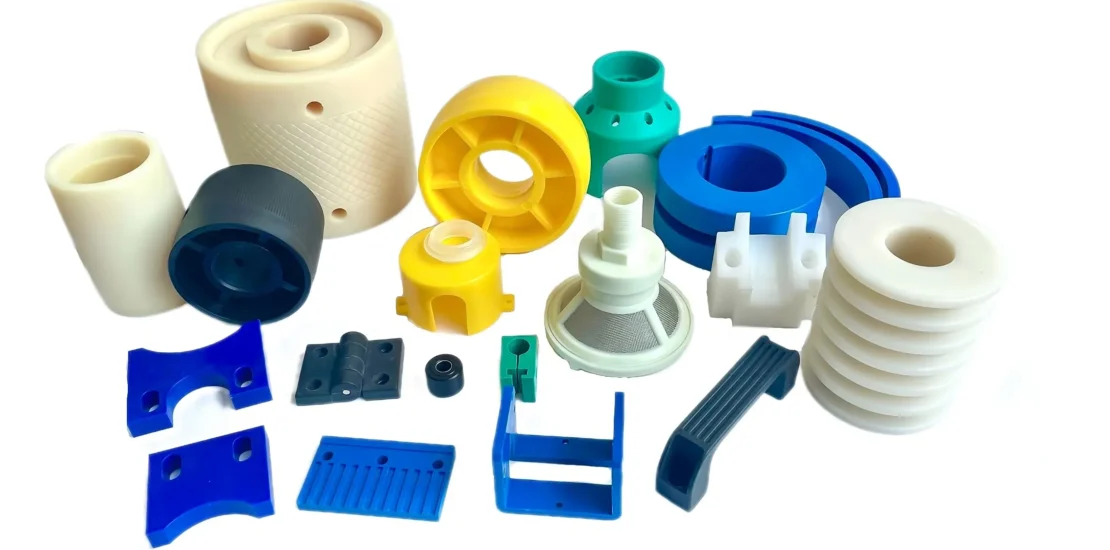
Large part injection molding is rapidly becoming a pivotal process in the manufacturing world. This method allows for the creation of large, high-precision parts that are crucial for various industries, from automotive to aerospace. The process involves injecting molten plastic into a mold under high pressure, forming complex and durable components in a cost-effective manner. In this article, we will explore how large part injection molding is revolutionizing manufacturing, making it more efficient, precise, and adaptable to the needs of modern industries.
The Evolution of Large Part Injection Molding: From Concept to Reality
Injection molding has been around for decades, but the ability to produce large parts with this technique is a relatively recent advancement. Early injection molding was primarily used for smaller, less intricate components. Over time, innovations in machinery, materials, and processes have allowed manufacturers to tackle larger, more complex parts. This evolution has been driven by advancements in machine size, molding pressure, and mold design, making large part injection molding a feasible option for a variety of industries. From its humble beginnings to its current capabilities, large part injection molding is now seen as a game changer in manufacturing, able to produce parts once thought impossible through traditional methods.
Why Large Part Injection Molding is Becoming a Game Changer in Manufacturing
Large part injection molding is reshaping the manufacturing landscape by offering numerous benefits that were previously unattainable. One of its most significant advantages is efficiency. This process allows manufacturers to create large parts with intricate designs much faster than traditional methods, reducing production time. In addition, the technology’s precision ensures that the final products meet exact specifications, which is crucial for industries that require high-quality standards, such as aerospace and automotive.
Another key benefit of large part injection molding is its cost-effectiveness. While the initial setup costs can be high due to the size of the machines and molds, the long-term savings are substantial. Once the system is in place, large part injection molding can produce parts at a lower cost per unit, reducing overall manufacturing expenses. The ability to produce large, complex parts in a single process, without the need for additional assembly, further drives down costs and enhances the competitiveness of businesses adopting this technology.
Industries Benefiting from Large Part Injection Molding
Many industries are reaping the rewards of large part injection molding, as it enables them to produce high-quality components that are both durable and lightweight. The automotive industry, for example, has embraced this process for creating large components such as bumpers, dashboards, and interior parts. The ability to mold these parts with precision ensures the safety, comfort, and functionality of vehicles while reducing the need for costly post-production modifications.
Aerospace and aviation manufacturers are also leveraging large part injection molding to produce lightweight, high-strength components for aircraft. These parts must withstand extreme conditions while maintaining their structural integrity, and injection molding allows for both strength and weight savings.
Consumer goods and electronics are another area where large part injection molding is making an impact. This process allows for the production of large, complex parts with minimal waste and reduced energy consumption, all while maintaining high levels of detail and functionality. As demand for more innovative and cost-effective products grows, industries across the board are turning to large part injection molding to meet these evolving needs.
Key Advantages of Large Part Injection Molding in Production
Large part injection molding offers several key advantages that make it an attractive option for manufacturers. One of the most significant benefits is the enhanced strength and durability of the molded parts. The high-pressure molding process results in parts that are more resilient and better able to withstand the stresses of their respective applications.
Additionally, the process minimizes material waste compared to other manufacturing methods. The precise control over the amount of material used, coupled with the ability to reuse excess material, makes large part injection molding an environmentally friendly choice. This reduction in waste not only helps the environment but also reduces costs associated with material procurement and disposal.
Perhaps one of the most appealing aspects of large part injection molding is the speed at which parts can be produced. In many cases, the entire process—from molding to cooling—can be completed in a fraction of the time it would take using traditional methods. This efficiency translates to shorter lead times, which is increasingly important in a fast-paced global marketplace.
Challenges in Large Part Injection Molding
Despite its many advantages, large part injection molding does come with its challenges. One of the primary obstacles is the complexity of molding large parts. The size and intricacy of the molds required for large parts demand advanced engineering and specialized equipment. Additionally, maintaining uniformity in the material flow and pressure during the molding process can be difficult, especially for larger components.
The initial investment required for large part injection molding is another consideration. The machines and molds needed to produce large parts are costly, and the setup process can be time-consuming. However, the high production capacity and long-term savings often justify these upfront costs.
Finally, environmental concerns related to large-scale plastic production remain a challenge. Manufacturers are increasingly pressured to adopt sustainable practices, such as using biodegradable materials or incorporating recycled plastics into the production process. Balancing production efficiency with eco-friendly practices is a key focus area for the industry as it continues to evolve.
Technological Advancements Paving the Way for Large Part Injection Molding
Technological advancements are continually improving the capabilities of large part injection molding. One of the key developments has been the evolution of more powerful and precise injection molding machines. These machines are now able to exert greater control over molding pressures and material distribution, allowing for more complex and uniform parts to be produced with greater ease.
In addition, the development of new materials has expanded the possibilities for large part injection molding. Today, manufacturers can use a wider range of thermoplastics and composites, each offering unique properties such as enhanced strength, flexibility, or resistance to heat. These material advancements have unlocked new potential for industries such as automotive and aerospace, where performance and safety are paramount.
Automation is also playing a significant role in the advancement of large part injection molding. Automated systems are streamlining the molding process by reducing human intervention, ensuring greater consistency and precision in production. Robotics are increasingly being used for tasks such as loading and unloading parts, trimming, and quality control, further boosting efficiency.
The Future of Large Part Injection Molding: What’s Next for the Industry?
Looking ahead, the future of large part injection molding is bright, with continued advancements on the horizon. As manufacturing processes become more sophisticated, the demand for large, high-precision parts will only increase. Emerging trends, such as the use of smart sensors to monitor and adjust the molding process in real-time, are set to further enhance efficiency and quality control.
Sustainability will also be a driving force in the future of large part injection molding. As industries look for ways to reduce their carbon footprint, eco-friendly materials and production techniques are expected to play a larger role. The development of biodegradable plastics, as well as the increased use of recycled materials, will help manufacturers meet sustainability goals without sacrificing performance.
The potential applications for large part injection molding are expanding beyond traditional industries. The technology is increasingly being explored for use in fields such as medical devices, renewable energy, and construction, where the need for durable, lightweight parts is critical. As these industries evolve, large part injection molding will continue to be a key player in driving innovation.
How Large Part Injection Molding Will Continue to Drive Industrial Innovation
Large part injection molding has already proven itself to be a transformative force in the manufacturing industry. With its ability to produce high-quality, durable parts efficiently and cost-effectively, it has become an indispensable tool for industries ranging from automotive to aerospace. As technology continues to evolve, the potential applications for this process will only grow, driving further innovation and shaping the future of manufacturing. The ongoing development of new materials, automated systems, and sustainable practices will ensure that large part injection molding remains a cornerstone of modern industrial production for years to come.