- May 7, 2025
- Posted by: feinuojixie
- Category: Injection Molding News
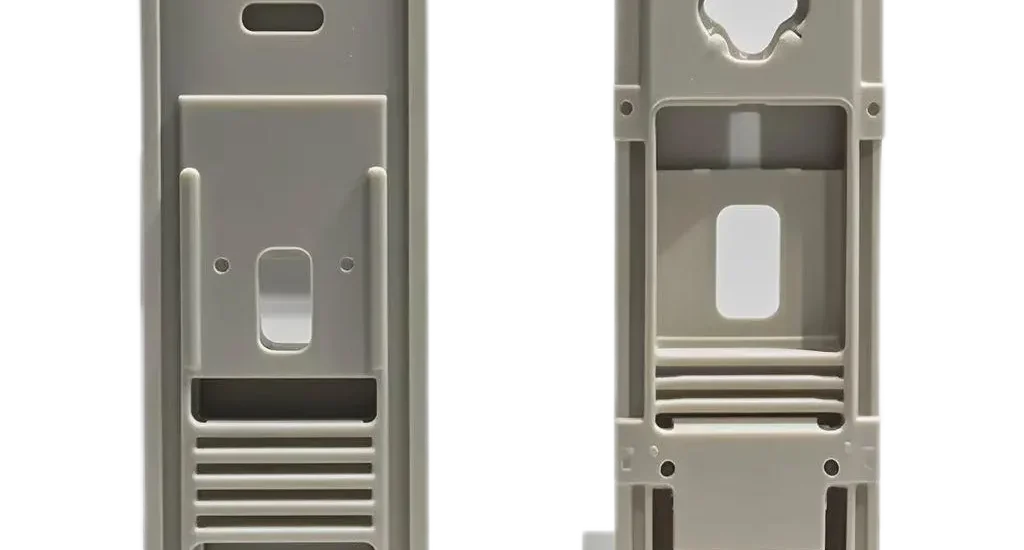
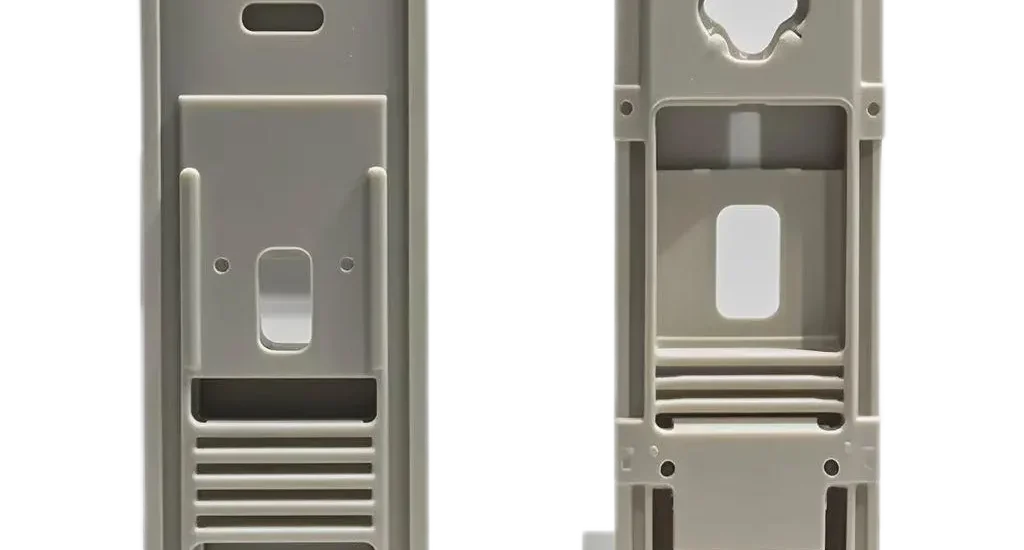
Plastic injection part may not grab headlines, but it is one of the most essential components driving the machinery of modern manufacturing. From the sleek casing of your smartphone to intricate components inside a car engine, plastic injection part plays a vital yet often overlooked role. Its significance lies in its versatility, scalability, and ability to deliver high-performance at low cost. As industries push for faster production and tighter tolerances, plastic injection part remains a quiet hero powering innovation behind the scenes.
The Rise of Plastic Injection Part in Industrial Evolution
The industrial revolution gave birth to mass production, but it was the advent of plastic injection molding in the mid-20th century that truly revolutionized manufacturing. Early uses focused on basic consumer goods, but the technology quickly matured. With advancements in machinery and polymer science, plastic injection part evolved from simple forms into highly precise, engineered solutions. Manufacturers across the globe began adopting the method to meet increasing demand for consistent, lightweight, and cost-effective components. Today, it stands as one of the most widely used manufacturing techniques.
Understanding the Plastic Injection Molding Process
At its core, the process of creating a plastic injection part begins with melting thermoplastic pellets and injecting the molten material into a steel mold cavity. Once the part cools and solidifies, it is ejected and inspected for quality. While the steps sound simple, each phase requires high-precision machinery and deep technical expertise. Mold design is especially critical, as it defines not just the shape, but the durability and accuracy of the final product. The cycle is fast—often just seconds—making it ideal for large-volume runs while maintaining tight tolerances.
Key Advantages of Using Plastic Injection Part in Manufacturing
Manufacturers favor plastic injection part for several compelling reasons. First, it offers remarkable design flexibility, allowing complex geometries that are hard to achieve with other methods. Second, it produces minimal waste, as excess material can often be recycled. Third, it ensures repeatability—parts come out nearly identical with each cycle. Most importantly, it drives down unit costs dramatically in high-volume production. These benefits combine to make plastic injection part a preferred choice in competitive, quality-driven environments.
Industries Relying on Plastic Injection Part
Plastic injection part serves as the backbone for many critical industries. In the automotive sector, it is used in everything from dashboard panels to under-the-hood components. The medical industry depends on it for sterile, single-use items like syringes and diagnostic equipment. Consumer electronics rely on it for sleek enclosures, connectors, and mounting brackets. Even aerospace manufacturers incorporate plastic injection part into their lightweight, high-strength systems. The common thread is reliability—each industry trusts the process to deliver consistent quality at scale.
Designing for Manufacturability: Engineering Plastic Injection Part
Successful production starts long before the mold is filled. Engineers must design plastic injection part with manufacturing in mind. This involves considering wall thickness to avoid warping, adding draft angles to aid ejection, and selecting materials that meet performance requirements. Failure to account for these factors can lead to defects or costly delays. Tools like computer-aided design (CAD) and simulation software help engineers test and refine their models before any tooling is created. This approach ensures the final part is not only functional but efficient to produce.
Innovations in Plastic Injection Molding Technology
The landscape of plastic injection molding is evolving rapidly. Micro-molding allows the creation of parts smaller than a grain of rice, critical for medical and electronic applications. Overmolding combines multiple materials into a single part, enabling hybrid products with both rigid and soft surfaces. Advanced polymers now offer properties such as flame resistance, UV stability, and anti-microbial surfaces. Smart sensors embedded in molds provide real-time data to fine-tune the process. These innovations are expanding what plastic injection part can achieve across all industries.
Sustainability and the Future of Plastic Injection Part
As environmental concerns grow, so does the pressure on manufacturers to adopt sustainable practices. Fortunately, plastic injection part is not at odds with sustainability. Many operations now incorporate recycled materials into their processes without compromising quality. Biodegradable resins are gaining traction in applications where long-term durability is not essential. Additionally, the energy efficiency of modern molding machines and the recyclability of scrap material contribute to a more circular production model. The future of plastic injection part includes both innovation and environmental responsibility.
Choosing the Right Partner for Plastic Injection Part Production
Choosing a qualified manufacturing partner is crucial to success. The ideal supplier offers not only state-of-the-art equipment but also deep technical expertise and a robust quality management system. Certifications such as ISO 9001 or ISO 13485 (for medical) indicate a commitment to standards. Look for partners who offer in-house mold design, material selection support, and fast prototyping. A good partner understands your product goals and collaborates to minimize time to market without sacrificing precision or durability.
Why Plastic Injection Part Will Continue to Drive Manufacturing Forward
The humble plastic injection part may rarely be seen or celebrated, but it holds together much of what we rely on in modern life. Its blend of precision, scalability, and adaptability ensures that it will remain indispensable across sectors. As technology advances and new challenges arise, plastic injection part will continue to evolve—quietly powering innovation, one molded component at a time.