- May 7, 2025
- Posted by: feinuojixie
- Category: Injection Molding News
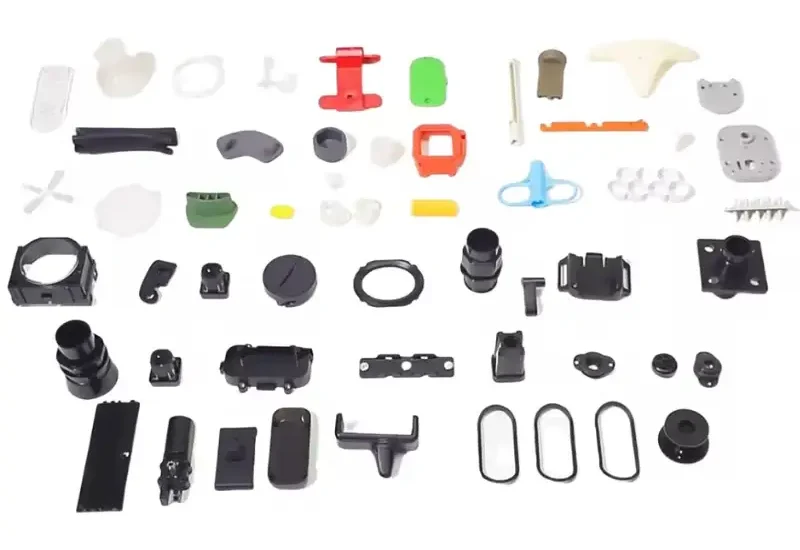
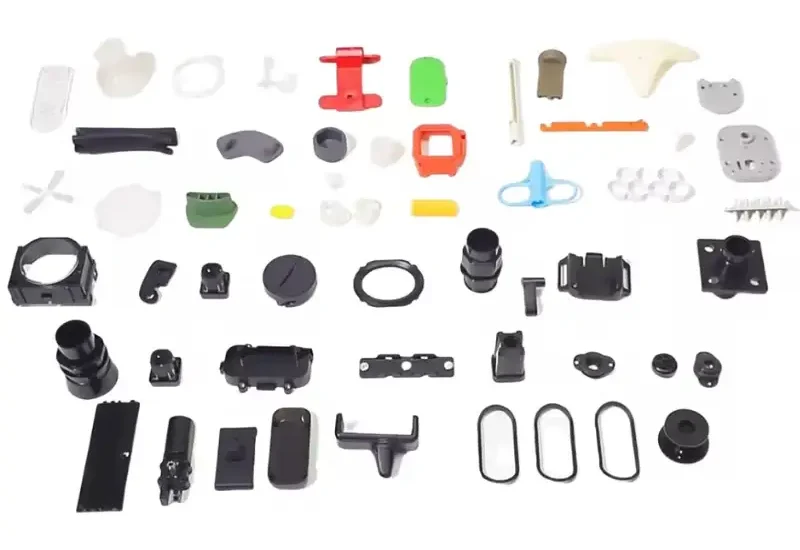
Plastic injection part are everywhere—from the buttons on your TV remote to precision components in medical devices. Behind every one of these products lies a meticulous process designed to maximize durability, accuracy, and cost-efficiency. The journey from raw plastic to a finished, market-ready part is anything but simple. It begins with thoughtful design and ends only when the final product meets rigorous quality standards. In this article, we’ll explore how plastic injection part are engineered not just to perform, but to endure. Whether you’re new to the field or looking to improve your product lifecycle, understanding this process is key to manufacturing success.
Designing for Durability: The Foundation of Long-Lasting Plastic Injection Part
Every high-quality plastic injection part starts with a precise design. Engineers and designers collaborate using advanced CAD software to create models that meet performance requirements, tolerances, and production feasibility. Material stress analysis, anticipated wear, and structural integrity are considered from the outset. The choice of design not only determines the appearance but also influences how well the part holds up under repeated use or environmental stress. In this stage, features such as wall thickness, rib placement, and draft angles are carefully calculated to avoid defects and ensure long-term durability.
Precision Mold Creation: Where Accuracy Begins
The mold is the blueprint for every plastic injection part, and its quality directly affects product consistency. Mold fabrication involves high-precision CNC machining and Electrical Discharge Machining (EDM) to carve detailed, hardened steel or aluminum tooling. Tight tolerances are maintained to ensure each cycle produces identical parts. Mold design also includes critical components like cooling channels, ejector pins, and gating systems. These elements control how plastic flows, cools, and exits the mold—each factor playing a role in preventing warping, voids, or other defects.
Material Selection: Choosing What Lasts
Not all plastics are created equal. The selection of the appropriate resin—such as ABS, polycarbonate, or nylon—depends on the part’s required strength, flexibility, chemical resistance, and thermal stability. Additives such as glass fibers, UV stabilizers, or flame retardants can be incorporated to further enhance durability. In applications like automotive or aerospace, the wrong material choice can lead to catastrophic failure, so material testing and specification alignment are essential. Making the right decision at this stage ensures the final part can withstand real-world conditions.
Injection Molding Process: Bringing Plastic Injection Part to Life
Once the mold and material are ready, the injection molding process begins. Thermoplastic pellets are fed into a heated barrel, melted, and injected into the mold cavity under high pressure. The molten plastic quickly fills the mold, taking on its shape, and then cools and solidifies. Timing, temperature, and pressure are tightly controlled to minimize shrinkage and internal stress. After cooling, the mold opens, and the part is ejected. This process may repeat thousands or even millions of times, so maintaining process stability is crucial to producing consistent, long-lasting part.
Quality Control: Ensuring Every Part Meets the Standard
Durability means nothing without consistency, and that’s where quality control plays its role. Each batch of plastic injection part undergoes inspections to verify dimensional accuracy, strength, surface finish, and defect-free construction. Techniques like coordinate measuring machines (CMM), visual inspection, and destructive testing are used to confirm the part meets all specifications. Statistical process control (SPC) is often employed to detect variations early and avoid costly recalls or failures in the field.
Post-Molding Processes: Finishing Touches That Matter
After molding, many plastic injection part require secondary operations to improve their functionality or appearance. Common processes include deflashing, surface texturing, ultrasonic welding, painting, or plating. These post-molding enhancements can increase wear resistance, improve grip, or meet aesthetic goals. Even seemingly minor steps, like trimming excess plastic or applying a surface treatment, contribute to the part’s overall quality and longevity.
Packaging and Logistics: Protecting Plastic Injection Part Until Delivery
Once manufactured, plastic injection part must be carefully handled to prevent damage before they reach their destination. Packaging is designed to shield parts from mechanical shock, dust, and moisture. Anti-static bags, molded trays, and shock-absorbing materials are often used. Just-in-time delivery systems may be implemented to reduce storage time and ensure part arrive fresh and ready for assembly or retail. Proper logistics play a silent but critical role in maintaining product quality.
Applications Across Industries: Where These Part Make a Difference
Plastic injection part serve as the backbone for components in countless industries. In automotive, they are used in dashboards, housings, and under-the-hood systems. In healthcare, they form the basis for syringes, inhalers, and surgical tools. Electronics manufacturers rely on them for casings, connectors, and micro components. The strength, repeatability, and design flexibility of injection molding allow these parts to perform in environments ranging from hospital rooms to outer space.
Sustainability in Production: Making Part to Last—And to Recycle
With increasing environmental awareness, many manufacturers are rethinking how they produce plastic injection part. Biodegradable polymers, recycled resins, and closed-loop systems are becoming standard practices. Design for disassembly and reuse is also gaining traction, helping extend the product lifecycle and reduce landfill waste. Even as companies strive for durability, they also aim to make part that can be responsibly retired or repurposed.
Built to Endure—Why Quality Plastic Injection Part Matter
From the first sketch to the final shipment, every decision in the manufacturing journey affects the performance and longevity of a plastic injection part. Attention to design, materials, precision tooling, process control, and inspection ensures that the end product is not only functional but resilient. In a world that demands reliability and efficiency, mastering the art of creating high-quality plastic injection part is essential to staying competitive—and sustainable—in the marketplace.