- May 9, 2025
- Posted by: feinuojixie
- Category: Injection Molding News
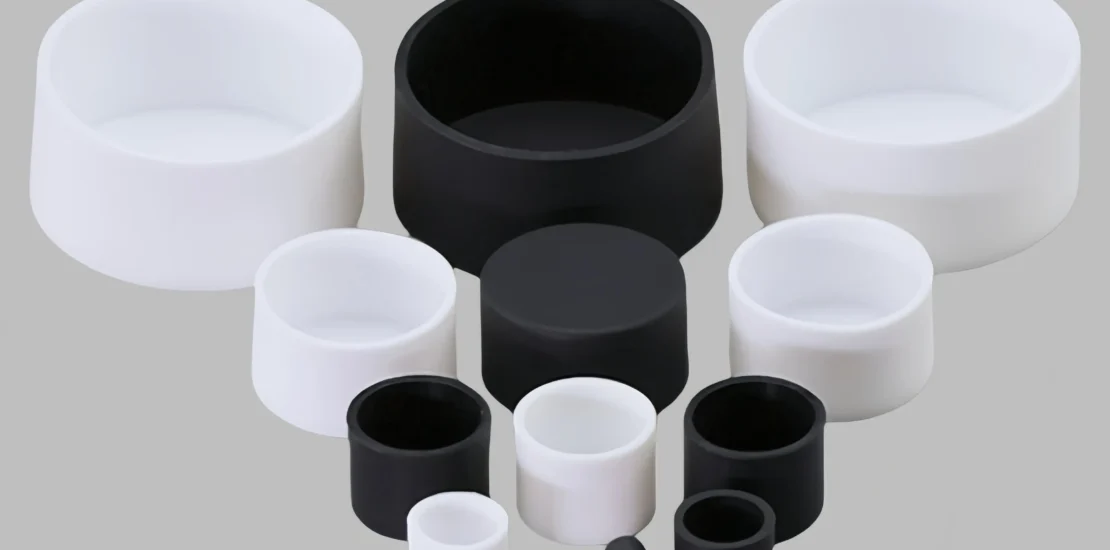
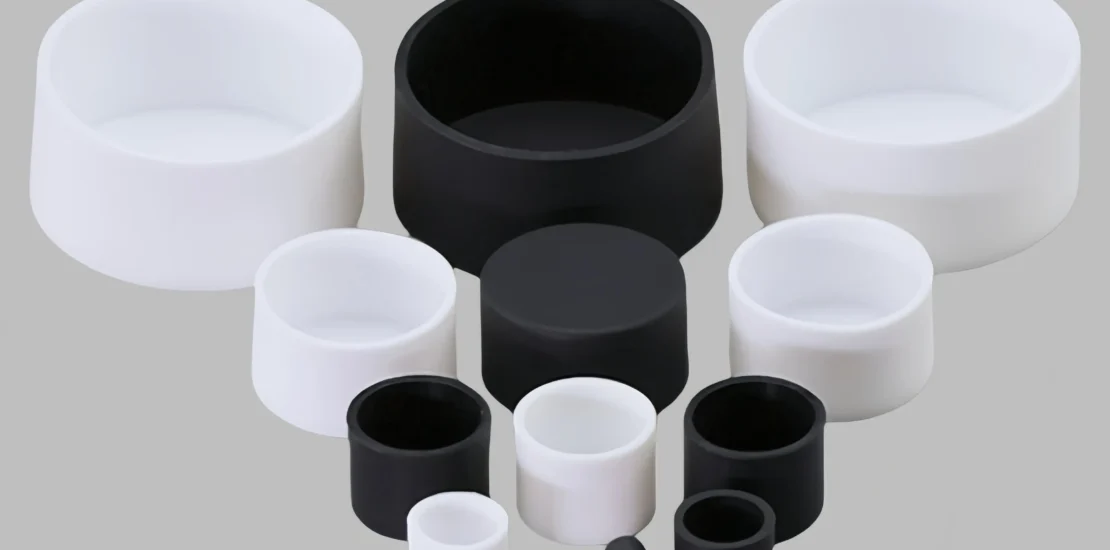
From car interiors to cutting-edge tech gadgets, plastic injection part have become the hidden champions of modern innovation. Once considered secondary to metal and other traditional materials, they are now reshaping how industries approach design, production, and performance. Their rise is driven by a need for lightweight materials, rapid production, and extreme precision—features that plastic injection molding delivers consistently. As the automotive and tech industries push the boundaries of functionality and sustainability, plastic injection part are at the heart of this transformation, quietly powering some of the most revolutionary products of our time.
Precision and Performance: Why Plastic Injection Part Are Ideal for Automotive Applications
Automotive manufacturing demands components that offer tight tolerances, repeatability, and structural integrity. Plastic injection part deliver exactly that. They are used in a wide range of applications including instrument panels, clips, sensor housings, and engine components. With the ability to mold intricate geometries, these parts reduce the number of assembly steps and ensure high performance under mechanical and thermal stress. Engineers favor them for their dimensional accuracy, which supports long-term durability and smooth vehicle operation.
Lightweighting the Future: Fuel Efficiency and Sustainability in Vehicles
As automakers strive to meet stricter fuel economy standards, lightweighting has become a critical design strategy. Replacing metal with plastic injection part significantly reduces overall vehicle weight. This translates directly into better fuel efficiency and lower carbon emissions. Moreover, the ability to consolidate multiple metal components into a single molded part reduces complexity and enhances efficiency in both design and manufacturing processes. Lighter cars are not only greener but also more agile and performance-driven—an essential in today’s competitive market.
Customization and Complexity: Meeting Tech Industry Demands with Plastic Injection Part
In the tech industry, product cycles are fast and consumer expectations are high. Plastic injection part offer the versatility needed to meet both challenges. They allow for complex shapes, thin walls, and integration of multiple features in one component—ideal for sleek, compact devices. Whether it’s the frame of a smartphone, internal brackets, or connector housings in laptops and wearables, the ability to customize parts without compromising strength or reliability gives tech companies a major edge in innovation.
Speed to Market: How Plastic Injection Part Accelerate Product Development Cycles
In both automotive and technology sectors, time-to-market is a critical factor. Plastic injection molding supports this urgency with rapid prototyping and scalable production. Design changes can be implemented swiftly using prototype tooling, allowing for fast iterations. Once finalized, the same process seamlessly transitions into mass production with minimal reconfiguration. This speed and efficiency are invaluable for companies racing to meet consumer demand or respond to market shifts.
Durability and Reliability: Enhancing Product Lifespan in Harsh Conditions
Modern vehicles and tech products are expected to perform in challenging environments—extreme temperatures, vibrations, moisture, and chemical exposure. Plastic injection part are engineered to withstand these conditions. High-performance resins like polyamide, PEEK, and polycarbonate offer excellent strength-to-weight ratios, chemical resistance, and thermal stability. This makes them ideal for under-the-hood automotive applications, industrial control units, and outdoor electronics.
Cost-Effective Innovation: Reducing Manufacturing Costs Without Sacrificing Quality
One of the standout benefits of plastic injection molding is its cost-efficiency. Once the mold is created, the per-part cost drops dramatically with volume, making it ideal for high-run production. Additionally, the ability to reduce waste, automate manufacturing, and minimize secondary processes like assembly or machining contributes to overall savings. Manufacturers can maintain high quality standards while keeping unit costs competitive—an ideal combination for industries under constant pressure to innovate at scale.
Sustainability and Recycling: The Green Potential of Plastic Injection Part
As industries seek greener alternatives, plastic injection part are evolving with sustainability in mind. More manufacturers are using recycled plastics and bio-based resins, which significantly reduce environmental impact. Some injection molding processes are also being optimized to reduce energy consumption and material waste. With growing infrastructure for recycling thermoplastics, the life cycle of a plastic injection part is becoming more circular, aligning with global sustainability goals.
Future Outlook: What’s Next for Plastic Injection Part in Automotive and Tech
The demand for high-performance, cost-effective, and sustainable parts will only intensify in the coming years. With the rise of electric vehicles, autonomous driving, smart home devices, and wearable tech, plastic injection part will continue to play a central role in innovation. Emerging materials, smarter design software, and even hybrid manufacturing techniques that combine injection molding with 3D printing are set to push the boundaries further. For companies aiming to stay competitive, investing in plastic injection part isn’t just a manufacturing decision—it’s a strategic one.