- March 17, 2025
- Posted by: feinuojixie
- Category: Injection Molding News
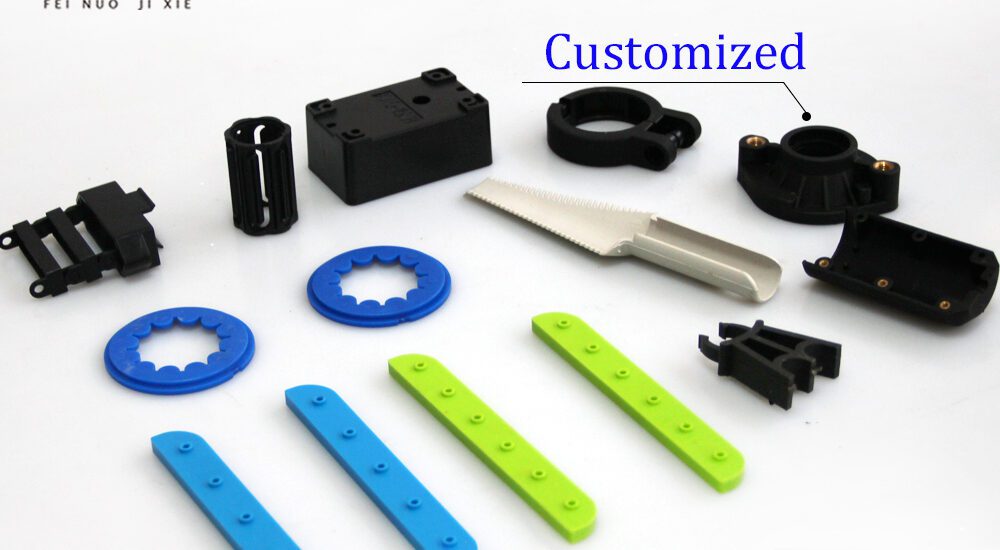
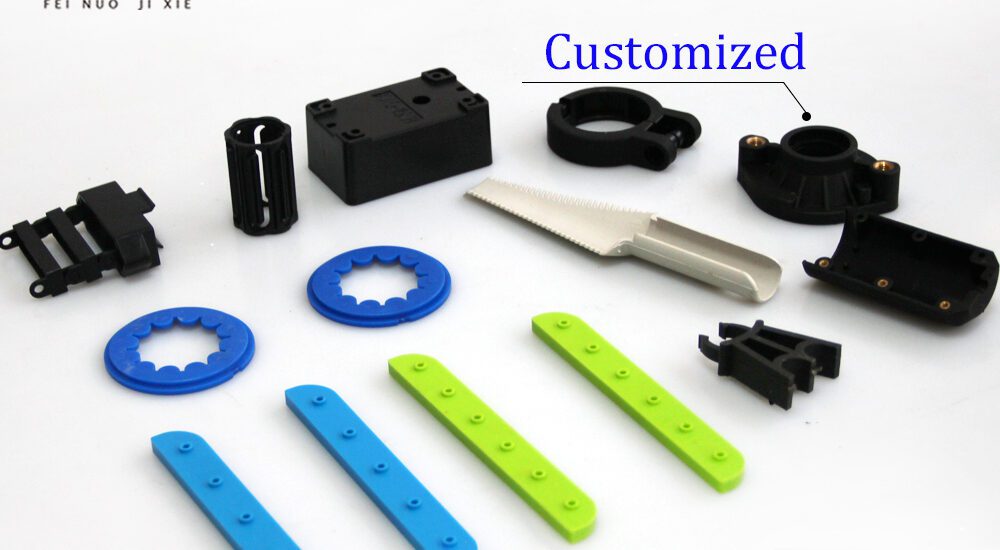
In the world of manufacturing, precision and durability are crucial for producing high-quality plastic parts. ABS injection moulding has emerged as a groundbreaking process that combines these two essential factors. As industries push for more reliable and accurate plastic components, ABS injection moulding plastic parts offer an exceptional solution. This article delves into the significance of ABS injection moulding, exploring its precise capabilities and long-lasting durability.
What is ABS Injection Moulding?
ABS, or Acrylonitrile Butadiene Styrene, is a thermoplastic polymer renowned for its strength and versatility. When used in the injection moulding process, ABS allows manufacturers to create plastic parts with high accuracy and durability. The injection moulding process involves injecting molten ABS plastic into a precisely designed mould under high pressure, where it cools and solidifies to form the final part. The ability to produce complex shapes and intricate details makes ABS injection moulding the preferred choice in various industries.
Why ABS Injection Moulding Plastic Parts Are Ideal for Precision
ABS injection moulding stands out for its ability to produce plastic parts with exceptional precision. The process allows for tight tolerances, which ensures that the finished product meets stringent design specifications. This level of precision is essential in applications where even the smallest deviation can lead to functional or aesthetic issues. Whether producing delicate, intricate components or large, structural parts, ABS injection moulding delivers highly accurate results that are critical for industries such as automotive, electronics, and consumer goods.
Unmatched Durability: How ABS Injection Moulding Enhances Plastic Parts
ABS injection moulding plastic parts are known for their outstanding durability. The material itself is impact-resistant, which makes it ideal for products that must withstand physical stress or harsh environments. In addition to its toughness, ABS offers excellent resistance to chemicals and weathering, allowing parts to maintain their integrity in a wide range of conditions. This durability makes ABS injection moulding a go-to solution for industries where longevity and reliability are paramount.
Applications of ABS Injection Moulding Plastic Parts
The versatility of ABS injection moulding plastic parts makes them suitable for a wide array of applications across multiple industries. In the automotive sector, ABS is used for everything from interior components to exterior panels, thanks to its strength and impact resistance. In electronics, ABS is favored for housings and enclosures due to its ability to protect sensitive components. The medical industry also benefits from ABS injection moulding for creating durable, precise components used in medical devices. ABS’s adaptability ensures it remains a critical material across diverse sectors.
The Advantages of ABS Injection Moulding for Manufacturers
ABS injection moulding offers several advantages to manufacturers. One of the most notable benefits is cost-effectiveness. The injection moulding process allows for high-volume production, reducing per-unit costs while maintaining high precision. Additionally, the speed of production and quick turnaround times ensure that products reach the market faster, providing manufacturers with a competitive edge. ABS’s inherent qualities, such as ease of colouring and processing, further enhance its appeal, making it an ideal choice for efficient, large-scale manufacturing.
Overcoming Challenges in ABS Injection Moulding
While ABS injection moulding offers numerous benefits, there are also challenges to be aware of. One common issue is the material’s susceptibility to warping during cooling, which can impact the final quality of the part. Furthermore, ensuring uniformity in wall thickness is crucial for achieving consistent results. However, with the right mould design and temperature control, these challenges can be mitigated. Manufacturers can also improve ABS performance by incorporating additives or modifying the processing conditions to enhance strength, stability, and appearance.
Future Trends in ABS Injection Moulding Plastic Parts
The future of ABS injection moulding looks promising, driven by ongoing technological advancements. Innovations in moulding techniques, such as 3D printing and automation, are enhancing the capabilities of ABS moulding processes. As industries demand even more precise and durable plastic parts, the development of new ABS formulations and processing methods will continue to expand the material’s applications. The growing focus on sustainability is also encouraging the creation of more eco-friendly ABS solutions, making it a material of choice for future manufacturing needs.
The Enduring Value of ABS Injection Moulding Plastic Parts
ABS injection moulding plastic parts are transforming industries by providing unparalleled precision, durability, and cost-effectiveness. Whether used in automotive, electronics, or medical applications, ABS continues to prove its value as a reliable material for producing high-quality plastic components. As manufacturing technologies evolve, the future of ABS injection moulding looks even brighter, offering new possibilities for innovation and growth across various sectors.