- March 13, 2025
- Posted by: feinuojixie
- Category: Injection Molding News
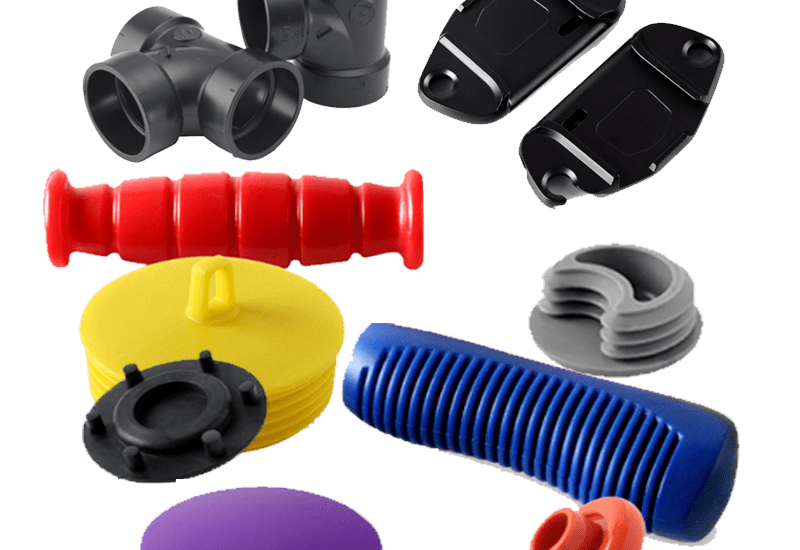
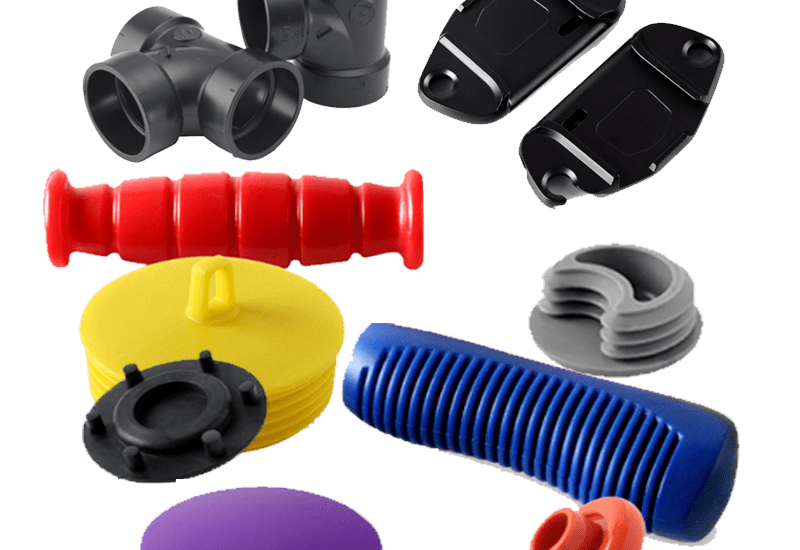
ABS injection moulding is a widely used manufacturing process known for its precision, durability, and versatility. This guide explores the fundamentals, advantages, applications, and key factors to consider when working with ABS injection moulding.
What is ABS Injection Moulding?
ABS injection moulding is a manufacturing process that involves injecting molten acrylonitrile butadiene styrene (ABS) into a mould cavity to create complex and durable plastic components. ABS is a preferred material due to its excellent mechanical properties, including impact resistance, toughness, and heat tolerance. Compared to other thermoplastics, ABS offers superior dimensional stability and ease of processing, making it ideal for high-precision applications.
The ABS Injection Moulding Process Explained
The ABS injection moulding process consists of several key steps:
- Material Preparation – ABS resin in the form of small pellets is dried to remove moisture, ensuring optimal material performance.
- Melting and Injection – The pellets are heated in the injection moulding machine until they reach a molten state. The material is then injected into the mould cavity under high pressure.
- Cooling and Solidification – Once inside the mould, the ABS material cools and solidifies, taking the shape of the mould. Cooling time varies based on part thickness and complexity.
- Ejection and Finishing – The mould opens, and the formed part is ejected. Additional post-processing, such as trimming or surface finishing, may be applied.
Common challenges in ABS injection moulding include warping, sink marks, and short shots. These can be minimized by optimizing temperature, pressure, and mould design.
Advantages of ABS Injection Moulding
ABS injection moulding offers several benefits that make it a popular choice in manufacturing:
- High Precision and Consistency – The process ensures tight tolerances and uniform quality in mass production.
- Excellent Durability – ABS components exhibit high impact resistance and wear tolerance, making them ideal for demanding applications.
- Cost-Effectiveness – Compared to other manufacturing methods, ABS injection moulding provides a cost-efficient way to produce high-volume plastic parts.
- Versatile Surface Finishes – ABS parts can be painted, plated, or textured to achieve various aesthetic and functional effects.
Key Applications of ABS Injection Moulding
ABS injection moulding is used across various industries due to its outstanding properties:
- Automotive Industry – Used in dashboards, trims, and protective housings due to its strength and heat resistance.
- Electronics – Commonly used for casings, housings, and connectors due to its electrical insulation properties.
- Consumer Products – Found in appliances, toys, and kitchenware because of its durability and ease of customization.
- Medical Equipment – Applied in medical device housings and instrument components, thanks to its chemical resistance and sterilizability.
Design Considerations for ABS Injection Moulding
To ensure optimal results, proper design strategies should be implemented:
- Wall Thickness Guidelines – Uniform wall thickness prevents defects such as warping and sink marks.
- Draft Angles – Including draft angles in mould design facilitates easy part ejection and prevents damage.
- Rib Structures – Reinforcing thin sections with ribs enhances structural integrity without adding excess material.
Factors Affecting ABS Injection Moulding Quality
Several factors influence the final quality of ABS injection moulding:
- Temperature Control – Proper temperature regulation ensures smooth material flow and prevents defects like burn marks or inconsistent textures.
- Injection Speed and Pressure – Optimized settings prevent short shots and voids while ensuring complete mould filling.
- Common Defects and Prevention – Warping, flash, and surface blemishes can be minimized with precise process control and mould maintenance.
Enhancing ABS Injection Moulding Performance
To improve the performance of ABS injection moulding parts:
- Use of Additives – Adding reinforcements, UV stabilizers, or flame retardants enhances specific properties.
- Surface Finishing Techniques – Processes such as painting, electroplating, and texturing improve appearance and functionality.
- Sustainability Considerations – Recycling ABS waste and using eco-friendly processing techniques help reduce environmental impact.
Choosing the Right Manufacturer for ABS Injection Moulding
Selecting a reliable manufacturer is crucial for achieving high-quality results:
- Expertise and Technology – Partnering with experienced manufacturers ensures precision and consistency.
- Quality Control Standards – Rigorous testing and inspection procedures guarantee defect-free products.
- Cost-Effectiveness – Balancing affordability with quality ensures optimal return on investment.
Future Trends in ABS Injection Moulding
Advancements in technology are shaping the future of ABS injection moulding:
- Innovations in Moulding Technology – Improved machinery and automation increase efficiency and precision.
- Sustainable Solutions – Development of biodegradable alternatives and enhanced recycling methods promote environmental responsibility.
- Integration of AI and Robotics – AI-driven process optimization and robotic automation enhance production capabilities.
Conclusion
ABS injection moulding remains a dominant process in manufacturing due to its precision, durability, and cost-effectiveness. Understanding its process, benefits, and best practices can help businesses achieve high-quality products with lasting performance.