- March 21, 2025
- Posted by: feinuojixie
- Category: Injection Molding News
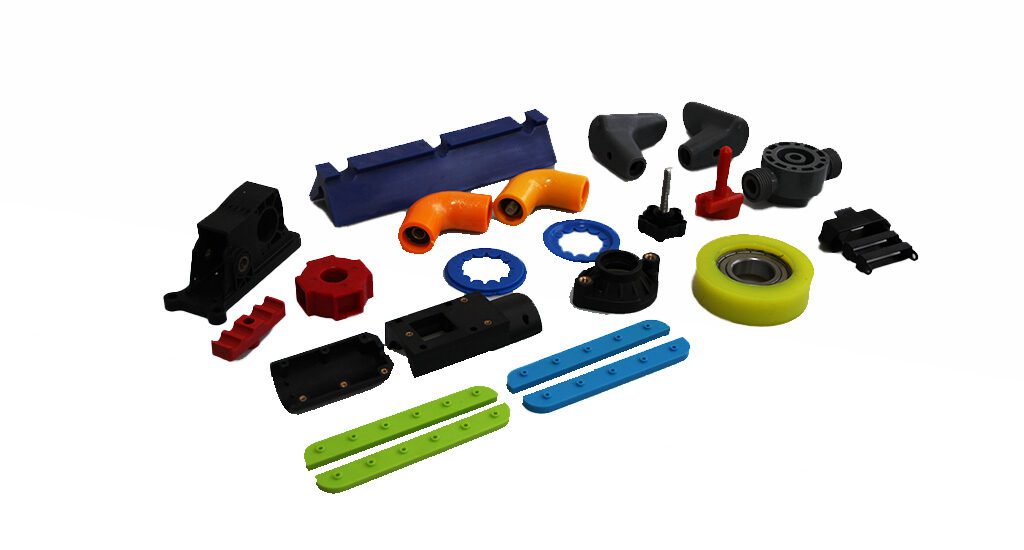
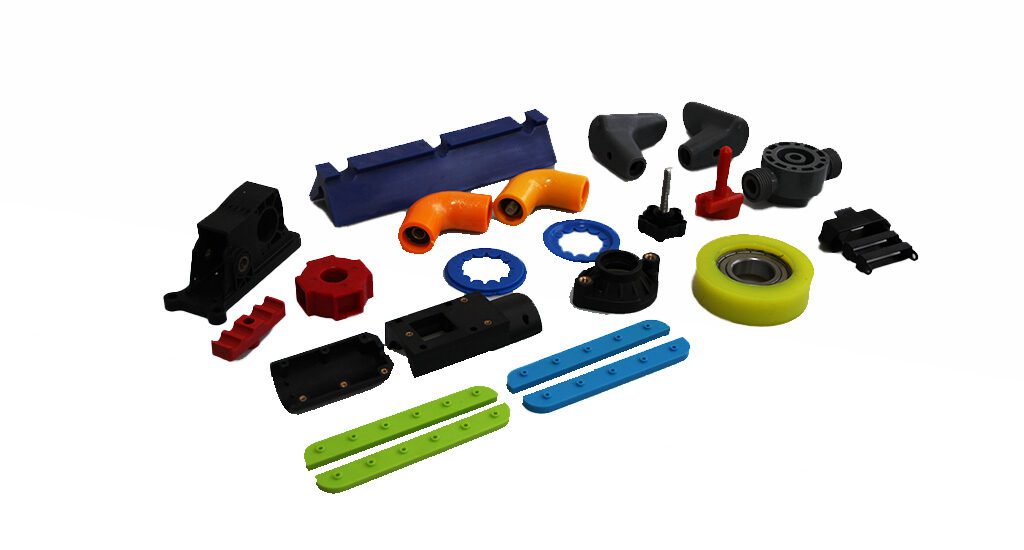
ABS injection moulding is a widely used manufacturing process that combines affordability with high performance. This technique allows manufacturers to produce strong, durable, and aesthetically pleasing plastic parts efficiently. Given its excellent impact resistance, ease of moulding, and cost-effectiveness, ABS injection moulding has become a preferred choice across multiple industries, including automotive, electronics, and consumer goods.
As industries continue to seek high-quality manufacturing solutions, ABS injection moulding stands out for its ability to create complex and precise components with minimal material waste. This article explores the benefits, applications, and challenges of ABS injection moulding, providing a comprehensive guide for businesses looking to leverage this efficient production method.
What is ABS Injection Moulding?
ABS injection moulding is a manufacturing process that involves injecting molten Acrylonitrile Butadiene Styrene (ABS) plastic into a mould cavity under high pressure. Once cooled and solidified, the material takes the shape of the mould, producing a precise and durable component.
ABS is a thermoplastic polymer known for its excellent mechanical properties, including high impact resistance, toughness, and good heat resistance. These characteristics make it a preferred choice for producing high-quality plastic parts used in various industries. Unlike other plastics, ABS combines strength with flexibility, allowing manufacturers to create intricate designs with fine details.
The Advantages of ABS Injection Moulding
ABS injection moulding offers several advantages that make it an attractive manufacturing method.
- High Durability and Strength – ABS provides excellent impact resistance, ensuring that products maintain their integrity under mechanical stress.
- Superior Aesthetic and Surface Finish – ABS can be easily coloured and textured, making it ideal for applications where visual appeal is important.
- Excellent Machinability – ABS is easy to mould and can be processed with high precision, reducing defects and improving efficiency.
- Good Heat and Chemical Resistance – ABS withstands moderate temperatures and is resistant to many chemicals, making it suitable for demanding environments.
- Cost-Effectiveness – ABS injection moulding minimizes material waste, supports mass production, and reduces manufacturing costs.
Key Applications of ABS Injection Moulding
ABS injection moulding is used across various industries due to its versatility and performance.
- Automotive Industry – ABS is used for interior and exterior vehicle components, including dashboards, bumpers, and trims.
- Electronics and Electrical Devices – Many consumer electronics, such as laptop casings, remote controls, and connectors, are made using ABS injection moulding.
- Medical Equipment – ABS is used in medical devices, such as housings for diagnostic tools, due to its durability and ease of sterilization.
- Consumer Goods – Products like toys, kitchen appliances, and protective cases benefit from ABS’s strength and aesthetic properties.
The ABS Injection Moulding Process
The ABS injection moulding process follows several key steps to ensure high-quality production.
- Material Preparation – ABS pellets are dried to remove moisture, preventing defects in the final product.
- Injection Moulding Setup – The ABS is melted inside the injection moulding machine at high temperatures.
- Mould Filling – The molten ABS is injected into a mould cavity under high pressure, ensuring the material fills every detail of the mould.
- Cooling and Solidification – The plastic cools down and hardens within the mould, taking its final shape.
- Ejection and Finishing – The finished part is ejected from the mould and undergoes additional processes like trimming, painting, or assembling if necessary.
Design Considerations for ABS Injection Moulding
Proper design is crucial for successful ABS injection moulding.
- Wall Thickness – Maintaining uniform wall thickness prevents warping and sink marks.
- Draft Angles – Slightly angled surfaces help in easy removal of the part from the mould.
- Surface Finishes – ABS allows for smooth, textured, or glossy finishes, depending on the application.
- Ribs and Reinforcements – Adding ribs improves structural integrity without increasing weight.
Cost-Effectiveness of ABS Injection Moulding
ABS injection moulding is a cost-effective solution due to several factors.
- Mass Production Efficiency – The process enables high-speed production with consistent quality.
- Low Material Waste – ABS injection moulding reduces scrap, as excess plastic can often be recycled.
- Reduced Post-Processing – The ability to create finished products with minimal additional work lowers labour costs.
- Affordable Raw Materials – ABS is a widely available thermoplastic with a balanced cost-to-performance ratio.
Challenges and Solutions in ABS Injection Moulding
Like any manufacturing process, ABS injection moulding presents some challenges, but they can be managed effectively.
- Warping and Shrinkage – Optimizing mould temperature and ensuring uniform wall thickness can reduce these defects.
- Sink Marks – Proper cooling and material flow control prevent surface depressions.
- Short Shots – Increasing injection pressure ensures the mould cavity is fully filled.
- Flashing – Adjusting mould clamping force and injection speed prevents excess plastic from leaking out of the mould cavity.
The Future of ABS Injection Moulding
ABS injection moulding continues to evolve with advancements in technology and materials.
- Automation and Robotics – The integration of smart machinery increases production efficiency and consistency.
- Sustainable Manufacturing – The development of recyclable ABS and biodegradable alternatives enhances environmental sustainability.
- 3D Printing and Hybrid Techniques – Combining injection moulding with additive manufacturing allows for rapid prototyping and customization.
- Advanced Surface Treatments – New finishing techniques improve the durability and aesthetic appeal of ABS products.
Conclusion
ABS injection moulding remains a key manufacturing process due to its affordability, durability, and versatility. Whether in the automotive, electronics, or consumer goods industries, this method offers high-quality production with minimal waste. As technology advances, ABS injection moulding will continue to provide innovative solutions for businesses seeking reliable and cost-effective manufacturing.