- March 18, 2025
- Posted by: feinuojixie
- Category: Injection Molding News
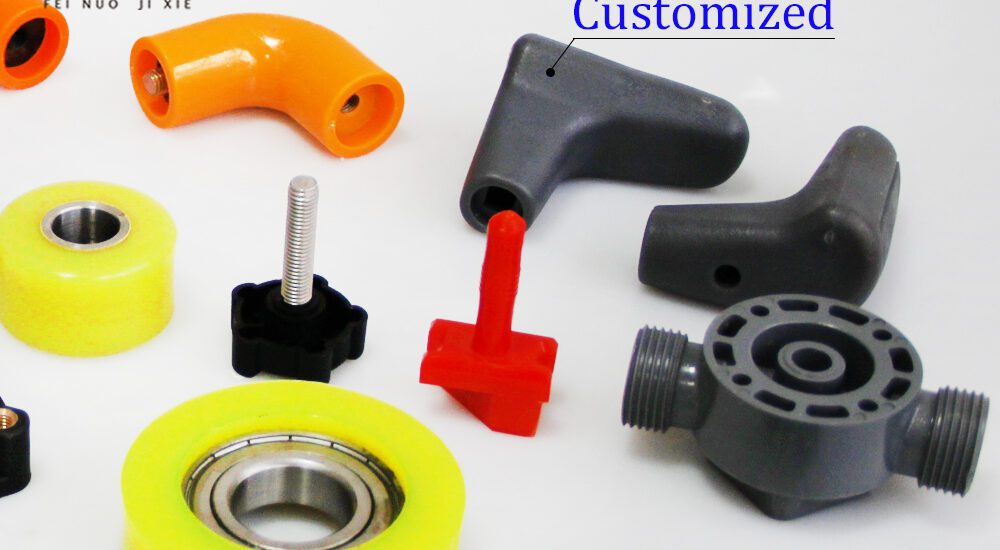
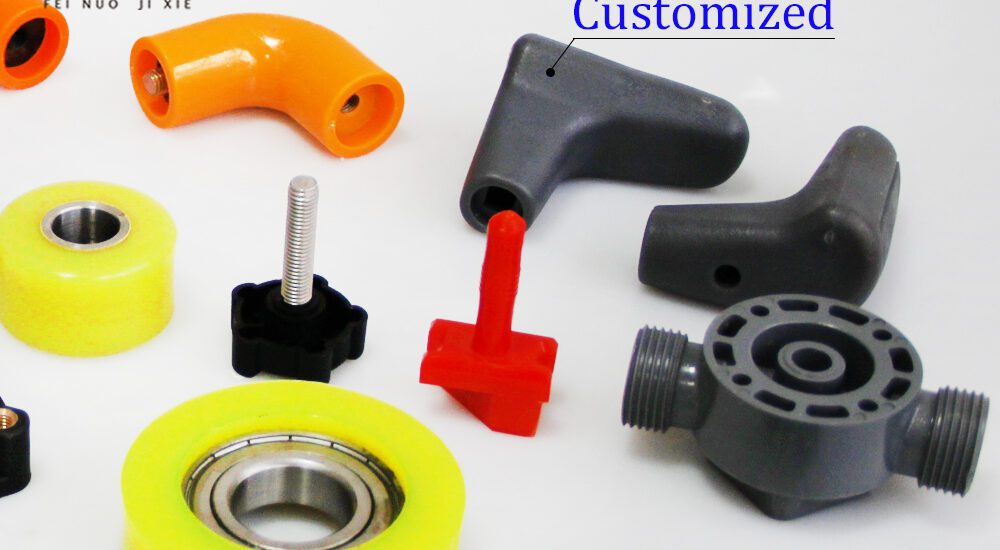
In the world of manufacturing, selecting the right moulding method can significantly impact product quality, production efficiency, and overall costs. Among the various moulding techniques available, ABS injection moulding has emerged as a preferred choice for industries requiring precision, durability, and scalability.
ABS, or Acrylonitrile Butadiene Styrene, is a versatile thermoplastic known for its excellent impact resistance, strength, and ease of processing. When combined with the precision of injection moulding, it creates high-quality components used in a wide range of industries, including automotive, electronics, and consumer goods.
While ABS injection moulding offers numerous benefits, it is essential to compare it with other moulding methods such as blow moulding, compression moulding, and rotational moulding. Each method has its own advantages and applications, but ABS injection moulding consistently proves to be the smart choice for manufacturers looking for efficiency, consistency, and cost-effectiveness.
This article will explore what makes ABS injection moulding unique, compare it with other common moulding methods, and highlight the key advantages that set it apart. By the end, you will have a clear understanding of why ABS injection moulding is an excellent choice for a wide range of manufacturing needs.
Understanding ABS Injection Moulding
ABS injection moulding is a widely used manufacturing process that involves injecting molten ABS plastic into a mould cavity under high pressure. Once the material cools and solidifies, it takes the shape of the mould, producing a precise and durable component. This technique is ideal for mass production, offering high efficiency and excellent part consistency.
ABS plastic itself is a popular thermoplastic due to its unique combination of strength, toughness, and ease of processing. It is resistant to impact, heat, and chemicals, making it a preferred material in industries such as automotive, electronics, consumer goods, and medical devices. The flexibility of ABS injection moulding allows manufacturers to create intricate designs with minimal material waste, ensuring cost-effective production without compromising quality.
Comparison with Other Moulding Methods
ABS Injection Moulding vs. Blow Moulding
Blow moulding is a manufacturing process used primarily for producing hollow plastic parts, such as bottles and containers. In this method, heated plastic is expanded using air pressure to take the shape of a mould.
While blow moulding is effective for lightweight and thin-walled products, it lacks the precision and strength required for complex parts. In contrast, ABS injection moulding allows for highly detailed and durable components, making it the superior choice for applications that demand structural integrity and intricate designs.
ABS Injection Moulding vs. Compression Moulding
Compression moulding involves placing a preheated plastic material into a mould, which is then pressed under high pressure until the material conforms to the desired shape. This method is often used for large and simple parts, such as automotive panels and electrical enclosures.
While compression moulding is beneficial for low-volume production and thick-walled parts, it does not offer the same level of precision and speed as ABS injection moulding. The injection process ensures accurate reproduction of fine details, making it ideal for industries that require tight tolerances and consistent quality.
ABS Injection Moulding vs. Rotational Moulding
Rotational moulding, or roto-moulding, involves slowly rotating a mould filled with powdered plastic inside an oven, allowing the material to coat the interior surface evenly. This technique is commonly used for producing large, hollow objects such as tanks and playground equipment.
Despite its advantages in creating seamless, hollow parts, rotational moulding is slower and less precise than ABS injection moulding. It also has limitations in producing parts with intricate geometries. For manufacturers requiring efficiency, repeatability, and design flexibility, ABS injection moulding remains the smarter option.
Key Advantages of ABS Injection Moulding
Superior Strength and Durability
ABS plastic is known for its toughness and impact resistance, making it ideal for products that need to withstand wear and tear. When combined with the injection moulding process, ABS components gain even greater strength due to the controlled cooling and material distribution. This results in long-lasting parts that maintain their structural integrity under various conditions.
High Precision and Consistency
One of the biggest advantages of ABS injection moulding is its ability to produce parts with high precision and uniformity. The process ensures that every component meets exact specifications, making it essential for industries such as automotive and electronics, where precision is critical. The ability to replicate detailed designs with minimal variation makes ABS injection moulding a preferred choice for high-quality manufacturing.
Cost-Effectiveness in Large-Scale Production
ABS injection moulding is highly efficient for mass production, reducing waste and optimizing material usage. Once a mould is created, thousands or even millions of identical parts can be produced at a low cost per unit. This makes it a cost-effective solution for businesses looking to manufacture products in large quantities without sacrificing quality.
Versatility in Design and Customization
Another major advantage of ABS injection moulding is its ability to accommodate complex shapes, textures, and finishes. Manufacturers can create components with smooth or textured surfaces, integrate different colors, and even add functional features such as clips or hinges directly into the design. This level of customization provides endless possibilities for product development.
Choosing the Right Moulding Method for Your Needs
When selecting a moulding method, it is important to consider factors such as production volume, design complexity, budget, and material properties. ABS injection moulding stands out as the best choice for manufacturers looking for:
- High precision and consistency
- Durable and impact-resistant products
- Cost-effective mass production
- Customizable and complex designs
While other moulding methods have their specific applications, ABS injection moulding offers the perfect balance of quality, efficiency, and affordability for a wide range of industries.
Conclusion
ABS injection moulding has proven to be a smart choice for manufacturers seeking high-quality, durable, and cost-effective plastic components. Compared to other moulding methods, it provides superior precision, strength, and scalability, making it an excellent option for industries that demand consistency and efficiency.
With its ability to produce intricate and long-lasting parts, ABS injection moulding continues to lead the way in modern manufacturing. Whether you are developing automotive components, consumer electronics, or industrial equipment, choosing ABS injection moulding ensures that your products meet the highest standards of quality and performance.