- April 10, 2025
- Posted by: feinuojixie
- Category: Injection Molding News
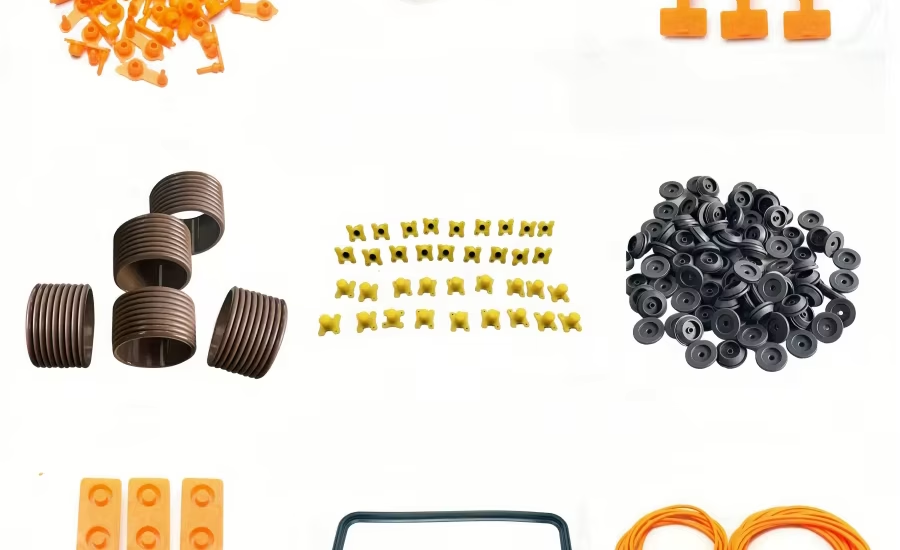
In the fast-paced world of manufacturing, precision is everything. Whether you’re creating components for the automotive, medical, consumer electronics, or aerospace industry, one element remains consistently critical—using the right plastic injection molding parts. These parts are more than just molded plastic; they are the foundation of your product’s quality, reliability, and cost-effectiveness. When the wrong part is used—even in a small assembly—it can lead to expensive production errors, functional failures, or compromised safety.
With global competition and growing customer demands, ensuring you’re working with the correct plastic injection molding part is no longer optional—it’s a strategic necessity. This guide will help you identify whether your current parts are meeting performance standards and show you how to make smart, informed decisions moving forward.
Understanding the Role of Plastic Injection Molding Parts in Product Development
Plastic injection molding parts play a vital role at every stage of product development. From initial prototyping to final mass production, these components directly influence the structure, functionality, and even the look and feel of your end product. A poorly made part can lead to design limitations or assembly challenges, while a well-crafted one allows for innovation and scalability. When chosen correctly, the right part contributes to a seamless product lifecycle—from design and testing to production and market launch.
Signs You May Be Using the Wrong Plastic Injection Molding Parts
If your production line is plagued by frequent defects or unexpected part failures, chances are you’re using the wrong plastic injection molding part. Common red flags include dimensional inconsistencies, warping, brittle finishes, or difficulties during assembly. You may also notice higher-than-average scrap rates, excessive tool wear, or even customer complaints related to product quality. These symptoms are often caused by inappropriate material selection, poor mold design, or substandard manufacturing processes.
Material Selection: A Key Factor in the Performance of Plastic Injection Molding Parts
The type of plastic you choose determines everything from strength and flexibility to chemical resistance and appearance. Not all plastics are created equal. For example, ABS is ideal for toughness and impact resistance, while polycarbonate offers clarity and heat tolerance. The wrong material can make an otherwise perfect design completely ineffective. Collaborating with engineers or suppliers who understand your industry standards can help ensure that the plastic injection molding part is made from a material that matches your exact requirements.
Design Optimization for the Right Plastic Injection Molding Parts
Design flaws can sabotage even the highest quality material. When creating or selecting plastic injection molding parts, factors like wall thickness, flow paths, and cooling times must be carefully considered. Uniform wall thickness helps prevent shrinkage or distortion, while appropriate draft angles facilitate easier part ejection from the mold. Design optimization ensures not only functionality and longevity but also improves cycle times and reduces waste.
Working with the Right Supplier for Quality Plastic Injection Molding Parts
Even the best designs and materials will fail without the right supplier. A trusted plastic injection molding partner should offer precision tooling, quality assurance processes, and in-depth technical support. Look for certifications such as ISO 9001, industry-specific experience, and a willingness to collaborate during development. The right supplier can help you troubleshoot problems, refine part designs, and deliver consistent results across large volumes.
Testing and Quality Control Measures for Plastic Injection Molding Parts
How do you know your plastic injection molding part meets performance expectations? Through rigorous testing and quality checks. Common procedures include dimensional verification, tensile strength tests, and thermal analysis. Advanced techniques like CT scanning or ultrasonic testing can also detect internal defects. Implementing these checks early and regularly helps catch issues before they escalate and ensures long-term product reliability.
Cost Implications of Using the Wrong Plastic Injection Molding Parts
Cutting corners in part selection might save money initially—but it often leads to higher costs in the long run. Poorly made plastic injection molding parts can result in frequent maintenance, downtime, rework, or even product recalls. These hidden costs not only affect your budget but can also damage your reputation. On the other hand, investing in high-quality parts minimizes risks and boosts overall profitability through improved efficiency and customer satisfaction.
How to Evaluate and Switch to the Right Plastic Injection Molding Parts
Not sure if you’re using the right plastic injection molding part? Start by evaluating your current components based on performance, failure rates, and material specifications. Seek feedback from your production team, analyze defect logs, and compare your parts to industry benchmarks. If gaps are found, begin testing alternatives in small batches. Work closely with suppliers to test new materials and designs before making a full transition.
Future Trends in Plastic Injection Molding Parts Selection and Innovation
The future of plastic injection molding is driven by innovation. Smart materials with self-healing properties, biodegradable plastics, and lightweight composites are reshaping how parts are made. In addition, AI and machine learning are being used to predict part performance and detect defects earlier in the production process. Staying updated with these trends helps ensure you’re not just using the right part today—but are also prepared for tomorrow’s demands.
Conclusion: Make the Right Choice for Long-Term Success
Choosing the right plastic injection molding part is more than just a technical decision—it’s a strategic move that affects every aspect of your operation. From material selection and design to quality control and supplier collaboration, each factor plays a role in product performance and company success. By paying attention to these details, you can reduce waste, improve quality, and stay competitive in a constantly evolving market. Don’t leave it to chance—start evaluating your plastic injection molding parts today.