- April 27, 2025
- Posted by: feinuojixie
- Category: Injection Molding News
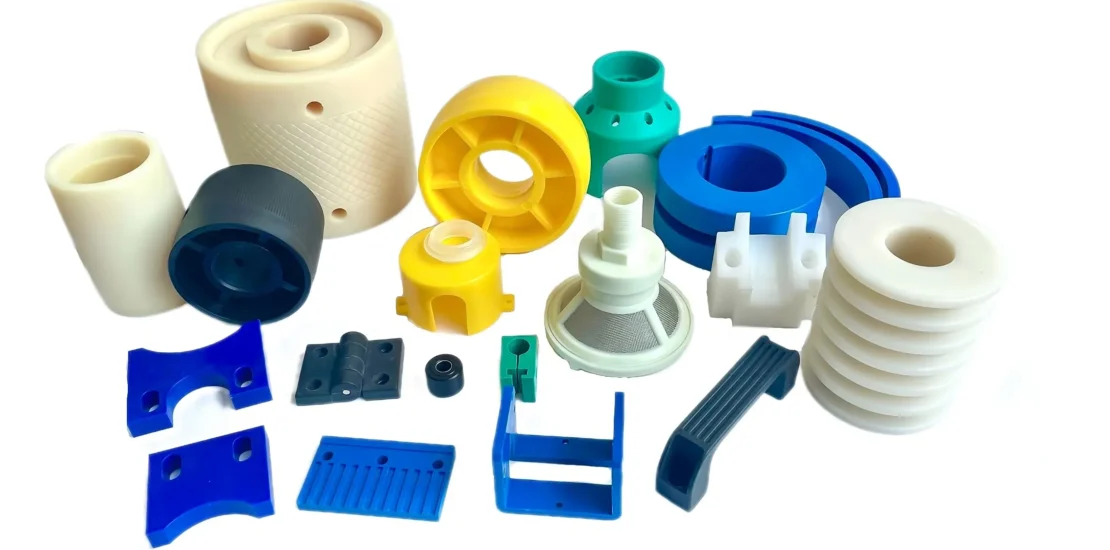
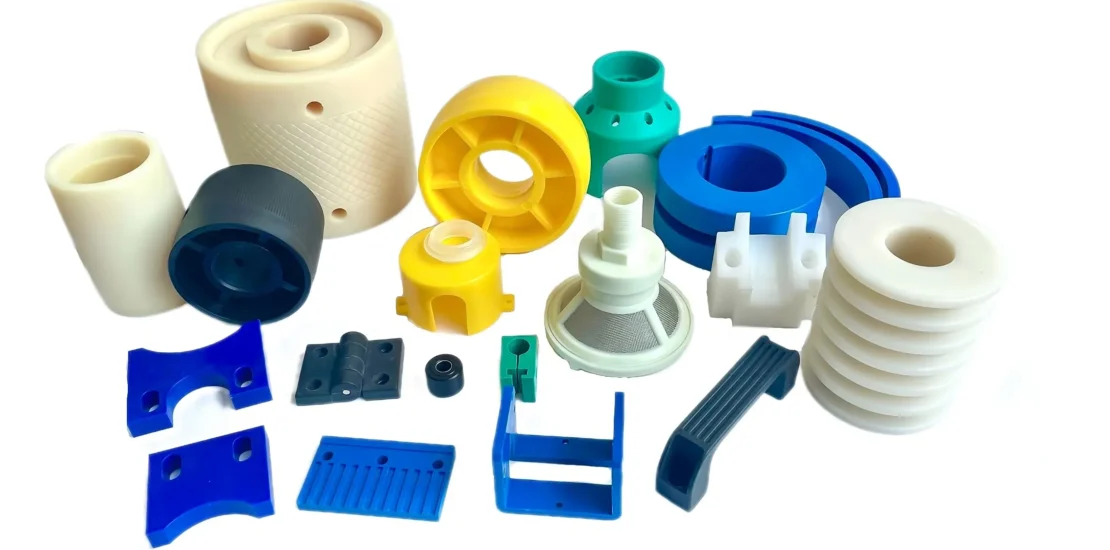
Injection parts play a critical role in countless industries, from automotive to consumer electronics. Yet, many businesses focus solely on the upfront cost when choosing these essential components. This narrow view often leads to unforeseen expenses that eat into profits and strain operations. Understanding the full impact of your injection part choices can empower you to make smarter decisions, reduce waste, and boost your bottom line. In this blog, we will explore the hidden costs of injection parts, common sourcing pitfalls, and actionable strategies to help your business save smarter, not just cheaper.
Understanding the True Cost of Injection Part
When evaluating injection part for your project, it is easy to be swayed by a low unit price. However, the true cost extends far beyond the purchase order. Maintenance expenses, unexpected downtime, defective product rates, and even energy consumption during production can all add up quickly. An injection part that seems economical at first glance may require frequent adjustments, additional labor, or early replacement, leading to a significantly higher total cost of ownership. By considering the complete lifecycle of injection part, companies can make more informed, cost-effective decisions.
Common Mistakes When Sourcing Injection Part
Many businesses fall into common traps when sourcing injection part. Choosing suppliers based solely on the lowest price often leads to quality issues that surface later in the production cycle. Ignoring material certifications can result in parts that fail regulatory requirements or wear out faster than expected. Another frequent mistake is underestimating lead times, leading to costly production halts. These oversights not only increase costs but also risk damaging a company’s reputation for reliability and performance.
Quality vs. Price: How Cheap Injection Part Could Hurt Your Bottom Line
While it is tempting to cut costs by opting for cheaper injection part, the long-term consequences can be devastating. Low-quality parts tend to fail prematurely, resulting in increased warranty claims, frequent replacements, and disrupted production schedules. Customer satisfaction can plummet if end products suffer from poor reliability. In some cases, saving a few cents per part can lead to losses amounting to thousands of dollars in rework, recalls, and brand damage. Investing in quality from the start is not an expense—it is protection for your business.
Hidden Costs in Injection Part Production You Should Know
The production of injection part often carries hidden costs that are not immediately apparent. For instance, poorly designed or substandard molds can wear out faster, requiring expensive repairs or replacements. A higher scrap rate from inconsistent part quality translates into wasted materials and increased labor costs. Secondary processing like trimming or reworking flawed parts eats into production efficiency. Moreover, imprecise parts can cause machine downtime due to misalignments or jams, further inflating operational expenses. Awareness of these hidden factors is key to controlling total costs.
How to Evaluate Injection Part Suppliers for True Value
Selecting the right supplier for your injection part involves looking beyond the price list. A reliable supplier will have robust quality control measures, hold certifications like ISO 9001, and provide transparent sourcing of raw materials. In-depth technical support and the ability to assist in design for manufacturability are strong indicators of a supplier’s commitment to value rather than just volume. Requesting sample parts for testing, performing facility audits, and checking client references are essential steps to ensure you are partnering with a trustworthy supplier who delivers long-term savings.
Strategies to Reduce the Overall Cost of Injection Part
Reducing the overall cost of injection part starts with smarter design and smarter sourcing. Investing in high-quality molds can dramatically extend mold life and improve part consistency. Simplifying designs for manufacturability minimizes complexity and lowers production costs. Consolidating suppliers to achieve better volume pricing and conducting regular audits to ensure consistent quality can also drive significant savings. Additionally, involving suppliers early in the design process often reveals opportunities to optimize material usage, improve part performance, and reduce secondary processing.
Real-World Case Studies: Saving Big by Managing Injection Part Costs
Consider a mid-sized electronics company that switched to a higher-quality injection part supplier after suffering from frequent product returns. Despite paying 15% more per part, their overall production costs fell by 22% due to reduced defects and lower warranty claims. Another example is an automotive firm that reengineered their part design with supplier input, cutting material costs by 10% and increasing mold life by 30%. These real-world stories highlight that the right approach to injection part management can lead to substantial financial gains.
Invest Smarter in Injection Part for Long-Term Profitability
Injection parts are the building blocks of countless products, and overlooking their true cost can quietly erode a company’s profits. By understanding hidden expenses, avoiding common sourcing mistakes, prioritizing quality over cheap pricing, and carefully evaluating suppliers, businesses can protect their margins and reputation. Investing wisely in injection part is not just about saving money—it is about building a stronger, more sustainable future for your business.