- May 8, 2025
- Posted by: feinuojixie
- Category: Injection Molding News
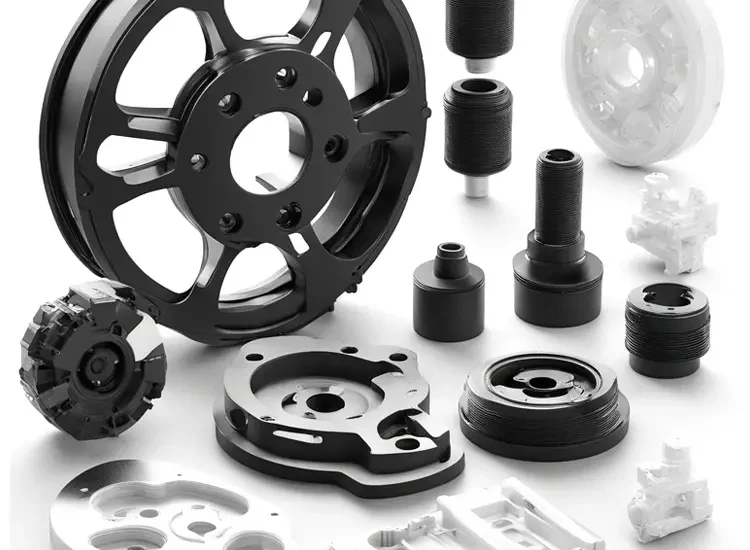
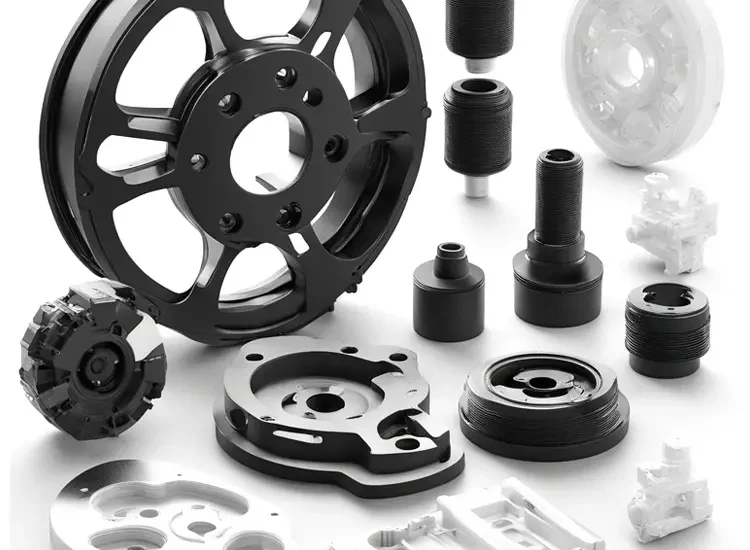
In today’s competitive manufacturing landscape, the smallest mistake in part selection can create significant downstream consequences. From product recalls to increased maintenance costs, the choice of plastic injection part directly impacts the success of your final product. Whether you are developing a consumer electronic device, an automotive component, or industrial housing, your selected part must meet performance, budget, and aesthetic expectations.
Yet many engineers, procurement teams, and entrepreneurs fall into avoidable traps when choosing their parts. Sometimes it’s due to a lack of experience, other times it’s a simple oversight. This article explores seven of the most common missteps that businesses make and provides insight into how to avoid them—so you can select the best plastic injection part with confidence, every time.
Ignoring the End-Use Requirements of the Plastic Injection Part
One of the most common and costly mistakes is failing to consider how the part will be used once it’s installed in a real-world environment. Will it need to endure high temperatures, chemical exposure, UV light, or continuous mechanical stress? A plastic injection part designed for indoor consumer use will likely fail in an outdoor automotive setting.
Ignoring these variables leads to premature failure, unnecessary redesigns, and wasted resources. Always start by clearly defining the performance requirements of the end-use environment and communicate those expectations to your mold design and material selection teams early in the process.
Choosing the Wrong Material for the Plastic Injection Part
Material selection is critical—and often misunderstood. Not all plastics are created equal, and choosing a generic resin without evaluating the specific demands of your application can cause major performance issues. For example, a low-cost ABS might save you money upfront, but if your part requires chemical resistance or structural rigidity, a more specialized engineering resin like PEEK or nylon might be essential.
Each material brings unique properties such as impact resistance, transparency, flame retardancy, or thermal stability. Work closely with material experts or suppliers to match your plastic injection part requirements with the right resin for the job.
Overlooking Design for Manufacturability (DFM)
Even the best ideas can fail if they’re difficult—or impossible—to mold. A lack of DFM considerations can result in sink marks, short shots, or warpage that render your part unusable. Common pitfalls include wall thickness inconsistencies, undercuts, and poor draft angles that complicate ejection from the mold.
Engaging with mold engineers early to apply DFM principles ensures your plastic injection part is designed not just for performance, but also for efficient production. This reduces tooling revisions, shortens lead times, and helps you avoid unnecessary costs.
Failing to Consider Tolerance and Fit Requirements
Many plastic injection parts are components within larger assemblies. When tolerance stack-up is ignored, parts may not fit correctly—causing binding, rattling, or structural issues. Plastic parts also behave differently than metal, with more sensitivity to shrinkage and environmental conditions.
To prevent costly assembly errors, define precise tolerance ranges and account for factors like material shrinkage, thermal expansion, and interaction with other components. Use simulations or prototype testing to verify the fit and function before moving to mass production.
Neglecting Mold Quality and Tooling Expertise
The performance of your plastic injection part is only as good as the mold that shapes it. A low-quality or poorly maintained mold can introduce surface imperfections, flash, dimensional inaccuracies, or longer cycle times that compromise production efficiency.
Tooling is not a place to cut corners. Partner with mold makers who specialize in your industry and have a proven track record of delivering high-quality, durable tools. A well-built mold pays for itself over time by minimizing downtime, scrap, and rework.
Underestimating Production Volume and Scalability
Choosing tooling or manufacturing strategies without considering future production volumes can lock you into a path that doesn’t scale. For example, opting for aluminum tooling may be suitable for low volumes but can wear out quickly under high-volume demands.
Clarify your projected production needs early. Will you require 1,000 units or 100,000 over the next year? These numbers will influence mold material, number of cavities, automation level, and unit cost. Planning for scalability helps you avoid production bottlenecks and expensive mold upgrades later.
Disregarding Supplier Experience with Plastic Injection Part
Not all suppliers are equipped to handle your specific requirements. A supplier might have years of experience with general plastic molding but may lack the expertise needed for your part’s complexity, size, or tolerance specifications.
Take time to vet suppliers based on their portfolio, certifications, quality systems, and customer reviews. Ask about their experience with similar plastic injection part projects and whether they offer support in design, material selection, or mold optimization. Choosing a knowledgeable partner reduces risk and boosts your project’s success rate.
Choosing the Right Plastic Injection Part with Confidence
Avoiding these seven mistakes can make the difference between a successful product launch and a costly manufacturing nightmare. Choosing the right plastic injection part is not just about picking a material or a vendor—it’s about making informed decisions at every step, from design to delivery.
By focusing on end-use performance, material science, smart design, precision, mold quality, scalability, and supplier reliability, you can set yourself up for long-term success. Remember, a proactive approach today saves time, money, and stress tomorrow. Choose wisely, and let every plastic injection part work as hard as you do.