- April 24, 2025
- Posted by: feinuojixie
- Category: Injection Molding News
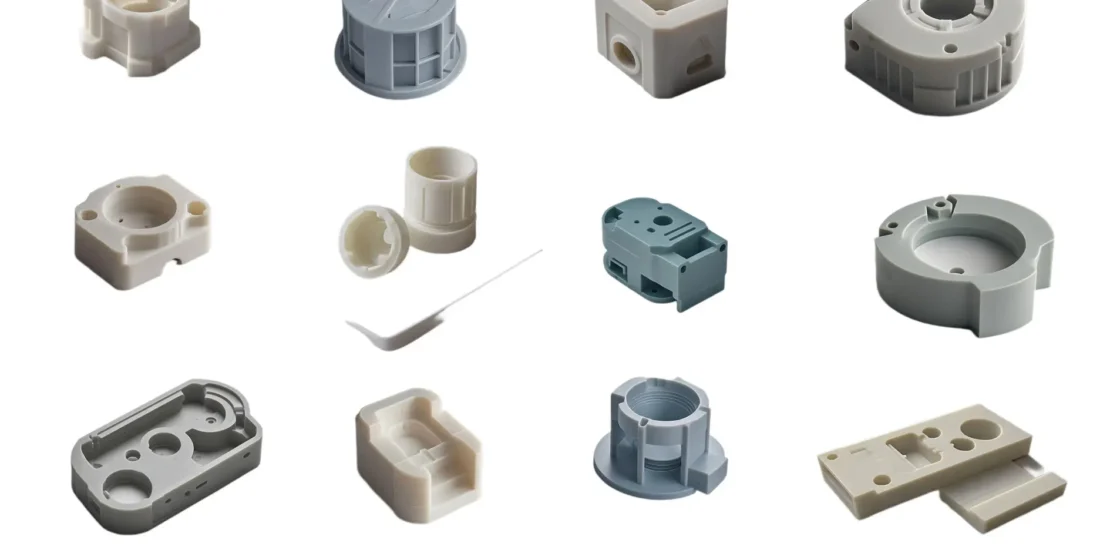
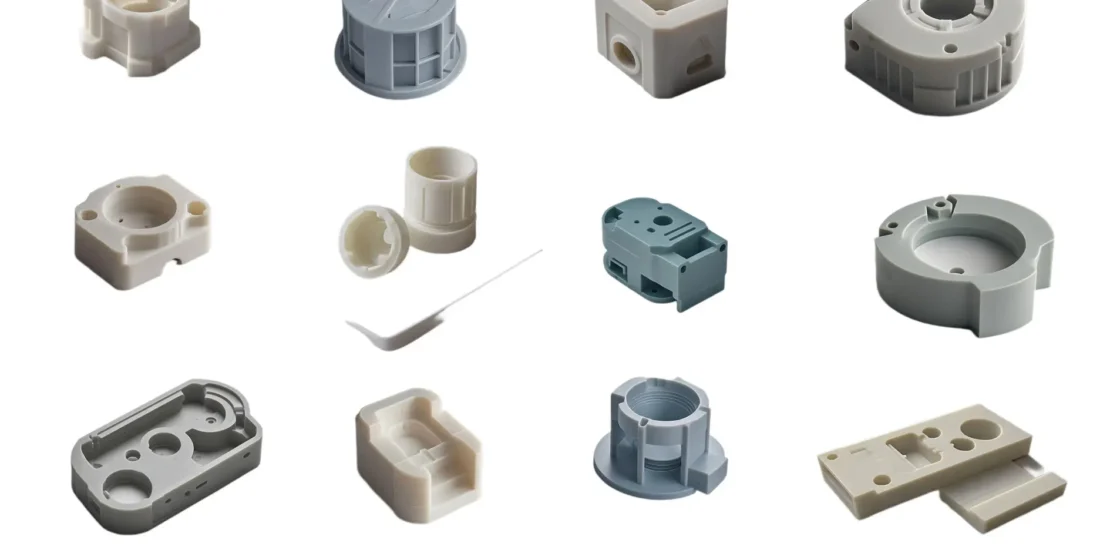
Injection moulding is one of the most widely used manufacturing processes for producing plastic components, thanks to its speed, scalability, and cost efficiency. However, despite its advantages, the process is highly sensitive to error. Small mistakes in design, material selection, tooling, or processing can lead to significant issues—from part deformation and structural failure to high scrap rates and production delays.
When it comes to injection moulding plastic parts, precision isn’t just a bonus—it’s a requirement. Engineers and manufacturers must collaborate closely across every stage of the production cycle to ensure that the final part meets specifications without incurring unnecessary costs or defects. In this article, we’ll break down the most common mistakes that compromise injection moulding plastic parts and how to avoid them. Whether you’re a design engineer, a toolmaker, or a quality specialist, these insights can help you streamline your processes and enhance product quality.
Design Oversights That Undermine Injection Moulding Plastic Parts
Ignoring Draft Angles
A common mistake in designing injection moulding plastic parts is neglecting draft angles. These angles, typically between 1° and 3°, are critical for ensuring smooth ejection from the mould. Without them, parts may stick to the mould surface, leading to scratches, deformation, or even damage to the tool. Including the proper draft reduces ejection force, extends mould life, and improves part aesthetics.
Overcomplicating the Geometry
Complex part geometry may seem innovative but can be a liability in injection moulding. Intricate shapes often require advanced tooling and may increase the risk of voids, warping, or inconsistent fill. Simplifying design where possible makes the moulding process more efficient, reduces cycle time, and improves repeatability without compromising function.
Inadequate Wall Thickness
Uniform wall thickness is key to successful injection moulding plastic parts. Variations in thickness can cause uneven cooling, leading to internal stresses, sink marks, and warping. Designers should aim for consistent wall dimensions throughout the part and avoid abrupt transitions, which can disrupt material flow and cooling.
Material Selection Errors That Lead to Failure
Choosing the Wrong Plastic Resin
Each plastic resin has its own mechanical and thermal properties. Choosing a resin that doesn’t align with the part’s performance requirements can result in cracking, brittleness, or degradation over time. For example, using a low-temperature resin for a high-heat application can compromise safety and durability. Proper material selection should be based on environmental exposure, load conditions, and aesthetic demands.
Neglecting Material Shrinkage Factors
Shrinkage is an inherent aspect of injection moulding. Failing to consider the shrinkage rate of the selected resin can lead to dimensional inaccuracies in the final part. Designers must work closely with material datasheets and tooling engineers to compensate for this during mould creation, ensuring that the parts meet the intended tolerances.
Tooling and Mould Issues to Avoid at All Costs
Poorly Designed Moulds
Even a perfect part design can fail if the mould isn’t well-executed. Common mould design errors include improperly located gates, insufficient venting, or poorly placed ejector pins. These flaws can lead to short shots, burn marks, or cosmetic defects. A well-designed mould facilitates smooth material flow, uniform cooling, and clean part ejection.
Lack of Proper Mould Maintenance
Injection moulding plastic parts rely heavily on the condition of the mould. Over time, moulds accumulate wear, residue, and corrosion. Without regular maintenance—cleaning, lubrication, and inspection—defects can multiply, and downtime increases. Implementing a preventive maintenance schedule is essential to maintaining part quality and reducing unplanned stoppages.
Process Control Mistakes That Compromise Quality
Inconsistent Processing Parameters
Maintaining consistent temperature, pressure, and injection speed is vital. Deviations in these parameters can cause bubbles, flash, or incomplete filling. Automated control systems and data monitoring help maintain process stability. Operators should also be trained to recognize and respond to signs of instability before it impacts production.
Ignoring Cooling Time Requirements
Cooling represents a significant portion of the moulding cycle, and rushing it can be detrimental. Inadequate cooling leads to internal stresses, dimensional errors, and poor surface finish. It’s important to balance cooling time with cycle efficiency—fast, but not rushed. Cooling system design, including channels and materials, should be optimized during the tool design stage.
Quality Assurance Pitfalls in Injection Moulding Plastic Parts
Skipping Early Prototyping or Testing
Prototype moulds or pilot runs help identify design and process issues before scaling to full production. Skipping this step can result in large batches of defective parts. Early testing also allows for validation of part functionality, aesthetics, and fit, reducing the risk of costly post-production revisions.
Insufficient Post-Moulding Inspection
Post-moulding inspections are the last line of defense against defective parts reaching the customer. Relying solely on automated checks without proper visual inspection or dimensional measurement can allow subtle defects to pass unnoticed. A robust quality control process should combine machine monitoring with human oversight, especially for critical applications.
Mastering the Process to Ensure Success
Injection moulding plastic parts is both an art and a science. Each step—from design and material selection to tooling, processing, and quality control—must be executed with care and precision. Avoiding common mistakes not only prevents costly errors but also enhances efficiency, product quality, and customer satisfaction. Whether you’re new to injection moulding or refining a mature process, staying aware of these pitfalls and continuously optimizing your workflow will lead to better results and long-term success in manufacturing.