- April 25, 2025
- Posted by: feinuojixie
- Category: Injection Molding News
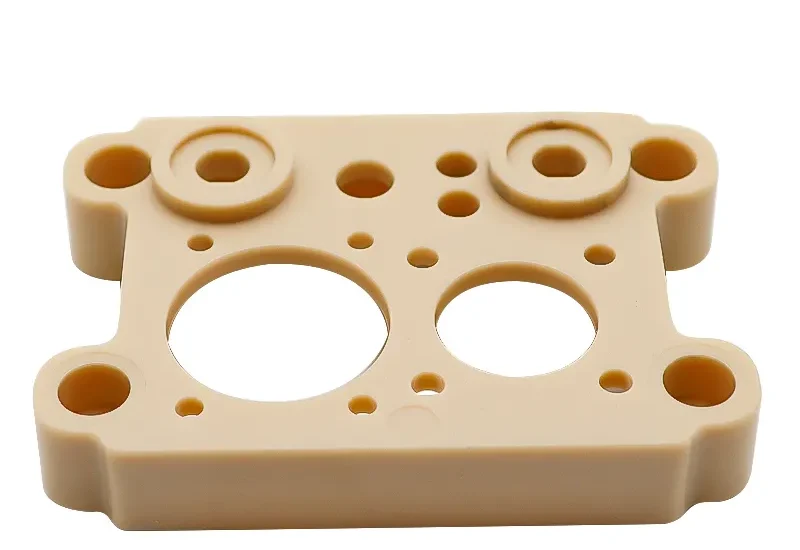
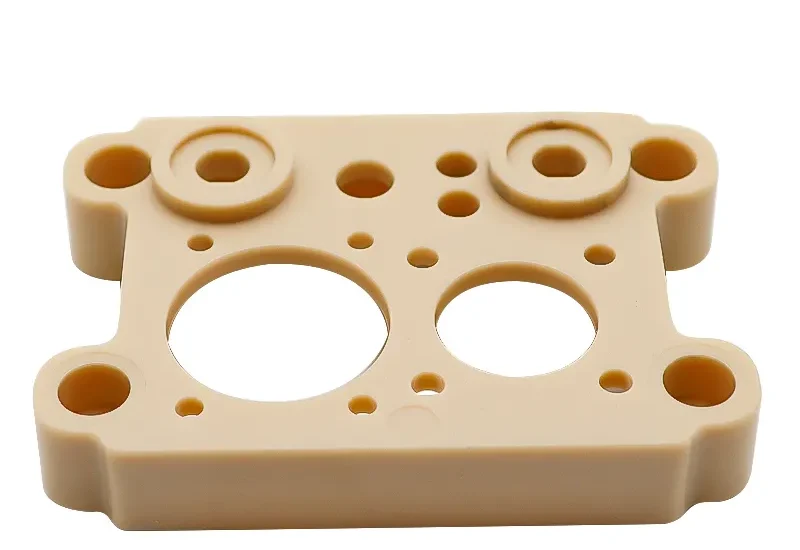
Injection part plays a foundational role in many manufacturing processes, serving as a critical component in producing consistent, high-quality products. Whether used in consumer electronics, automotive systems, or medical devices, the integrity of injection part can significantly influence the overall success of a product. Unfortunately, many decision-makers underestimate the importance of making informed choices during the selection process.
Choosing the right injection part is not just a technical decision—it’s also a strategic one. A poor choice can lead to production delays, increased costs, and even product recalls. To avoid these costly consequences, it’s essential to understand and sidestep the most common mistakes that occur when selecting injection part.
This article will explore the frequent missteps businesses make during injection part selection and offer practical guidance to help ensure your project runs smoothly from prototype to production. Let’s begin by understanding the role injection part plays in modern product development.
Understanding the Role of Injection Part in Product Development
Injection part is more than just a molded component—it is the backbone of precision, performance, and repeatability in modern manufacturing. From structural support to aesthetic detailing, injection part affects both functionality and appearance. Engineers must consider the intended use, stress factors, and environmental conditions when designing and selecting the right injection part. A misstep here can compromise the entire product.
Material selection, mold design, and dimensional accuracy all play a role in determining how effective an injection part will be in its final application. Understanding these fundamentals is key before moving into production or sourcing.
Ignoring Material Compatibility
One of the most frequent mistakes is overlooking how different materials behave under specific conditions. Not all polymers or metals perform the same way under stress, heat, or chemical exposure. Using a material that doesn’t align with product requirements can lead to deformation, brittleness, or failure over time.
For example, a part exposed to high temperatures should not be made with a low-heat-tolerance plastic. Material compatibility should be assessed in terms of mechanical strength, thermal stability, chemical resistance, and regulatory compliance. Always consult material datasheets and conduct testing when in doubt.
Choosing Cost Over Quality
While cost is always a factor in product development, prioritizing it over quality often leads to bigger expenses in the long run. A lower-cost injection part might initially seem appealing, but if it results in high defect rates, frequent replacements, or additional assembly issues, the total cost of ownership can skyrocket.
Instead of focusing solely on price per unit, consider the entire lifecycle cost: durability, performance consistency, and the cost of potential failures. A well-made injection part may cost slightly more upfront, but it will reduce downtime and maintenance costs over time.
Overlooking Tolerance Requirements
Injection molding requires tight tolerances to ensure parts fit and function properly. Ignoring this critical aspect can cause issues like poor fit, stress concentrations, or leaks in assembled products. Tolerances become even more crucial when parts interact with others in a system or when used in safety-critical environments.
Precision matters. Work closely with the design and mold engineering team to define acceptable tolerances, and ensure the supplier has the capability to meet those specifications consistently.
Not Considering Production Volume
Production volume directly influences material choice, tooling investment, and processing strategy. A part that is ideal for low-volume prototyping may not be suitable for mass production. Mistaking one for the other can result in either overspending or underperforming parts.
For high-volume runs, investing in hardened steel tooling may offer better durability, whereas aluminum tooling might suffice for short-run projects. Aligning your injection part strategy with your production volume will save both time and money.
Neglecting Supplier Qualification
Choosing a supplier based solely on price or availability is risky. Inexperienced or unverified suppliers may lack the expertise or equipment to produce high-quality injection part consistently. This can result in inconsistent dimensions, poor surface finishes, or even regulatory non-compliance.
To mitigate this, always vet your suppliers. Look for ISO certifications, request production samples, and review their manufacturing capabilities. A qualified partner should offer design support, quality control, and clear communication throughout the process.
Failing to Account for Post-Processing Requirements
Injection molding is rarely the final step in the production of a part. Trimming, coating, assembly, or surface treatments are often required. Failing to account for these steps during the design and planning phase can lead to delays, extra costs, or even part redesigns.
Consider the full journey of your injection part—from mold to market. Understanding how post-processing will affect tolerances, finishes, or structural integrity is essential for ensuring seamless integration into your product workflow.
Skipping Design for Manufacturability (DFM) Review
DFM is the practice of designing parts that are easy and cost-effective to manufacture. Skipping this review can result in parts that are difficult to mold, prone to defects, or require unnecessary complexity.
A DFM check helps identify areas where part geometry can be simplified, mold flow improved, and manufacturing costs reduced. Collaborate with your injection part supplier early to evaluate the design and prevent issues before they reach the production floor.
How to Make Better Choices When Selecting Injection Part
Choosing the right injection part is a nuanced process that requires attention to detail, strategic thinking, and collaboration with experts. By avoiding common mistakes such as ignoring material compatibility, undervaluing quality, and skipping DFM reviews, you can ensure your parts meet performance expectations and deliver long-term value.
Use this guide as a checklist when evaluating injection part options:
-
Verify material suitability
-
Balance cost with quality
-
Define critical tolerances
-
Align with production volume
-
Qualify your suppliers
-
Plan for post-processing
-
Conduct a DFM review
By applying these principles, you’ll not only avoid costly errors—you’ll also gain a competitive edge in bringing high-performance products to market faster and more reliably.