- March 26, 2025
- Posted by: feinuojixie
- Category: Injection Molding News
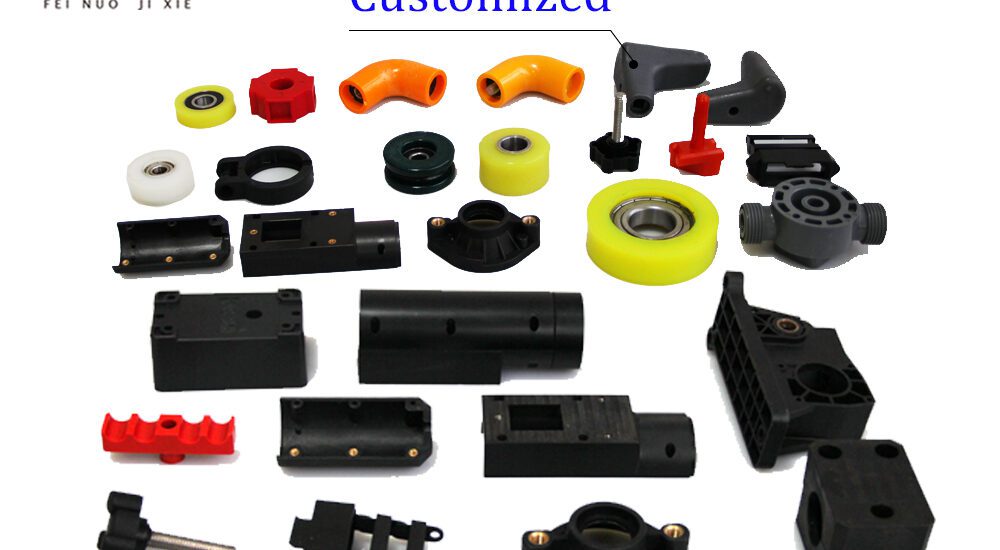
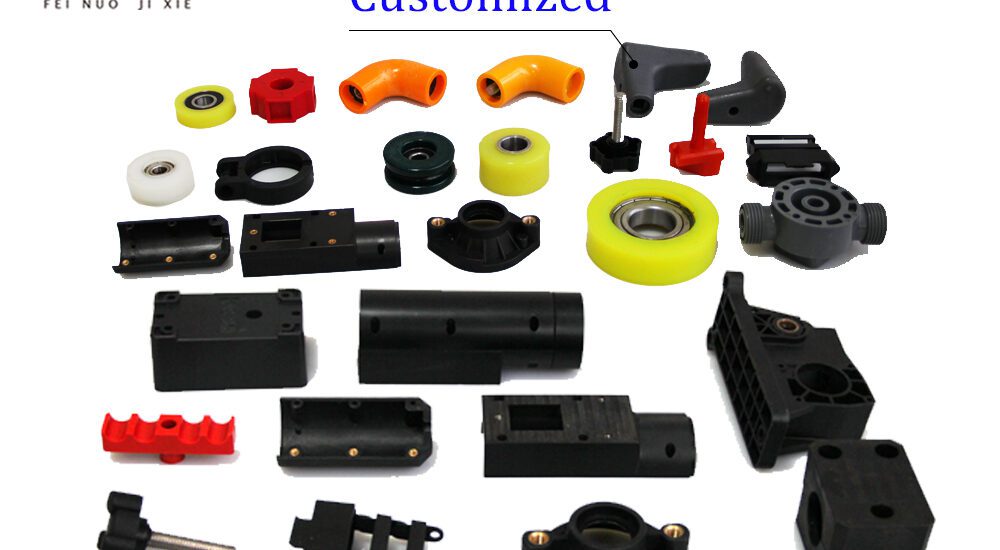
ABS injection moulding plays a critical role in modern manufacturing, offering a balance of durability, flexibility, and cost-effectiveness. From automotive parts to consumer electronics, ABS is one of the most versatile thermoplastics used in injection moulding. However, not all ABS grades are the same, and selecting the right one can significantly impact product quality and performance. This guide will help you understand the various ABS grades available and how to choose the most suitable one for your injection moulding needs.
Understanding ABS in Injection Moulding
ABS, or Acrylonitrile Butadiene Styrene, is a widely used thermoplastic in injection moulding due to its excellent balance of strength, impact resistance, and ease of processing. It combines the properties of three monomers:
-
Acrylonitrile: Provides chemical resistance and thermal stability
-
Butadiene: Enhances impact resistance and toughness
-
Styrene: Contributes to rigidity and a smooth surface finish
This unique composition makes ABS an ideal choice for applications that require durability, aesthetic appeal, and cost-effectiveness. Its versatility allows manufacturers to customize its properties by adjusting the ratio of its components or adding modifiers, leading to a range of ABS grades suitable for different applications.
Different Grades of ABS for Injection Moulding
Choosing the right ABS grade depends on the specific requirements of your project. Here are the most common ABS grades used in injection moulding:
-
High-Impact ABS
Designed for applications requiring superior toughness, high-impact ABS contains a greater proportion of butadiene, improving shock absorption and crack resistance. It is commonly used in automotive parts, sports equipment, and industrial tools where durability is crucial. -
Heat-Resistant ABS
Some ABS grades are modified to withstand higher temperatures without losing structural integrity. Heat-resistant ABS is ideal for applications such as automotive dashboards, electronic housings, and appliances that experience prolonged heat exposure. -
Flame-Retardant ABS
Certain industries, such as electronics and automotive manufacturing, require materials with fire-resistant properties. Flame-retardant ABS contains additives that help it meet fire safety standards, making it suitable for electrical casings, battery enclosures, and safety equipment. -
General-Purpose ABS
This standard ABS grade provides a well-balanced combination of strength, rigidity, and ease of processing. It is commonly used for everyday consumer products, toys, and low-stress structural components. -
Specialty ABS
Some applications demand enhanced properties such as UV resistance, antistatic properties, or chemical resistance. Specialty ABS grades are formulated with additional additives to meet specific industry requirements, such as outdoor equipment or medical devices.
Key Factors to Consider When Selecting an ABS Grade
Selecting the right ABS grade requires evaluating the following factors:
-
Mechanical Strength
Consider the level of impact resistance required. If your product needs to withstand heavy use or potential drops, high-impact ABS is the best choice. -
Thermal Stability
If the product will be exposed to high temperatures, heat-resistant ABS ensures better performance without deformation. -
Chemical Resistance
Some applications, such as automotive components and medical devices, require ABS grades resistant to oils, solvents, or cleaning agents. -
Surface Finish and Aesthetics
For consumer products and high-end electronics, a smooth and glossy finish is important. ABS grades with enhanced surface properties ensure an attractive final product. -
Processing Ease
Some ABS grades require precise processing conditions to avoid defects like warping and shrinkage. Choosing a grade that aligns with your production capabilities can improve efficiency.
Applications of Different ABS Grades in Injection Moulding
ABS is used in a variety of industries due to its adaptability. Here are some common applications:
-
Automotive Industry
Heat-resistant and impact-resistant ABS is used for dashboards, interior panels, and bumpers due to its durability and lightweight properties. -
Electronics
Flame-retardant ABS ensures safety in electrical enclosures, battery housings, and computer casings by minimizing fire hazards. -
Consumer Goods
General-purpose ABS is commonly found in household appliances, furniture parts, and toys because of its affordability and ease of manufacturing. -
Medical Devices
Specialty ABS with biocompatibility and chemical resistance is used for sterilizable components, diagnostic equipment, and protective cases.
Common Challenges in ABS Injection Moulding and How to Overcome Them
While ABS is relatively easy to process, certain challenges can arise during injection moulding:
-
Warping and Shrinkage Issues
Uneven cooling can lead to warping, while shrinkage can cause dimensional inaccuracies. Maintaining uniform cooling rates and proper mould design can help prevent these issues. -
Surface Defects
Marks, bubbles, and weld lines may appear if processing parameters are not optimized. Adjusting injection speed, pressure, and temperature can improve surface quality. -
Adhesion Problems
Some applications require bonding ABS with other materials. Using compatible adhesives or surface treatment techniques can enhance adhesion.
Tips for Optimizing ABS Injection Moulding Performance
To achieve the best results in ABS injection moulding, consider the following tips:
-
Optimize Processing Temperature and Pressure
Maintaining the right balance prevents defects such as burning, warping, or incomplete filling of the mould. -
Proper Drying and Pre-Treatment of ABS Pellets
ABS absorbs moisture, which can cause surface imperfections. Pre-drying the material before moulding ensures a smooth finish. -
Use Additives for Enhanced Properties
UV stabilizers, impact modifiers, and fire retardants can be added to customize the material for specific applications.
Conclusion
Choosing the right ABS grade for injection moulding is essential for achieving the desired balance of durability, aesthetics, and functionality. Each grade offers distinct advantages, making it important to consider factors such as impact resistance, heat stability, and surface quality when making a selection. By understanding the unique properties of different ABS grades and optimizing processing conditions, manufacturers can ensure high-quality, reliable products that meet industry requirements.