- March 20, 2025
- Posted by: feinuojixie
- Category: Injection Molding News
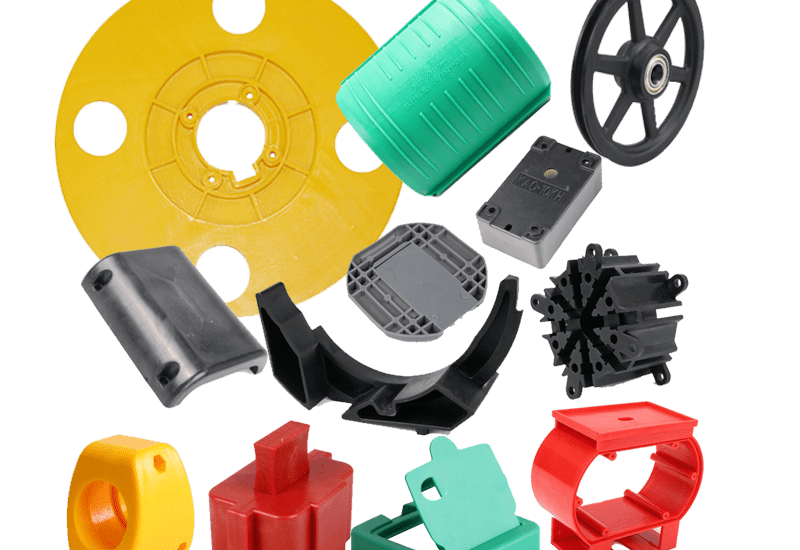
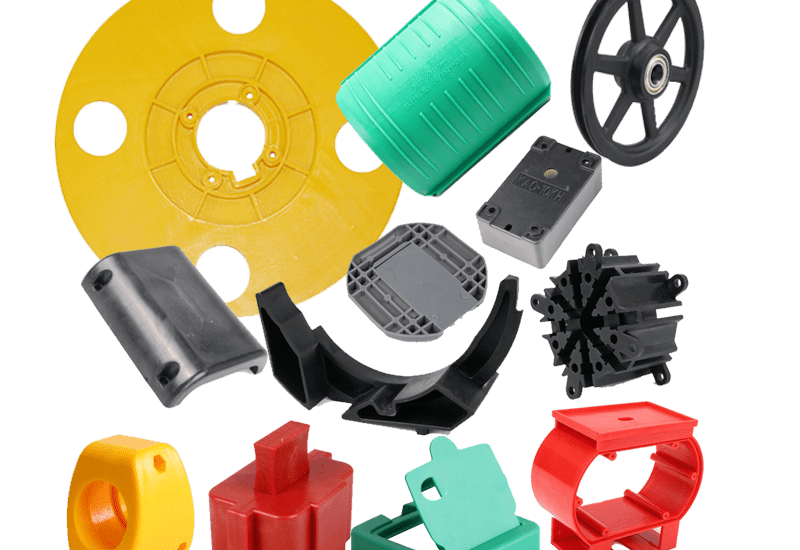
ABS injection moulding is one of the most commonly used manufacturing processes for producing high-quality plastic parts with excellent strength, durability, and finish. Whether used in automotive, consumer electronics, or industrial applications, selecting the right ABS injection moulding process is crucial for achieving maximum efficiency, reducing costs, and ensuring superior product quality. This article explores the different ABS injection moulding techniques and key factors to consider when choosing the best method for your production needs.
Understanding ABS Injection Moulding
What is ABS and Why It Is Widely Used
Acrylonitrile Butadiene Styrene (ABS) is a thermoplastic polymer known for its toughness, impact resistance, and ease of processing. It is widely used in injection moulding due to its ability to maintain strength while offering design flexibility. Manufacturers prefer ABS because it can be easily melted, shaped, and solidified without significant material degradation.
Key Properties That Make ABS Ideal for Injection Moulding
ABS stands out due to its excellent balance of mechanical and aesthetic properties, making it an ideal material for various applications. Some of its notable characteristics include:
- High Impact Resistance – ABS can withstand significant force without breaking, making it suitable for durable products.
- Good Heat Resistance – It maintains structural integrity even under moderate temperatures.
- Excellent Surface Finish – ABS allows for smooth and glossy finishes, which is essential for consumer products.
- Chemical Resistance – It resists many acids, alkalis, and oils, improving product longevity.
- Strong Dimensional Stability – ABS retains its shape and precision even after repeated moulding cycles.
Common Applications of ABS Injection Moulding
Due to its versatility, ABS injection moulding is widely used in industries such as:
- Automotive – Dashboard panels, interior trim, and protective covers
- Electronics – Housings for laptops, smartphones, and remote controls
- Medical Equipment – Sterile and impact-resistant casings for medical devices
- Household Goods – Kitchen appliances, vacuum cleaner components, and toys
Key Factors to Consider When Selecting an ABS Injection Moulding Process
Product Design Complexity and Material Requirements
The complexity of the product design determines which ABS injection moulding technique is most suitable. Intricate parts may require advanced processes such as overmoulding or gas-assisted injection moulding to ensure precise details and strong structural integrity. Additionally, understanding material properties like thickness, flexibility, and rigidity is crucial for selecting the appropriate process.
Production Volume and Cost Considerations
High-volume production often requires efficient moulding techniques that minimize waste and optimize cycle times. If production runs are small, it may be more cost-effective to use conventional ABS injection moulding rather than investing in complex moulding processes.
Mould Design and Tooling Selection
Choosing the right mould design impacts efficiency, material usage, and overall product quality. Factors like gate placement, cooling channels, and cavity design influence how well ABS flows and solidifies within the mould. Proper tooling selection can also prevent defects such as warping and sink marks.
Cycle Time and Energy Efficiency
Optimizing cycle time directly affects production speed and operational costs. The faster the injection moulding process, the higher the output. However, maintaining quality while reducing cycle time requires careful control of mould temperature, injection speed, and cooling rates.
Different Types of ABS Injection Moulding Techniques
Conventional ABS Injection Moulding
This standard process involves injecting molten ABS into a mould cavity at high pressure. Once the plastic cools and solidifies, the part is ejected. Conventional injection moulding is ideal for mass production of simple to moderately complex parts with consistent quality.
Overmoulding with ABS
Overmoulding is used when ABS needs to be combined with another material, such as rubber or metal. This technique enhances product functionality by adding grip, cushioning, or extra durability. It is commonly used in tool handles, automotive parts, and consumer electronics.
Gas-Assisted ABS Injection Moulding
This technique involves injecting pressurized gas (usually nitrogen) into the mould, which creates hollow sections in thick parts. The benefits include:
- Reduced material usage
- Lighter weight components
- Minimized warping and sink marks
Gas-assisted injection moulding is widely used in manufacturing large plastic components, such as automotive panels and furniture.
Thin-Wall ABS Injection Moulding
For products requiring lightweight designs, thin-wall ABS injection moulding is the best choice. This method allows for reduced material costs while maintaining strength and durability. It is often used in packaging, electronic casings, and aerospace components.
Optimizing Efficiency in ABS Injection Moulding
Best Practices for Reducing Cycle Times
To enhance efficiency, manufacturers should focus on:
- Using high-speed injection moulding machines
- Optimizing cooling times with well-designed moulds
- Implementing automated ejection systems
Proper Temperature and Pressure Control
Maintaining the correct temperature and pressure settings prevents defects such as burn marks, bubbles, and uneven filling. ABS typically requires a processing temperature between 200°C and 250°C, depending on the specific formulation and product design.
Preventing Defects and Improving Product Consistency
Common ABS injection moulding defects include:
- Warping – Caused by uneven cooling; resolved by optimizing mould design
- Flash – Excess material escaping the mould; prevented with precise clamping force
- Short Shots – Incomplete filling of the mould; corrected by adjusting pressure and injection speed
Using advanced monitoring systems ensures real-time quality control, minimizing production defects.
Automation and Advanced Monitoring Systems
Modern ABS injection moulding facilities utilize robotic automation and AI-driven monitoring systems to improve efficiency. These technologies:
- Reduce labor costs
- Enhance consistency and accuracy
- Enable predictive maintenance for fewer machine downtimes
Sustainability and Cost-Saving Measures
Recycling and Reusing ABS Material
To minimize waste, manufacturers can recycle ABS scrap and defective parts back into the production process. Regrinding and reprocessing ABS not only reduce material costs but also contribute to environmental sustainability.
Reducing Waste Through Precise Moulding Techniques
Techniques such as gas-assisted moulding and thin-wall injection moulding reduce material consumption, making production more cost-effective.
Energy-Efficient Machinery and Production Strategies
Investing in energy-efficient injection moulding machines with optimized heating and cooling systems significantly lowers electricity consumption. Switching to servo-driven hydraulic systems can further improve operational efficiency.
Conclusion
Selecting the right ABS injection moulding process is crucial for maximizing efficiency, reducing costs, and maintaining high product quality. By considering factors such as product design, production volume, and moulding techniques, manufacturers can optimize their processes for better performance. Implementing best practices in temperature control, automation, and sustainability ensures a competitive advantage in the ever-evolving manufacturing industry.