- April 3, 2025
- Posted by: feinuojixie
- Category: Injection Molding News
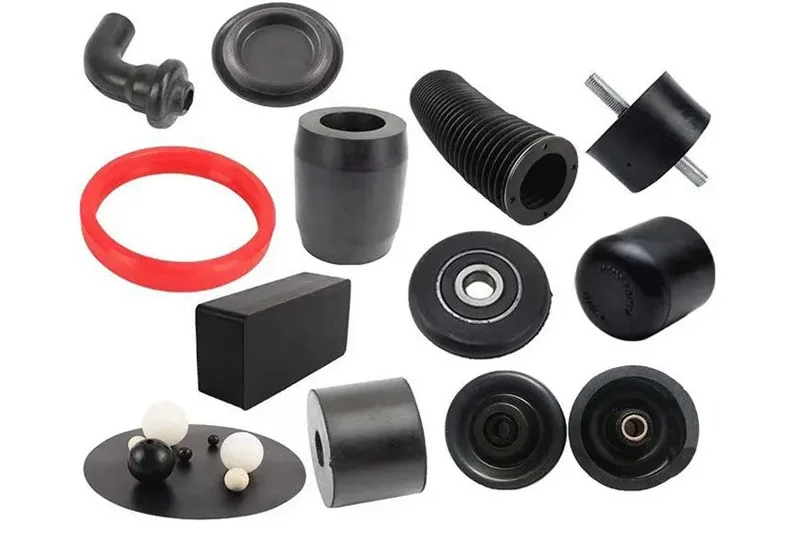
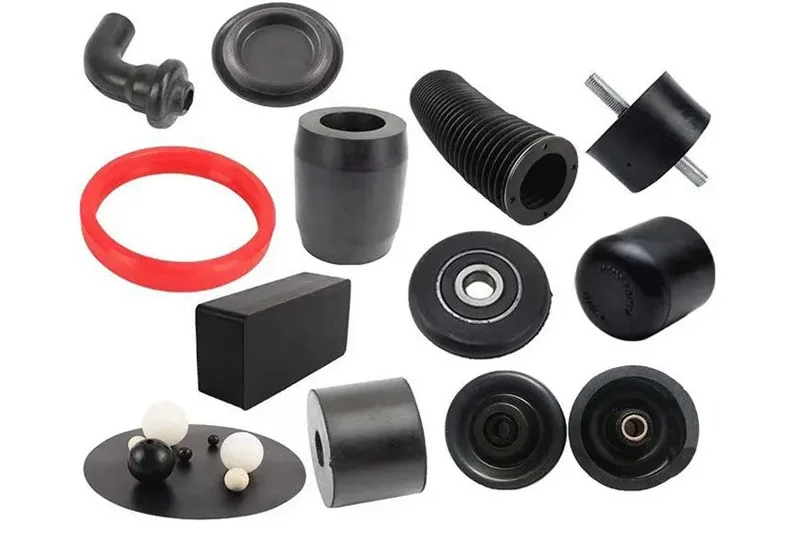
Injection machine parts play a crucial role in the plastic manufacturing process. These machines are responsible for producing precise and high-quality molded products, making them indispensable in various industries. However, frequent failures in critical machine parts can lead to production downtime, increased costs, and compromised product quality. Understanding the common issues associated with injection machine parts and implementing effective prevention strategies can significantly enhance machine longevity and efficiency. This article explores the most common failures in injection machine parts and provides practical solutions to prevent them.
Understanding the Importance of Injection Machine Parts
Injection machines consist of various components, each performing a specific function to ensure smooth and efficient operation. Key parts include the nozzle, screw, barrel, hydraulic system, clamping system, electrical components, and cooling system. These components work in harmony to maintain production consistency and precision. Any malfunction in one part can disrupt the entire manufacturing process, leading to defective products and costly repairs. Regular maintenance and proper handling of these parts are essential for sustaining operational efficiency and preventing unexpected breakdowns.
Common Injection Machine Parts Failures and Their Causes
Nozzle Blockage and Leakage
Nozzle issues are one of the most frequent problems encountered in injection machines. Blockages occur due to residue buildup, improper cleaning, or the use of incompatible materials. Leakage can result from worn-out seals, misalignment, or excessive pressure. Both issues can cause inconsistent material flow, leading to defective products and production delays. Regular cleaning, proper material selection, and timely seal replacement can prevent these failures.
Screw and Barrel Wear
The screw and barrel are responsible for melting and injecting plastic into the mold. Over time, friction, high temperatures, and abrasive materials can cause wear and tear, leading to inconsistent melt flow and reduced injection pressure. Signs of wear include poor plasticization, uneven molding, and increased cycle times. Using high-quality materials, maintaining proper temperature settings, and replacing worn-out parts can help extend their lifespan.
Hydraulic System Malfunctions
Hydraulic issues can lead to severe performance problems in injection machines. Common failures include pressure loss, overheating, and fluid contamination. Worn-out valves, faulty pumps, and inadequate lubrication contribute to hydraulic inefficiencies. Regular oil checks, proper filtration, and timely replacement of hydraulic components can prevent these issues and ensure optimal performance.
Clamping System Failure
The clamping system holds the mold securely during the injection process. If the clamping force is insufficient, it can result in incomplete molds, flash formation, or even mold damage. Causes of clamping failure include mechanical wear, hydraulic pressure loss, and misalignment. Periodic calibration, lubrication of moving parts, and hydraulic pressure monitoring can help maintain proper clamping force and prevent costly repairs.
Electrical Component Issues
Electrical failures can significantly disrupt machine operation. Problems such as faulty sensors, wiring issues, and power fluctuations can lead to sudden stoppages and inconsistent production. Heat exposure, dust accumulation, and worn-out connections further contribute to these failures. Regular inspection of electrical connections, proper grounding, and maintaining stable power supply conditions can minimize these risks.
Cooling System Inefficiencies
The cooling system regulates the mold temperature to ensure proper solidification of plastic parts. Poor water flow, clogged cooling channels, and inadequate temperature control can lead to warping, shrinkage, or other molding defects. Regular descaling, ensuring proper coolant levels, and maintaining optimal cooling settings can improve efficiency and reduce product defects.
How to Prevent Injection Machine Parts Failures
Routine Inspection and Preventive Maintenance
Scheduled inspections help identify potential issues before they escalate into major failures. Implementing a preventive maintenance program that includes checking wear levels, lubricating moving parts, and replacing worn-out components can extend the life of injection machine parts and enhance performance.
Proper Cleaning and Lubrication
Cleaning plays a vital role in preventing residue buildup and blockages in critical components. Regular lubrication reduces friction and heat generation, preventing premature wear. Using manufacturer-recommended cleaning solutions and lubricants ensures optimal performance.
Using High-Quality Materials and Replacement Parts
Investing in high-quality machine parts and materials significantly improves machine durability. Low-quality or counterfeit parts may seem cost-effective initially but can lead to frequent breakdowns and increased maintenance costs in the long run. Choosing OEM or trusted aftermarket parts ensures better reliability.
Training Operators for Optimal Machine Handling
Improper operation is a major contributor to machine failures. Providing comprehensive training for operators on machine handling, maintenance procedures, and troubleshooting techniques can prevent human errors and prolong machine life. Well-trained personnel can also detect early signs of wear and address them promptly.
Monitoring and Upgrading Technology
Modern monitoring systems and automation technologies help detect early warning signs of machine failures. Implementing real-time monitoring systems for pressure, temperature, and lubrication levels can improve preventive maintenance efforts. Upgrading to advanced machinery with smart diagnostics can further enhance efficiency and reduce downtime.
Conclusion
Injection machine parts are critical to the efficiency and reliability of the plastic manufacturing process. Understanding common failure points and implementing preventive measures can help avoid costly downtimes and improve product quality. By following routine maintenance, using high-quality materials, training operators, and leveraging advanced monitoring technologies, manufacturers can ensure smooth and uninterrupted production. Investing in proactive maintenance and high-performance components leads to long-term operational success and reduced repair costs.