- March 19, 2025
- Posted by: feinuojixie
- Category: Injection Molding News
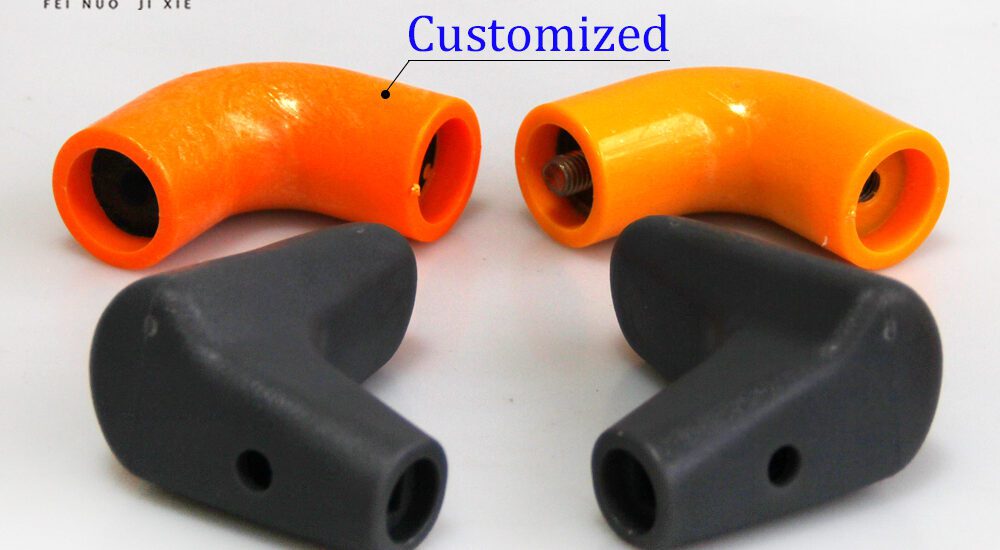
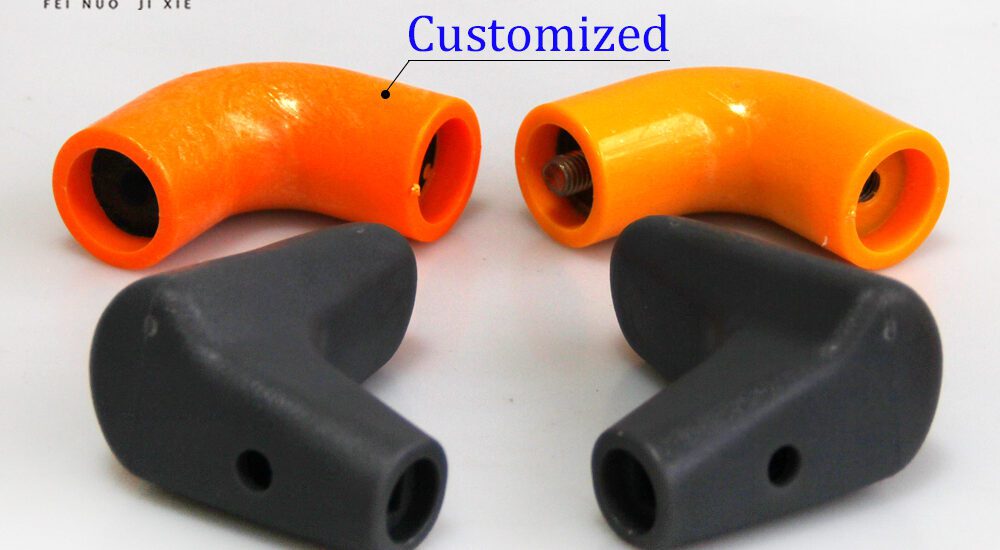
ABS injection moulding is a widely used manufacturing process due to its excellent impact resistance, ease of processing, and cost-effectiveness. However, achieving high-quality results requires precise control over various factors. Many manufacturers face common issues that affect product quality, production efficiency, and overall cost. Understanding these mistakes and implementing preventive measures can significantly improve the moulding process. This article explores the most frequent errors in ABS injection moulding and provides practical solutions to avoid them.
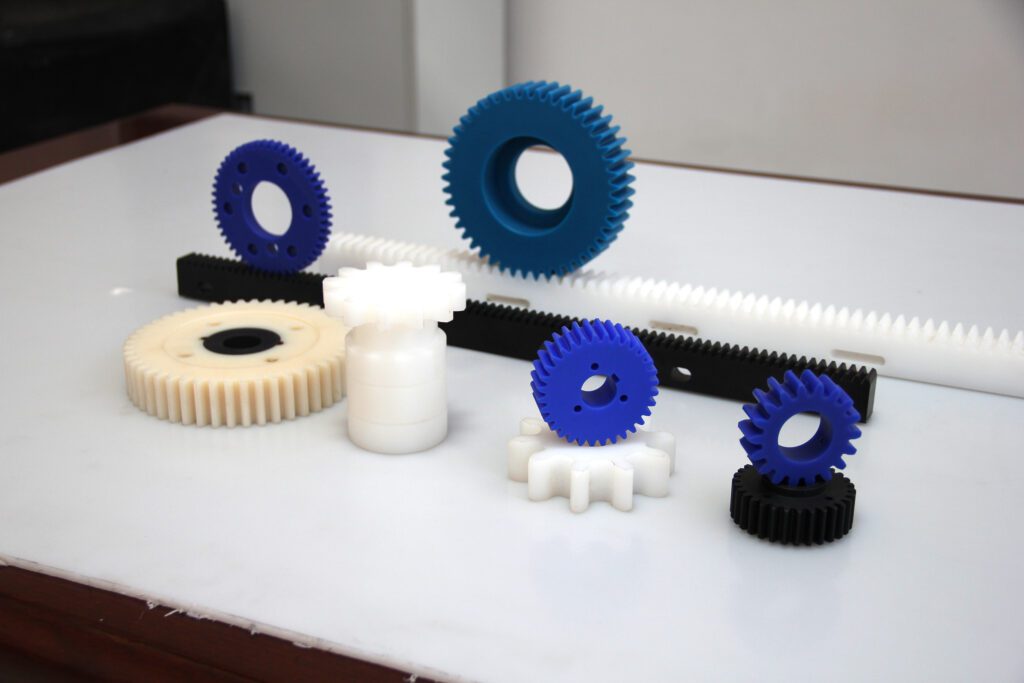
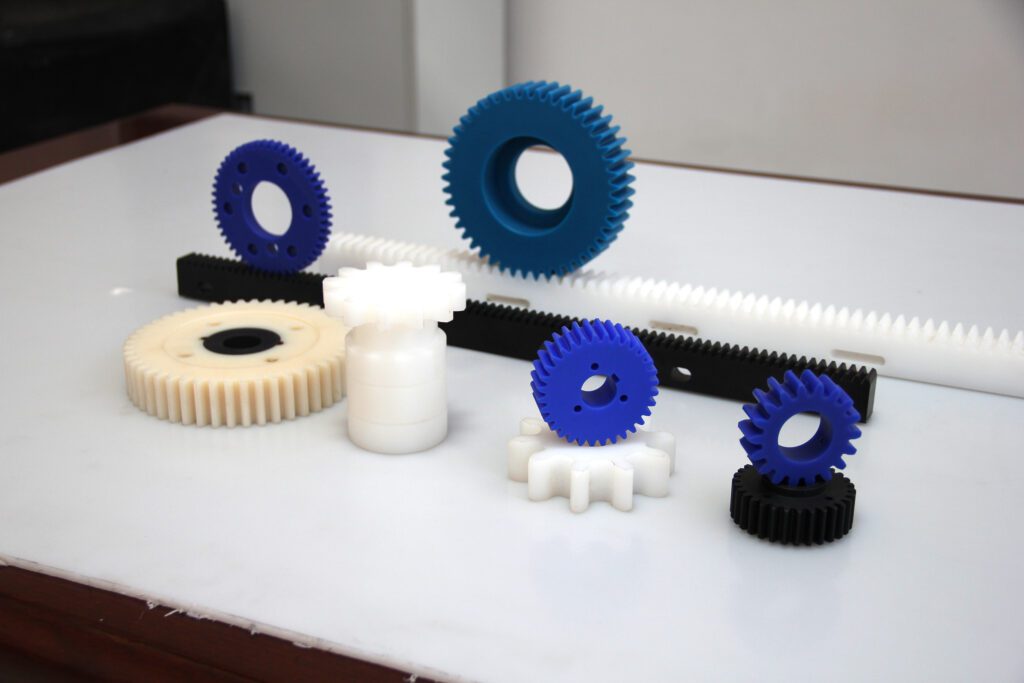
Material Preparation Mistakes and How to Prevent Them
Incorrect Drying Process
ABS is a hygroscopic material, meaning it absorbs moisture from the air. If the resin is not properly dried before moulding, moisture can turn into steam during injection, leading to surface defects, bubbles, and weak mechanical properties. To prevent this issue:
- Dry ABS resin at 80–85°C for 3–4 hours using a dehumidifying dryer.
- Store dried resin in a moisture-proof container to prevent reabsorption.
- Regularly check moisture levels using a moisture analyzer before processing.
Contaminated Raw Material
Impurities such as dust, oil, or foreign plastic particles can cause inconsistent melting and poor adhesion between polymer chains. Contaminated resin can result in weak, brittle parts or unwanted discoloration. To avoid contamination:
- Store ABS resin in sealed, clean containers.
- Ensure proper handling by using gloves and avoiding direct contact with raw material.
- Regularly inspect the resin for impurities before feeding it into the injection moulding machine.
Injection Moulding Parameter Errors and Their Solutions
Inappropriate Temperature Settings
Temperature plays a crucial role in ABS injection moulding. If the temperature is too low, the material may not fully melt, causing short shots and poor surface quality. On the other hand, excessive heat can degrade the polymer, resulting in yellowing, burning, or loss of mechanical strength. The ideal melt temperature for ABS is 210–270°C, depending on the grade and part design. To maintain proper temperature control:
- Use a consistent barrel temperature profile, ensuring gradual heating.
- Monitor and calibrate temperature sensors regularly.
- Avoid sudden temperature fluctuations by preheating the machine before production.
Incorrect Injection Speed and Pressure
Injection speed and pressure must be carefully balanced to ensure proper filling without causing defects.
- Excessive speed and pressure can lead to burn marks, flash, and material degradation.
- Insufficient speed and pressure can result in short shots, flow lines, and poor weld strength.
To optimize settings:
- Adjust injection pressure gradually to achieve a complete fill without overheating.
- Use a moderate injection speed to prevent burn marks while ensuring a smooth flow.
- Monitor fill time and adjust based on part thickness and complexity.
Mould Design Issues and Best Practices
Poor Venting and Gas Traps
During the injection process, trapped air and gas can cause burn marks, voids, or incomplete filling. Inadequate venting restricts airflow and increases defects. To improve mould ventilation:
- Design vents at strategic locations, especially in areas where air is likely to be trapped.
- Keep vent depth between 0.02–0.05 mm to allow air escape without flash formation.
- Regularly clean and inspect vents to prevent clogging.
Inadequate Wall Thickness Control
Inconsistent wall thickness can lead to warping, shrinkage, and sink marks. Thick sections cool slower, causing internal stress and dimensional instability. To ensure uniform wall thickness:
- Maintain a recommended thickness between 1.2–4 mm, depending on part function.
- Use gradual transitions instead of abrupt thickness changes to prevent stress concentrations.
- Implement ribs and supports instead of thick sections to improve strength without increasing weight.
Defects in ABS Injection Moulding and How to Fix Them
Warping and Shrinkage
Warping occurs when different sections of a moulded part cool at varying rates, leading to distortions. Shrinkage, on the other hand, results in dimensional inaccuracies. To reduce these defects:
- Optimize cooling channel design for even temperature distribution.
- Use slow and controlled cooling to minimize internal stress.
- Ensure consistent mould temperature, ideally 60–80°C, for uniform contraction.
Sink Marks and Voids
Sink marks and internal voids form when the outer surface cools faster than the inner material, causing uneven density. To prevent these defects:
- Increase packing pressure to ensure proper material distribution.
- Reduce thickness variations and use core-outs in thick sections.
- Adjust holding time and pressure to compensate for material shrinkage.
Machine Maintenance and Operator Training
Neglecting Regular Maintenance
A poorly maintained injection moulding machine can cause inconsistent pressure, temperature fluctuations, and mechanical failures. Without routine maintenance, defects become more frequent, and production downtime increases. To maintain machine efficiency:
- Perform daily, weekly, and monthly maintenance checks on heating elements, screws, and hydraulic systems.
- Regularly clean nozzles and moulds to prevent material buildup.
- Calibrate sensors and controllers to ensure accurate readings.
Lack of Skilled Operators
Even with the best machines and mould designs, improper operation can lead to defective parts. Many production issues stem from operator errors, such as incorrect parameter settings or improper handling of materials. To enhance operator competency:
- Implement regular training programs on process optimization and troubleshooting.
- Encourage documentation of best practices for consistent production quality.
- Use automated monitoring systems to assist operators in maintaining ideal settings.
Conclusion
Avoiding common mistakes in ABS injection moulding requires a thorough understanding of material preparation, process control, mould design, and machine maintenance. By carefully managing temperature, pressure, cooling, and material quality, manufacturers can significantly improve production efficiency and part reliability. With proper training and preventive maintenance, ABS injection moulding can achieve outstanding results, reducing defects and maximizing product performance.