- March 26, 2025
- Posted by: feinuojixie
- Category: Injection Molding News
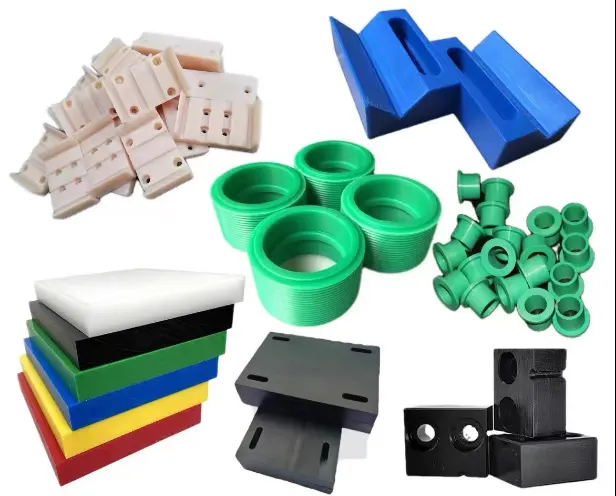
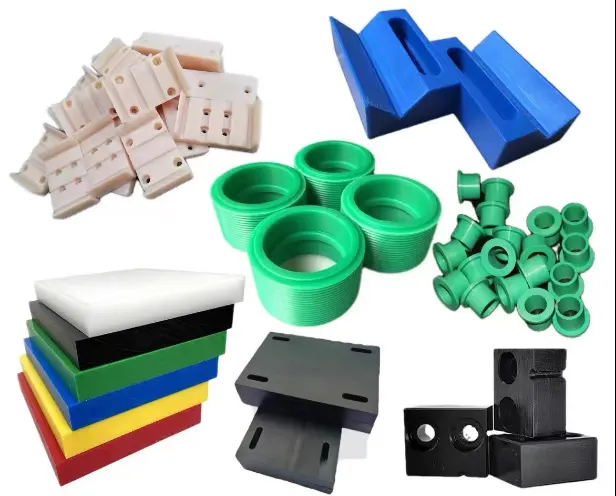
Understanding ABS Injection Moulding
ABS injection moulding is a manufacturing process used to produce high-precision plastic parts. Acrylonitrile Butadiene Styrene (ABS) is a popular thermoplastic due to its excellent impact resistance, toughness, and ease of processing. It is widely used in automotive components, electronic housings, and consumer products.
The injection moulding process involves heating ABS pellets until they melt, injecting the molten material into a mould, allowing it to cool and solidify, and finally ejecting the finished part. While this process seems straightforward, various factors must be carefully controlled to ensure defect-free production.
Common Mistakes in ABS Injection Moulding and Their Solutions
Improper Temperature Control
Temperature plays a critical role in ABS injection moulding. If the melting temperature is too high, it can cause degradation, burning, or excessive shrinkage. If it is too low, the material may not flow properly, leading to short shots or poor surface quality.
How to avoid this mistake:
-
Maintain the recommended melting temperature between 210°C and 250°C.
-
Ensure the mould temperature is set within 50°C to 80°C for optimal cooling and surface finish.
-
Use a reliable temperature control system to monitor and adjust settings in real-time.
Incorrect Injection Speed and Pressure
Injection speed and pressure must be carefully balanced. If the speed is too high, it can lead to flash, warping, or excessive internal stress. If it is too low, the material may not fill the mould completely, causing short shots or uneven distribution.
How to avoid this mistake:
-
Adjust injection speed to allow smooth and complete mould filling without excessive turbulence.
-
Maintain pressure at a level that ensures full cavity filling while minimizing defects.
-
Use a multi-stage injection process to control pressure variations.
Poor Ventilation and Gas Trapping
When air or gas gets trapped in the mould cavity, it can create burn marks, bubbles, or incomplete filling. This issue is often caused by inadequate venting or improper gate positioning.
How to avoid this mistake:
-
Design proper vents in the mould to allow air to escape during injection.
-
Position gates strategically to facilitate smooth material flow.
-
Use vacuum-assisted moulding techniques for complex parts.
Inadequate Drying of ABS Material
ABS is hygroscopic, meaning it absorbs moisture from the air. If the material is not dried properly before processing, the moisture turns into steam during moulding, causing surface defects and weakened mechanical properties.
How to avoid this mistake:
-
Pre-dry ABS pellets in a desiccant dryer at 80°C for 2 to 4 hours before moulding.
-
Store ABS material in sealed containers to prevent moisture absorption.
-
Regularly check material moisture content to maintain consistency.
Improper Mould Design
A poorly designed mould can cause defects such as warping, sink marks, and poor dimensional accuracy. Common design issues include insufficient draft angles, thin walls, sharp corners, and inadequate runner systems.
How to avoid this mistake:
-
Ensure proper draft angles of at least 1° to 3° for easy part ejection.
-
Maintain a uniform wall thickness of 1.5mm to 4mm to prevent uneven cooling.
-
Round off sharp corners to avoid stress concentration and material flow issues.
Inconsistent Cooling Time
Uneven cooling leads to shrinkage, internal stress, and deformation. If cooling is too fast, it may cause warping; if too slow, production time increases, reducing efficiency.
How to avoid this mistake:
-
Use uniform cooling channels in the mould to ensure even temperature distribution.
-
Maintain a cooling time that allows gradual solidification without excessive stress.
-
Monitor mould temperature using thermocouples to adjust cooling cycles as needed.
Wrong Selection of Additives and Fillers
ABS is often modified with additives and fillers to enhance its properties. However, using incompatible additives can reduce impact resistance, cause discoloration, or weaken the structure.
How to avoid this mistake:
-
Use reinforcing fillers like glass fibers for added strength when needed.
-
Select UV stabilizers if parts will be exposed to sunlight.
-
Ensure all additives are tested for compatibility with ABS resin.
Insufficient Mould Maintenance
Over time, moulds accumulate residue from ABS material, leading to poor part quality and increased defect rates. Worn-out mould components can also result in dimensional inaccuracies.
How to avoid this mistake:
-
Perform regular mould cleaning to remove residue and contaminants.
-
Inspect and replace worn-out parts, such as ejector pins and gate seals.
-
Use a mould release agent to reduce sticking and prolong mould life.
Conclusion
ABS injection moulding is a highly effective process, but common mistakes can lead to defects, production delays, and increased costs. By carefully controlling temperature, injection speed, mould design, and material preparation, manufacturers can achieve high-quality, defect-free parts.
Understanding and addressing these challenges not only improves efficiency but also enhances the durability and appearance of ABS moulded products. With the right techniques and maintenance, ABS injection moulding can deliver consistent and reliable results, making it a preferred choice for various industries.