- March 20, 2025
- Posted by: feinuojixie
- Category: Injection Molding News
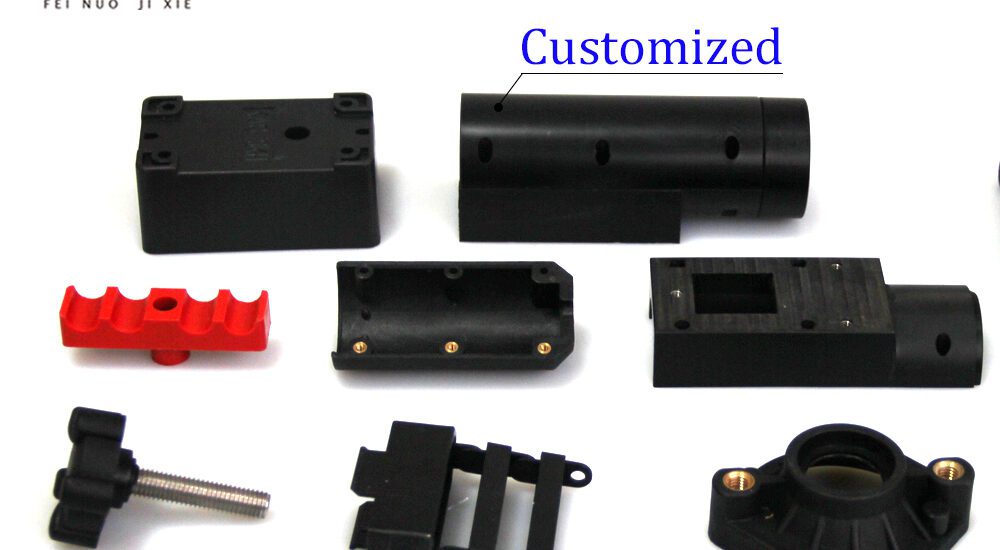
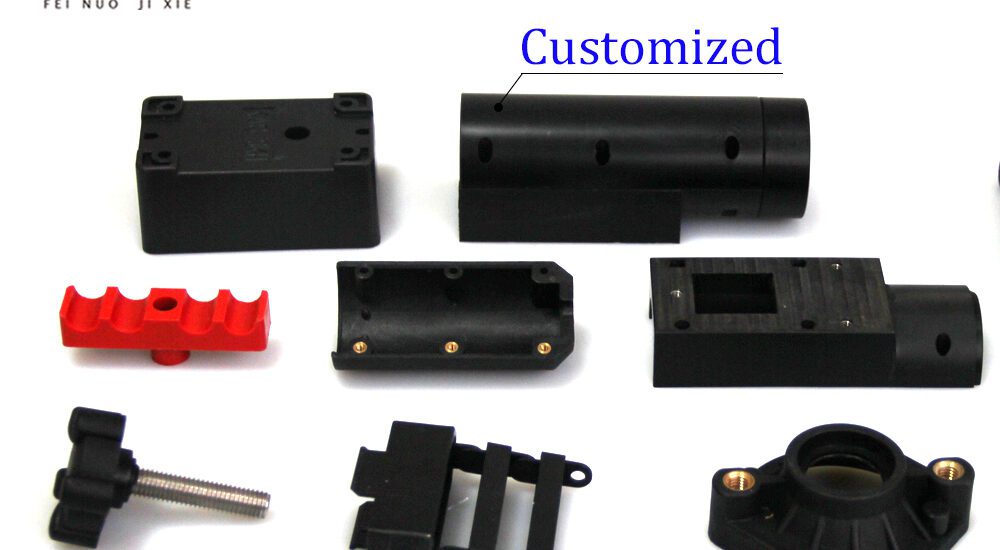
ABS injection moulding is one of the most efficient and reliable manufacturing techniques used across various industries. Known for its cost-effectiveness and high performance, this process provides an excellent balance between durability, flexibility, and affordability. ABS, or Acrylonitrile Butadiene Styrene, is a thermoplastic polymer that combines impact resistance, heat stability, and easy machinability. These qualities make it an ideal material for producing a wide range of products, from automotive components to consumer electronics.
The growing demand for lightweight, durable, and cost-efficient materials has positioned ABS injection moulding as a go-to solution for manufacturers worldwide. Unlike traditional fabrication methods, injection moulding offers unparalleled precision, minimal material wastage, and a streamlined production process. This article delves into why ABS injection moulding remains a preferred choice, exploring its economic benefits, performance attributes, design flexibility, and sustainability considerations.
What Is ABS Injection Moulding?
ABS injection moulding is a manufacturing process that involves injecting molten ABS plastic into a mould cavity under high pressure. Once the material cools and solidifies, it takes the shape of the mould, producing precise and repeatable components. This process is widely used due to its ability to create complex shapes with minimal post-processing requirements. The key advantages of ABS injection moulding include its efficiency, consistency, and the ability to scale production while maintaining product quality.
The Cost-Effectiveness of ABS Injection Moulding
Low Material Cost
ABS is a relatively inexpensive thermoplastic compared to other engineering plastics. Its affordability makes it an attractive choice for manufacturers looking to minimize material costs without sacrificing quality.
Efficient Production Process
The injection moulding process optimizes material usage, reducing waste and maximizing efficiency. Additionally, automated production lowers labor costs, further enhancing its cost-effectiveness.
Minimal Post-Processing Requirements
Unlike other manufacturing methods that require extensive finishing, ABS injection moulding produces smooth and precise parts that need little to no additional machining or modifications.
High Performance and Durability
Impact Resistance
ABS is well known for its excellent impact resistance, making it a preferred choice for applications requiring toughness and durability, such as automotive parts and protective housings.
Heat and Chemical Resistance
ABS can withstand moderate heat levels and exposure to various chemicals, making it suitable for industrial and consumer applications where environmental conditions may fluctuate.
Structural Stability
Products made from ABS maintain their dimensional accuracy and strength over time, ensuring long-lasting performance in demanding environments.
Design Flexibility and Versatility
Complex Geometries
ABS injection moulding allows for intricate designs and detailed features that would be challenging to achieve using other manufacturing techniques.
Wide Range of Finishes
ABS parts can be easily painted, textured, or coated to meet aesthetic and functional requirements, giving designers more creative freedom.
Lightweight Yet Strong
Despite being lightweight, ABS provides sufficient strength for many structural and functional applications, making it an excellent choice for reducing product weight without compromising performance.
Applications of ABS Injection Moulding
Automotive Industry
ABS is commonly used in the automotive sector for dashboards, trims, and structural components due to its durability and lightweight nature.
Consumer Electronics
From laptop casings to smartphone covers, ABS injection moulding is widely employed in electronics manufacturing to produce sturdy and stylish enclosures.
Medical Equipment
The sterility and impact resistance of ABS make it suitable for medical device housings and other healthcare-related applications.
Household and Industrial Products
ABS is frequently used for tool handles, storage containers, and various household goods that require strength, affordability, and ease of manufacturing.
Environmental Considerations and Sustainability
Recyclability
ABS is a recyclable thermoplastic, allowing manufacturers to reduce material waste and promote sustainable production practices.
Energy Efficiency
Injection moulding is an energy-efficient manufacturing process compared to other methods, reducing overall production costs and environmental impact.
Longevity and Reusability
The durability of ABS ensures that products last longer, reducing the need for frequent replacements and minimizing overall material consumption.
Conclusion
ABS injection moulding provides a perfect balance of cost-effectiveness, high performance, and design flexibility. Its wide range of applications and environmental benefits make it a preferred choice across industries. Whether for large-scale manufacturing or specialized components, this method continues to set the standard for quality and efficiency. As industries evolve, ABS injection moulding remains a key driver of innovation and cost savings.