- May 1, 2025
- Posted by: feinuojixie
- Category: Injection Molding News
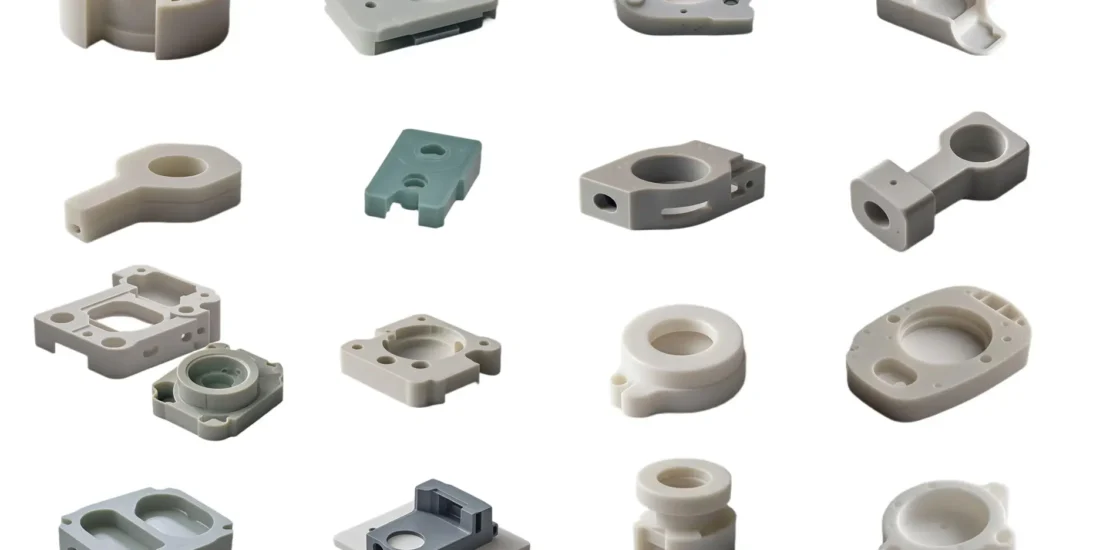
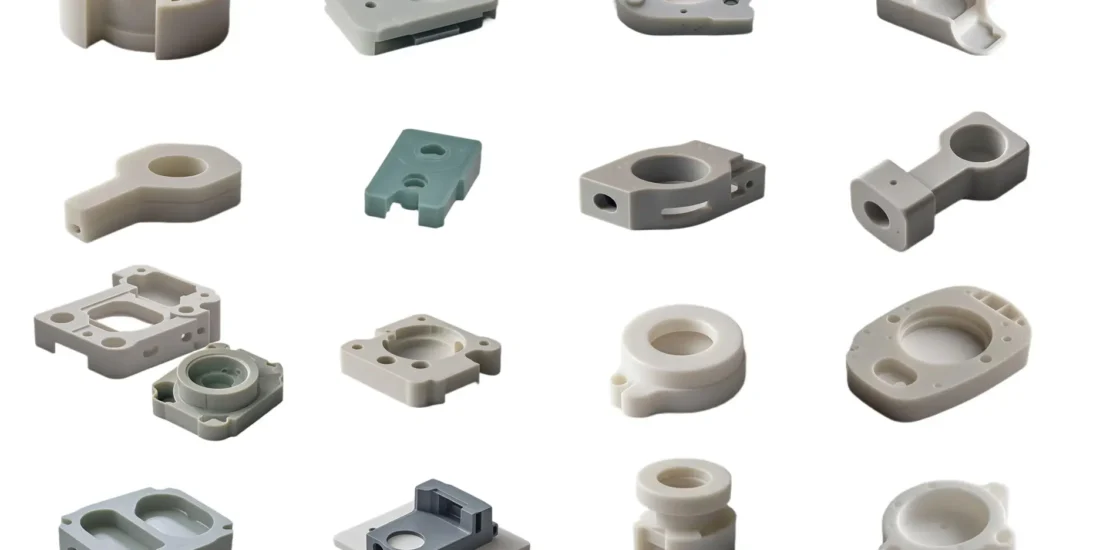
In today’s competitive automotive industry, manufacturers face increasing pressure to deliver high-performance vehicles at lower costs. Every component, from structural brackets to interior panels, must meet rigorous quality standards while remaining cost-effective to produce. As automakers seek efficient production strategies, injection molding has emerged as a powerful solution—particularly for automotive parts that require precision, durability, and scalability. By adopting injection molding, manufacturers can strike a crucial balance between cost control and uncompromising quality, enabling them to meet consumer expectations and industry regulations without inflating their bottom line.
Understanding Injection Molding in Automotive Part Production
Injection molding is a manufacturing process where molten material, typically plastic or composite, is injected into a precision-designed mold to form a specific shape. In automotive part production, this method offers unmatched consistency, the ability to create complex geometries, and high repeatability. Injection molding is ideal for automotive applications because it can efficiently produce intricate designs that would be costly or impossible with traditional methods. From dashboard components to exterior trim, the process allows manufacturers to achieve tight tolerances and durable performance, all critical for the automotive market.
Cost-Efficiency of Injection Molding in Automotive Parts
One of the major advantages of injection molding for automotive part production is its inherent cost efficiency. High-volume manufacturing allows the cost per unit to drop significantly once the mold is created. Injection molding minimizes material waste by using precise amounts of raw material, which reduces overhead. Short cycle times further lower labor costs and increase overall throughput. Additionally, the ability to automate much of the process enhances production speed and consistency, offering an attractive path for manufacturers aiming to maximize their return on investment.
Maintaining High Quality with Injection Molding in Automotive Applications
While cutting costs is essential, maintaining high quality is non-negotiable in automotive manufacturing. Injection molding supports this demand by enabling the use of high-precision molds and strict process control. Every stage of production, from initial material heating to mold filling and cooling, can be monitored and adjusted to ensure the final product meets detailed specifications. Quality assurance is reinforced through the integration of real-time inspection systems and rigorous testing protocols. This capability ensures that even with reduced costs, automotive part manufactured by injection molding retains the durability, functionality, and aesthetic quality expected in the industry.
Material Selection: Balancing Performance and Cost
Choosing the right material is crucial for balancing cost and performance in automotive injection molding. Common materials include polypropylene, ABS, nylon, and polycarbonate, each offering unique advantages such as heat resistance, impact strength, and lightweight properties. Selecting a material depends on the specific application requirements, such as exposure to temperature extremes or mechanical stress. Strategic material selection enables manufacturers to meet performance standards while managing material costs effectively. Sometimes, blending polymers or adding reinforcements like glass fiber can further optimize both performance and budget.
Design Optimization for Cost Reduction
Effective part and mold design play a vital role in controlling costs in injection molding automotive part production. Techniques such as minimizing undercuts, maintaining uniform wall thickness, and consolidating multiple components into a single molded piece can reduce production complexity and material use. Additionally, designing for ease of mold release reduces wear and tear on the mold, extending its lifespan and reducing maintenance expenses. Early collaboration between design and manufacturing teams ensures that the part design is optimized not only for function but also for cost-efficiency.
Advanced Technologies Enhancing Injection Molding in Automotive Parts
Technological advancements are continually improving injection molding in automotive manufacturing. Automation systems streamline part handling and assembly, while real-time monitoring technology ensures that every cycle adheres to strict quality parameters. Innovations like microcellular molding reduce material consumption without sacrificing strength. Artificial intelligence applications are also emerging, helping to predict defects before they occur and optimizing production parameters dynamically. These advancements allow manufacturers to further cut costs, improve yields, and deliver superior automotive part to market faster.
Sustainability and Waste Reduction
Sustainability has become a key focus in the automotive industry, and injection molding supports these initiatives. Many manufacturers are now incorporating recycled materials into their processes without compromising quality. Injection molding generates minimal waste compared to other manufacturing techniques, and any excess material, such as sprues and runners, can often be reprocessed. By focusing on sustainability, companies not only meet regulatory demands but also appeal to increasingly eco-conscious consumers, creating a competitive advantage.
Common Challenges and How to Overcome Them
Despite its advantages, injection molding presents certain challenges in automotive manufacturing. High initial tooling costs can be a barrier, but strategic planning and amortization across large production runs mitigate this impact. Warpage and shrinkage issues can affect part precision; these are best addressed through careful material selection, mold design, and process control. Production defects like voids or sink marks can be minimized with optimized injection parameters and robust mold maintenance. Proactively managing these challenges ensures that the benefits of injection molding outweigh potential drawbacks.
Case Studies: Successful Use of Injection Molding in Automotive Manufacturing
Several leading automotive companies have successfully leveraged injection molding to enhance their production. For example, a major electric vehicle manufacturer adopted lightweight injection molded interior panels, reducing vehicle weight and manufacturing costs simultaneously. Another global automaker integrated AI-driven monitoring into its injection molding process, achieving a 30% reduction in scrap rates while speeding up production times. These examples illustrate how strategic use of injection molding can drive innovation, cost savings, and quality improvements in real-world applications.
Strategic Use of Injection Molding for Competitive Advantage
Injection molding offers a powerful way for automotive manufacturers to cut costs without sacrificing quality. By understanding the process, optimizing material and design choices, leveraging advanced technology, and committing to sustainability, companies can create high-quality automotive part efficiently and economically. In a market where cost pressures and quality demands continue to intensify, strategic use of injection molding provides a vital competitive edge, positioning manufacturers for long-term success.