- February 21, 2025
- Posted by: feinuojixie
- Category: Injection Molding News
No Comments
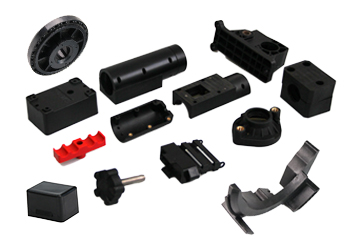
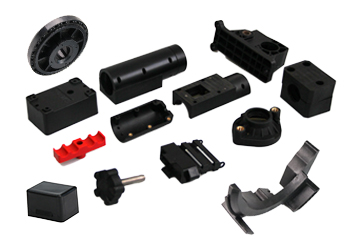
In today’s industrial landscape, injection molded parts have become an integral part of countless products across various industries. From automotive components to consumer electronics, these precision – crafted parts play a crucial role in bringing innovative ideas to life. In this blog post, we will take a deep dive into the world of injection molded parts and discover why they are the ideal choice for your next big project.
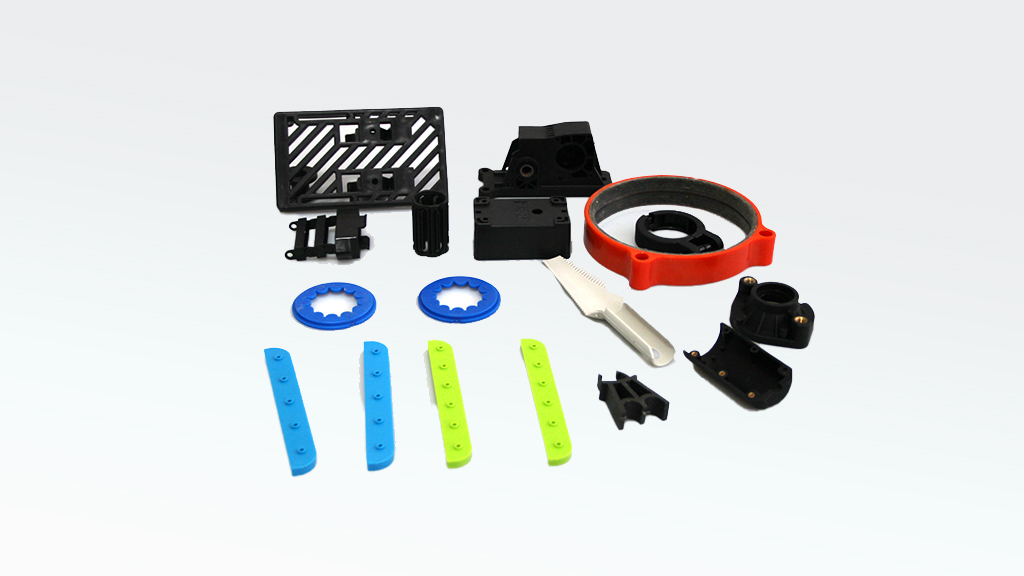
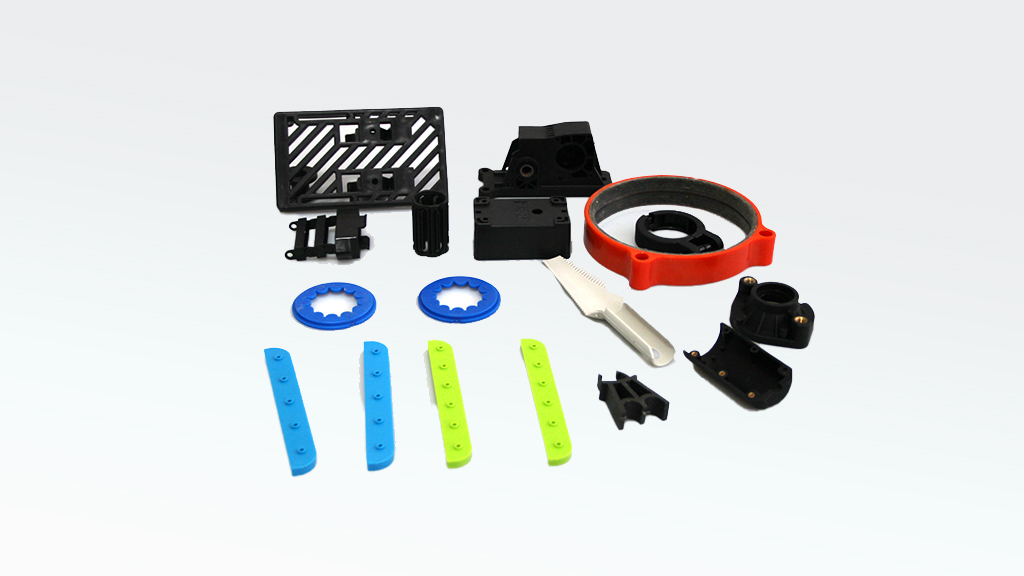
The Advantages of Injection Molded Parts
Cost – Efficiency
Injection molding offers significant cost savings, especially for large – scale production. Once the mold is created, the cost per part is relatively low, making it an affordable option for high – volume manufacturing.
High Precision
With advanced technology, injection molded parts can achieve extremely high precision. This ensures that each part meets the exact specifications, reducing the need for post – production adjustments.
High Production Efficiency
The injection molding process is fast, allowing for a large number of parts to be produced in a short period. This high production rate can help you meet tight deadlines.
Diverse Material Options
There is a wide range of materials available for injection molding, including plastics, metals, and elastomers. This diversity enables you to choose the material that best suits your project’s requirements.
Key Design Considerations for Injection Molded Parts
Design Principles
A well – designed injection molded part should be easy to manufacture and meet the functional requirements. Keep the design simple and avoid complex geometries that may cause manufacturing difficulties.
Wall Thickness
Maintaining a consistent wall thickness is crucial. Uneven wall thickness can lead to warping, shrinkage, and other defects.
Draft Angles
Proper draft angles are necessary to ensure easy removal of the part from the mold without damaging it.
Material Selection
Common Materials and Their Properties
Plastics like ABS, PP, and PC have different properties such as strength, heat resistance, and chemical resistance. Metals like aluminum and zinc alloys offer high strength and durability. Understanding these properties is essential for making the right choice.
Choosing the Right Material for Your Project
Consider factors such as the part’s end – use, environmental conditions, and mechanical requirements when selecting a material.
Quality Control
The Importance of Quality Control
Quality control is vital to ensure that the injection molded parts meet the required standards. Defective parts can lead to product failures and costly recalls.
Quality Inspection Methods and Standards
Various inspection methods, such as visual inspection, dimensional inspection, and material testing, are used to ensure the quality of the parts. Adhering to industry standards is also crucial.
Selecting the Right Supplier
Experience Matters
Choose a supplier with extensive experience in injection molding. An experienced supplier is more likely to handle complex projects and provide high – quality parts.
Equipment and Technology
State – of – the – art equipment and advanced technology can ensure efficient production and high – precision parts.
Customer Service
Good customer service is essential. The supplier should be responsive to your needs and provide timely communication throughout the project.
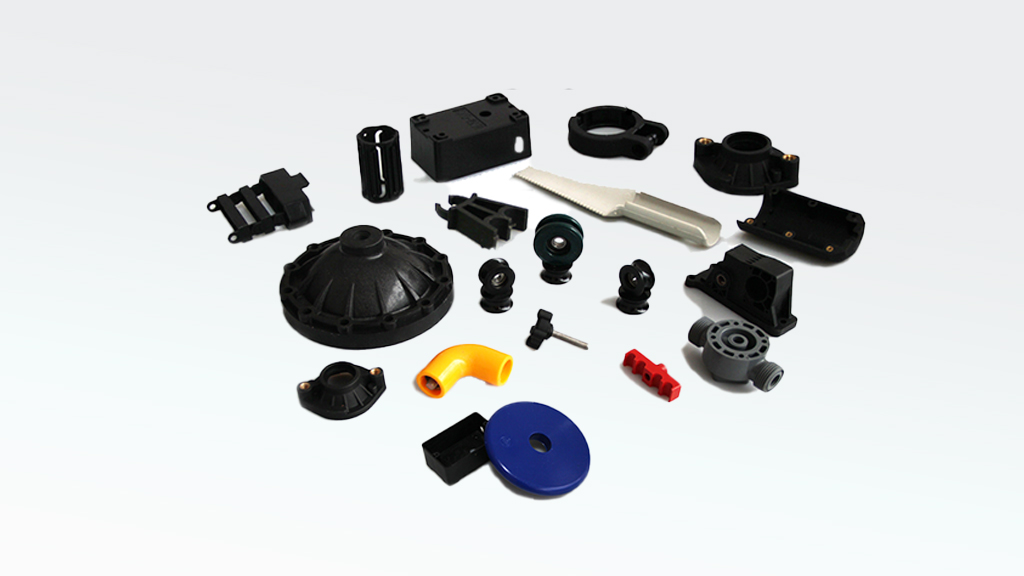
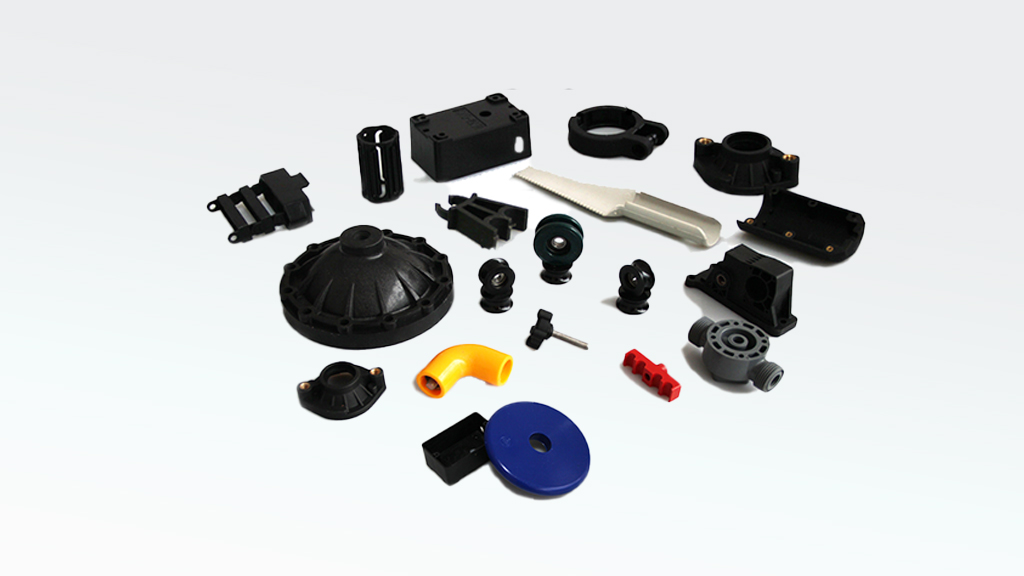
Real – World Case Studies
Showcasing Success Stories
Let’s look at some real – world examples of how injection molded parts have contributed to the success of big projects. These case studies will illustrate the benefits and possibilities of using injection molded parts.
Conclusion
Injection molded parts offer a combination of cost – effectiveness, high precision, and design flexibility that make them an excellent choice for your next big project. By understanding their advantages, design considerations, material options, quality control, and how to choose the right supplier, you can ensure the success of your project. Don’t hesitate to explore the world of injection molded parts and take your project to the next level.